Sshire
Well-Known Member
- Joined
- Jun 29, 2011
- Messages
- 935
- Reaction score
- 267
Elmers #29 - Mine Engine
Mine, All Mine
Episode 1
And you thought Id gone into hiding. No such luck. Couldnt resist starting a new build.
Ive been looking at this one for a while and the plans have migrated to the top of the pile. After looking at the size (small), I almost did a 2X build but I smacked myself and came to my senses. A larger version isnt out of the question down the road.
Here is the assembly drawing. This, along with the Pumping Engine, are two of Elmers better looking designs.
As I began to square up the floor (.125) there was way too much chatter because if was too far above the vise jaws. I swapped the stock Kurt jaws for these 3 MonsterJaws. Problem solved. I know that clamping a part high on tall jaws is not a good idea, but full height clamping works just fine.
After squaring up and sizing the floor, base and sub-base, the face mill with the super sharp non-ferrous inserts, does its work.
I laid out the three base parts. Even though Im using the DRO, I like to do a layout as a double-check.
Drilling and deburring. I should have gotten this Noga Rotadrive deburring/chamfering tool long ago. Very quick and no machine setups.
Then drilling, tapping and slot milling.
The bases will have a 5 degree bevel at some point. Right now, Im keeping them square in case I have to put them back in the vise.
Next are 4 posts. .250 diameter with 5-40 threaded ends. Since these support a plate that has the crosshead guide, it seemed critical to have them at identical lengths. Collet stops on the lathe are close but can have variation in how far the part sticks depending on how tight you crank on the collet thread. I wasnt that thrilled with the prospect of taking a facing cut, removing the part, measuring and remounting the part.
Of course, the easy way is to take a longer piece, poke it through the collet and spindle bore and part off to length. I dont have a spider on the end of my spindle, but I did try this, starting the lathe very slowly. By the time I got to about 100 RPM, I thought I noticed the free end beginning to move. Not wanting to bend, or otherwise distort the only .250 brass round in stock. I came up with another way.
I cut the four pieces about 30 thou long and cleaned up one end at the mill. I did switch to V-jaws.
With the rod of the vise stop slid into the v-jaw, I was able to get perfectly repeatable lengths.
The drawing says 3.0625. Each piece had no more than a half thou variation.
With that done, I used the DRO on the lathe to turn the threaded parts to a length of .250.
With the posts threaded in place, its time to move on to the table. I realized Id need 5-40 nuts to half the table so those came first.
.250 12L14 Hex bar, drilled and tapped.
Corners knocked off
Parted off. If you look at the back of the nut, you can see that I turned a small boss. Help! Does this feature have a name?
I went a bit too far on the corners. I think the arc is supposed to meet the flat. I need to use my 10X magnifier when I remake them. Any nut tips would be appreciated.
Now for the table. All laid out and ready for the mill.
Everything is referenced from the center of the table.
2-56 form tap. This is a Balax. I only say that because they were the only form tap manufacturer whose tech support guy would talk to me after finding out that I wasnt General Motors or NASA. He was fascinated when I mentioned small engines and spent a long time telling me more than anyone needs to know about form taps. Im a committed Balax purchaser and quite sure that the 5 form taps Ive bought this year made a significant difference to their bottom line.
Bolt hole circle
Slots milled and that finished this part.
So, here we are after two days in the shop. More to come.
Mine, All Mine
Episode 1
And you thought Id gone into hiding. No such luck. Couldnt resist starting a new build.
Ive been looking at this one for a while and the plans have migrated to the top of the pile. After looking at the size (small), I almost did a 2X build but I smacked myself and came to my senses. A larger version isnt out of the question down the road.
Here is the assembly drawing. This, along with the Pumping Engine, are two of Elmers better looking designs.
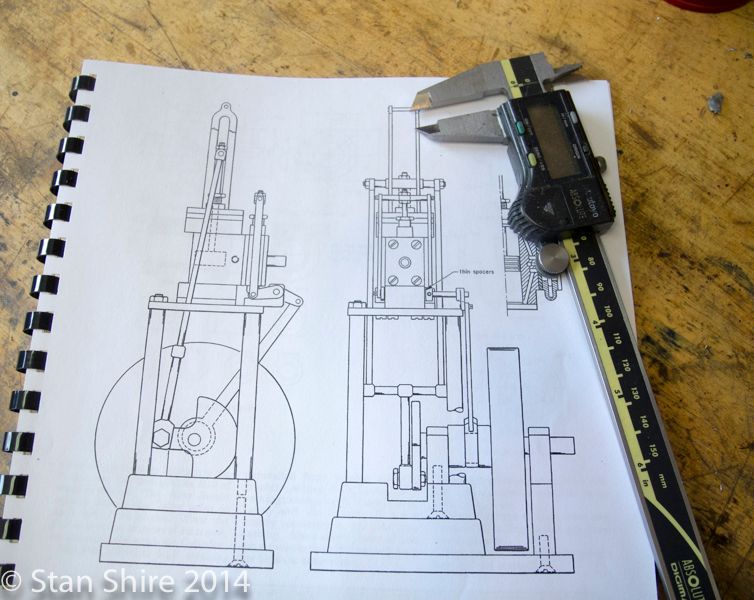
As I began to square up the floor (.125) there was way too much chatter because if was too far above the vise jaws. I swapped the stock Kurt jaws for these 3 MonsterJaws. Problem solved. I know that clamping a part high on tall jaws is not a good idea, but full height clamping works just fine.
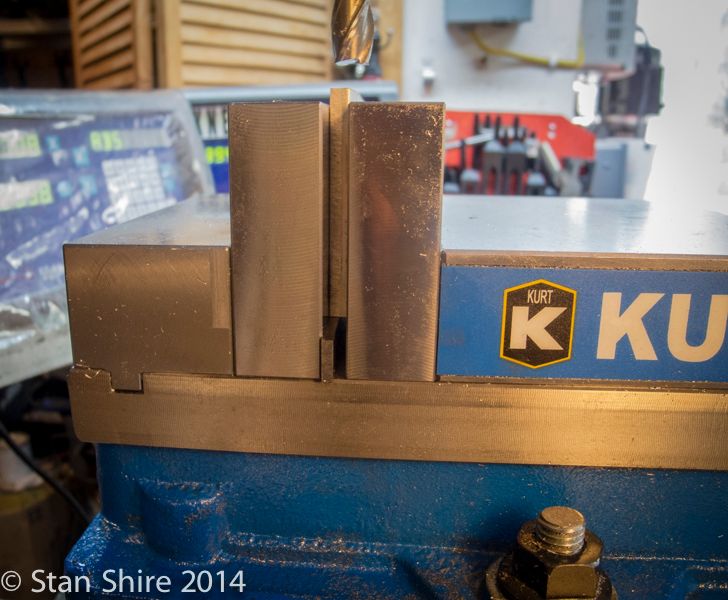
After squaring up and sizing the floor, base and sub-base, the face mill with the super sharp non-ferrous inserts, does its work.
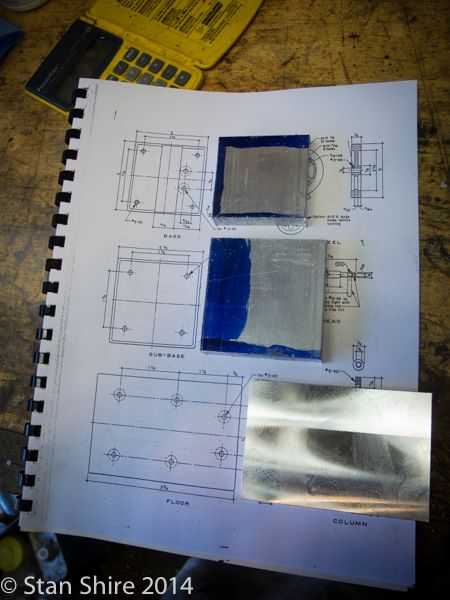
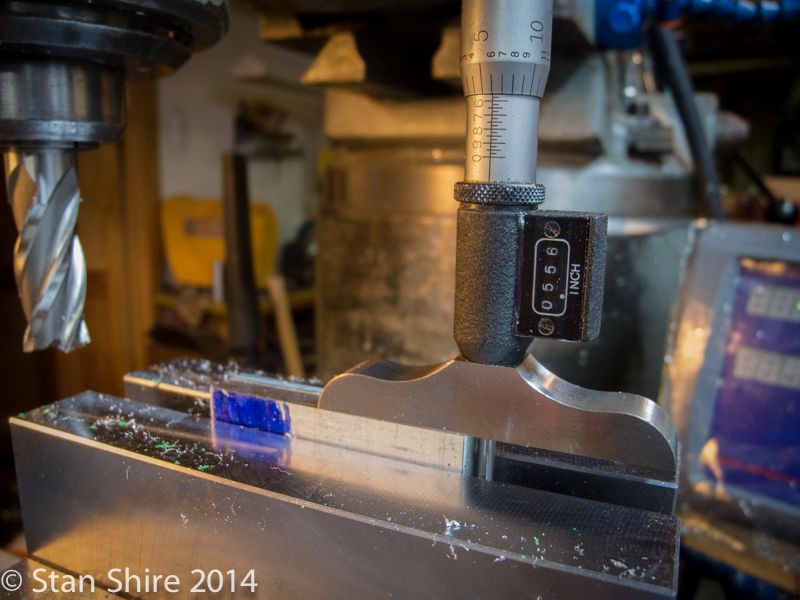
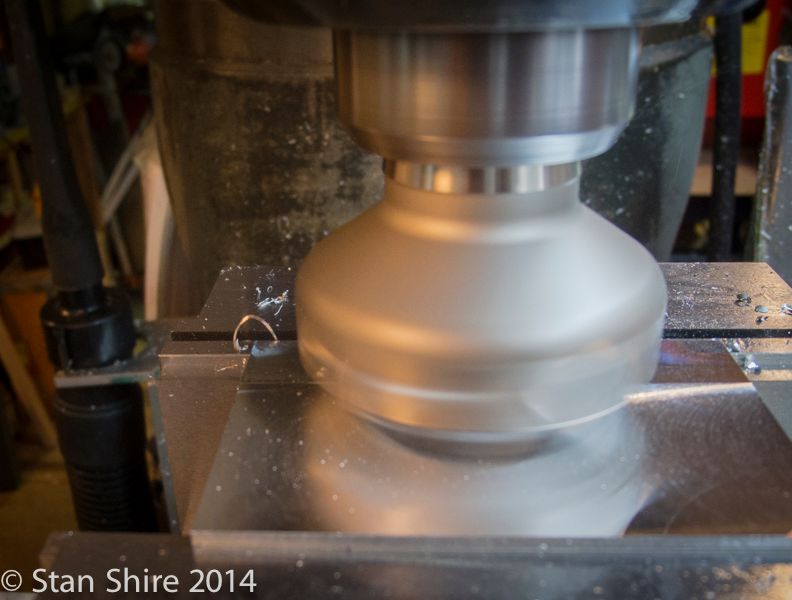
I laid out the three base parts. Even though Im using the DRO, I like to do a layout as a double-check.
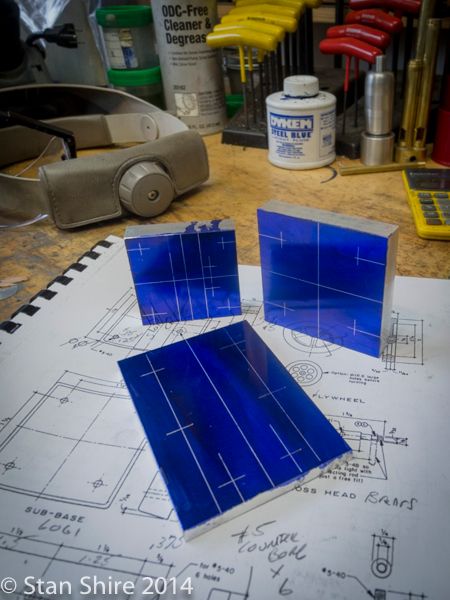
Drilling and deburring. I should have gotten this Noga Rotadrive deburring/chamfering tool long ago. Very quick and no machine setups.
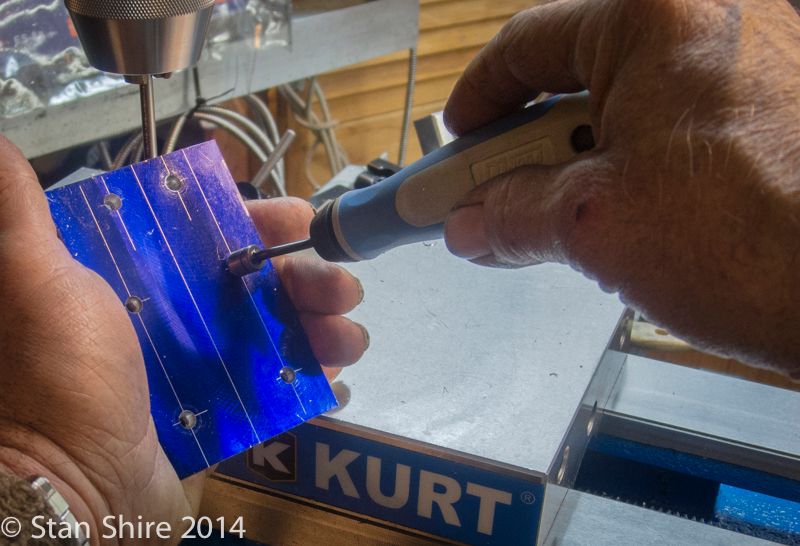
Then drilling, tapping and slot milling.
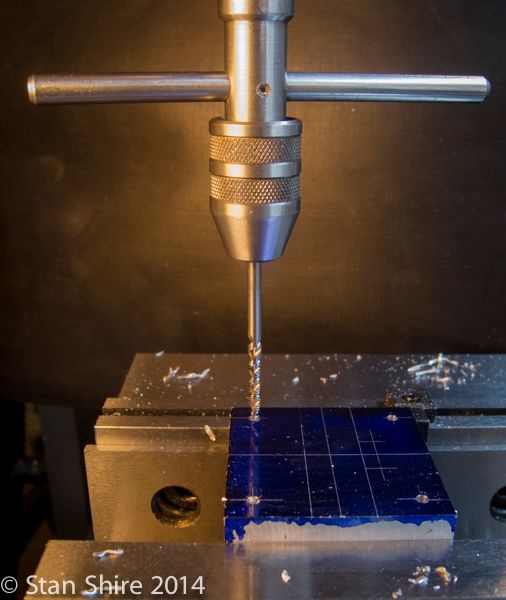
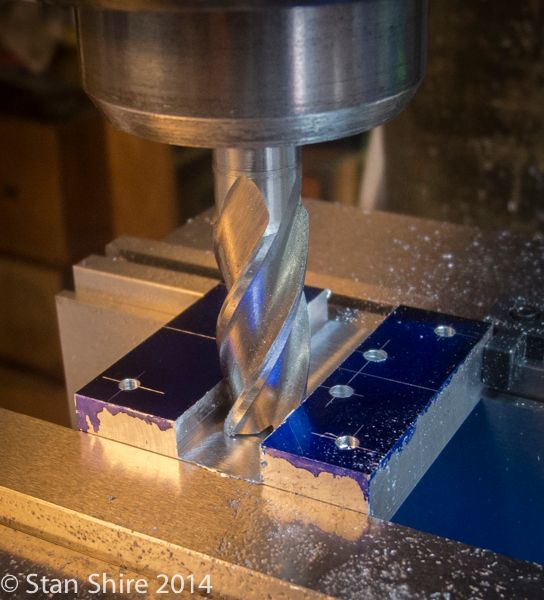
The bases will have a 5 degree bevel at some point. Right now, Im keeping them square in case I have to put them back in the vise.
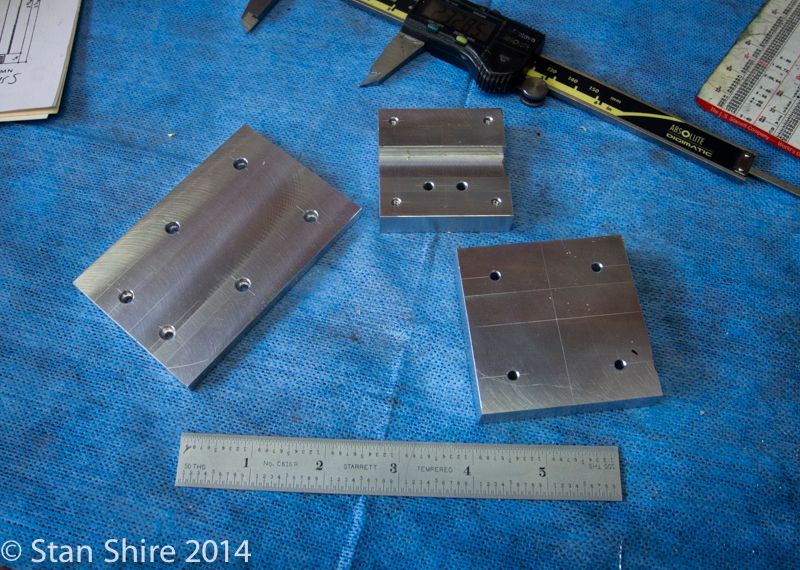
Next are 4 posts. .250 diameter with 5-40 threaded ends. Since these support a plate that has the crosshead guide, it seemed critical to have them at identical lengths. Collet stops on the lathe are close but can have variation in how far the part sticks depending on how tight you crank on the collet thread. I wasnt that thrilled with the prospect of taking a facing cut, removing the part, measuring and remounting the part.
Of course, the easy way is to take a longer piece, poke it through the collet and spindle bore and part off to length. I dont have a spider on the end of my spindle, but I did try this, starting the lathe very slowly. By the time I got to about 100 RPM, I thought I noticed the free end beginning to move. Not wanting to bend, or otherwise distort the only .250 brass round in stock. I came up with another way.
I cut the four pieces about 30 thou long and cleaned up one end at the mill. I did switch to V-jaws.
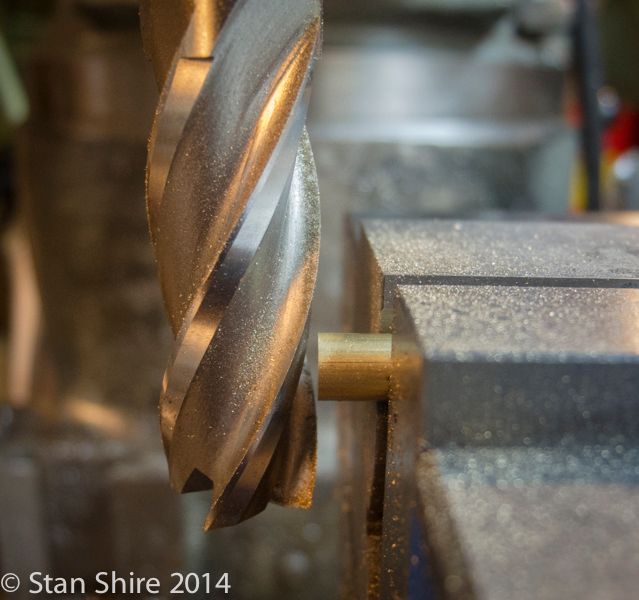
With the rod of the vise stop slid into the v-jaw, I was able to get perfectly repeatable lengths.
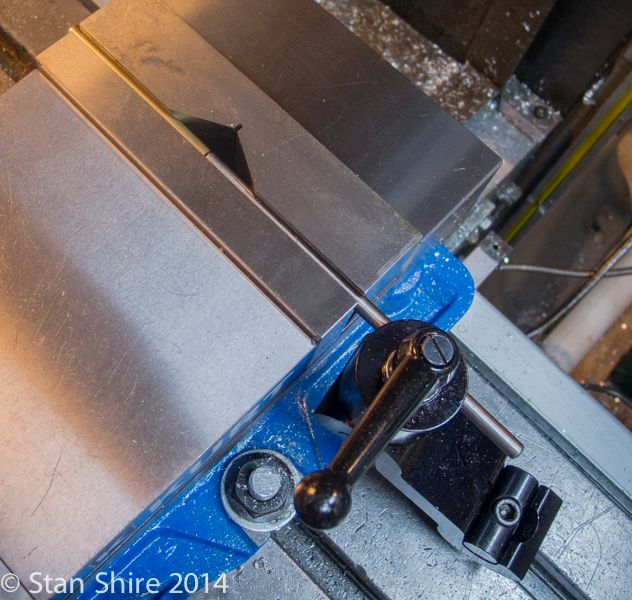
The drawing says 3.0625. Each piece had no more than a half thou variation.
