Let me start out by saying that I have made my own piston rings in the past---and failed dismally. I was so disheartened by my failed attempt that I went to Viton o-rings and never looked back. Now I have ten or twelve years engine building experience, and I am going to try again. I have a 1" bore side shaft engine which I built a few years ago with a Viton ring, and it runs very good, and has incredible compression. I have chosen this engine because I can undo the con-rod bolts and remove the piston without disturbing any of the other engine settings. This will require that I machine a new piston and two rings.
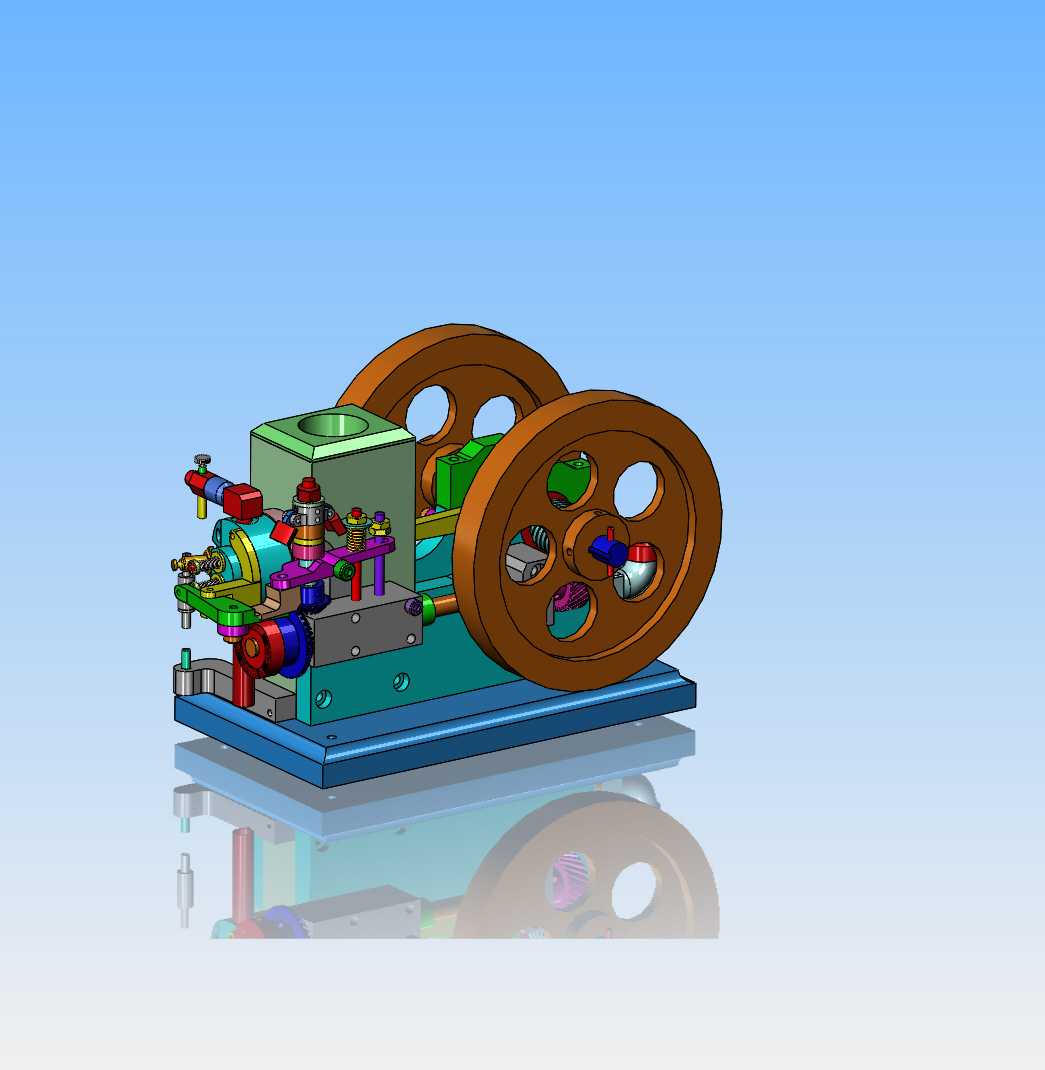