DavesWimshurst
DavesWimshurst
- Joined
- Dec 7, 2008
- Messages
- 102
- Reaction score
- 3
Hi,
I liked the look of Elmer's mine engine but wanted to add some extra details:
I added fluted columns and finials:
I used a milling spindle to do the fluting:
I wanted a fancier flywheel than the plans showed. I had some 4 inch copper pipe to use for the rim. The base parts were made thicker to accommodate the larger size. The core of the flywheel was made as an aluminum disk about 0.005 inch larger than the ID of the pipe. The disk was placed in a polypropylene dish filled with liquid nitrogen left over from a science show. When the bubbling stops the disk was about 325 deg F below zero. It fit easily into the copper pipe, sorry no pictures of this step.
I wanted a design with five curved spokes but didn't fancy the elaborate setups some have used for such tasks so I proceeded as follows. First I drilled the corner holes for the cutouts between the spokes:
A pattern disk shown on the right was made by drawing the cutout shape on paper and gluing it to the disk. The corner holes for one space and one in the next space were drilled using the rotary table the pattern was glued on and the opening was cut out:
This disk was then used to scribe the outlines for each opening. The flywheel was returned to the rotary table and the waste cut out using a short pass in each opening indexing to make the same cut in the other spaces with the same setup. It took about 2 hours to get the flywheel roughed out and another 2 hours to file to the lines. It takes some time but is not difficult if no visitors are around. :
I wanted to use a slip eccentric reverse and I also wanted the flywheel position to be adjustable to set the timing. For this I used a collet mounting for the flywheel and cut a semicircular groove in the eccentric:
A pin in the collet engages the groove to allow the eccentric to be in the correct position for each direction (ignore the extra hole :-[ ) :
I made a short video showing the action, the engine is running on 3 psi:
I know I have been brief so feel free to ask.
Dave
I liked the look of Elmer's mine engine but wanted to add some extra details:
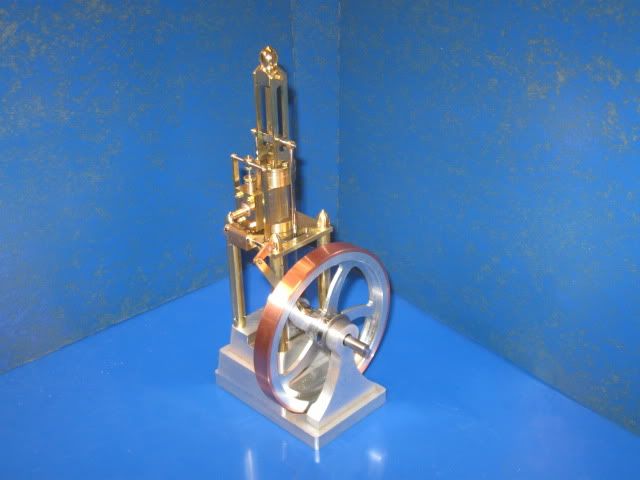
I added fluted columns and finials:
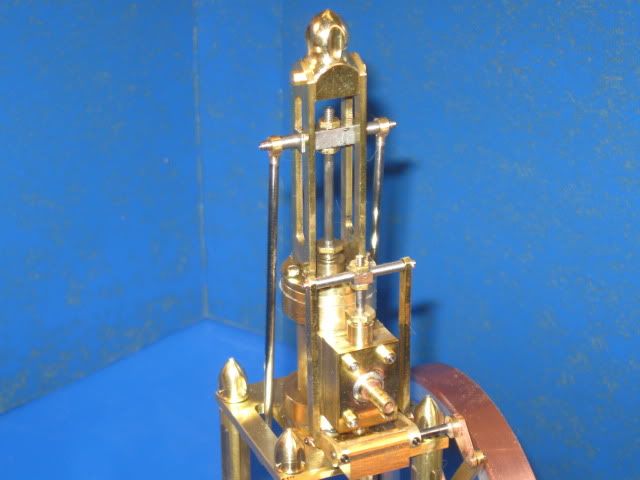
I used a milling spindle to do the fluting:
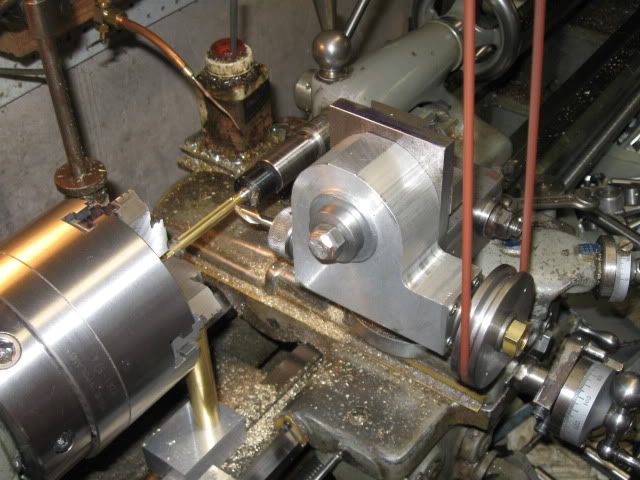
I wanted a fancier flywheel than the plans showed. I had some 4 inch copper pipe to use for the rim. The base parts were made thicker to accommodate the larger size. The core of the flywheel was made as an aluminum disk about 0.005 inch larger than the ID of the pipe. The disk was placed in a polypropylene dish filled with liquid nitrogen left over from a science show. When the bubbling stops the disk was about 325 deg F below zero. It fit easily into the copper pipe, sorry no pictures of this step.
