rake60
Well-Known Member
- Joined
- Jul 8, 2007
- Messages
- 4,756
- Reaction score
- 126
They needed a fixture at work to accurately mic the distance from an OD fit to the top of a flange
on a part we manufacture.
The print they gave me was a solid piece with a 7/8" deep groove in the face, leaving an approximately
5/8" pin in the middle with the larger ID being just under 1-3/4" The top face of the ring and pin
must be perfectly flat and at the exact same height.
I do not have the tooling to cut a groove that deep at those diameters, so I cheated.
I made it a two piece assembly.
The outer ring was bored to the specified size, drilled and tapped for 10-24 screws.
The inner part was turned to have a 1/8" stuff to stuff fit to the ring ID, then it was
drilled and the holes countersunk 82° for the heads of the screws.
Bolt it all tightly together.
Then put the assembly back into the lathe to turn the faces flat.
A few quick licks on the surface grinder guaranteed the faces were perfectly in line.
Sure beat trying to fight a groove into a face that deep!
Now they can drop the parts into the fixture and depth mic down to the center pin to check the length.
Rick
on a part we manufacture.
The print they gave me was a solid piece with a 7/8" deep groove in the face, leaving an approximately
5/8" pin in the middle with the larger ID being just under 1-3/4" The top face of the ring and pin
must be perfectly flat and at the exact same height.
I do not have the tooling to cut a groove that deep at those diameters, so I cheated.
I made it a two piece assembly.
The outer ring was bored to the specified size, drilled and tapped for 10-24 screws.
The inner part was turned to have a 1/8" stuff to stuff fit to the ring ID, then it was
drilled and the holes countersunk 82° for the heads of the screws.
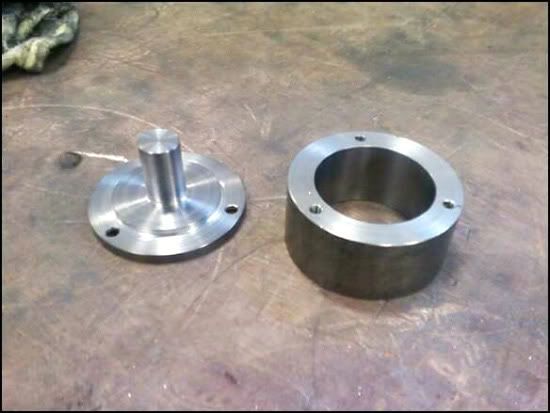
Bolt it all tightly together.

Then put the assembly back into the lathe to turn the faces flat.
A few quick licks on the surface grinder guaranteed the faces were perfectly in line.
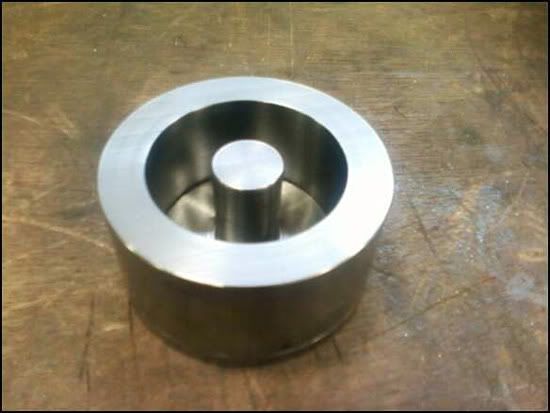
Sure beat trying to fight a groove into a face that deep!
Now they can drop the parts into the fixture and depth mic down to the center pin to check the length.
Rick