- Joined
- Jun 4, 2008
- Messages
- 3,294
- Reaction score
- 636
Until today I didn't have a good way to bore on my lathe. I previously made an aluminum holder to use with a broken endmill, but that didn't ever work very well, and the endmill is 1/2" diameter which elminated small holes. So I tended to rely on reaming to get a precise hole.
A while back I purchased a couple of "micro" carbide boring bars from a seller on PM, but they had lain unused for lack of a holder. Today I decided to make one. Here's the larger bar. The shank is 5/16" diameter and about 1.5" long:
I started with a 3" piece of 1" diameter 12L14 steel that I faced and drilled/reamed on the lathe. Then I chucked it in the milling vise and milled a 1/4" flat on the top. Following this I center drilled and drilled 7 holes on the flat for set screws. The next step was to clamp the bar with the flat against the fixed jaw and mill the relief cuts. They are ~3/8 wide and test fit on the AXA tool holder. Finally I tapped the holes for 5-40 set screws. Here's the assemblage:
Note that the boring bar has a flat on the top, so that the set screws assure a horizontal alignment of the cutting surface. I also cut both the side reliefs at the same time so that the holder will mount squarely on the AXA holder.
Mounted on the QCTP:
I use the quill of the tailstock to align the holder, and thus the boring bar, with the ways. After adjusting for height, a first practice cut produced an excellent result. I'm pretty happy with 90 minutes or so of shop work to make this. The other boring bar is a lot smaller, so I think I can make a bushing that will allow me to use it in the same holder.
A while back I purchased a couple of "micro" carbide boring bars from a seller on PM, but they had lain unused for lack of a holder. Today I decided to make one. Here's the larger bar. The shank is 5/16" diameter and about 1.5" long:
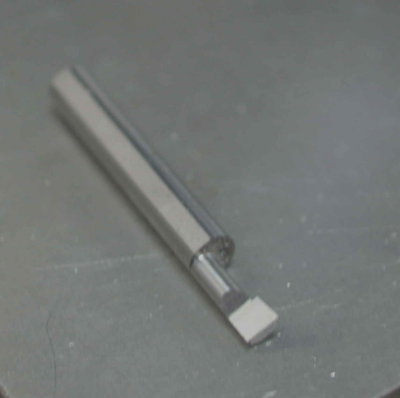
I started with a 3" piece of 1" diameter 12L14 steel that I faced and drilled/reamed on the lathe. Then I chucked it in the milling vise and milled a 1/4" flat on the top. Following this I center drilled and drilled 7 holes on the flat for set screws. The next step was to clamp the bar with the flat against the fixed jaw and mill the relief cuts. They are ~3/8 wide and test fit on the AXA tool holder. Finally I tapped the holes for 5-40 set screws. Here's the assemblage:
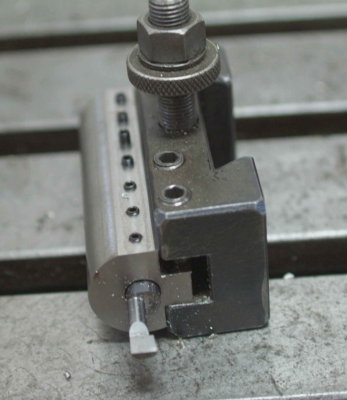
Note that the boring bar has a flat on the top, so that the set screws assure a horizontal alignment of the cutting surface. I also cut both the side reliefs at the same time so that the holder will mount squarely on the AXA holder.
Mounted on the QCTP:
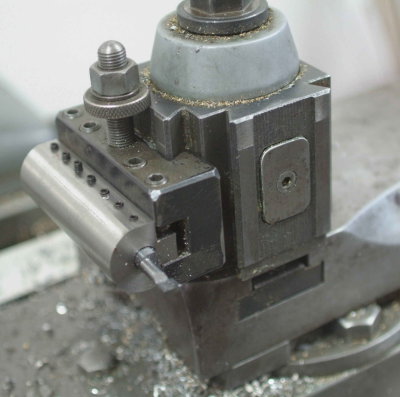
I use the quill of the tailstock to align the holder, and thus the boring bar, with the ways. After adjusting for height, a first practice cut produced an excellent result. I'm pretty happy with 90 minutes or so of shop work to make this. The other boring bar is a lot smaller, so I think I can make a bushing that will allow me to use it in the same holder.
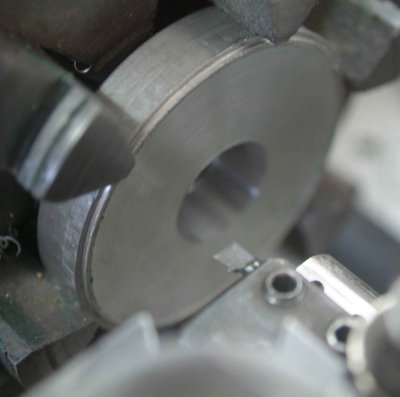