DavesWimshurst
DavesWimshurst
- Joined
- Dec 7, 2008
- Messages
- 102
- Reaction score
- 3
I built this Stirling engine for a friend. It's to J. Senft's design with some changes to use available materials. I had some acrylic tubing with surface damage that could be machined thinner to make the displacer cylinder. The power cylinder is a modified "Airpot" a commercially made dashpot using a glass cylinder and graphite piston. My friend placed it under a glass dome with a small electric heating pad set at a very low setting, it also will run on the heat of ones hands. It has been running continuously 24-7 for the last four years.
I made another engine that gets much use as a demo:
Another view for you flywheel fans: :hDe:
And my first one that keeps my TV company:
This engine most closely follows the original plans. For the displacer cylinder I heated a strip of 3/8 " acrylic sheet in my kitchen oven until it was flexible. (About 275 deg F IICR) Using hot pads I bent it into a rough circle shape. I trimmed the ends and reheated it to get the ends to match and glued the joint with thin acrylic solvent cement. (The nasty methylene chloride stuff) This gave a crude thick walled ring from which I machined the final cylinder. The joint hardly shows in the finished part. The machining sequence was to first bore the interior holding the ring in the four jaw chuck. A disk of thick plywood screwed to a faceplate was turned down to make an arbor to hold the part while finishing the outside to size. While laborious Dr Senft suggested machining the thin walled cylinder from a solid one inch thick slab of acrylic. :wall: I used what I had.
Dave
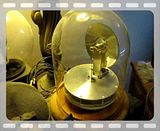
I made another engine that gets much use as a demo:
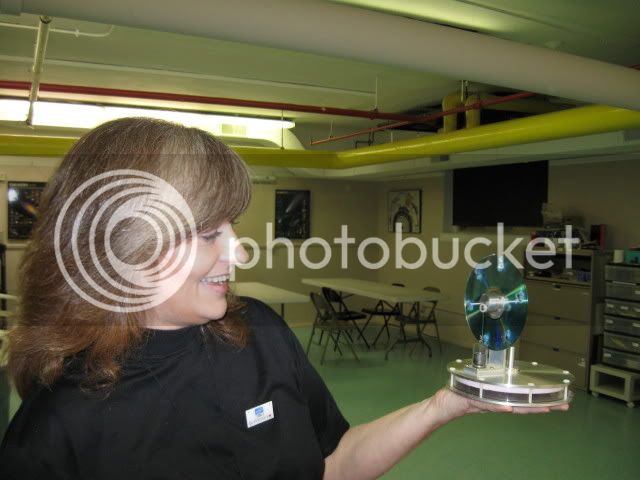
Another view for you flywheel fans: :hDe:
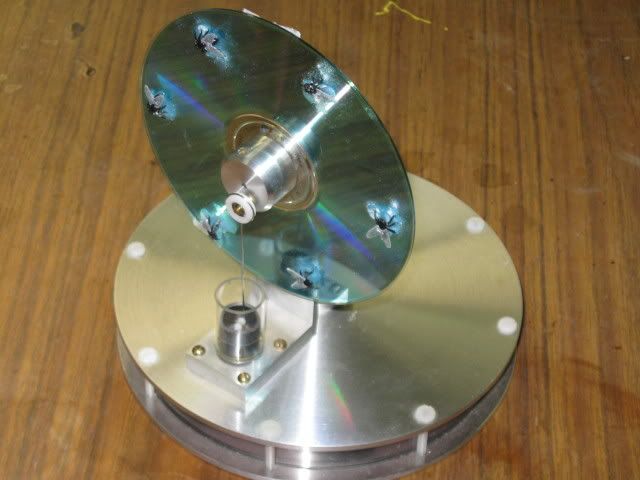
And my first one that keeps my TV company:

This engine most closely follows the original plans. For the displacer cylinder I heated a strip of 3/8 " acrylic sheet in my kitchen oven until it was flexible. (About 275 deg F IICR) Using hot pads I bent it into a rough circle shape. I trimmed the ends and reheated it to get the ends to match and glued the joint with thin acrylic solvent cement. (The nasty methylene chloride stuff) This gave a crude thick walled ring from which I machined the final cylinder. The joint hardly shows in the finished part. The machining sequence was to first bore the interior holding the ring in the four jaw chuck. A disk of thick plywood screwed to a faceplate was turned down to make an arbor to hold the part while finishing the outside to size. While laborious Dr Senft suggested machining the thin walled cylinder from a solid one inch thick slab of acrylic. :wall: I used what I had.
Dave