This is going to be something a bit different. Most of you will have a fairly good knowledge of how a hit and miss engine runs. On a hit and miss engine, the governor disables the exhaust valve when the pre-set rpm is surpassed, holding the exhaust valve open and letting the engine coast until the engine slows down, at which point the governor allows the exhaust valve to close and the engine will once more be able to build compression and fire. However, there is a different way of governing an engines speed for engines which are not "hit and miss" types. In this type of governing, the governor opens and closes the butterfly valve in the carburetor to adjust the engine speed. In a perfect world, you "dial in" the speed at which you want the engine to run. If the engine speed slows beyond that point, a linkage from the governor opens the butterfly valve in the carburetor and admits more air/fuel mix to bring the engine back up to the "dialed in" rpm setting. If the engine rpm exceeds the "dialed in" speed setting, the governor closes the butterfly valve, thus starving the engine for fuel until it slows down to the dialed in rpm. I have a twin cylinder opposed engine that I built a few years ago, which has a manually controlled butterfly valve in the carburetor. I also have a governor which was salvaged from the very first "hit and miss" engine which I designed and built. (The engine ran, but was horribly unbalanced). Over the course of the next few weeks, I am going to try and "marry" the two bits of technology to end up with a "throttle controlled" engine. Follow along. It should be interesting.---Brian
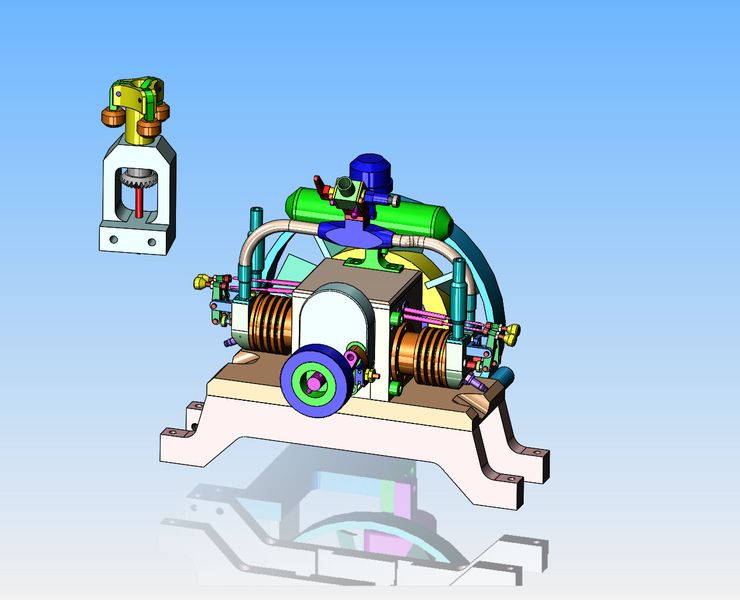