Lads
In the shot below is a set up on the milling machine of me trying to Slit-saw a taper pin expansion rod i am making. The saw thickness is .007 thou x 1 1/8th od, i ran the mill at 150 rpms the part is made out of 304 stainless.
In this shot you see the work in front of the slitting saw, i centered the saw blade to the pin center and i plunged cut in (moving the part away into the blade) .075 thou. that worked fine, i bathed it in Kroil and slowly fed the part onto the blade.
I then needed to slit the other side of it so i just raised the quill and moved the table 180deg, lowered the quill to center height and started to slit this side.
The device you see poking into the end of the collet block is a stop for the pin up in the hole, my thought was the blade may want to throw the pin out. That will become clearer on the next photos.
Here is a shot of the first side i successfully cut.
Well!!!!!!!!! here is what happened when i did the other-side, i got to about .050 in the cut and the thing turned to ****e, the blade snapped and at the same time gouged the piece which is now ruined.
Here is the shot of the part with the pin included, i installed a sacrifice pin into the arbor for the machining process in slitting, the wall thickness on the taper tube end is around .032 thou
I figured that what i am trying to explain may be a little hard to do in words so i can show you my drawings for you all to get a better perspective.
Linear drawing showing taper reamer and drill, this is to scale.
Detailed drawing.
And a shot of the pin installed before being turned down.
What i shall do now is re-make another one and this time just index the pin, as i know it worked in that location.
if anyone has any experience in using very thin slitting saws i would appreciate the advice, i have never slitted anything this thin.
Happy days Anthony.
In the shot below is a set up on the milling machine of me trying to Slit-saw a taper pin expansion rod i am making. The saw thickness is .007 thou x 1 1/8th od, i ran the mill at 150 rpms the part is made out of 304 stainless.
In this shot you see the work in front of the slitting saw, i centered the saw blade to the pin center and i plunged cut in (moving the part away into the blade) .075 thou. that worked fine, i bathed it in Kroil and slowly fed the part onto the blade.
I then needed to slit the other side of it so i just raised the quill and moved the table 180deg, lowered the quill to center height and started to slit this side.
The device you see poking into the end of the collet block is a stop for the pin up in the hole, my thought was the blade may want to throw the pin out. That will become clearer on the next photos.
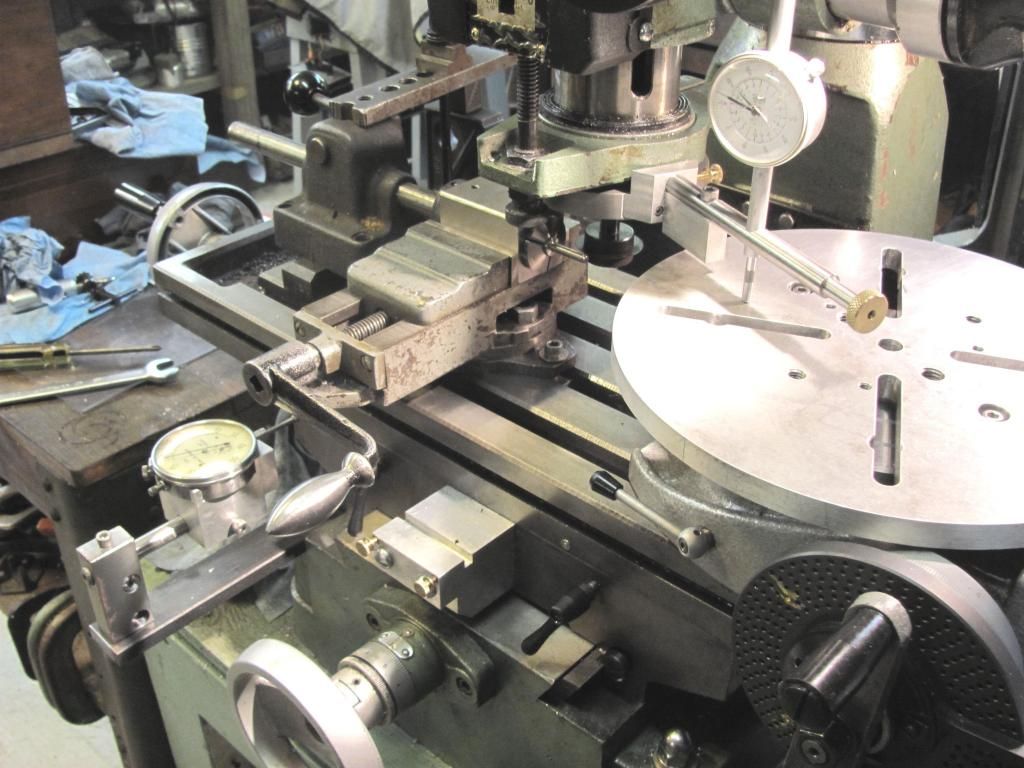
Here is a shot of the first side i successfully cut.
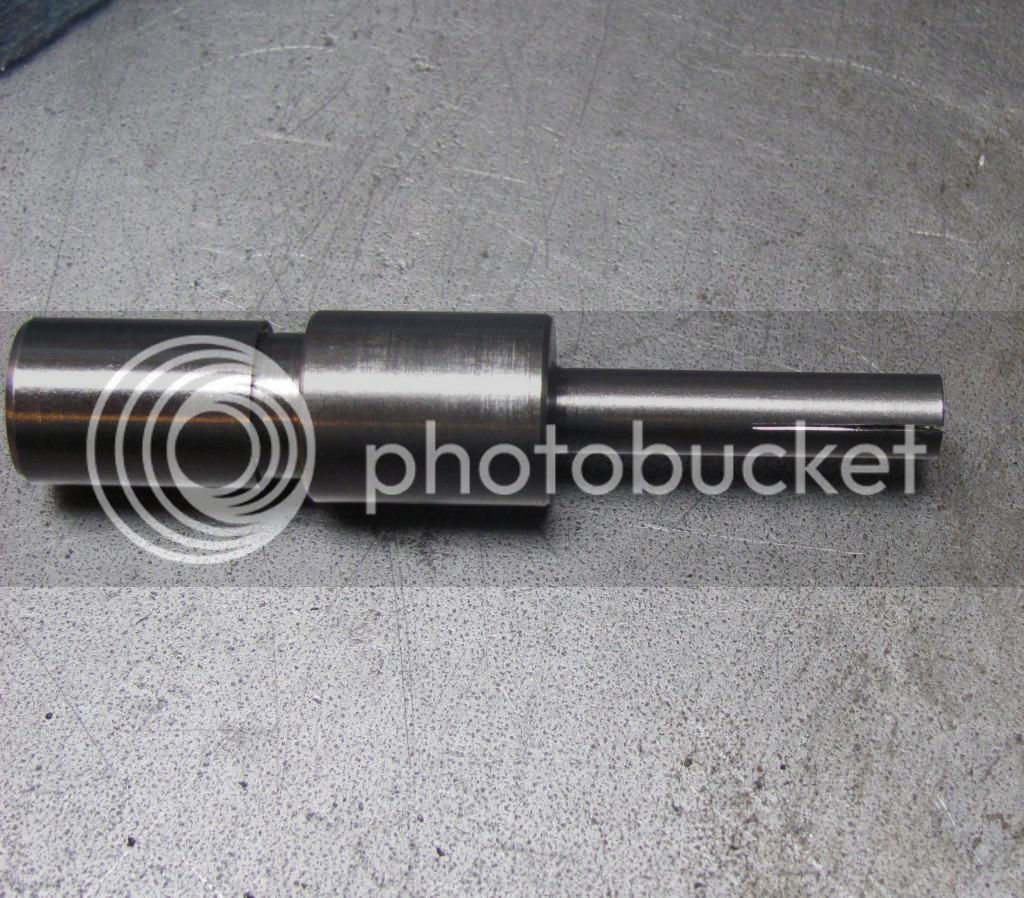
Well!!!!!!!!! here is what happened when i did the other-side, i got to about .050 in the cut and the thing turned to ****e, the blade snapped and at the same time gouged the piece which is now ruined.
