aonemarine
Well-Known Member
- Joined
- Nov 18, 2012
- Messages
- 887
- Reaction score
- 212
Well I got my G0704 mill today and the steppers and drivers. Im waiting on a conversion kit from arizona video on you tube to finish the pkg. I made a couple of passes with the mill today and can tell right away im for a learning cure. This mill is no where near as ridgid as my bridgeport. Im hoping that after getting to know it a little better, and getting the right speeds and feeds will improve upon the finish, time will tell..
any one play with one of these? I could use some honest insight...
any one play with one of these? I could use some honest insight...
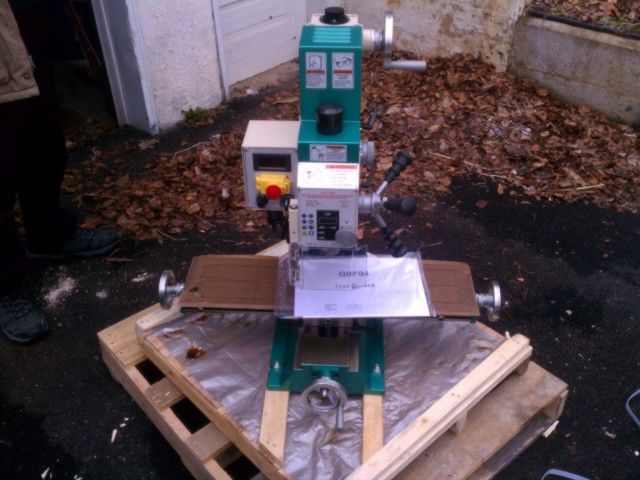
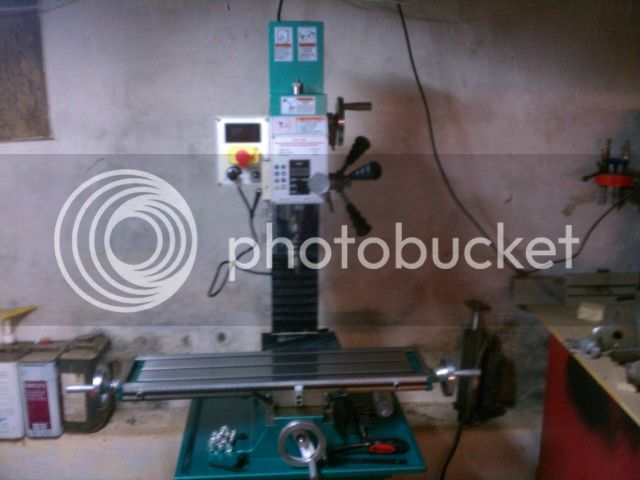
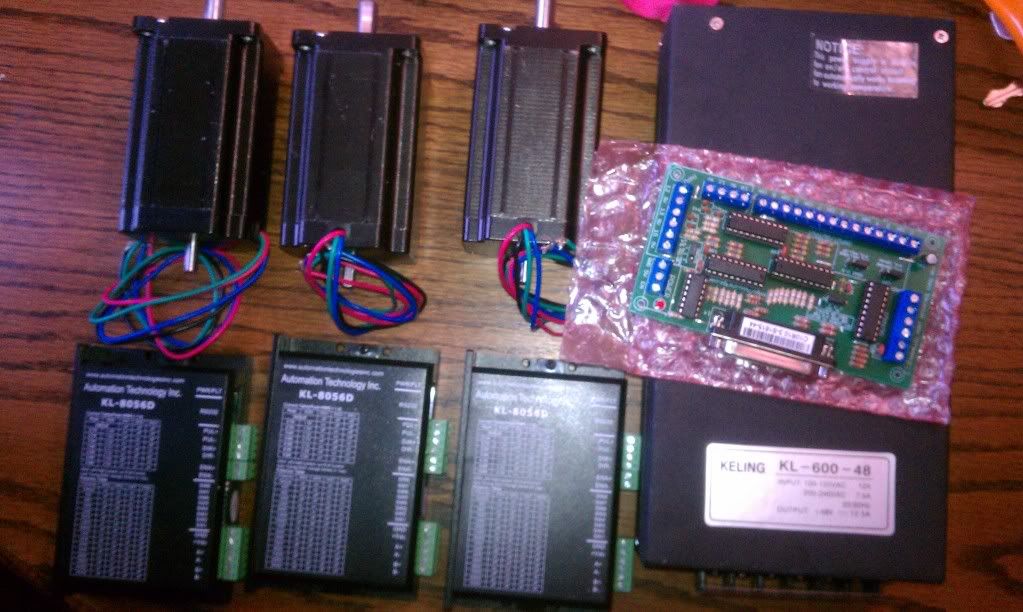