Years ago started on making a 4 cylinder T-head engine called Simplex. Didn't get all the castings. Main ones missing were the 4 con rods. Wanting to do lost wax casting thought it would be a good place to start. This is my second try, first try didn't allow for shrinkage in the rubber mold and in the metal plus couple other things I did wrong. Mostly finished a new model of the rod that is 6 percent bigger then hopefully the finished size will be. Shrinkage of 3 to 4 percent for the rubber and about 1 and half percent for the metal.
The model is made up of 11 pieces silver brazed together. Didn't get all the seams silver soldered so hope to redo tomorrow without destroying it. Then hopefully vulcanize rubber mold of the model tomorrow. From the rubber mold wax patterns will be made.
The model is made up of 11 pieces silver brazed together. Didn't get all the seams silver soldered so hope to redo tomorrow without destroying it. Then hopefully vulcanize rubber mold of the model tomorrow. From the rubber mold wax patterns will be made.
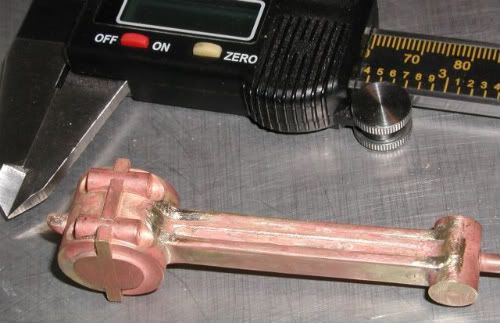