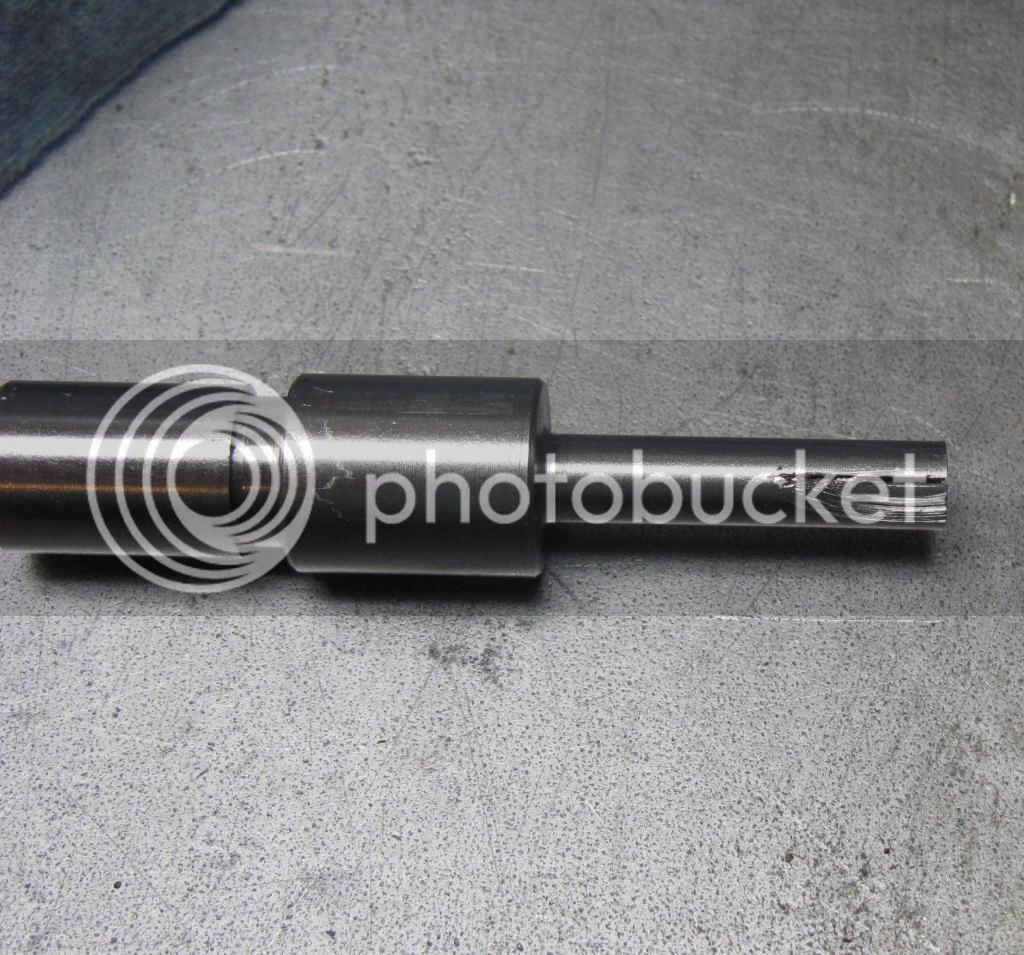
Here is the shot of the part with the pin included, i installed a sacrifice pin into the arbor for the machining process in slitting, the wall thickness on the taper tube end is around .032 thou
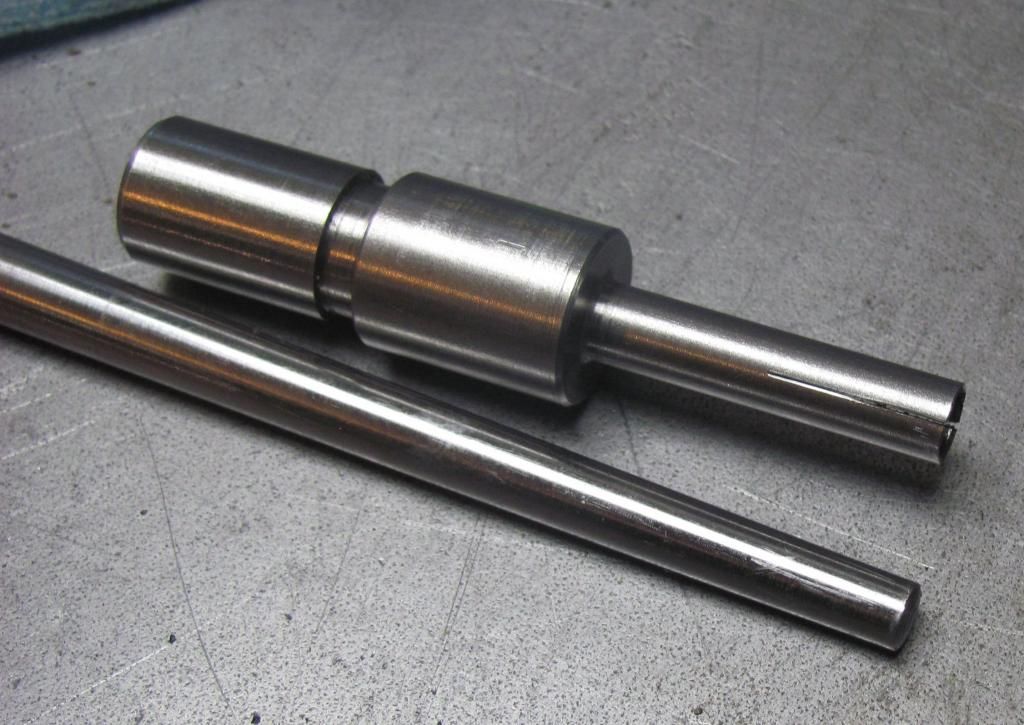
I figured that what i am trying to explain may be a little hard to do in words so i can show you my drawings for you all to get a better perspective.
Linear drawing showing taper reamer and drill, this is to scale.
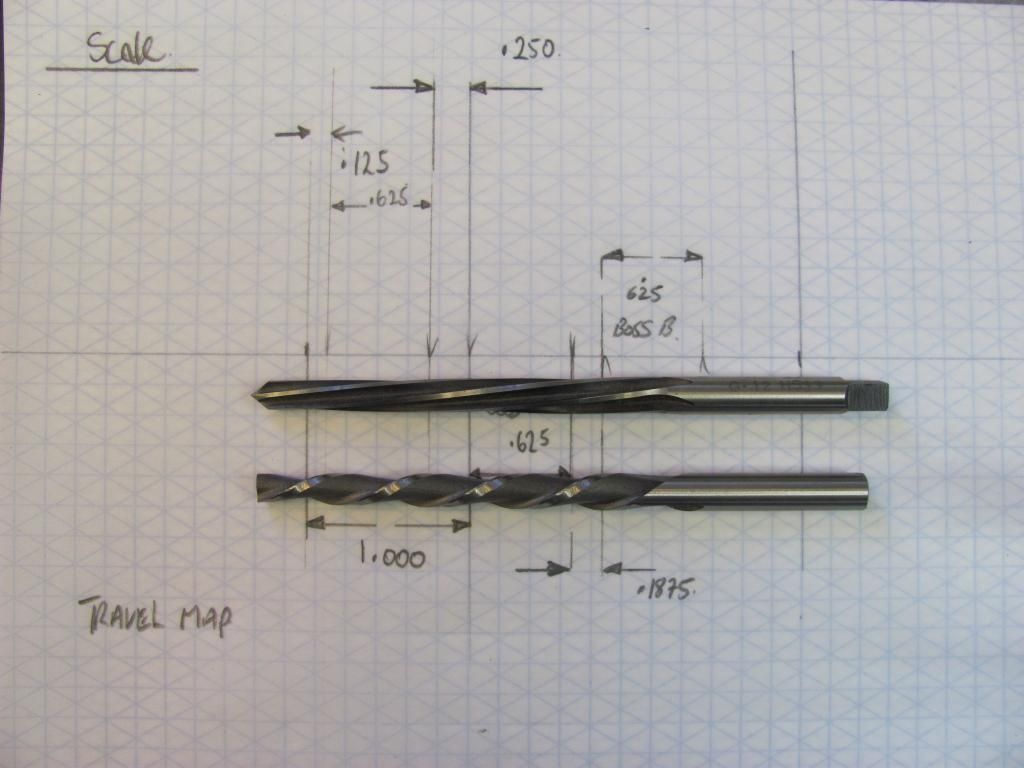
Detailed drawing.
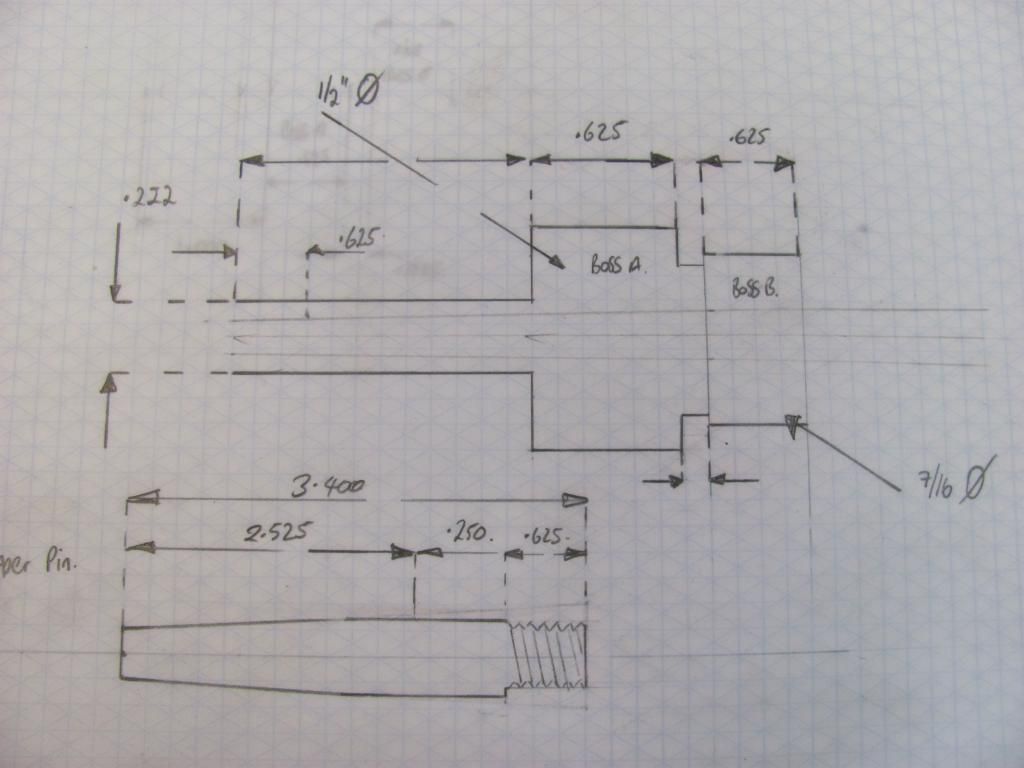
And a shot of the pin installed before being turned down.
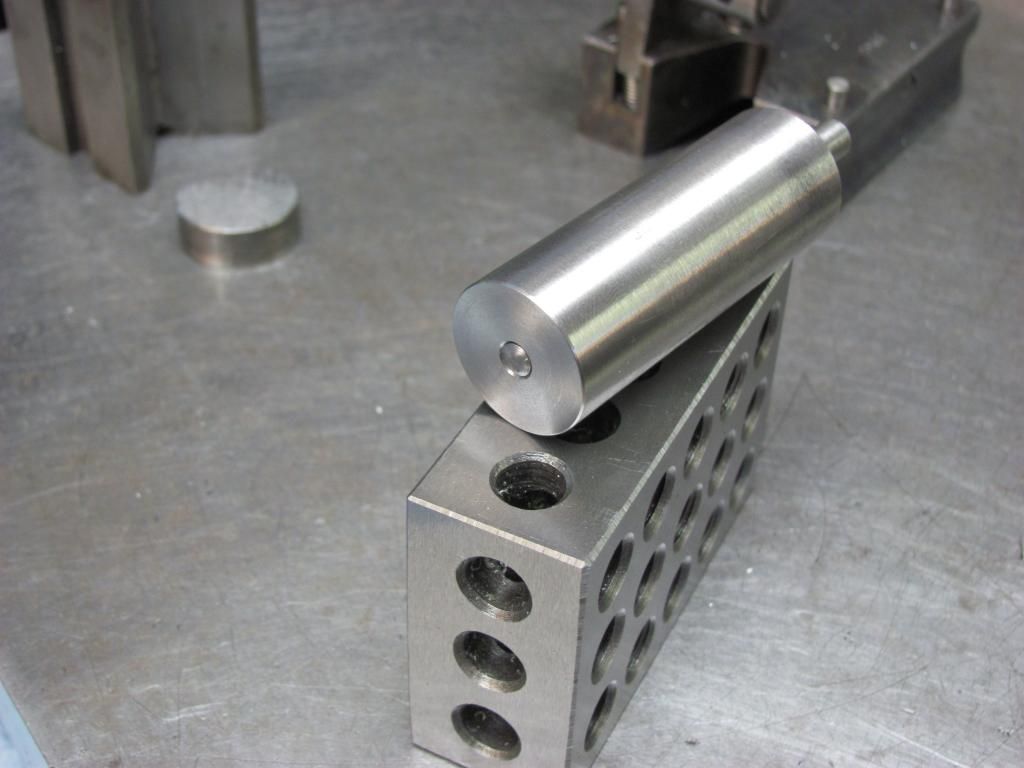
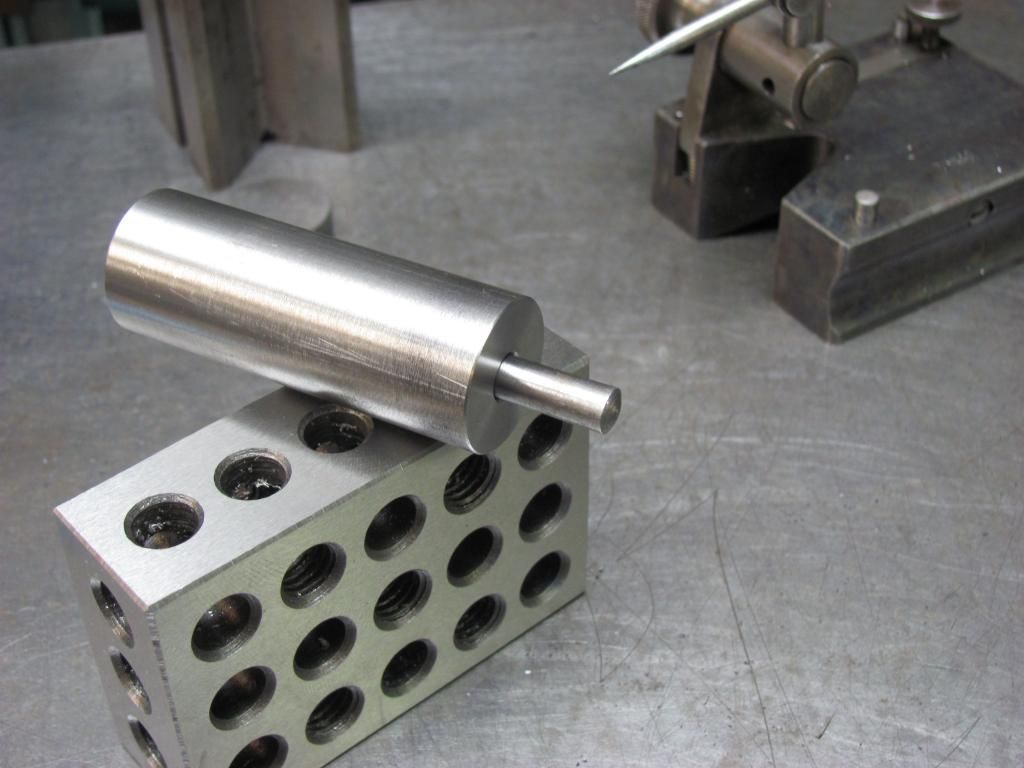
What i shall do now is re-make another one and this time just index the pin, as i know it worked in that location.
if anyone has any experience in using very thin slitting saws i would appreciate the advice, i have never slitted anything this thin.
Happy days Anthony.