Powder keg
Well-Known Member
- Joined
- Oct 10, 2007
- Messages
- 1,091
- Reaction score
- 3
Well, I decided to see if I could figure out this crazy cam ring. It took me a bit to get my head around it and figure out how to draw it. But I think everything turned out OK? I printed it out and scanned the image. Here it is. From this I have a piece of aluminum plate that I can make one of these 3X bigger
)
I just have to scale it up and do a toolpath on it. I drew it up with Mastercam. The hard part was the line that the rollers roll on. I had a heck of a time getting it tangent with the rollers.
Later, Wes
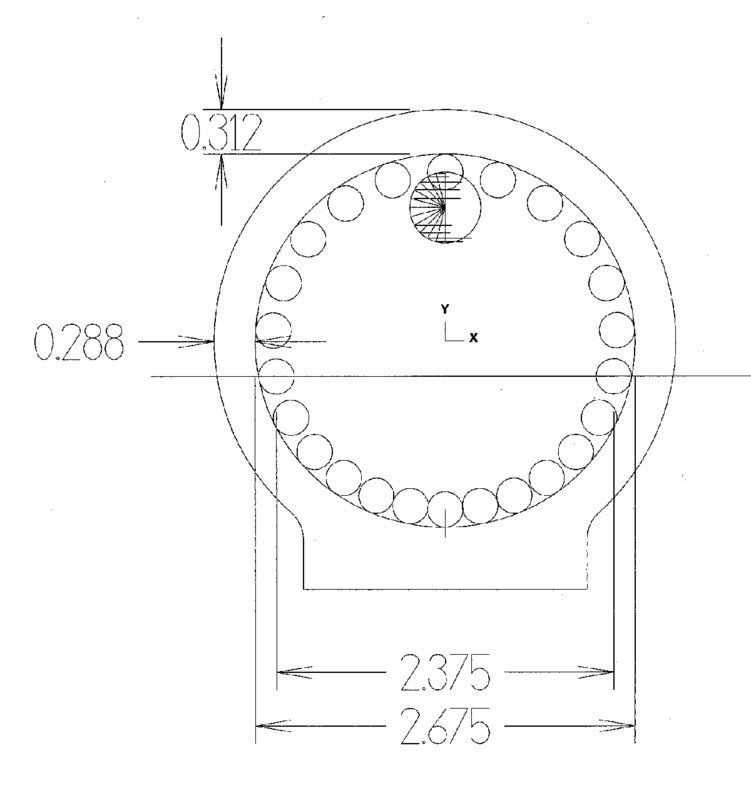
I just have to scale it up and do a toolpath on it. I drew it up with Mastercam. The hard part was the line that the rollers roll on. I had a heck of a time getting it tangent with the rollers.
Later, Wes