Joachim Steinke
Active Member
- Joined
- Jun 14, 2010
- Messages
- 29
- Reaction score
- 22
Hi
For machining the fins of my next scheduled cylinder heads I will need some special groove cutters.
Special because for two reasons:
A small cutting diameter to follow the desired contour tail combined with a relative high cutting depth, in detail about 20mm (0.8in) of diameter and 6mm (0.25in) cutting depth.
And the possibility to run the tool a little bit faster than a normal saw blade. I want to use my CNC portal for the first time to do some of the outer shape operations. But I havent build a low speed / high torque milling spindle yet (this is on schedule for the beginning of 2011), so I have to use my old KRESS router motor which makes 8000 rpm at its lowest setting.
So normal saw blades with a diameter of 1.5 to 2in are no choice and the real small ones with 0.8in are too fine in tooth pitch (40 teeth), this will not work properly at 8000, especially with this cutting depth.
The most suitable commercial tools would be these small groove mills with exchangeable 3 blade carbide heads normally used for circular inner milling operations. Unfortunately they are not made for cutting depth more than about 0.1in.
So again I had to make my own cutter.
The shaft is made from 8mm silver steel and the exchangeable inserts from ETG (some mild machining but very good hardening and stress free steel).
The needed side clearance is realized with two 2.5deg undercuts towards the blade body.
Hardening is done with the propane torch, then quenching in oil and tempered at 250deg C for an hour at last.
And finally the grinding of the upper and front surface of the cutting edges.
ETG is some very fine steel for tool making, when suitable hardened and tempered it will be even more durable for cutting operations than silver steel (drill rod). And it doesnt tend to distort and crack on sharp corners. You can design even complex and fragile tool shapes and harden it with our simple home methods (meaning without professional equipment), which would be much more problematical with silver steel.
But most of the time I get some real ugly pox grain surface when heating this material with the propane flame, as you can see on the pictures. The ugly surface is no real problem for the tool purpose anyway, but I would like to know the reason for it. Maybe its because of the sulphur, our German steel nomenclature says 45 S 20 ore 44 SMn 28, so the alloy is containing some sulphur, I guess to achieve the very mild machining properties.
Finally I made two cutting blades of 1mm (0,04in) and 1,5mm (0,06in) width.
I didnt have the opportunity to run the cutters on my CNC portal with in the last days. But I made some testing on my bench miller which is recently rebuild with a frequency controlled induction motor, so I can run the spindle up to over 10 thousand rpm now. They both make a nice and sharp cut, no shatter and vibrations. I dont intend to use them on steel parts anyway, they are only made for machining aluminium, high strength alloy (EN-7075) and the mild machining EN-2007 quality.
After getting a good impression of the cutting force and the whole cutting behaviour on my bench miller I think the groove cutters will do their intended job right well. But being more fragile than the rigid commercial carbide groove cutters they must be driven with a little bit of care on the CNC. That means only small infeed per pass but fairly fast feed rates according to the high spindle revolution to get a suitable chip load.
At last a little example for what duty the cutter is designed .but this head construction is not finished yet ...it is only a rough layout for testing my CAM module.
Achim
For machining the fins of my next scheduled cylinder heads I will need some special groove cutters.
Special because for two reasons:
A small cutting diameter to follow the desired contour tail combined with a relative high cutting depth, in detail about 20mm (0.8in) of diameter and 6mm (0.25in) cutting depth.
And the possibility to run the tool a little bit faster than a normal saw blade. I want to use my CNC portal for the first time to do some of the outer shape operations. But I havent build a low speed / high torque milling spindle yet (this is on schedule for the beginning of 2011), so I have to use my old KRESS router motor which makes 8000 rpm at its lowest setting.
So normal saw blades with a diameter of 1.5 to 2in are no choice and the real small ones with 0.8in are too fine in tooth pitch (40 teeth), this will not work properly at 8000, especially with this cutting depth.
The most suitable commercial tools would be these small groove mills with exchangeable 3 blade carbide heads normally used for circular inner milling operations. Unfortunately they are not made for cutting depth more than about 0.1in.
So again I had to make my own cutter.
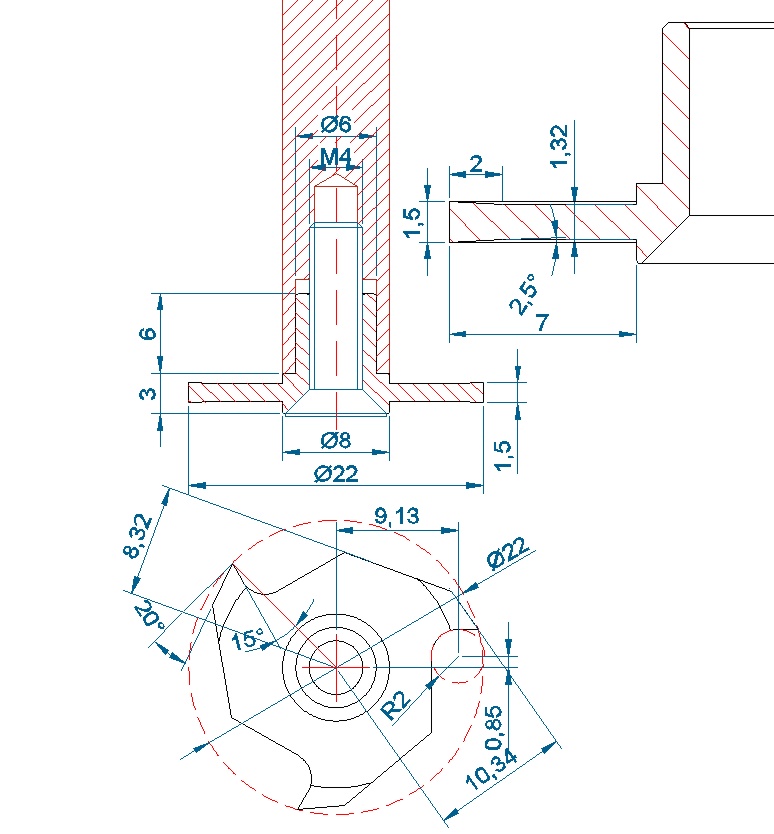
The shaft is made from 8mm silver steel and the exchangeable inserts from ETG (some mild machining but very good hardening and stress free steel).
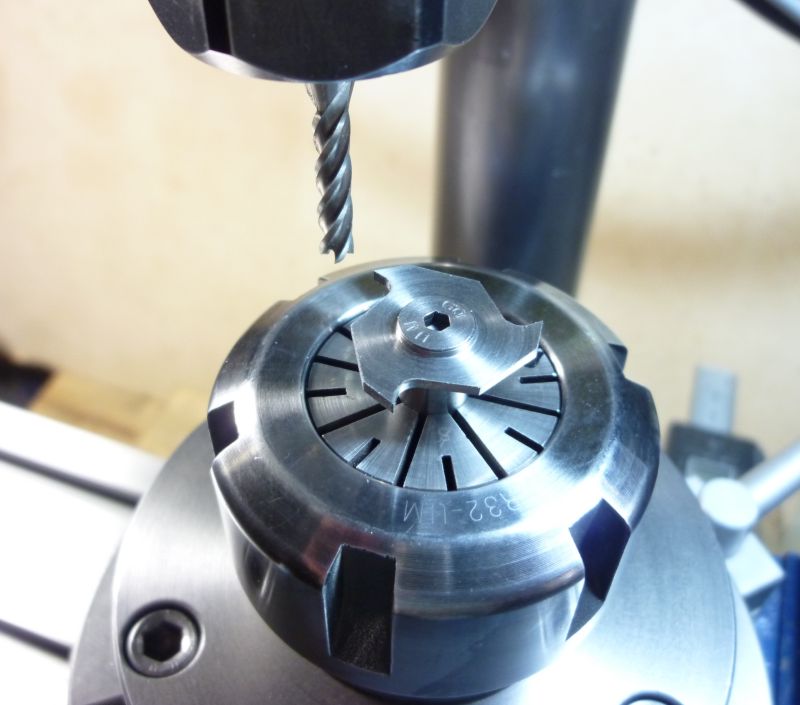
The needed side clearance is realized with two 2.5deg undercuts towards the blade body.
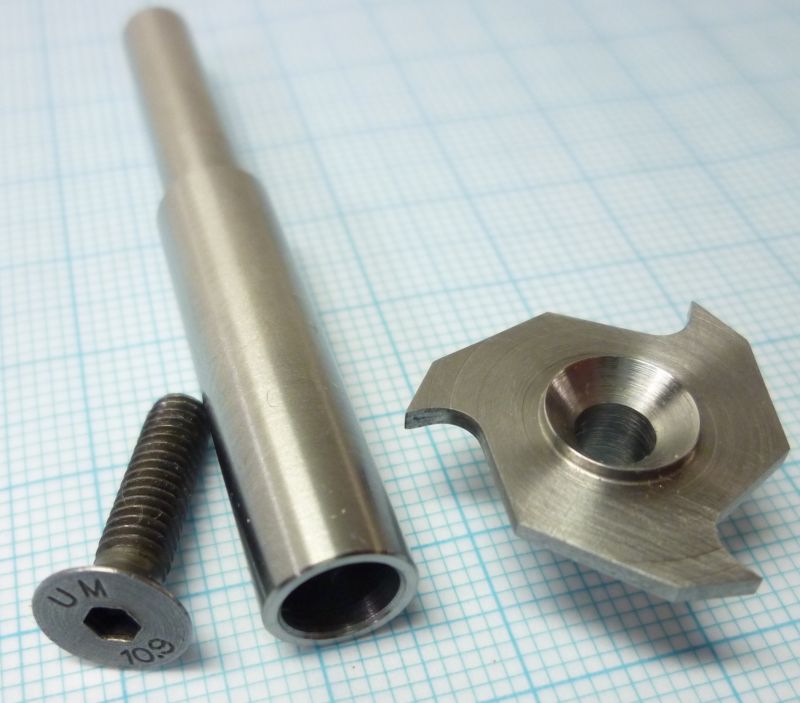
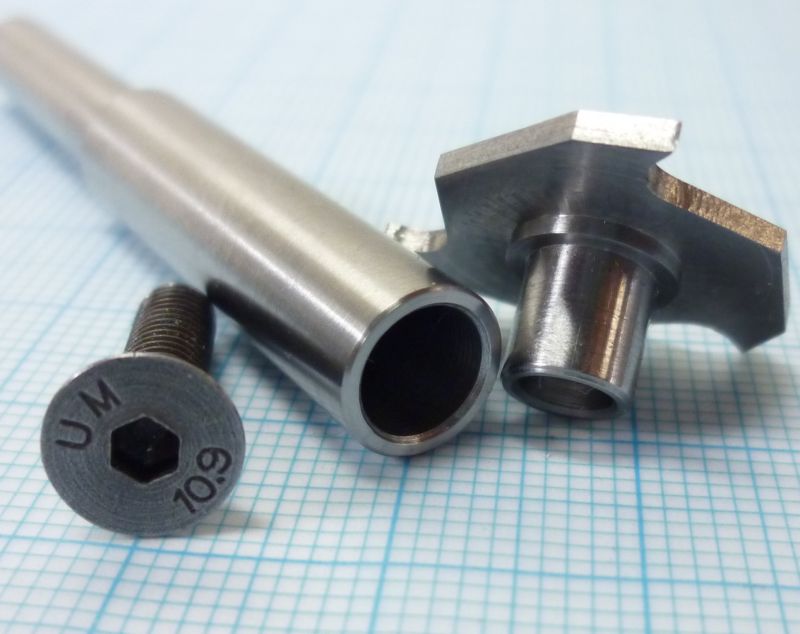
Hardening is done with the propane torch, then quenching in oil and tempered at 250deg C for an hour at last.
And finally the grinding of the upper and front surface of the cutting edges.
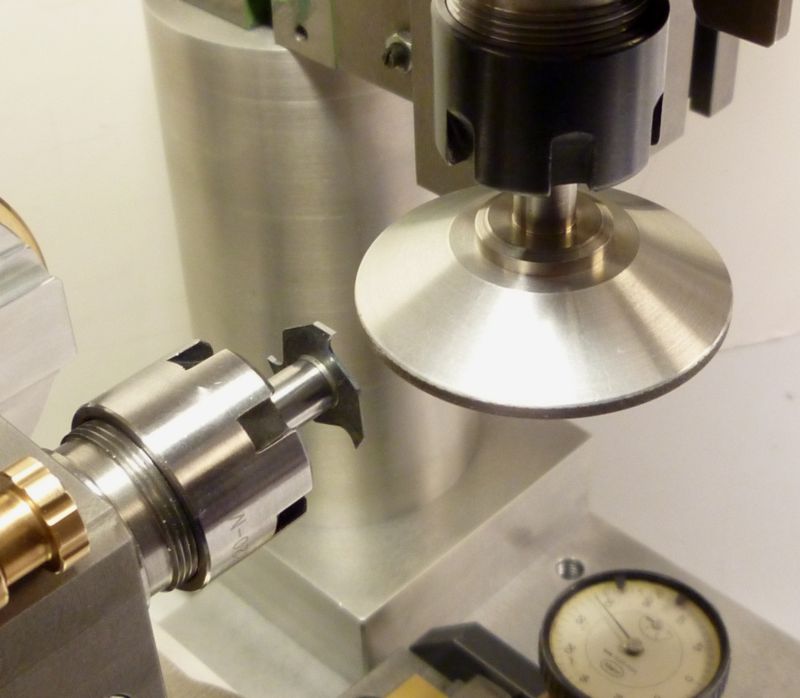
ETG is some very fine steel for tool making, when suitable hardened and tempered it will be even more durable for cutting operations than silver steel (drill rod). And it doesnt tend to distort and crack on sharp corners. You can design even complex and fragile tool shapes and harden it with our simple home methods (meaning without professional equipment), which would be much more problematical with silver steel.
But most of the time I get some real ugly pox grain surface when heating this material with the propane flame, as you can see on the pictures. The ugly surface is no real problem for the tool purpose anyway, but I would like to know the reason for it. Maybe its because of the sulphur, our German steel nomenclature says 45 S 20 ore 44 SMn 28, so the alloy is containing some sulphur, I guess to achieve the very mild machining properties.
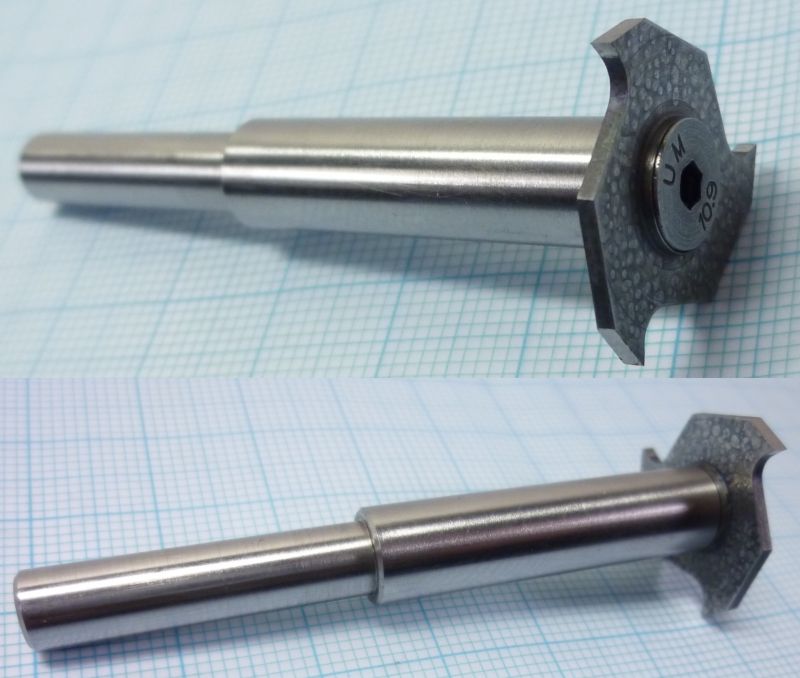
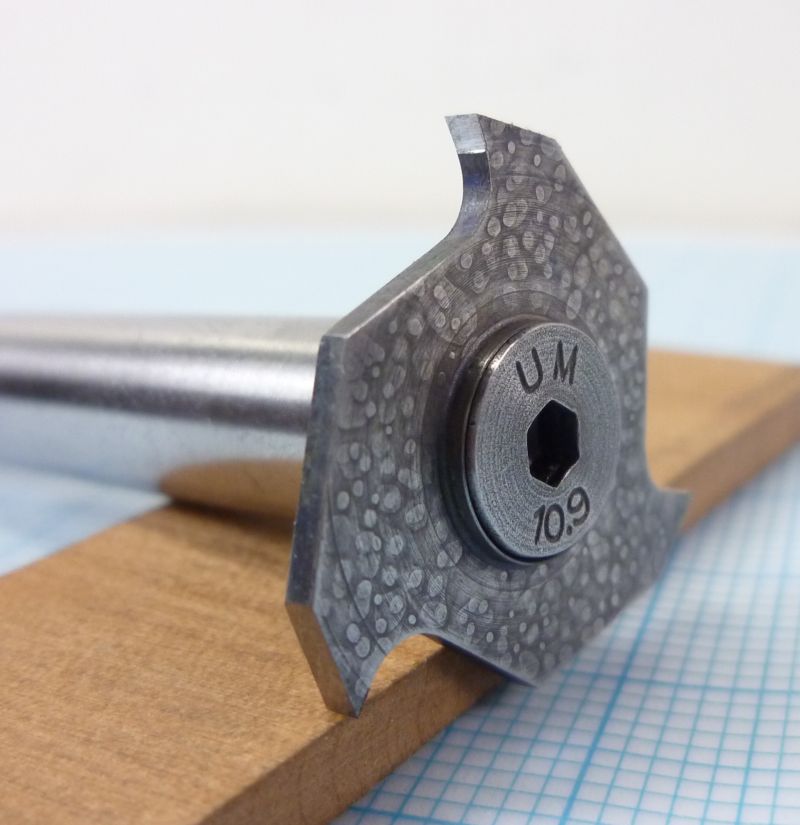
Finally I made two cutting blades of 1mm (0,04in) and 1,5mm (0,06in) width.
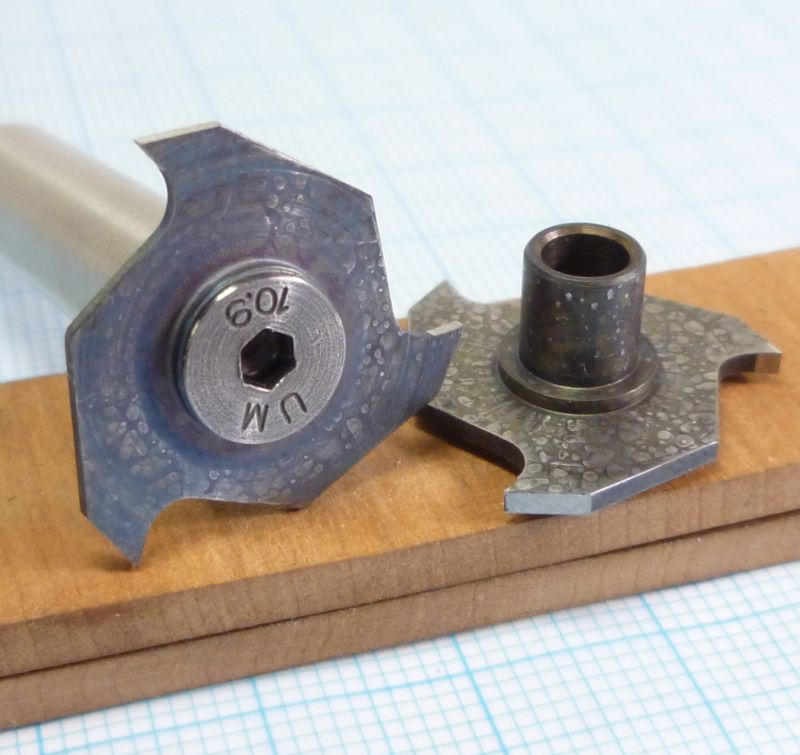
I didnt have the opportunity to run the cutters on my CNC portal with in the last days. But I made some testing on my bench miller which is recently rebuild with a frequency controlled induction motor, so I can run the spindle up to over 10 thousand rpm now. They both make a nice and sharp cut, no shatter and vibrations. I dont intend to use them on steel parts anyway, they are only made for machining aluminium, high strength alloy (EN-7075) and the mild machining EN-2007 quality.

After getting a good impression of the cutting force and the whole cutting behaviour on my bench miller I think the groove cutters will do their intended job right well. But being more fragile than the rigid commercial carbide groove cutters they must be driven with a little bit of care on the CNC. That means only small infeed per pass but fairly fast feed rates according to the high spindle revolution to get a suitable chip load.
At last a little example for what duty the cutter is designed .but this head construction is not finished yet ...it is only a rough layout for testing my CAM module.
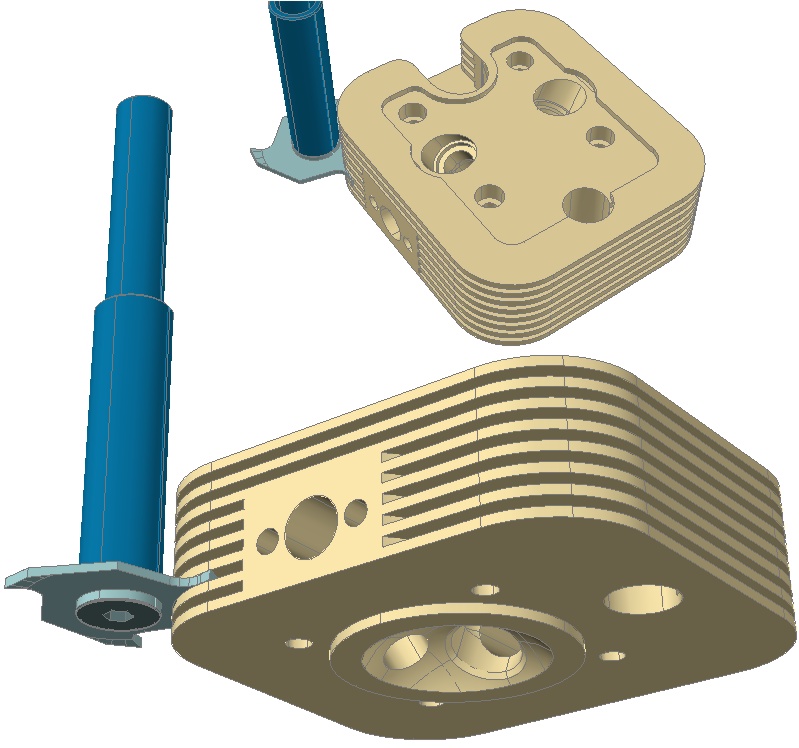
Achim