Today I'm learning all about trembler coils. Perhaps more than I ever wanted to know!! I have everything hooked up, electric starter, engine, and trembler coil. The trembler coil fires the sparkplug like crazy ---but only when the engine first begins to rotate, or when the engine is coasting to a stop. However, it doesn't want to fire the sparkplug while the engine is turning at a higher rpm. Okay, that's weird!!! My best guess is that this failure to perform at higher rpm has something to do with the amount of flat that I have on the cam. Damn!! I thought this was going to be easy. This coil fires when the points first MAKE contact, opposite to a conventional points and coil system which fires the coil when the points BREAK contact. Right now, the cam has a flat on one side only, as shown in the attached model. MAYBE I have to make the flat area on the cam extend part way around the 360 degree body of the cam so the system has a longer "dwell" with the points in contact with each other.
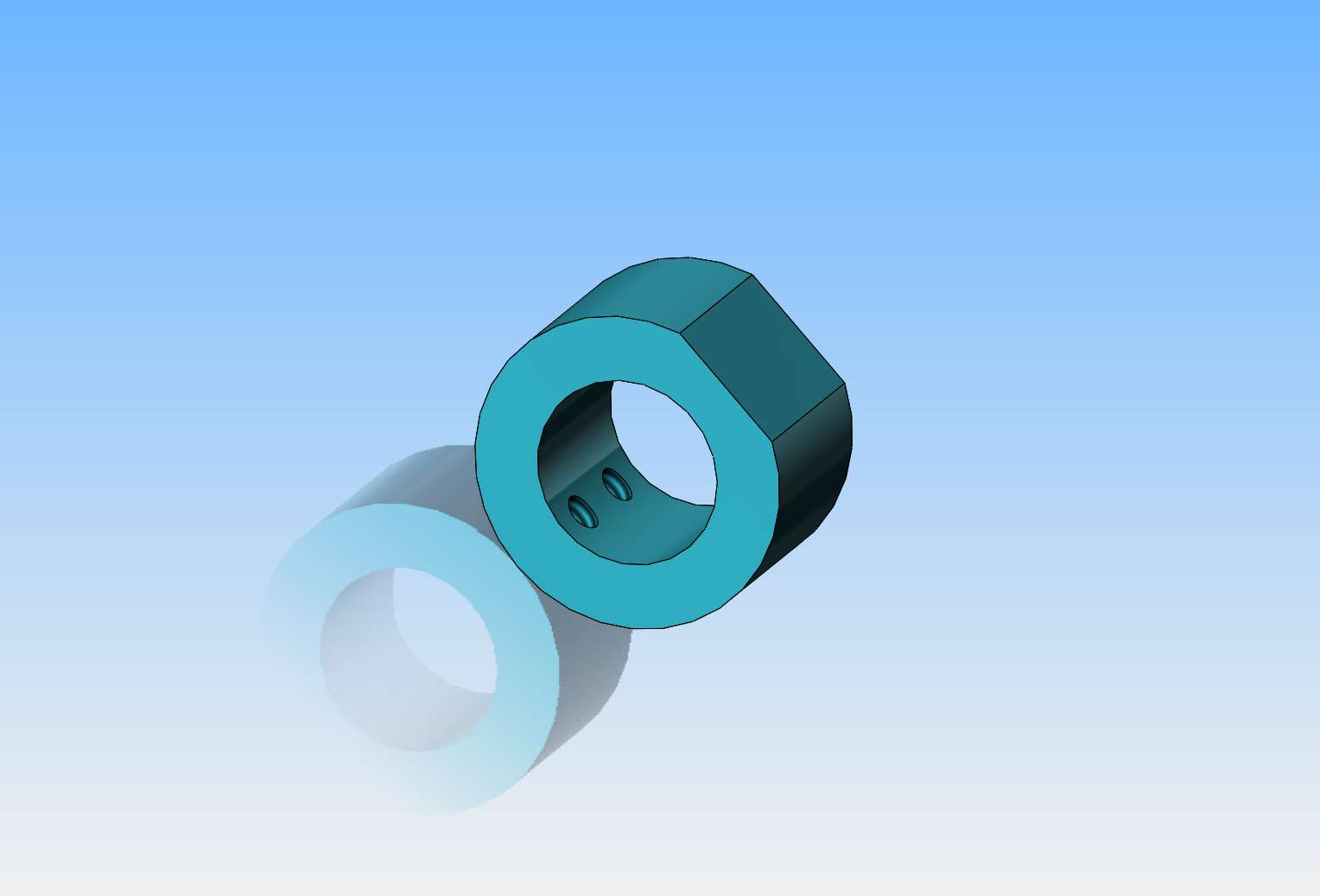