Kaleb
Senior Member
- Joined
- Jan 3, 2010
- Messages
- 272
- Reaction score
- 27
Now I've got my Wiggins/Coles S.T. running, I have decided to start work on a little steamboat powered by it.
My next door neighbour gave me this part finished hull and prop shaft to use as the basis for the build. The hull will need some work to get it watertight, but the prop shaft is good to go. I'll also be building the boiler. I'm thinking of using a flexible coupling between the engine and prop shaft to give a bit more leeway when it comes to mounting the engine. I'm currently thinking of using either a universal joint or a beam coupling, but I'm not sure which would be best. I know of the method of using a piece of silicone tubing, but I think it would be better to use a proper coupling.
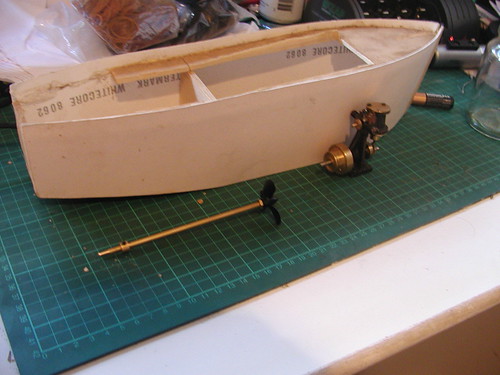
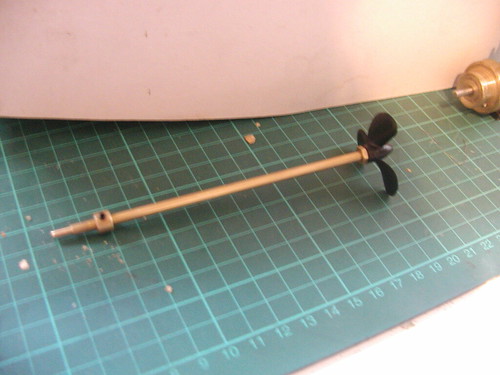
My next door neighbour gave me this part finished hull and prop shaft to use as the basis for the build. The hull will need some work to get it watertight, but the prop shaft is good to go. I'll also be building the boiler. I'm thinking of using a flexible coupling between the engine and prop shaft to give a bit more leeway when it comes to mounting the engine. I'm currently thinking of using either a universal joint or a beam coupling, but I'm not sure which would be best. I know of the method of using a piece of silicone tubing, but I think it would be better to use a proper coupling.