About 3 yrs. since I built my first I/C twin engine. My "GEMINI" is a good start but I want another crack at an inline twin to address a couple of shortcomings in its build. Can I make improvements in service, durability and add a new feature using basic machine shop know how and NO PLANS
in the same scale? scratch.gif .....The story of "OVERTIME" starts this weekend!
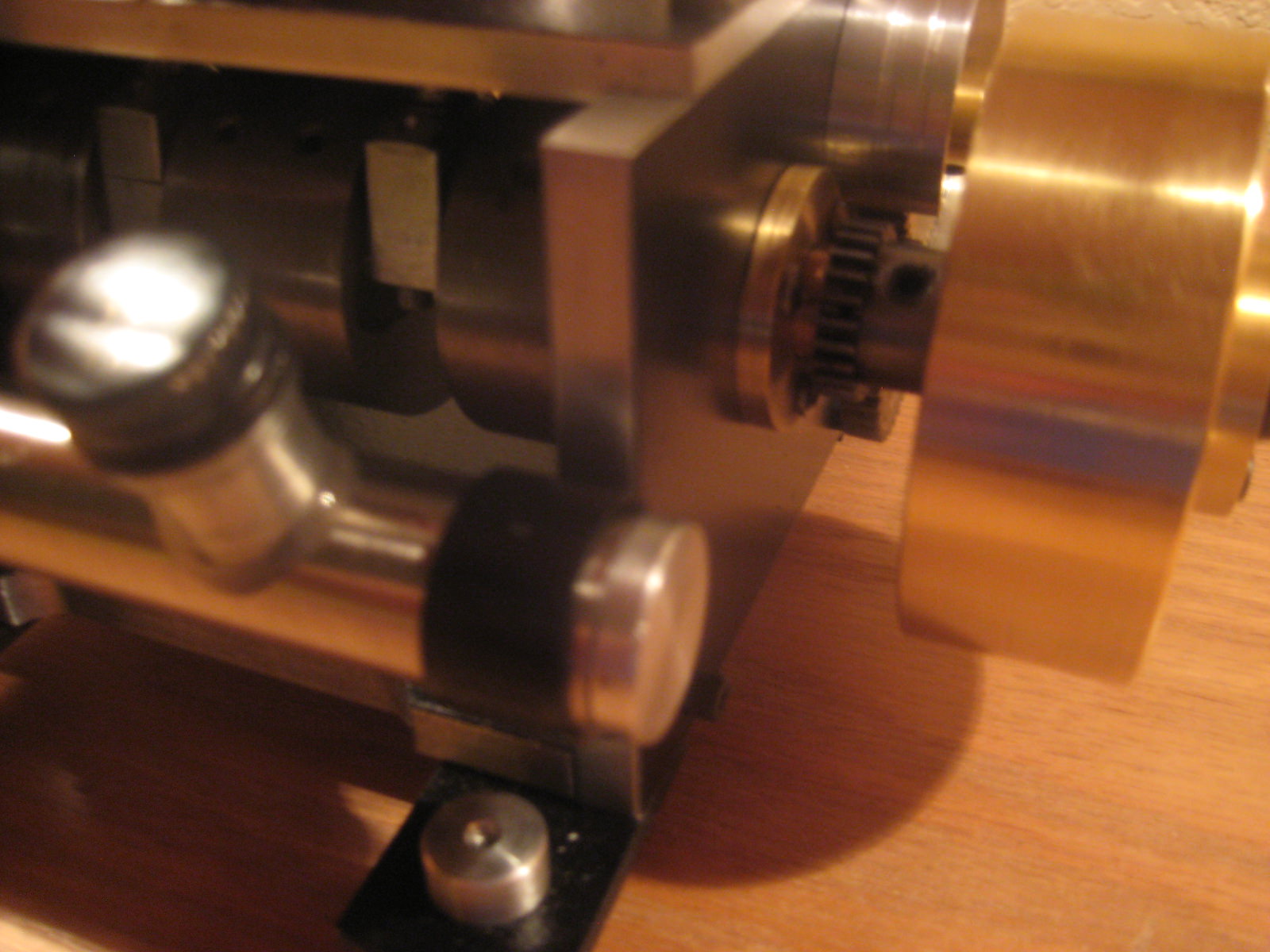
Last edited: