Philjoe5
Well-Known Member
- Joined
- Jul 12, 2007
- Messages
- 1,727
- Reaction score
- 321
I saw a model of the James Coombes Mine Engine at a show in Kent, Connecticut in 2006 and the exhibitor, Tom Kokinchak, was selling his plans for it. I was really impressed with the valve mechanism for the engine and bought the plans. At that time I was really a novice and closer inspection of the plans discouraged me from just jumping in to start it. For example, at the time I owned a lathe but did not have a four jaw chuck :shrug:. Well after 4 years, and many, many pounds of chips Im ready to tackle this project.
I thought Id do this as a work in progress and post pictures of the various assemblies as they are completed. As usual, your comments and suggestions always welcomed.
First some background. I have, so far, not located a lot of information about the James Coombes Mine Engine. Theres some information on the Stuart website as they offer this engine as a castings kit. However, Im still trying to find out who James Coombes was, how many of these engines were built and what, if any, advantage this design presented when compared to existing configurations. Anyone with info is welcomed to chime in here.
The engine Im building is a barstock model. I recently saw a completed version at Cabin Fever last month. It was built by Steve from Massachusetts. Steve if youre reading this, take a bow :bow:, because you made a very impressive looking model.
It is pictured here:
Theres also a video of this engine here:
[ame]http://www.youtube.com/watch?v=ZCfXcAZTrO0[/ame]
I started with the cylinder block. I had a lump of cast iron (Durabar) left from a previous project and began by milling a block to the overall dimensions.
I drilled and bored the cylinder on the lathe and then turned the ends to round them.
The steam chest mounting holes were drilled/tapped, the steam ports milled and drilled and the cylinder head mounting holes were drilled/tapped. When I angle drilled the first of four holes that connect the cylinder bore to the steam chest I had calculated the depth of the hole for the breakthrough of the drill. I always hold my breath when drilling the first one, because if any of my calculations or settings are wrong this is a great opportunity to make a paperweight. But all went well and the picture here shows a red tipped wooden dowel in the port on one end of the cylinder extending to the steam chest port (whew!)
Some of the excess material from the central exterior of the cylinder block was milled away. Then the exhaust port was drilled and tapped. This completes the machining of the cylinder block.
This is all I have to report on for this session.
Cheers,
Phil
I thought Id do this as a work in progress and post pictures of the various assemblies as they are completed. As usual, your comments and suggestions always welcomed.
First some background. I have, so far, not located a lot of information about the James Coombes Mine Engine. Theres some information on the Stuart website as they offer this engine as a castings kit. However, Im still trying to find out who James Coombes was, how many of these engines were built and what, if any, advantage this design presented when compared to existing configurations. Anyone with info is welcomed to chime in here.
The engine Im building is a barstock model. I recently saw a completed version at Cabin Fever last month. It was built by Steve from Massachusetts. Steve if youre reading this, take a bow :bow:, because you made a very impressive looking model.
It is pictured here:
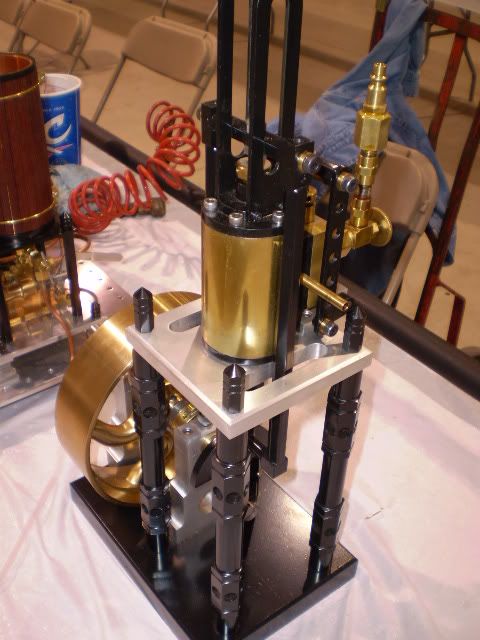
Theres also a video of this engine here:
[ame]http://www.youtube.com/watch?v=ZCfXcAZTrO0[/ame]
I started with the cylinder block. I had a lump of cast iron (Durabar) left from a previous project and began by milling a block to the overall dimensions.
I drilled and bored the cylinder on the lathe and then turned the ends to round them.
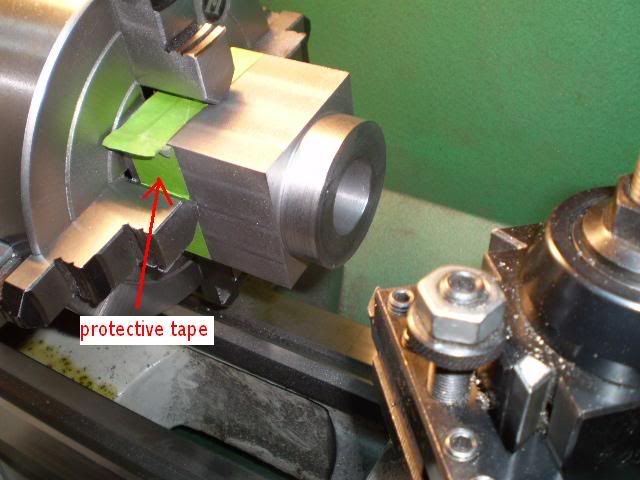
The steam chest mounting holes were drilled/tapped, the steam ports milled and drilled and the cylinder head mounting holes were drilled/tapped. When I angle drilled the first of four holes that connect the cylinder bore to the steam chest I had calculated the depth of the hole for the breakthrough of the drill. I always hold my breath when drilling the first one, because if any of my calculations or settings are wrong this is a great opportunity to make a paperweight. But all went well and the picture here shows a red tipped wooden dowel in the port on one end of the cylinder extending to the steam chest port (whew!)
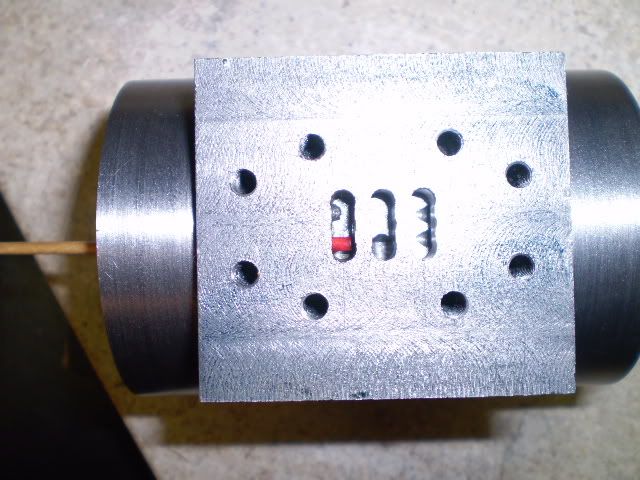
Some of the excess material from the central exterior of the cylinder block was milled away. Then the exhaust port was drilled and tapped. This completes the machining of the cylinder block.
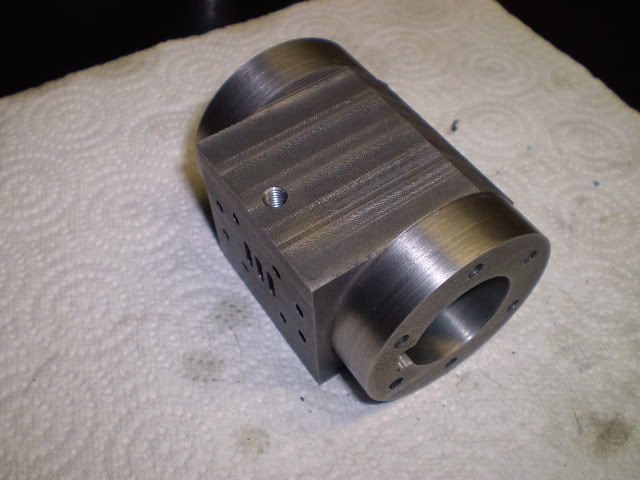
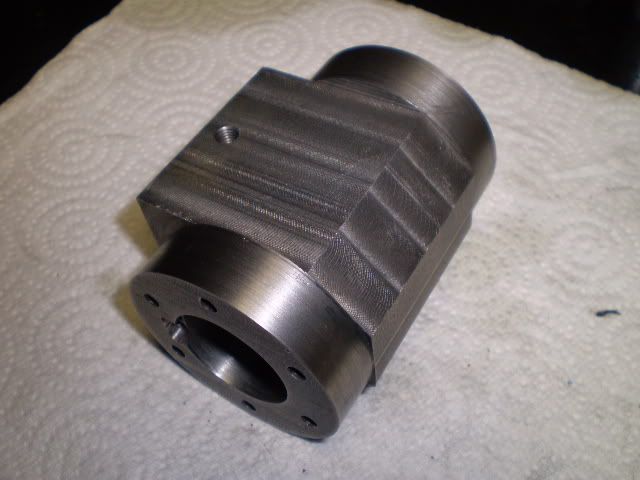
This is all I have to report on for this session.
Cheers,
Phil