Sshire
Well-Known Member
- Joined
- Jun 29, 2011
- Messages
- 935
- Reaction score
- 267
Elmers #33 - Mill Engine
Cross HeadCase
Episode 1
Ive yet to make a mill engine and,since its been nearly 24 hours since I finished the cross twin, and I have that extra flywheel casting
I usually build from the base up, so the base and sub base are first up. Dykemd (is that a word?) and marked out. My usual M.O. to prevent mental lapses.
Spot drilling, drilling and tapping followed. When I can, Ive been using spiral point or spiral flute taps for small holes. Less chance of the chip binding the tap.
So the base has all of the holes done. So then, Im looking at the plans and I see this.
A radiused slot??? I can usually figure out some way to do things but this one had me stumped. Im quite sure that everyone knows how to do this but me. I was just about to post a How do I do this? question on the forum when I thought about the shape and my slotting saws. Now, my thickest saw if .06 so thats not going to work, but, a 2.5 x .5 one would give me the width and the 1.25 radius.
Ordered and received 2 days later. No way was I going to buy a $75 mandrel. Ive made mandrels for my slotting saws. I had some 7075 1.125 round bar and made this.
Since I have the headroom and I hate indicating the vise, I clamped an angle plate in the vise.
After some adjustments (%#*&*&&#!!), I got the part level enough.
With the Bridgeport in back gear and light cuts, I got my radiuses slot with a nice finish.
Then the sub base. Nothing but some drilling, two ¼ slots and a run with the face mill.
The first two parts done.
Pull up a chair. The fun never ends.
Cross HeadCase
Episode 1
Ive yet to make a mill engine and,since its been nearly 24 hours since I finished the cross twin, and I have that extra flywheel casting
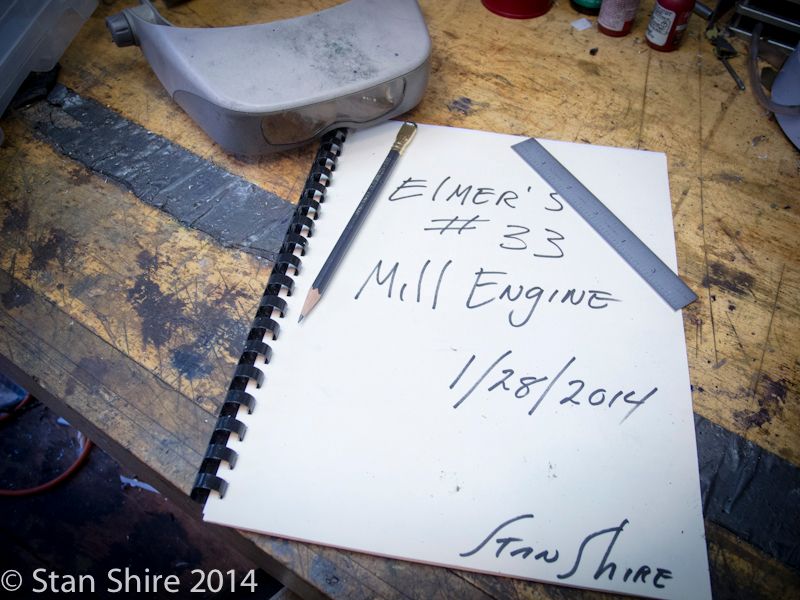
I usually build from the base up, so the base and sub base are first up. Dykemd (is that a word?) and marked out. My usual M.O. to prevent mental lapses.
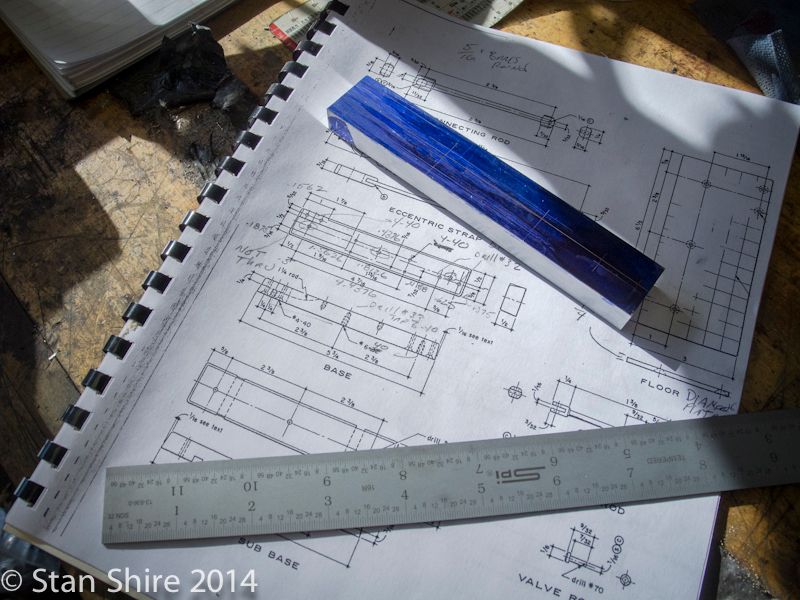
Spot drilling, drilling and tapping followed. When I can, Ive been using spiral point or spiral flute taps for small holes. Less chance of the chip binding the tap.
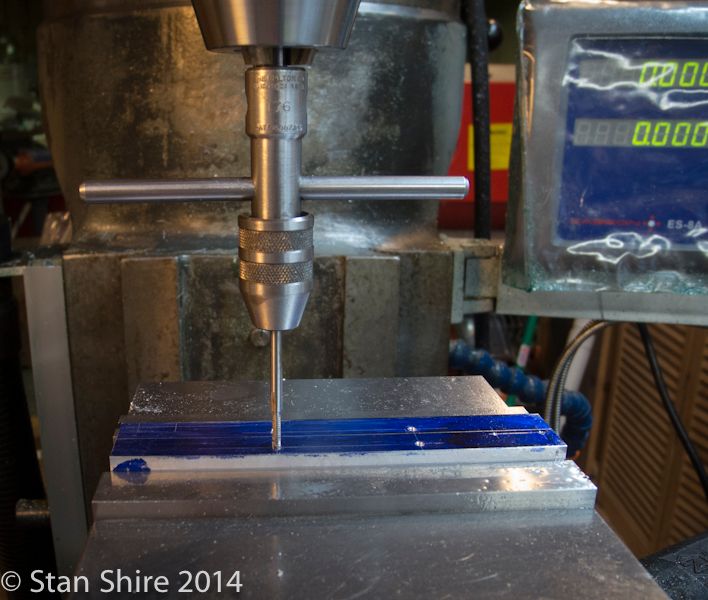
So the base has all of the holes done. So then, Im looking at the plans and I see this.
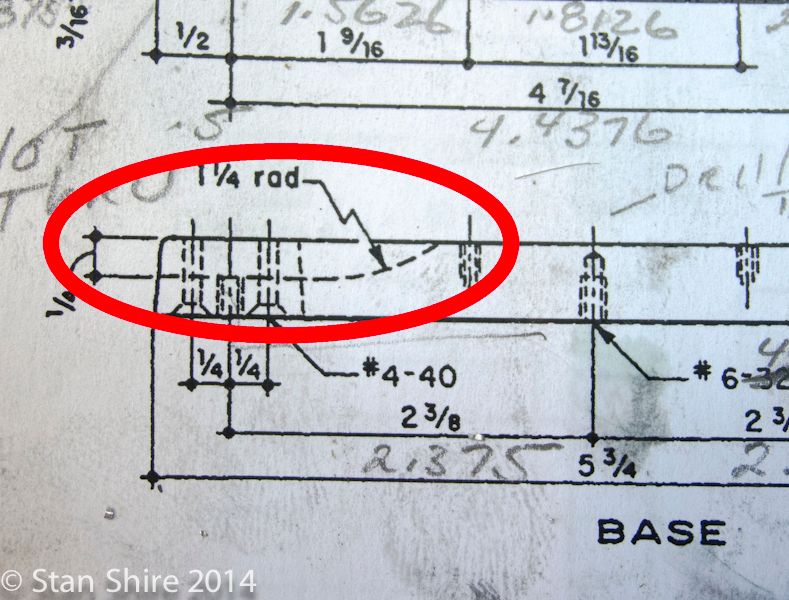
A radiused slot??? I can usually figure out some way to do things but this one had me stumped. Im quite sure that everyone knows how to do this but me. I was just about to post a How do I do this? question on the forum when I thought about the shape and my slotting saws. Now, my thickest saw if .06 so thats not going to work, but, a 2.5 x .5 one would give me the width and the 1.25 radius.
Ordered and received 2 days later. No way was I going to buy a $75 mandrel. Ive made mandrels for my slotting saws. I had some 7075 1.125 round bar and made this.
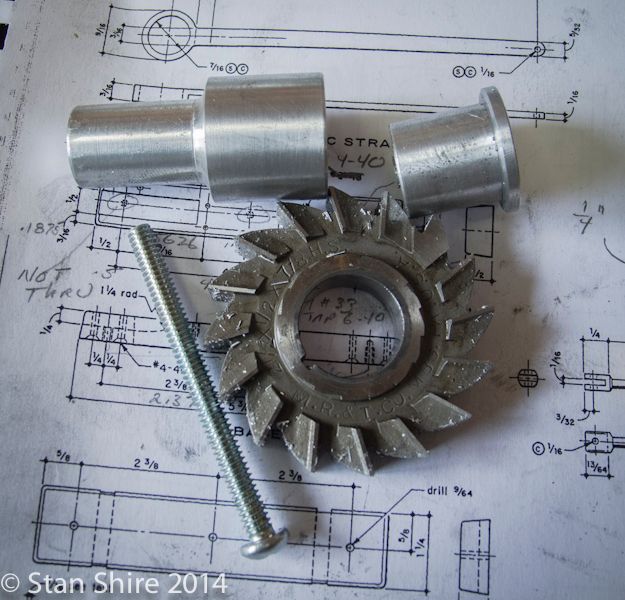
Since I have the headroom and I hate indicating the vise, I clamped an angle plate in the vise.
After some adjustments (%#*&*&&#!!), I got the part level enough.
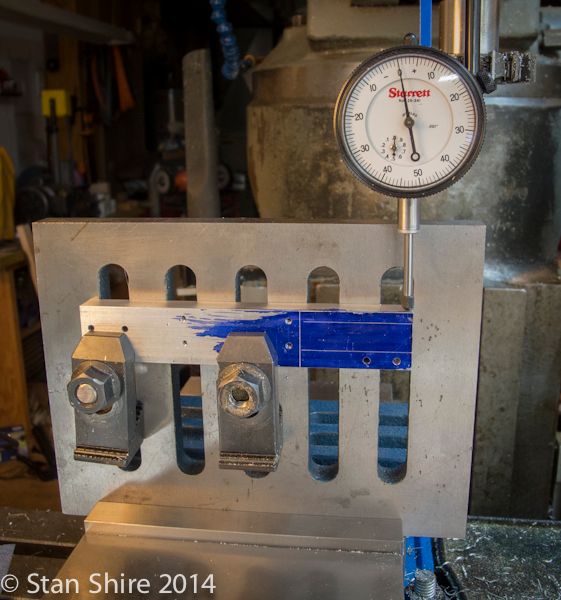
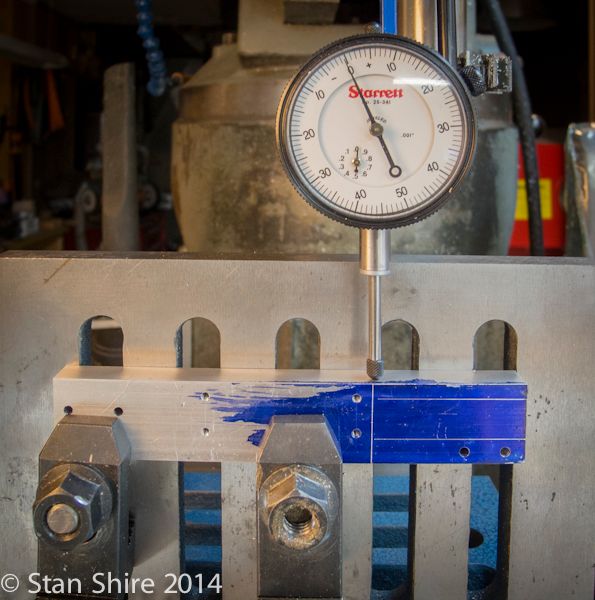
With the Bridgeport in back gear and light cuts, I got my radiuses slot with a nice finish.
