- Joined
- Aug 25, 2007
- Messages
- 3,890
- Reaction score
- 715
The compound on the standard 7 x 10/12/14 minilathe sucks. Having to crank the compound all the way back each time you want to change the angle is just miserable and for that reason, I usually don't have the compound mounted on my lathe. But, I do need a compound from time to time and I've finally decided to see if I can come up with something better. Here is the existing base of the included minilathe compound. I have modified mine, drilling a second set of mounting holes and shaving 3/16" off the bottom to lower the profile.
I considered making the new base from either aluminum or brass, since I have those materials on hand, but I really wanted to use cast iron. The only cast iron I had was a round bar 2 1/16" diameter about 3 1/2" long. So, mounting it up I the mill, I started whacking away with my face mill. Here I've go one side milled down to size.
And here I've whittled down the two sides, also to size.
Next I'll finish cutting the top down to size and continue with the dovetail shaping. The new mounting will use screws coming in from the side to clamp against an inverted, cone-shaped piece.
Chuck
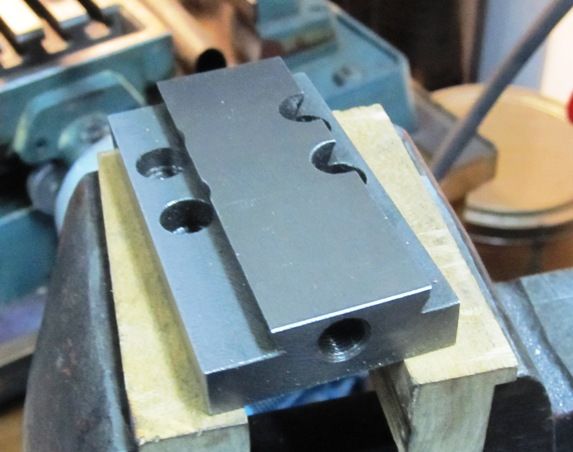
I considered making the new base from either aluminum or brass, since I have those materials on hand, but I really wanted to use cast iron. The only cast iron I had was a round bar 2 1/16" diameter about 3 1/2" long. So, mounting it up I the mill, I started whacking away with my face mill. Here I've go one side milled down to size.
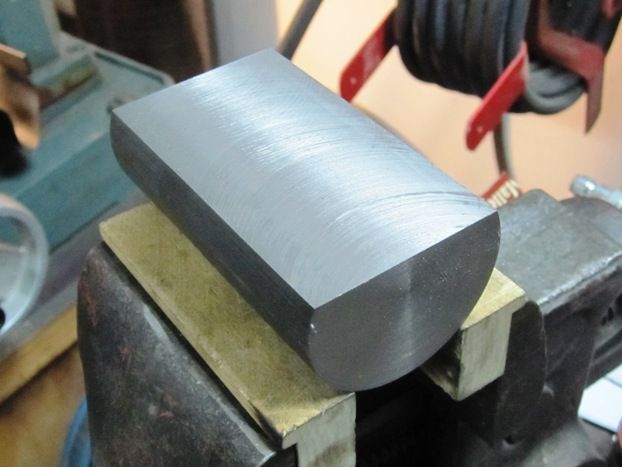
And here I've whittled down the two sides, also to size.
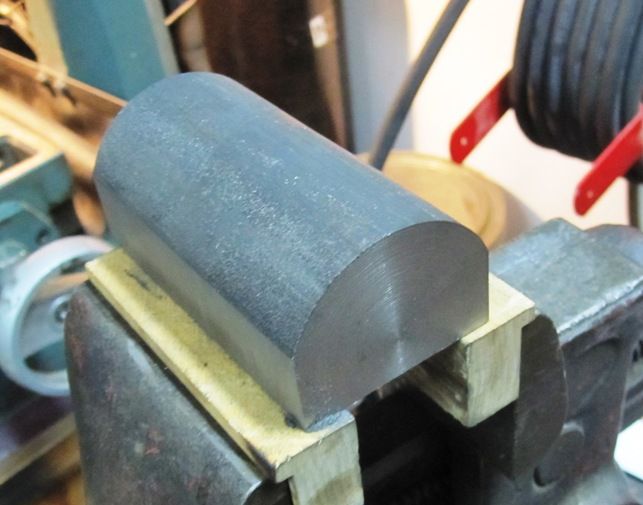
Next I'll finish cutting the top down to size and continue with the dovetail shaping. The new mounting will use screws coming in from the side to clamp against an inverted, cone-shaped piece.
Chuck