Just for the heck of it, here are a couple of shots of the gas tank end stands coming to life. I start with one bar set up in the vice and work from both ends. I have a couple more holes to put in in this set-up, then I will cut them out.
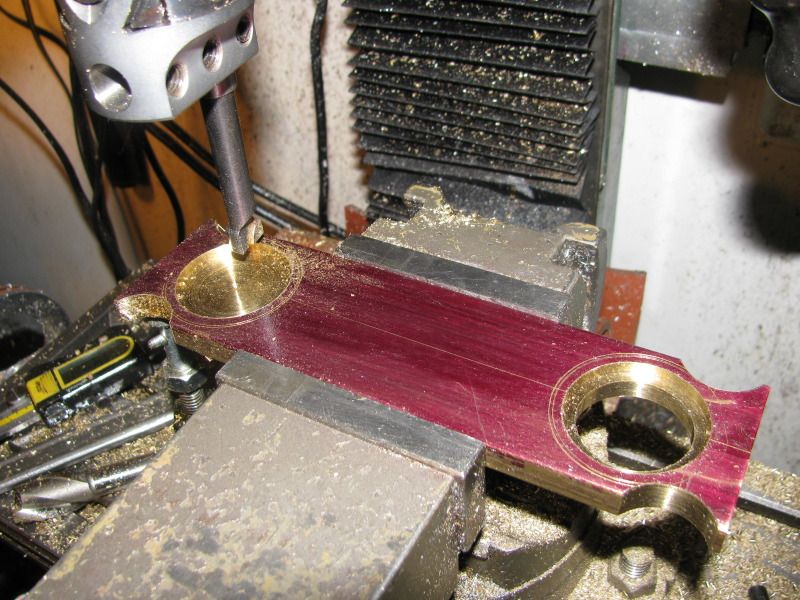
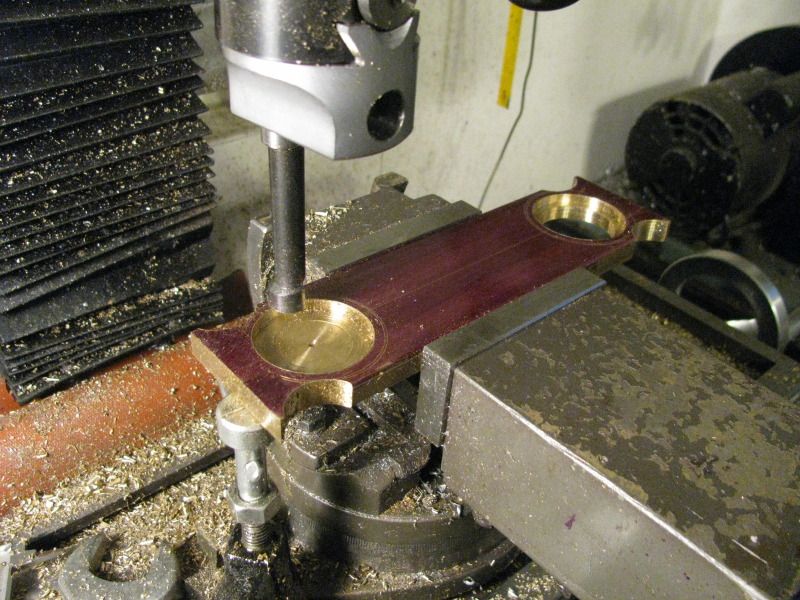
Brian.......do you put side rake on the carbide boring bar for this cut??Just for the heck of it, here are a couple of shots of the gas tank end stands coming to life. I start with one bar set up in the vice and work from both ends. I have a couple more holes to put in in this set-up, then I will cut them out.
![]()
![]()
Hey Brian,Well, here's a beginning. The first thing I notice is that Jan used a 24mm bore, and I only have a 7/8" (22.22mm) reamer. Since I have more faith in my ability to get a good consistent reamed finish than a good consistent bored finish, I THINK I will design this with a 7/8" bore. Jan calls up grey pearlitic cast iron for the cylinder, and since I haven't worked with that before, I may try and use it, depending on cost.
![]()
A gentleman out of USA (I think) emailed me that he had sent me a peice of glass yesterday.I think the two-tone tank goes very well with the rest of the engine. Did you find a source for your glass yet?
Brian
Sorry about your mishap with the tank. I guess these things happen to all of us. Just out of curiosity, what material are you now using for the tank and did you soft solder it?
Vince