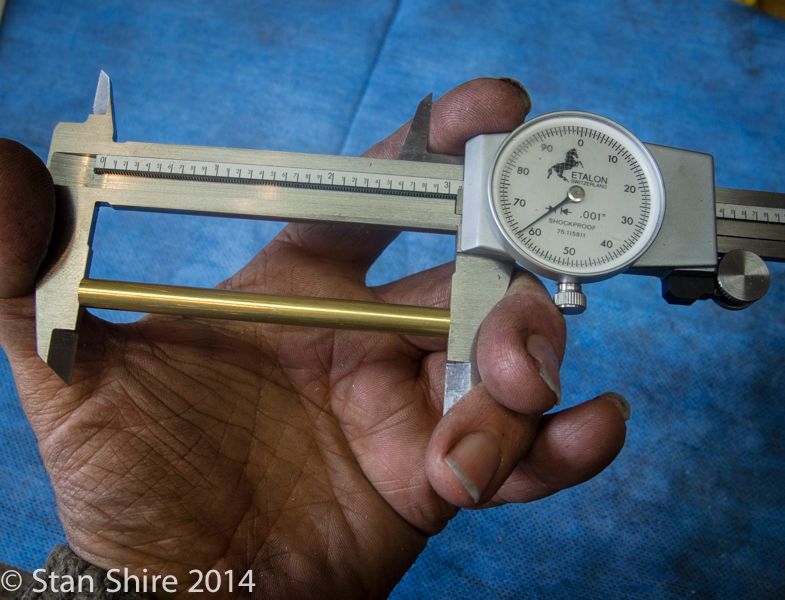
With that done, I used the DRO on the lathe to turn the threaded parts to a length of .250.
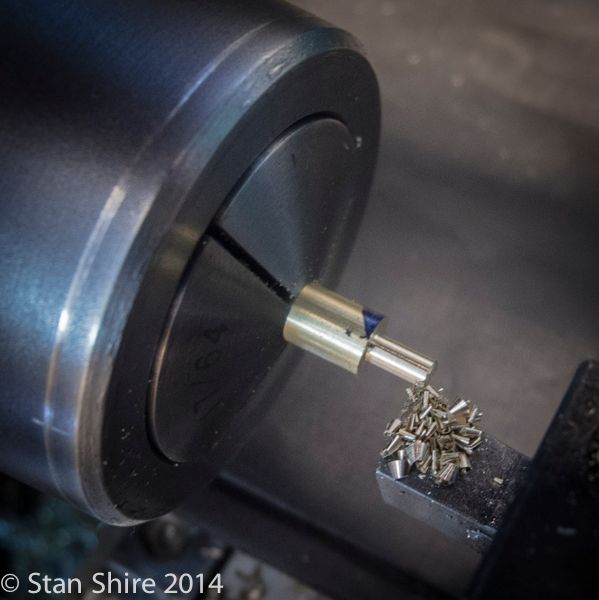
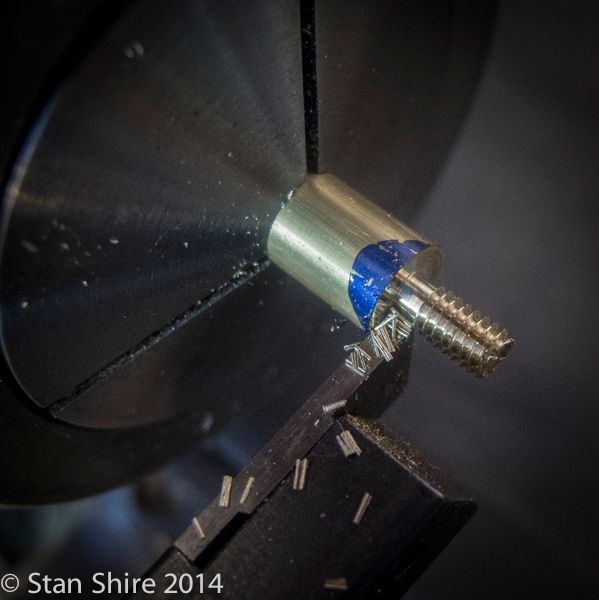
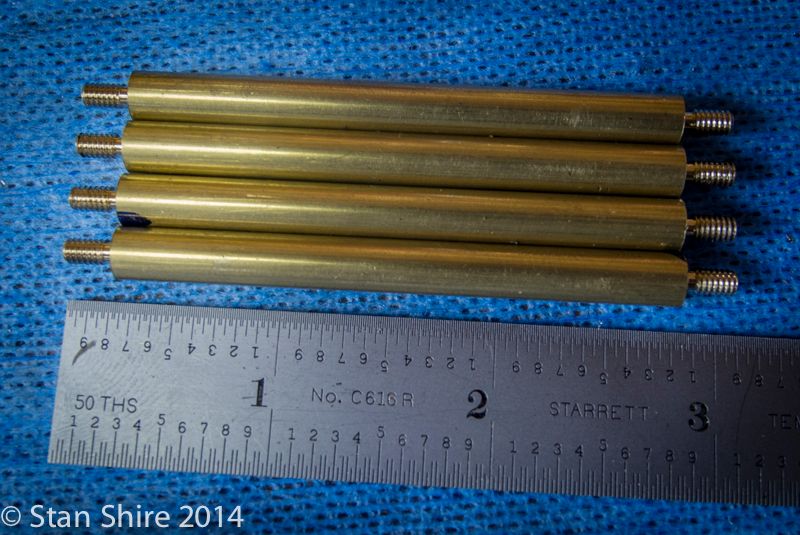
With the posts threaded in place, its time to move on to the table. I realized Id need 5-40 nuts to half the table so those came first.
