dparker
In Rembrance 8/2021
- Joined
- Aug 24, 2007
- Messages
- 218
- Reaction score
- 5
Marv: You did it to me again---I saw your tooling and just had to make something like it.
I already had the plate to go on the tailstock ram but was never satisfied with how to mount my magnetic base dial indicator and ended up with it on the carriage or some other flimsy setup. When I saw your dial indicator mounted on the tailstock casting I started to think of how I could do that on the round casting on my lathe. I ended up using a "General" mag base that I had set up to hold a deflector that I rarely used and it sits quite securely on the round casting, made a indicator mount out of some aluminum angle and it looks like it will work nicely.
With all the talk about collets I made a holder above my lathe out of PVC pipe and used a #3 morse taper reamer to make them seat securely. I ended up hot gun glueing the PVC to the angle iron. A spindle thread cover for safety is at the right of the rack with a roll pin to insert in one of the holes if it becomes too tight on the threads to undo by hand.
At this rate of trying to adapt your ideas on tooling to use on my machines I may never get more engines built. Keep showing your special tooling, I really like your ideas and ingenuity of solving some of the little problems that seem to keep coming up.
Thank You--but alas I'm beginning to need more tool boxes---don
I already had the plate to go on the tailstock ram but was never satisfied with how to mount my magnetic base dial indicator and ended up with it on the carriage or some other flimsy setup. When I saw your dial indicator mounted on the tailstock casting I started to think of how I could do that on the round casting on my lathe. I ended up using a "General" mag base that I had set up to hold a deflector that I rarely used and it sits quite securely on the round casting, made a indicator mount out of some aluminum angle and it looks like it will work nicely.
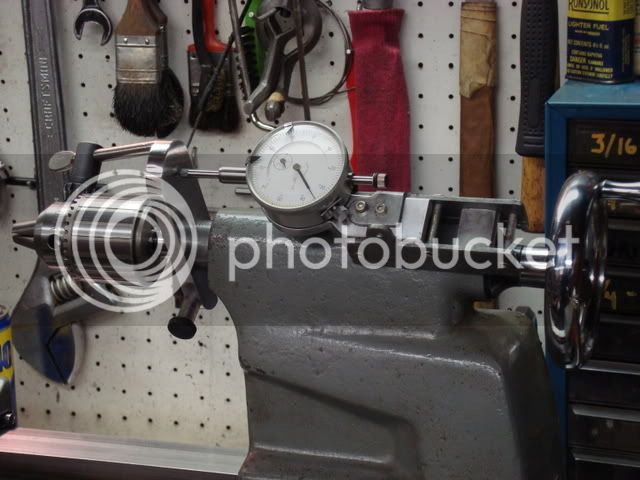
With all the talk about collets I made a holder above my lathe out of PVC pipe and used a #3 morse taper reamer to make them seat securely. I ended up hot gun glueing the PVC to the angle iron. A spindle thread cover for safety is at the right of the rack with a roll pin to insert in one of the holes if it becomes too tight on the threads to undo by hand.
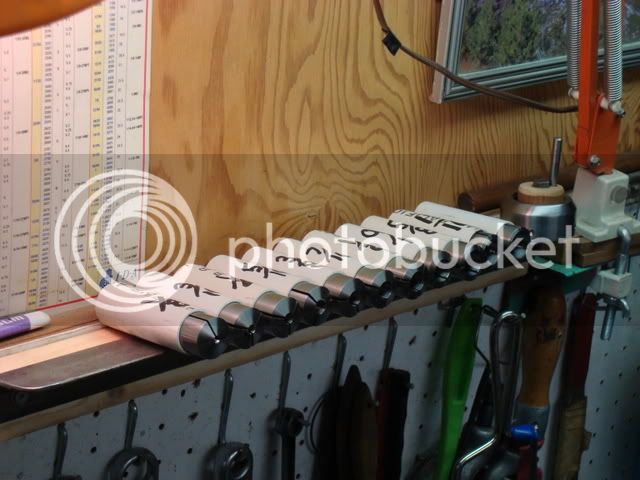
At this rate of trying to adapt your ideas on tooling to use on my machines I may never get more engines built. Keep showing your special tooling, I really like your ideas and ingenuity of solving some of the little problems that seem to keep coming up.
Thank You--but alas I'm beginning to need more tool boxes---don