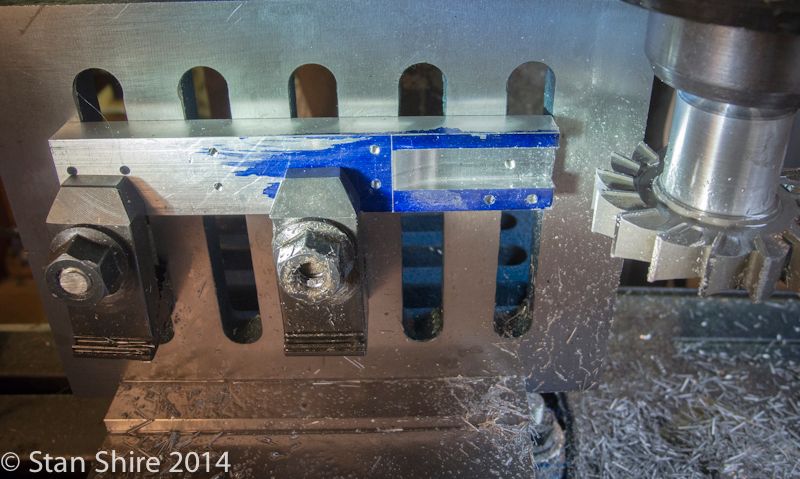
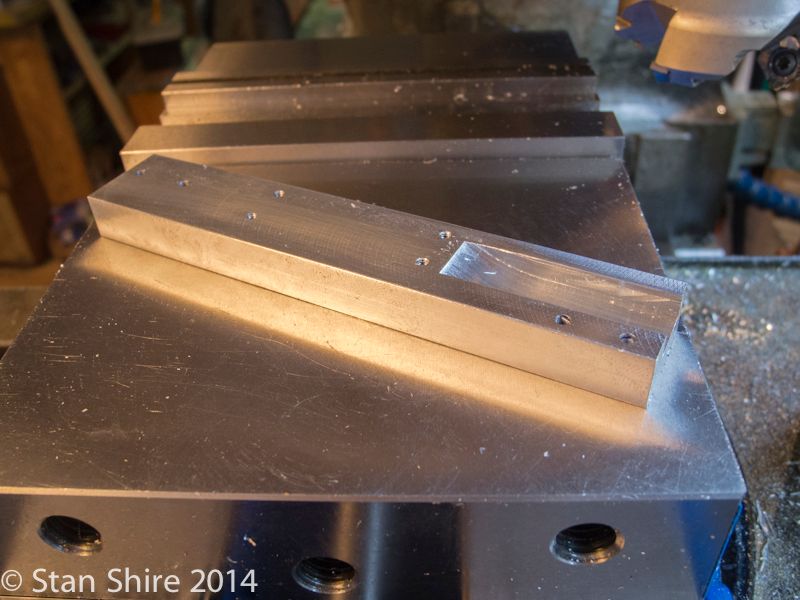
Then the sub base. Nothing but some drilling, two ¼ slots and a run with the face mill.
