I have been wanting to try out a larger indexable insert holder on my small (7 X 10) lathe, just to see if there were any benefits. When I got a 20% discount offer I took the plunge and bought the tool below (Dorian MTGNR08-2A).
After some initial trials I conclude that I would not recommend this purchase for a small lathe. I'm posting this here for the benefit of anyone else contemplating a similar purchase.
Here's a short summary of my findings:
- fits my QCTP toolholder, but I had to modify the tool to get it to center
- tight fit (or no fit) for some cutting operations
- no major advantages, some disadvantages
For a more detailed overview with more photos see this link:
https://sites.google.com/site/lagad...athes-mills-etc/review---indexable-toolholder
P.S.
I'm not saying this is a bad tool, just that it is not a good fit for a small lathe.
After some initial trials I conclude that I would not recommend this purchase for a small lathe. I'm posting this here for the benefit of anyone else contemplating a similar purchase.
Here's a short summary of my findings:
- fits my QCTP toolholder, but I had to modify the tool to get it to center
- tight fit (or no fit) for some cutting operations
- no major advantages, some disadvantages
For a more detailed overview with more photos see this link:
https://sites.google.com/site/lagad...athes-mills-etc/review---indexable-toolholder
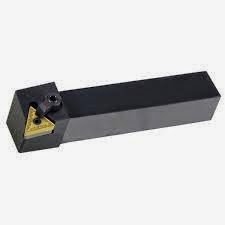
P.S.
I'm not saying this is a bad tool, just that it is not a good fit for a small lathe.