- Joined
- Jul 16, 2007
- Messages
- 3,047
- Reaction score
- 1,159
Last year I had built a tubing bender for tubing up to .312 diameter. The design of the V-twin necessitated a new bender capable of bending .375 tubing. As this one didn't need to be universal like the other one I made some quick sketches and started cutting. I decided to make the radius plate out of aluminum. The bending arms would be steel with an aluminum filler block. The clamping block and the forming die would be made from steel. I didn't go to extra pains with this because I mainly had to see if it was going to work first. There's always time to pretty it up. The first couple of pictures are just layout and squaring up the radius plate.
The next step was to pick up the edges with the edge finder so that I could drill all the holes, mostly .25 with a .50 hole for the pivot shaft.
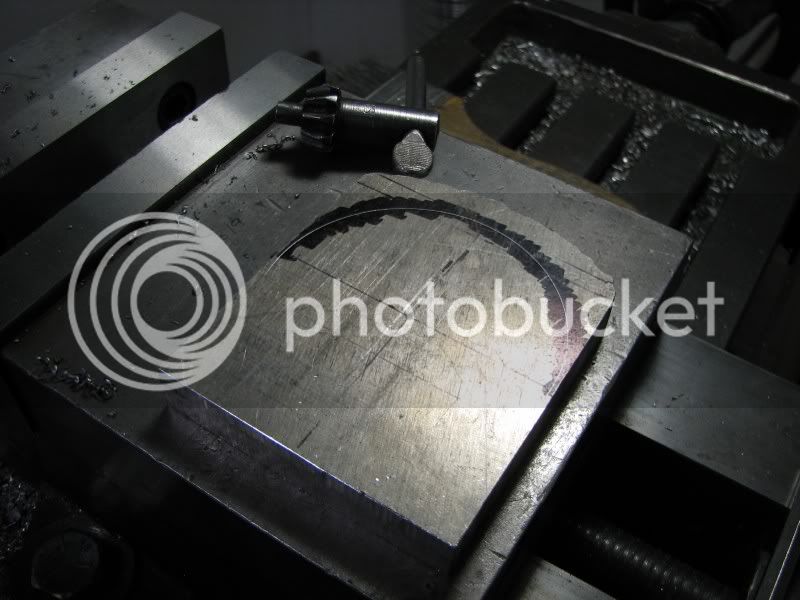
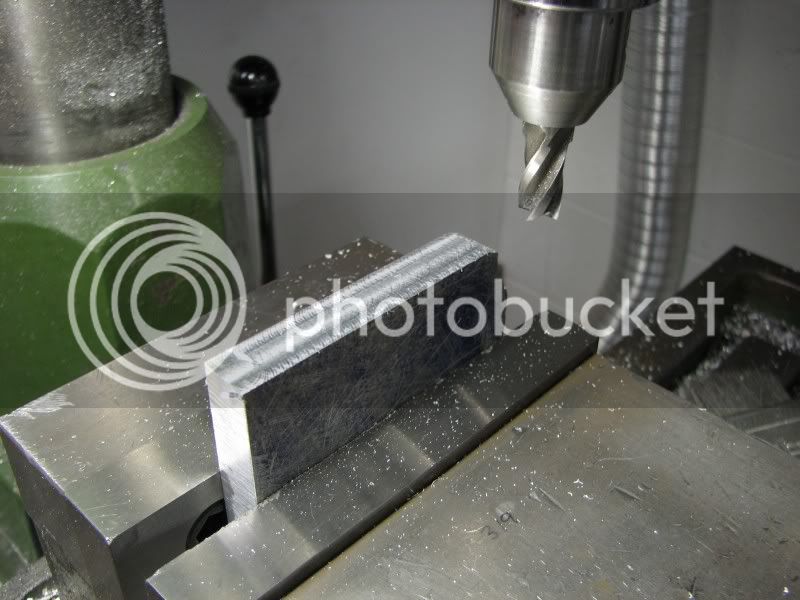
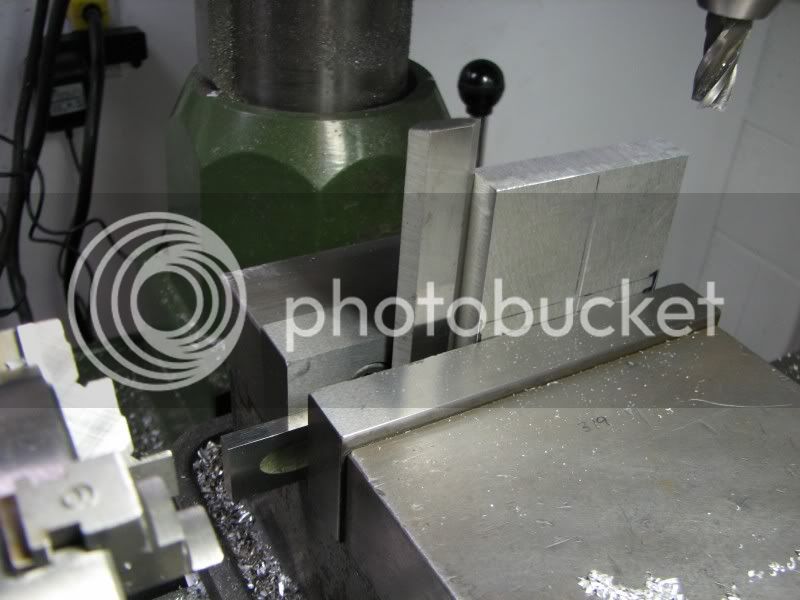
The next step was to pick up the edges with the edge finder so that I could drill all the holes, mostly .25 with a .50 hole for the pivot shaft.
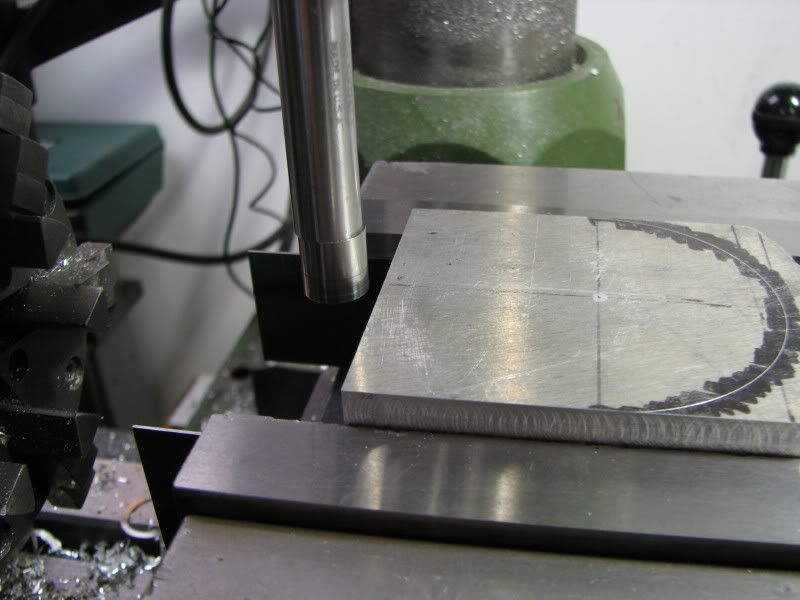
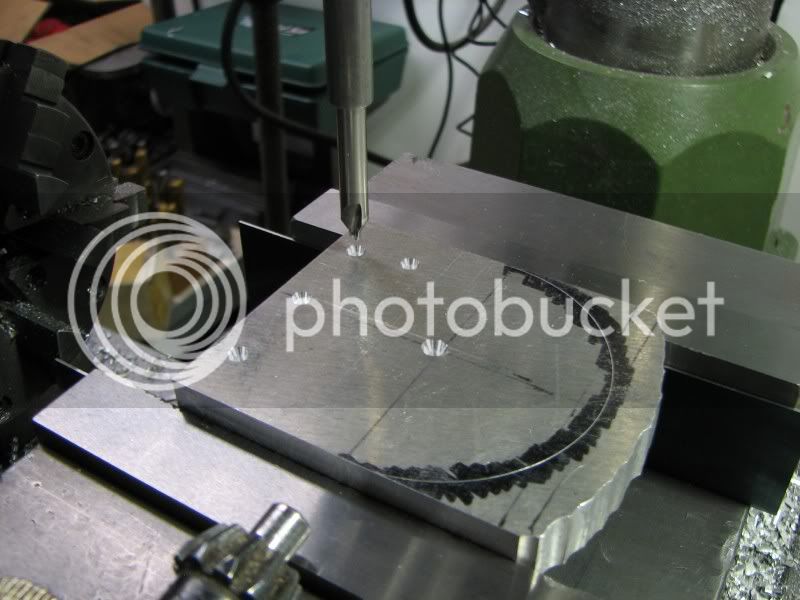
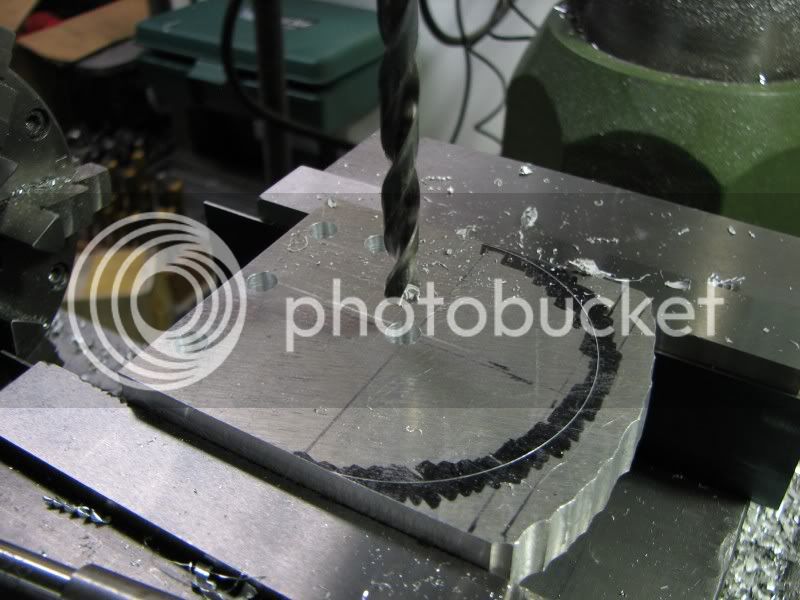
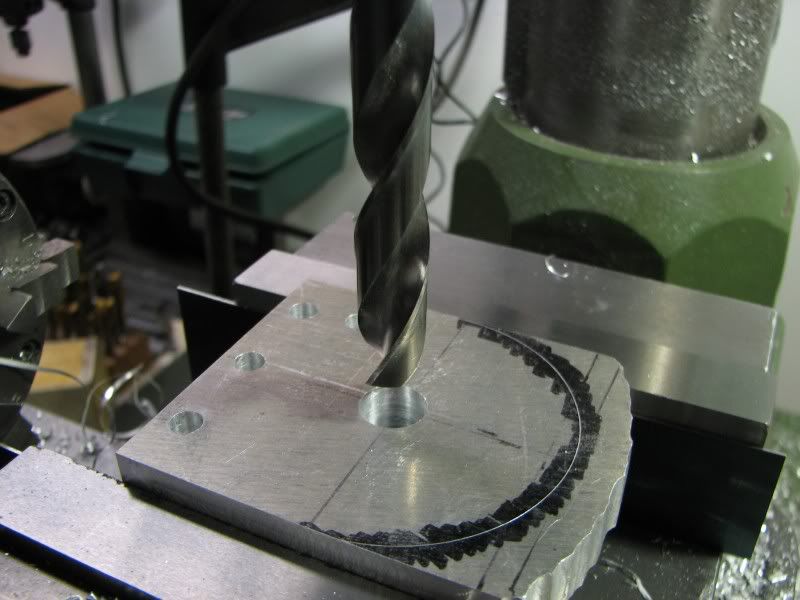