This is an engine which has always interested me. I think I first seen an engine like this posted by Tel from Australia. I was bored today, so I thought I would begin sussing out a design for one, built from bar stock. The one in this post has 1" bore cylinders with a 1.732" stroke. The flywheel is almost 4" in diameter (I am still trying to find a way to use those two steel rings I made up for the Kerzel. They didn't work out on the Kerzel, but they may do fine here.) Stay tuned, and as the design develops I will posted updated models.
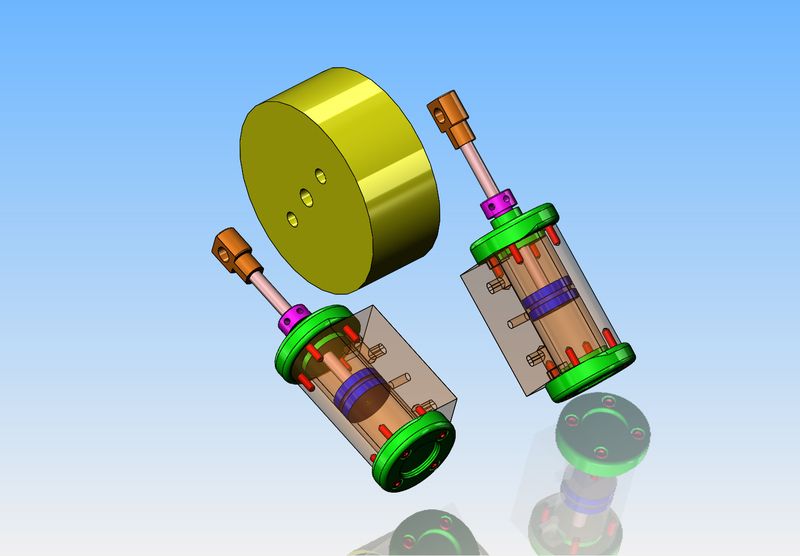