deere_x475guy
Well-Known Member
Babba,
Thanks for your input on this. I am now using a variac for a power supply.
The pc power supply box you see mounted to the top of it is gutted and I have a full wave bridge rectifier mounted to a vary large heatsink inside this. Note that I am only using one transformer out of the gang of 3. It will output around 140 volts and up to 10 amps. The thing is huge and heavy and I will be separating the other two transformers from it soon..
Once I am ready to begin the process I use an anodizing calculator that I downloaded from the net (see sample output below). I input the surface area, after a couple of minutes I get my amp reading that the part is drawing at 15 to 16 volts. In this case it would be 1.8 amps. What I am doing throughout the process now is making small adjustments to the variac to keep the amperage at that initial reading of 1.8 amps throughout the 66 minutes. I read that the voltage must be at least 15 volts to get the pore size correct and the amps control how deep they are. With the battery power supply, and the pc power supply my voltages were always to low, at best maybe 12 volts but the amps were within range...however as you pointed out the amps would drop off and it was a constant recalculating process for the time in the tank. So yes, to get the best possible repeatable results a proper power supply is needed.
The anodizing bath was first mixed at a 1 to 1 ratio. 6 quarts of battery acid to 6 quarts of distilled water. At this ratio and setting the variac to 15 - 16 volts my amps were always higher than what the calculator called for so I was reducing the time needed in the bath by the percentage the amps were over. Last week I added another 2 quarts of battery acid and that seemed to lower the amperage that the parts are drawing at the 15 - 16 volts enough so that I can go by the calculated time.
I am heading to the shop right now to get this next part in. We have some storms moving in our way so I hope we don't loose power when I am half way through the process.
Again thanks for you input. BTW what power supply are you using? Does it allow you to set the voltage and amps separately? Do they stay to your setting throughout the process?
Thanks for your input on this. I am now using a variac for a power supply.
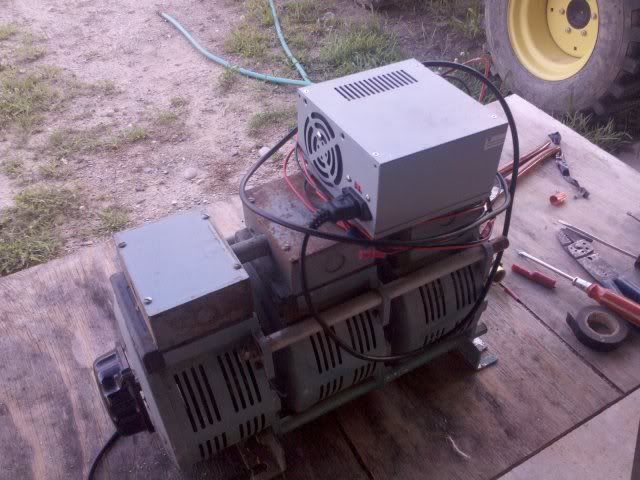
The pc power supply box you see mounted to the top of it is gutted and I have a full wave bridge rectifier mounted to a vary large heatsink inside this. Note that I am only using one transformer out of the gang of 3. It will output around 140 volts and up to 10 amps. The thing is huge and heavy and I will be separating the other two transformers from it soon..
Once I am ready to begin the process I use an anodizing calculator that I downloaded from the net (see sample output below). I input the surface area, after a couple of minutes I get my amp reading that the part is drawing at 15 to 16 volts. In this case it would be 1.8 amps. What I am doing throughout the process now is making small adjustments to the variac to keep the amperage at that initial reading of 1.8 amps throughout the 66 minutes. I read that the voltage must be at least 15 volts to get the pore size correct and the amps control how deep they are. With the battery power supply, and the pc power supply my voltages were always to low, at best maybe 12 volts but the amps were within range...however as you pointed out the amps would drop off and it was a constant recalculating process for the time in the tank. So yes, to get the best possible repeatable results a proper power supply is needed.
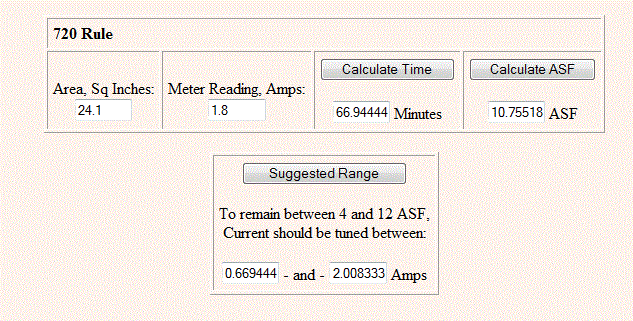
The anodizing bath was first mixed at a 1 to 1 ratio. 6 quarts of battery acid to 6 quarts of distilled water. At this ratio and setting the variac to 15 - 16 volts my amps were always higher than what the calculator called for so I was reducing the time needed in the bath by the percentage the amps were over. Last week I added another 2 quarts of battery acid and that seemed to lower the amperage that the parts are drawing at the 15 - 16 volts enough so that I can go by the calculated time.
I am heading to the shop right now to get this next part in. We have some storms moving in our way so I hope we don't loose power when I am half way through the process.
Again thanks for you input. BTW what power supply are you using? Does it allow you to set the voltage and amps separately? Do they stay to your setting throughout the process?