BobWarfield
Well-Known Member
- Joined
- Dec 27, 2007
- Messages
- 1,151
- Reaction score
- 1
The ubiquitous HF tool grinders are handy beasts around the shop. I've been very happy with mine. Periodically, folks like John Stevenson have been on about how to use a universal vise to make a simple T&C grinder out of one so you can sharpen you end mills and drill bits.
Here is the HF grinder I refer to:
I've followed the discussions with interest, but never done much more about it. I know some fellows have made some pretty nifty attachments along these lines. But recently I came across some great videos on YouTube that show how to use one of the Asian Deckel clones to sharpen lathe tools, end mills, and drill bits. Here is one such:
[ame]http://www.youtube.com/watch?v=CkYVUy7hmDk[/ame]
This video really got me thinking. That tool holder pivoting on the rail sure looks like this other thing I have had sitting in my shop:
Yep, it's an "800watt" universal vise, readily available on eBay for circa $60. You can make one too--Mcgyver welded up a very pretty one and posted up pix on another board.
So here is my "artists concept" of how to put that HF grinder together with a universal vise to do this kind of sharpening:
The universal vise is mounted to a precision rod that can pivot to stroke the tool against the grinding wheel. The universal vise allows precise control of the angle of the plane at which the tool which sweep the grinder face when the assembly is pivoted. The depth of cut is adjustable with the threaded rod that bears on the end of the shaft. The adjusting rod is mated to a ball bearing pressed into the shaft end. This way the shaft can be rotated for the tool grinding without turning the adjustment rod and move the tool holder left or right.
The shaft itself is held in bronze bushings. For endmill sharpening, one could mount a precision air bearing in the tool holder and go from there.
This sort of accessory looks relatively easy to build, and I don't know why it wouldn't be capable of results very similar to a commercial grinder of this type.
Note that this style of grinder can't do everything. There are grinders with more sophisticated geometries that are more versatile. The T&C community endlessly debates the merits of the various exotic specimens such as the Quorn and others. My focus was to find something fairly cheap and easy to build that could take care of a lot of the more common operations.
I don't have time to try building one at the moment, but it's on my list, and I keep a page about it on my site here:
http://www.cnccookbook.com/CCBDToolGrinder.htm
I call it the "Beijing Deckel" for obvious reasons! :big:
Here is the HF grinder I refer to:
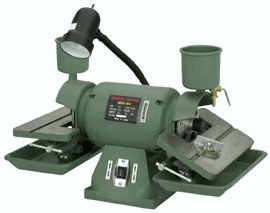
I've followed the discussions with interest, but never done much more about it. I know some fellows have made some pretty nifty attachments along these lines. But recently I came across some great videos on YouTube that show how to use one of the Asian Deckel clones to sharpen lathe tools, end mills, and drill bits. Here is one such:
[ame]http://www.youtube.com/watch?v=CkYVUy7hmDk[/ame]
This video really got me thinking. That tool holder pivoting on the rail sure looks like this other thing I have had sitting in my shop:
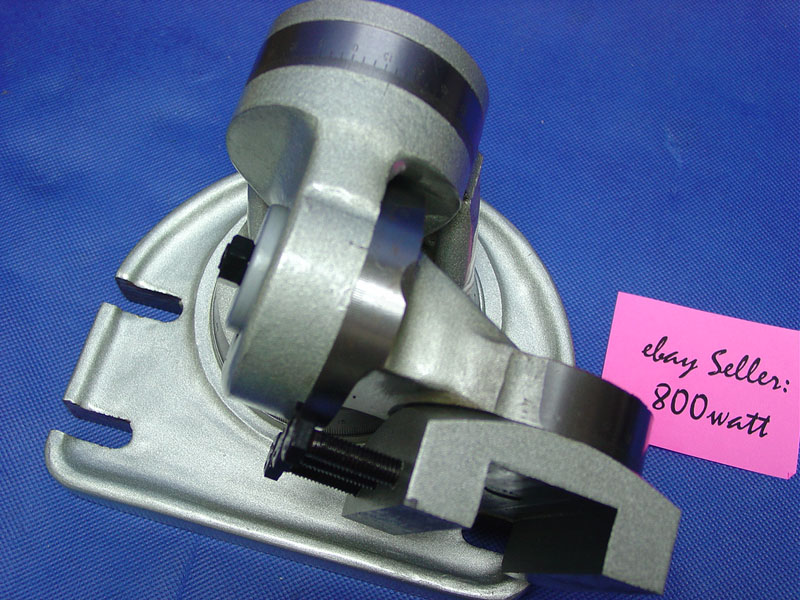
Yep, it's an "800watt" universal vise, readily available on eBay for circa $60. You can make one too--Mcgyver welded up a very pretty one and posted up pix on another board.
