And this is all the work I'm going to do today. The brass has been sized to fit into the groove in the top of the rotor and glued in there with J.B. Weld. Tomorrow I will see whether or not the J.B. Weld is going to stick to the rotor.
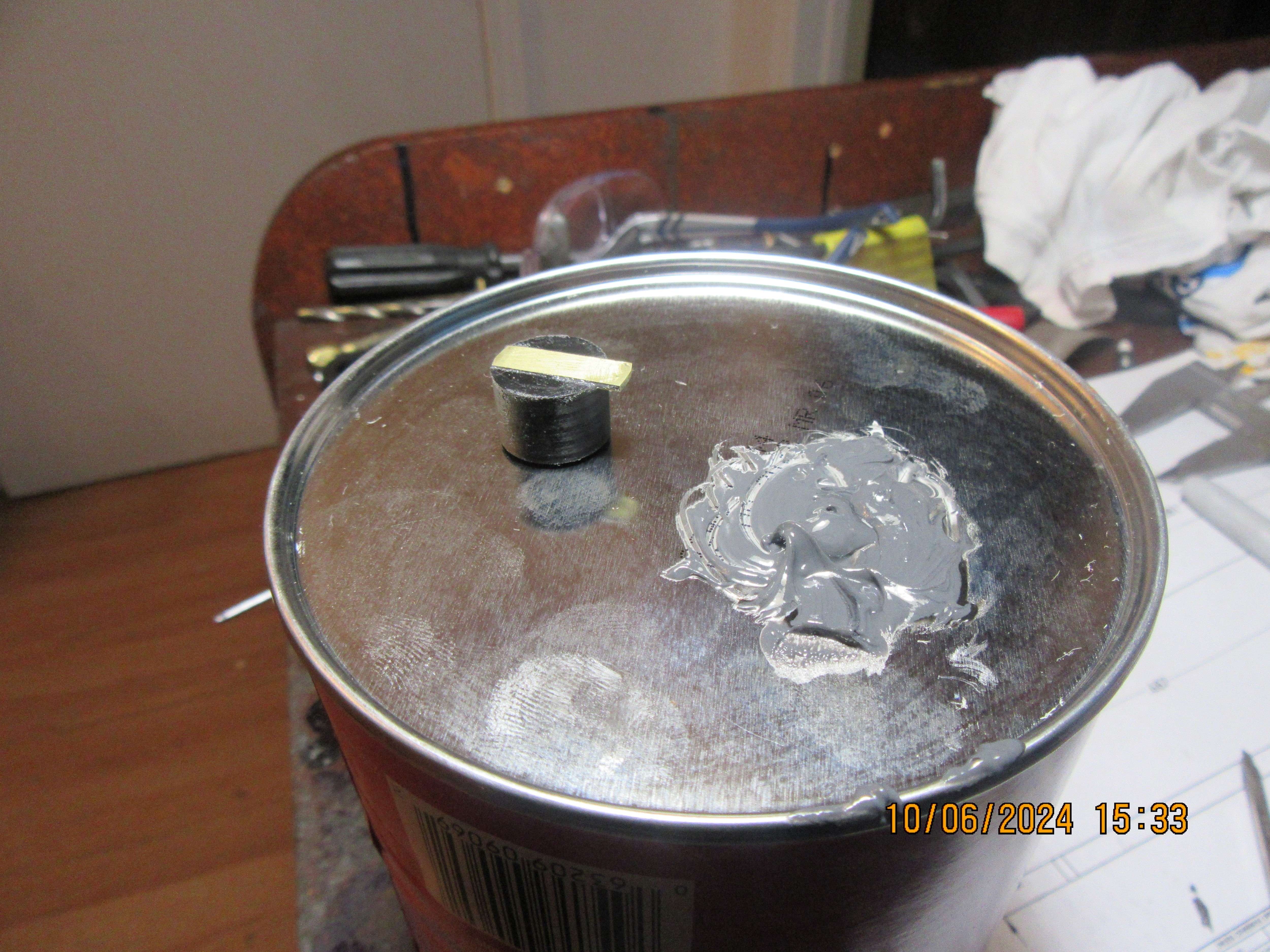
Yes. Roy has retired to some extent, and now it is being carried on by a new fellow. Nice guy. He knows the ignition systems.S/S had what you ar3e looking for but he has retired. Apparently someone else has taken over the business
https://www.cncengines.com/index.html
I have been using TPU. Somewhat flexible but still pretty rigid. The ones that I have made do work.You can buy more flexible filement but would have to find a use for the other 99% of the drum
Hi Roy--I need two of the 90 degree sparkplug boots for the engine I am currently building. The sparkplugs are very small 1/4"-32 plugs (I may have bought them from you) the porcelain measures 0.180" diameter x 0.350" long and the brass part on top of the porcelain measures 0.160" diameter x about 0.10" long. I will need sparkplug wires 4" long attached to each boot----I will look after terminating the other end of the wires. Please shoot me a price for this [email protected] -Brian RupnowBrian, I do still have some of those 1/4-32 boots. Also, Dan has had the large CM-6 clips made and I think he is also working on the 1/4-32 clips. I still have the die set from Bruce Satra for the small 10-40 plugs which will be available to Dan. We were concentrating on the CDI but I will make anything available that Dan would like to keep in stock. All of the Satra distributor parts are still available. I've retired so I can get some engines built, so far without much success, but I'm not planning on going away any time soon. I'll be at the 2024 Indiana Show this year.
Roy
Enter your email address to join: