- Joined
- Aug 25, 2007
- Messages
- 3,890
- Reaction score
- 715
I've done a number of things to my minilathe to improve it. It's basically a very utilitarian machine and can do very nice work. I had previously converted the 3-jaw chuck to an adjust-tru version so I could bring the run-out down to virtually zero. I've used the lathe like this for over a year but recently noticed that the lathe was cutting tapers on longer work. Using the Rollie's Dad method, I discovered the taper to be about a .002" every 3 inches of travel. Up to now, the lathe was simply sitting on the workbench, not bolted down. So, I bought a piece of 5" x 1/2" hot rolled steel which I cut down to 24" in length for my 14" bed. I drilled holes in the steel plate to match the holes in the lathe feet.
After bolting the lathe securely to the plate, I again checked the taper and, while better, it was still off by about .003" over 8" of travel. I loosened the two bolts on the tailstock end and used a feeler gauge to determine the right amount of shimming to eliminate the taper. I settled on a piece of brass shim stock about .015" thick to bring the taper down to near zero over 8" of travel.
Haven't tried it yet, but I'm expecting to get more rigidity now which will lead to less chatter and more consistency in turning work pieces.
Chuck
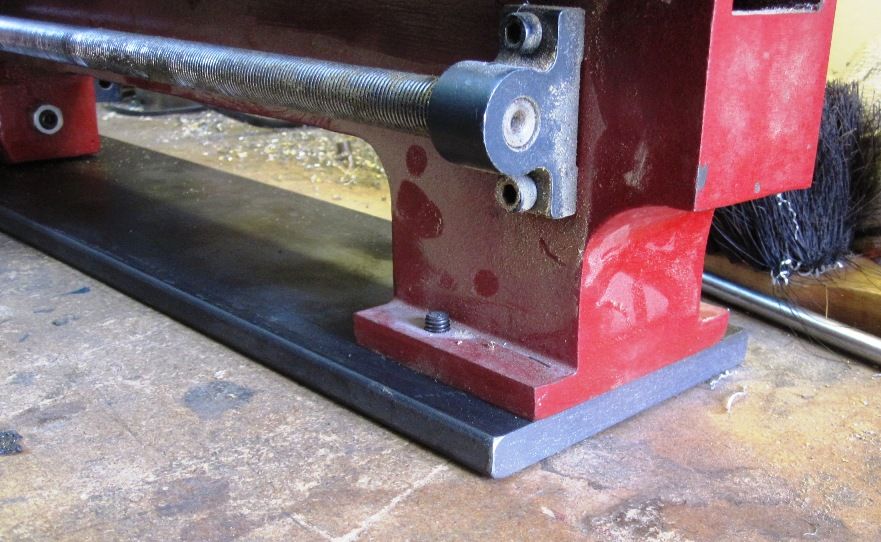
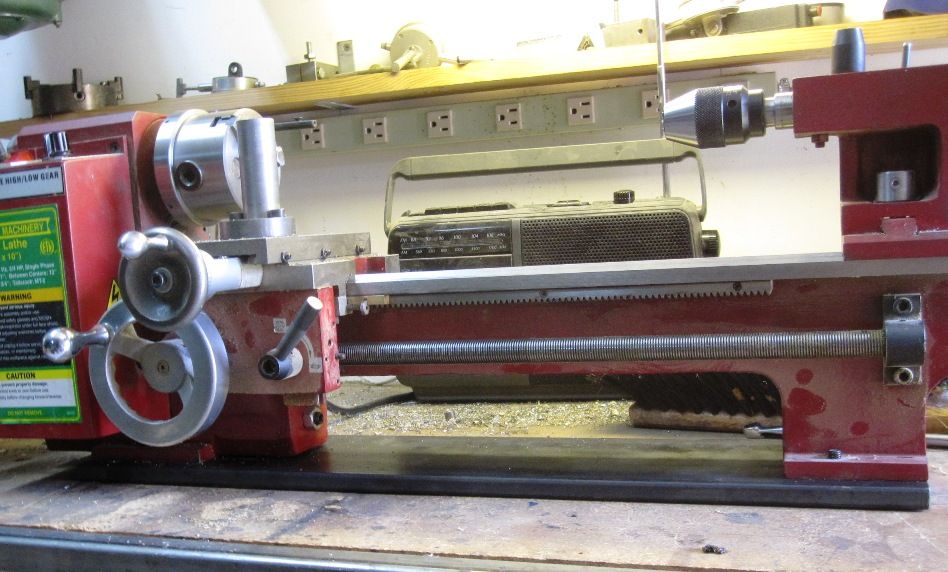
After bolting the lathe securely to the plate, I again checked the taper and, while better, it was still off by about .003" over 8" of travel. I loosened the two bolts on the tailstock end and used a feeler gauge to determine the right amount of shimming to eliminate the taper. I settled on a piece of brass shim stock about .015" thick to bring the taper down to near zero over 8" of travel.
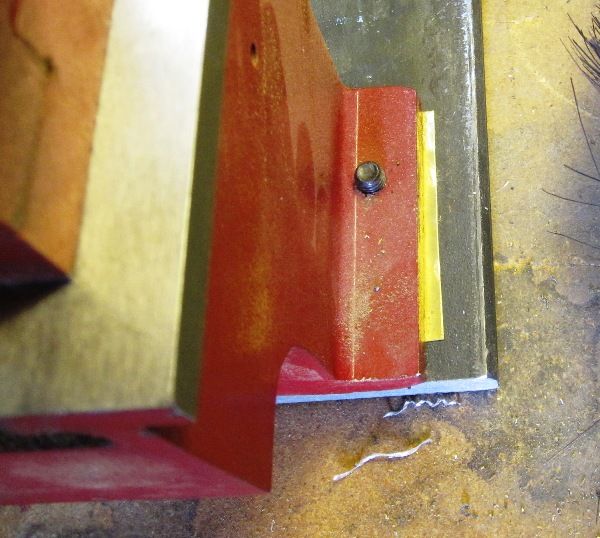
Haven't tried it yet, but I'm expecting to get more rigidity now which will lead to less chatter and more consistency in turning work pieces.
Chuck