So here is my "artists concept" of how to put that HF grinder together with a universal vise to do this kind of sharpening:
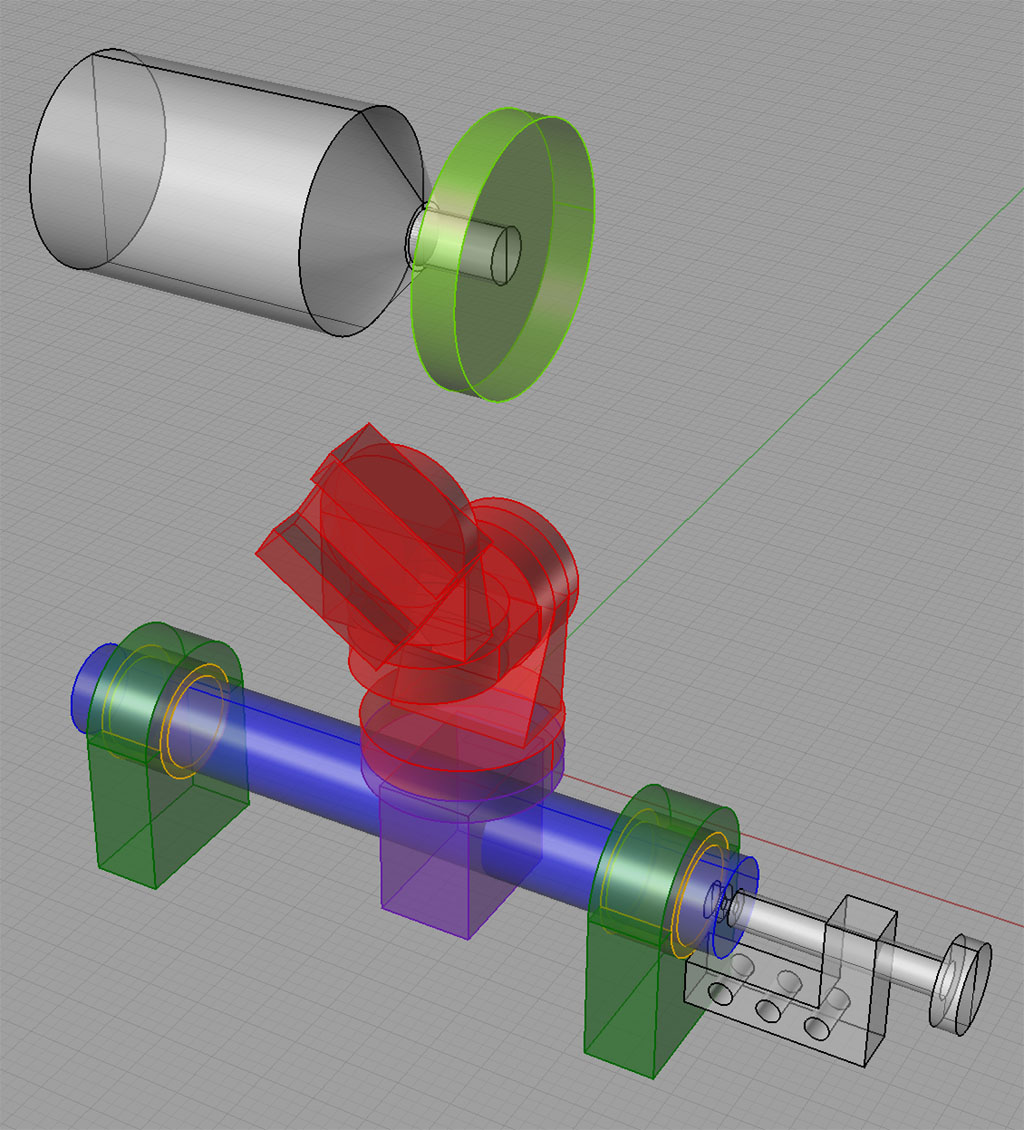
The universal vise is mounted to a precision rod that can pivot to stroke the tool against the grinding wheel. The universal vise allows precise control of the angle of the plane at which the tool which sweep the grinder face when the assembly is pivoted. The depth of cut is adjustable with the threaded rod that bears on the end of the shaft. The adjusting rod is mated to a ball bearing pressed into the shaft end. This way the shaft can be rotated for the tool grinding without turning the adjustment rod and move the tool holder left or right.
The shaft itself is held in bronze bushings. For endmill sharpening, one could mount a precision air bearing in the tool holder and go from there.
This sort of accessory looks relatively easy to build, and I don't know why it wouldn't be capable of results very similar to a commercial grinder of this type.
Note that this style of grinder can't do everything. There are grinders with more sophisticated geometries that are more versatile. The T&C community endlessly debates the merits of the various exotic specimens such as the Quorn and others. My focus was to find something fairly cheap and easy to build that could take care of a lot of the more common operations.
I don't have time to try building one at the moment, but it's on my list, and I keep a page about it on my site here:
http://www.cnccookbook.com/CCBDToolGrinder.htm
I call it the "Beijing Deckel" for obvious reasons! :big: