rake60
Well-Known Member
- Joined
- Jul 8, 2007
- Messages
- 4,756
- Reaction score
- 125
I'm setting up a secondary machining division where I work.
It's kind of a "figure it out as you go venture" but it's coming along.
We needed to make some spring loaded mandrels to insert the raw parts into
the machine collet from the turret of these old production machines.
So, I was sent home from work this morning to work in my hobby shop,
AND get paid for it!
Parts turned out fine with no remakes.
I still need two more heavy washer, but the machining is all done.
The assembled overall lengths are all within .004" I can live with that.
I knew these were coming up so I had ordered a new QCTP and proper parting tool to do them.
Those will be here next Monday, a little too late... :
The parting tool I had to use is kind of rough.
It was hand ground from a piece of 7/16 tool steel about 3 years ago.
I didn't sharpen it, just shimmed it to center and used it.
It parted off 9 parts right to length every time.
It was pretty noisy at times and the finishes needed some polishing up, but I was impressed.
Now I'm wondering if I can figure out how to use a "REAL" cutoff blade when it gets here.
Rick
It's kind of a "figure it out as you go venture" but it's coming along.
We needed to make some spring loaded mandrels to insert the raw parts into
the machine collet from the turret of these old production machines.
So, I was sent home from work this morning to work in my hobby shop,
AND get paid for it!
Parts turned out fine with no remakes.
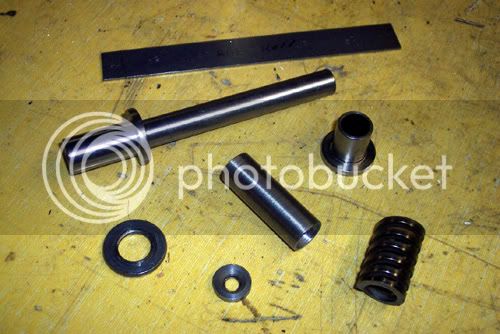
I still need two more heavy washer, but the machining is all done.
The assembled overall lengths are all within .004" I can live with that.
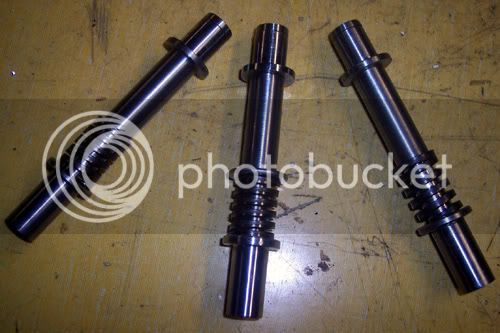
I knew these were coming up so I had ordered a new QCTP and proper parting tool to do them.
Those will be here next Monday, a little too late... :
The parting tool I had to use is kind of rough.
It was hand ground from a piece of 7/16 tool steel about 3 years ago.
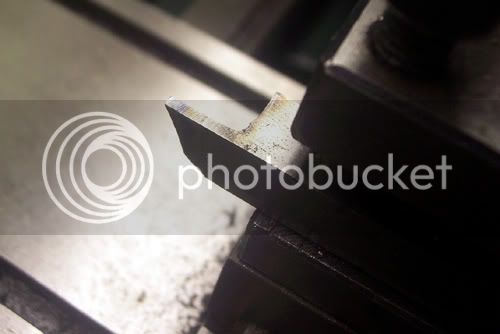
I didn't sharpen it, just shimmed it to center and used it.
It parted off 9 parts right to length every time.
It was pretty noisy at times and the finishes needed some polishing up, but I was impressed.
Now I'm wondering if I can figure out how to use a "REAL" cutoff blade when it gets here.
Rick