So looking round for bits to do for the display board and reading a post on another group about flywheels so great a fancy flywheel.
Did a web search for some drawing but only found a few pictures so decided to draw one out.
I took close note on the time spent on all the aspects.
started after tea tonight and drew a flywheel up in Fastcad which took 15 minutes but I am used to the program, then went out to see what material I had in the bits drawer.
Came back in and altered the drawing to suit the bit of 85mm brass that I had found.
[ Note to self - check material first ]
Another 10 minutes spent scaling the drawing to fit the brass :-X
Moved the drawing into VCarve and processed it, that took 25 minutes but some of that time was spent putting some engraving on the edge.
Shot into the workshop at just gone 10.00pm on the pretext of locking up, put the brass in the chuck already on the bed, set the 6mm cutter and the corner radiusing cutter up - forget the engraving that 85mm brass was actually 82mm [ well it's been a long day ]
Pocket the recess and cut the spokes out - 18 minutes
Change cutter for the corner radiusing, press go and Oh shite, 3,786 miles per hour [ approx ]
12 seconds to radius the spokes and 17 seconds to radius the recess
Well at least it came out alright even if it was a bit frightening.
Locked up and went back in, checked the program and because the radiusing cutter was 3/32" on a 3/8" shank it was programmed as imperial. so my 175mm per min which is quite sensible turns out to be 175 in per minute, about 4,400 mm per min, as I say it was a long day............
Anyway here's the picture, ignore the stupid sized hole in the middle, that was already in the brass blank.
.
Did a web search for some drawing but only found a few pictures so decided to draw one out.
I took close note on the time spent on all the aspects.
started after tea tonight and drew a flywheel up in Fastcad which took 15 minutes but I am used to the program, then went out to see what material I had in the bits drawer.
Came back in and altered the drawing to suit the bit of 85mm brass that I had found.
[ Note to self - check material first ]
Another 10 minutes spent scaling the drawing to fit the brass :-X
Moved the drawing into VCarve and processed it, that took 25 minutes but some of that time was spent putting some engraving on the edge.
Shot into the workshop at just gone 10.00pm on the pretext of locking up, put the brass in the chuck already on the bed, set the 6mm cutter and the corner radiusing cutter up - forget the engraving that 85mm brass was actually 82mm [ well it's been a long day ]
Pocket the recess and cut the spokes out - 18 minutes
Change cutter for the corner radiusing, press go and Oh shite, 3,786 miles per hour [ approx ]
12 seconds to radius the spokes and 17 seconds to radius the recess
Well at least it came out alright even if it was a bit frightening.
Locked up and went back in, checked the program and because the radiusing cutter was 3/32" on a 3/8" shank it was programmed as imperial. so my 175mm per min which is quite sensible turns out to be 175 in per minute, about 4,400 mm per min, as I say it was a long day............
Anyway here's the picture, ignore the stupid sized hole in the middle, that was already in the brass blank.
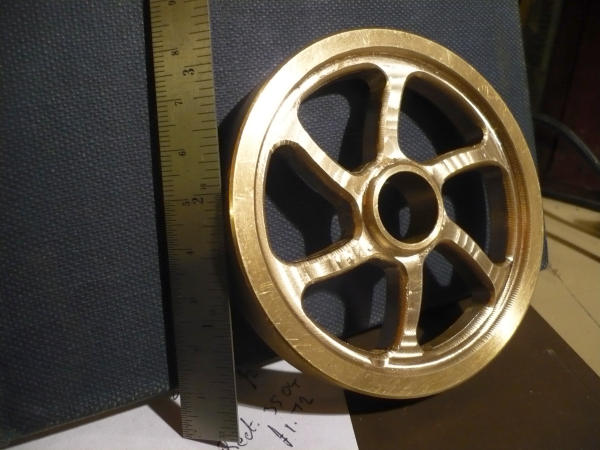
.