rake60
Well-Known Member
- Joined
- Jul 8, 2007
- Messages
- 4,756
- Reaction score
- 125
We need to come up with a way of pressing thin wall bearing bushings into parts that we
manufacture at work. The bushing need to be perfectly aligned, but the process has to be
made a production worker will be able to operate it easily.
(The parts are proprietary to our customer so I will not discuss them, only the pressing process.)
This is my approach to doing that.
First I machined a pin with one fit very close to the bore of the part and another fit very close
to the finished ID of the bushing after pressing. The pressing cap has a tiny .010" long fit turned
in it to set the bushing just below the top surface of the part. The spring allows the pin to slide
through the part in the process while still keeping everything in alignment.
It will look very much like this in the press.
I have already made a system like this for a larger bushing pressing process.
It works very well.
The spring canister is just a short piece of 1-5/8" tubing. I turned both ends true then turned a
shallow fit in one end for a plate cap to be welded in.
The cap plate was made by cutting a 2" long piece off of a 2" wide chunk of 1/4" flat stock.
Drill a 1/2" hole in the center then put a bolt through it with a nut securing it and chuck on the bolt.
It is very much like the process used in making a 4 bolt compound clamp for a 9 X 20 lathe.
After the parts are all assembled you can see how the alignment pin will slide out of the way
as the press comes down.
Total cost of that build was $1.20 for a spring I had to by at the local hardware store.
All of the other material were odds and ends found around the plant.
The press is even cooler!
It's a simple air press that will develop 5 tons of force using 5 heavy truck brake canisters.
Three of the canister have threaded rods going to the press ram and two are boosters.
There is a little more to it than that, but I don't own the rights to discuss it any further either.
I may be making a copy of it for my home shop.
I love my job!
I get to take an idea from conception to production with minimal interference.
Rick
manufacture at work. The bushing need to be perfectly aligned, but the process has to be
made a production worker will be able to operate it easily.
(The parts are proprietary to our customer so I will not discuss them, only the pressing process.)
This is my approach to doing that.
First I machined a pin with one fit very close to the bore of the part and another fit very close
to the finished ID of the bushing after pressing. The pressing cap has a tiny .010" long fit turned
in it to set the bushing just below the top surface of the part. The spring allows the pin to slide
through the part in the process while still keeping everything in alignment.
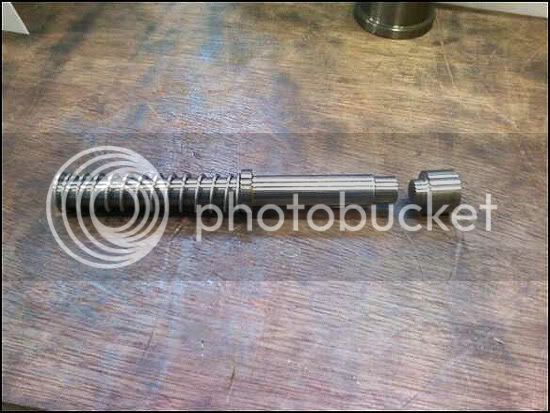
It will look very much like this in the press.
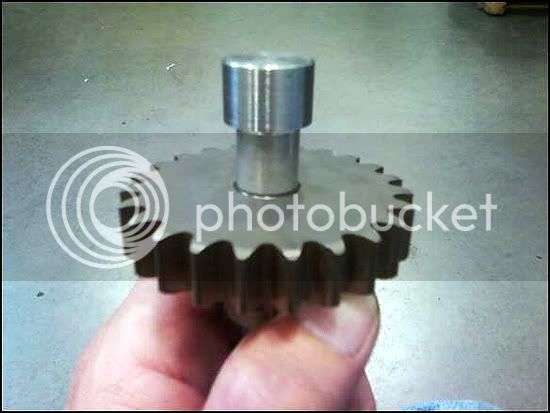
I have already made a system like this for a larger bushing pressing process.
It works very well.
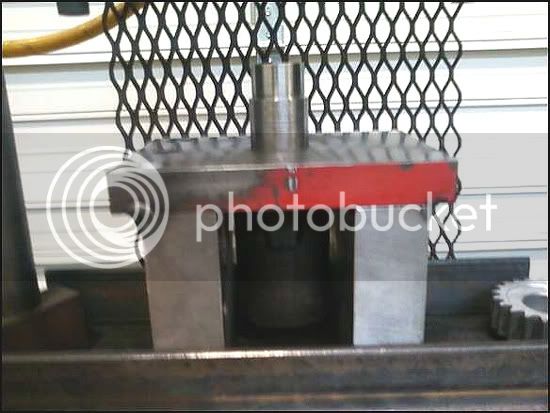
The spring canister is just a short piece of 1-5/8" tubing. I turned both ends true then turned a
shallow fit in one end for a plate cap to be welded in.
The cap plate was made by cutting a 2" long piece off of a 2" wide chunk of 1/4" flat stock.
Drill a 1/2" hole in the center then put a bolt through it with a nut securing it and chuck on the bolt.
It is very much like the process used in making a 4 bolt compound clamp for a 9 X 20 lathe.
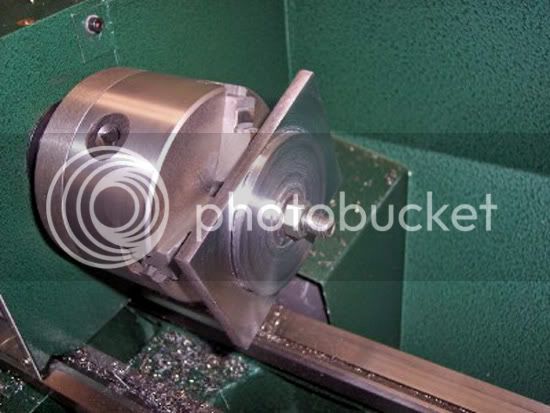
After the parts are all assembled you can see how the alignment pin will slide out of the way
as the press comes down.
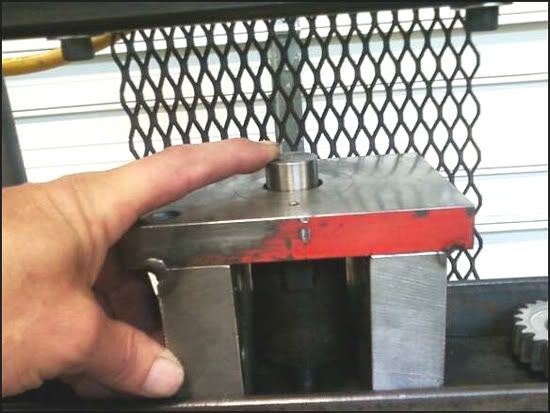
Total cost of that build was $1.20 for a spring I had to by at the local hardware store.
All of the other material were odds and ends found around the plant.
The press is even cooler!
It's a simple air press that will develop 5 tons of force using 5 heavy truck brake canisters.
Three of the canister have threaded rods going to the press ram and two are boosters.
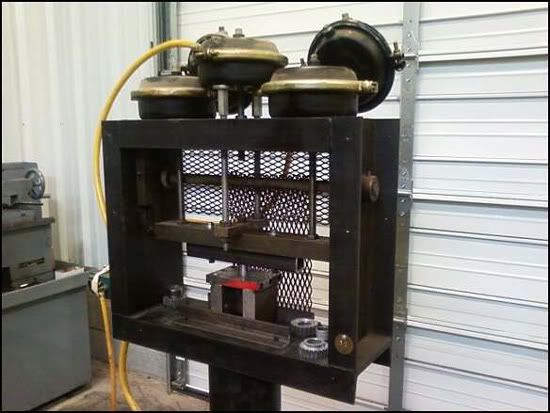
There is a little more to it than that, but I don't own the rights to discuss it any further either.
I may be making a copy of it for my home shop.
I love my job!
I get to take an idea from conception to production with minimal interference.
Rick