After completing the vertical hit and miss engine, I have tried three or four different ways to make the engine go in and out of "hit and miss" no load operation and "only hit-no miss" loaded operation. Some of the things I tried were successful, but they demanded that I be part of the operation. I wanted something totally automatic to do this job, where I wouldn't have to be involved. My absolute best video of the engine doing what I wanted was with the engine turning a winch to raise a load. I have done a great deal of thinking how this could be done without needing me to engage and disengage the winch. So---I'm a bit early into the game here, but far enough to share a concept. Last year I designed and built a mechanism that would reverse a flat belt drive, in order to mimic the reversing of a belt drive from a line shaft. It worked. It was rather crude and "sorta" worked but after making a couple of videos of it in operation it has set on a shelf in my office and never been touched again. However--there was a little bit of magic at work there, because when the lower shaft was driven by a motor, the two semi transparent drums turned in opposite directions. Now, imagine a winch drum that sets between the two outside drums and is not keyed to the shaft. It is actually a bit narrower than the space. Think "dog clutch". If I had a mechanism that would slide the drum to the left or to the right, it would rotate clockwise when forced up against the driven drum on one side, and counterclockwise when it was forced up against the other drum. Now think of two mechanical "bobs" attached to the winch line, that contact an arm at maximum height and forces the moveable winch drum against the opposite driven drum. This reverses the rotation of the winch drum and pays out line until at minimum height the second "bob" contacts the same arm and swings it over against the other driven drum. There won't be enough force to make the faces a friction drive. It will have to be a dog clutch that engages very easily. Will share more with you fellows after I have thought this out a bit more clearly in my head.---Brian
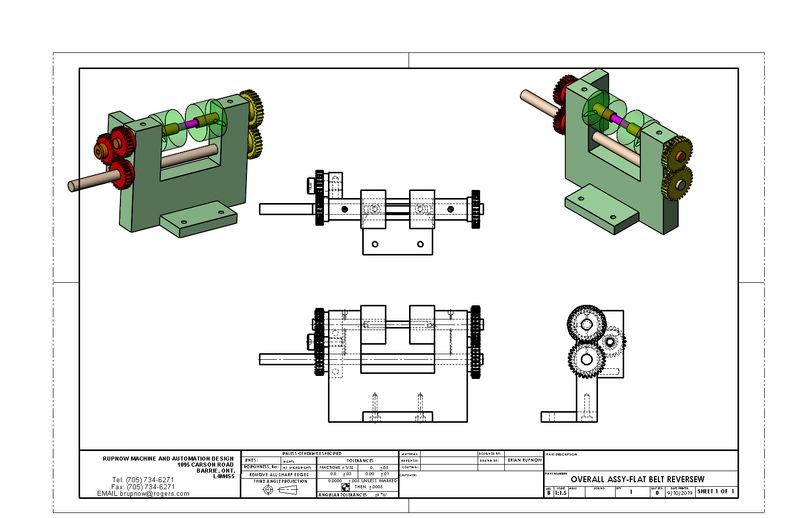