I wanted a design with five curved spokes but didn't fancy the elaborate setups some have used for such tasks so I proceeded as follows. First I drilled the corner holes for the cutouts between the spokes:
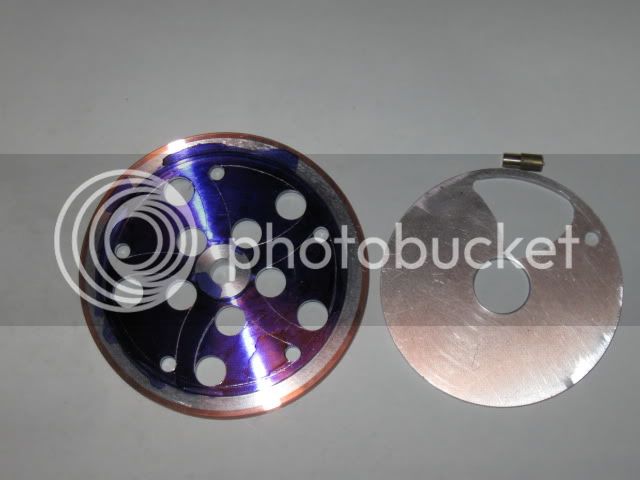
A pattern disk shown on the right was made by drawing the cutout shape on paper and gluing it to the disk. The corner holes for one space and one in the next space were drilled using the rotary table the pattern was glued on and the opening was cut out:
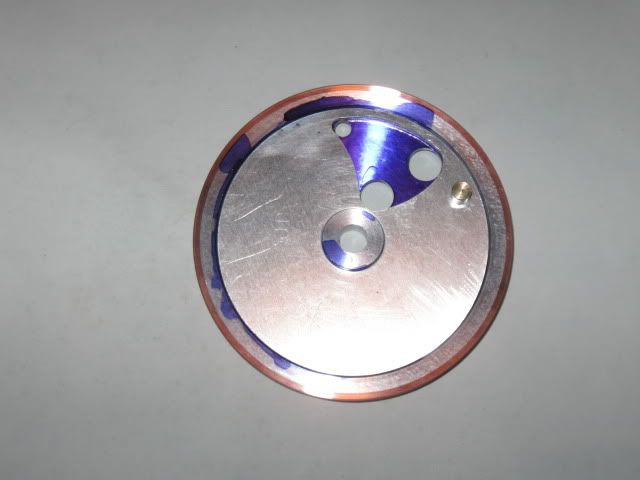
This disk was then used to scribe the outlines for each opening. The flywheel was returned to the rotary table and the waste cut out using a short pass in each opening indexing to make the same cut in the other spaces with the same setup. It took about 2 hours to get the flywheel roughed out and another 2 hours to file to the lines. It takes some time but is not difficult if no visitors are around. :
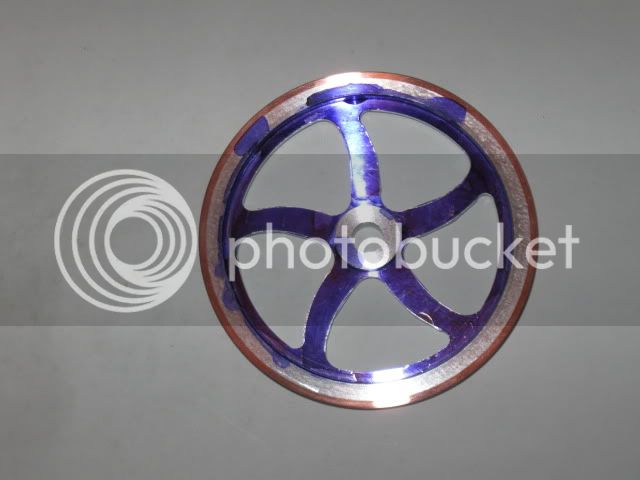
I wanted to use a slip eccentric reverse and I also wanted the flywheel position to be adjustable to set the timing. For this I used a collet mounting for the flywheel and cut a semicircular groove in the eccentric:
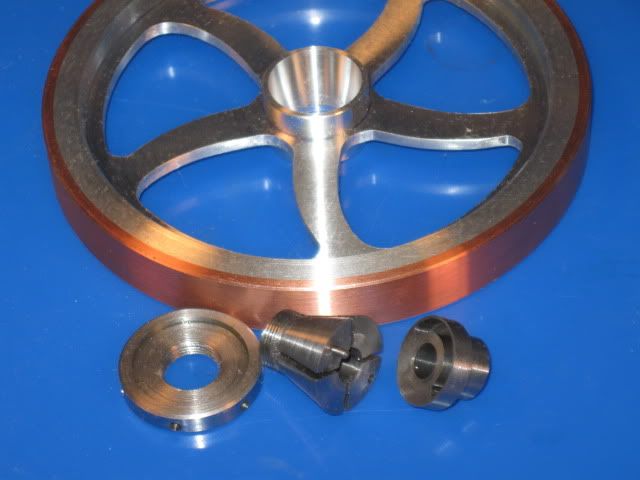
A pin in the collet engages the groove to allow the eccentric to be in the correct position for each direction (ignore the extra hole :-[ ) :
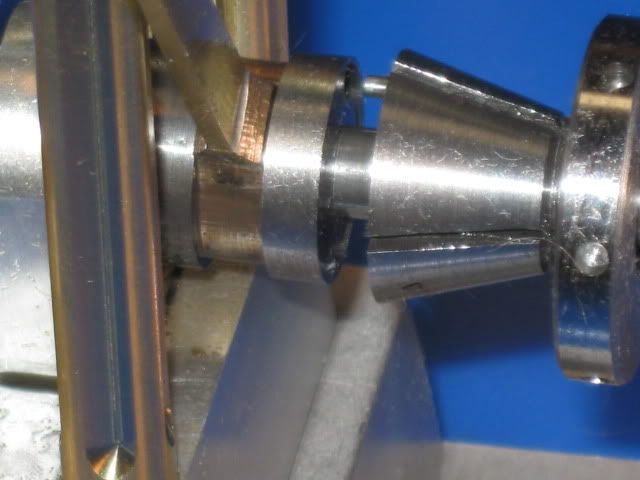
I made a short video showing the action, the engine is running on 3 psi:
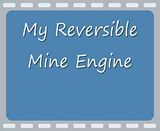
I know I have been brief so feel free to ask.
Dave