Many of you folks will know about pin vices, (also called finger chucks) but some are not aware they exist. This set of four cost me $30 including tax. They will hold round diameters from 3/64" (0.047") up to and including 3/16" (0.1875"). They are the perfect thing for lapping small valves into seats on model engines. As you can see, the part which you hold between your thumb and finger are knurled, and are small (-1/4") The chuck end on them is also relatively small, which means that you can grip the stem of an intake valve to lap it without having to remove the exhaust valve to get room to do it. (or vice-versa). When I make valves I turn them from cold rolled steel with a 92 degree included angle, and make the valve seats from brass with a 90 degree included angle. Then I insert the valve into it's guide and using first #300 grit and then 600 grit lapping paste I grip the stem of the valve in the appropriate pin vice, and while applying mild pressure of valve into seat I spin the pin vice back and forth between my thumb and finger. I generally put some #300 compound on the face of the valve, then spin it back and forth ten times, lift it up and turn it 90 degrees, and repeat another set of ten, until I reach a total count of 100. Then wipe off all of the compound and repeat with #600 grit compound. This will not give a wide contact area on the valve face where it fits against the seat, but it will give a very good air tight seal, which is all you need.-Be sure not to get any compound on the stem of the valve because you don't want the valve to be sloppy in it's guide.--And---never ever try and lap valves with a power tool. This must be done manually, with finger power only.
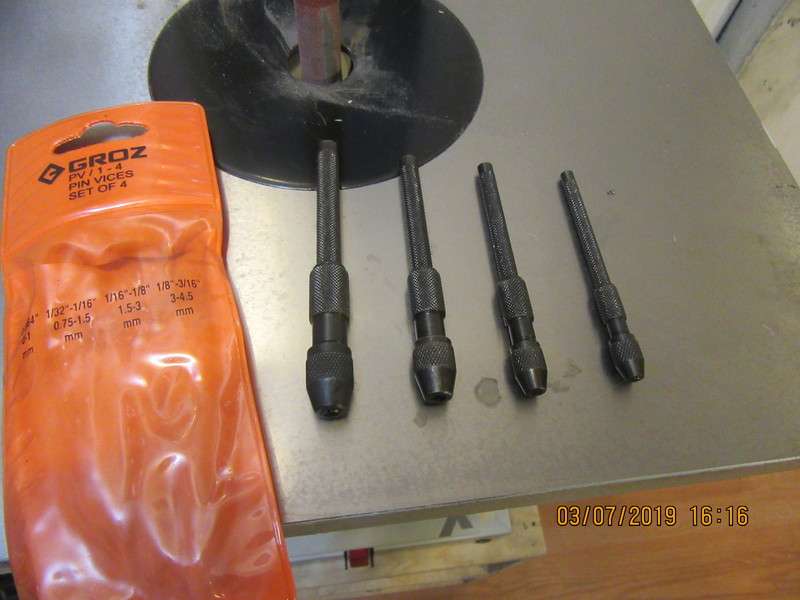