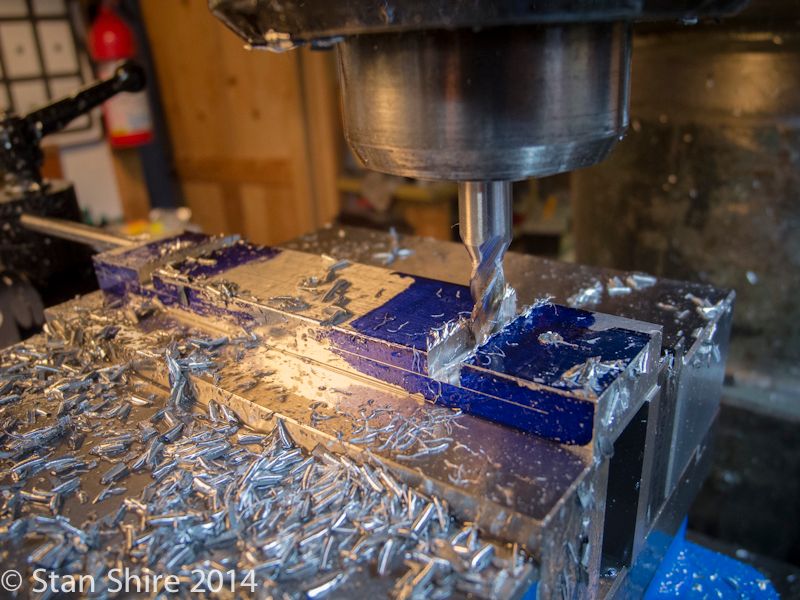
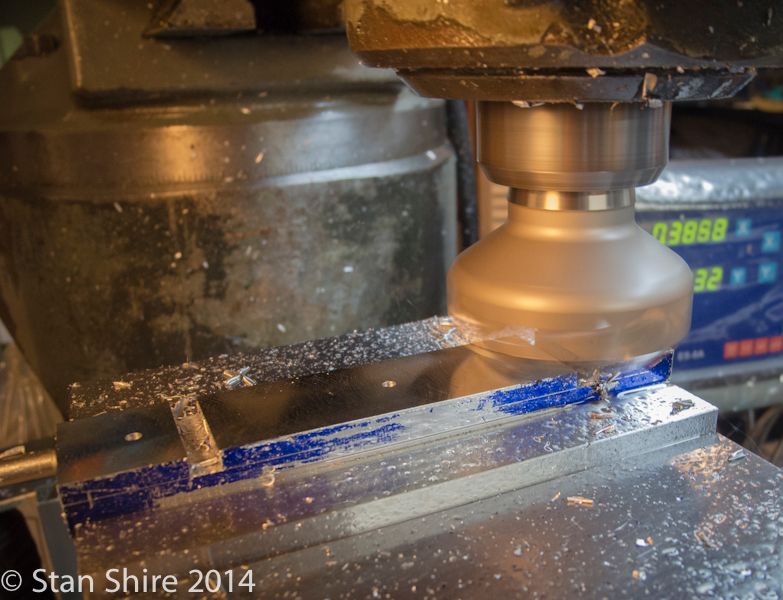
The first two parts done.
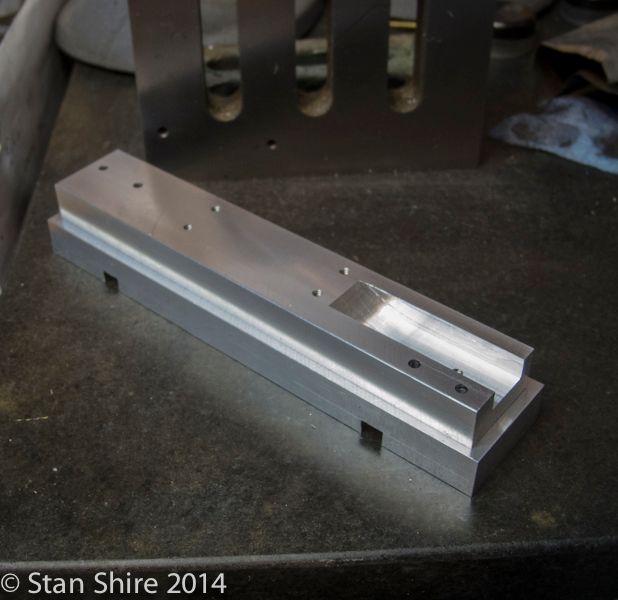
Pull up a chair. The fun never ends.