.250 12L14 Hex bar, drilled and tapped.

Corners knocked off
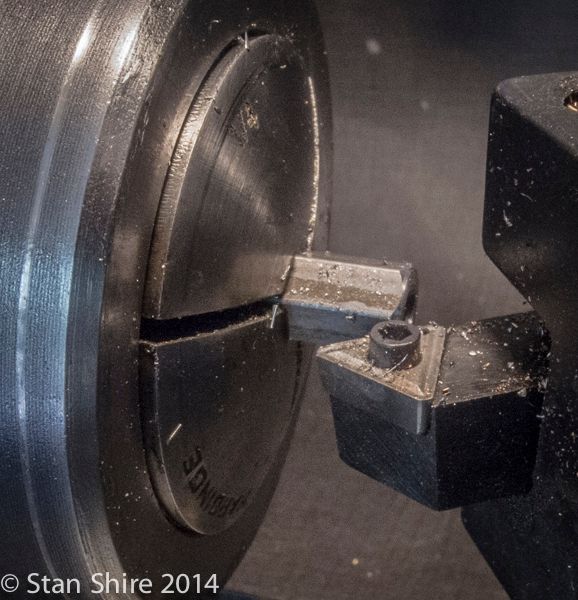
Parted off. If you look at the back of the nut, you can see that I turned a small boss. Help! Does this feature have a name?
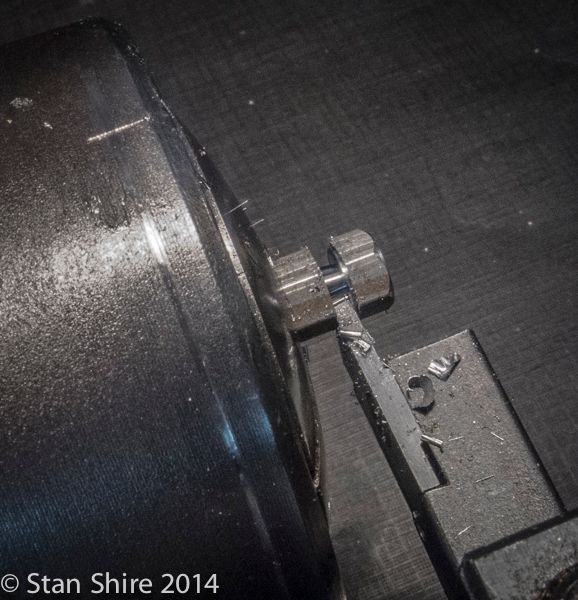
I went a bit too far on the corners. I think the arc is supposed to meet the flat. I need to use my 10X magnifier when I remake them. Any nut tips would be appreciated.
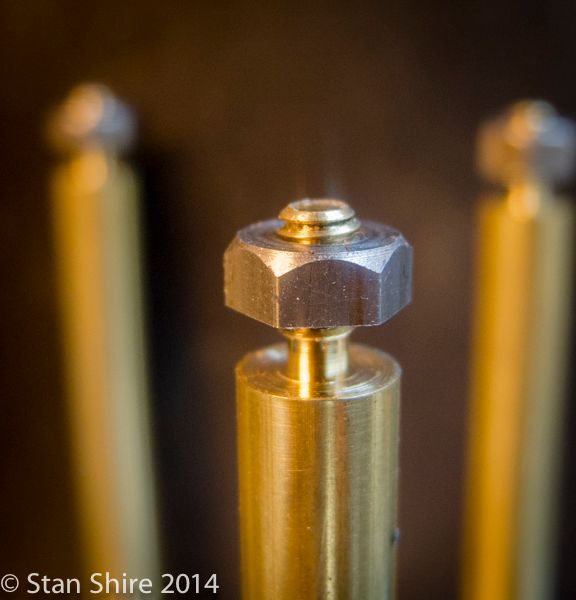
Now for the table. All laid out and ready for the mill.
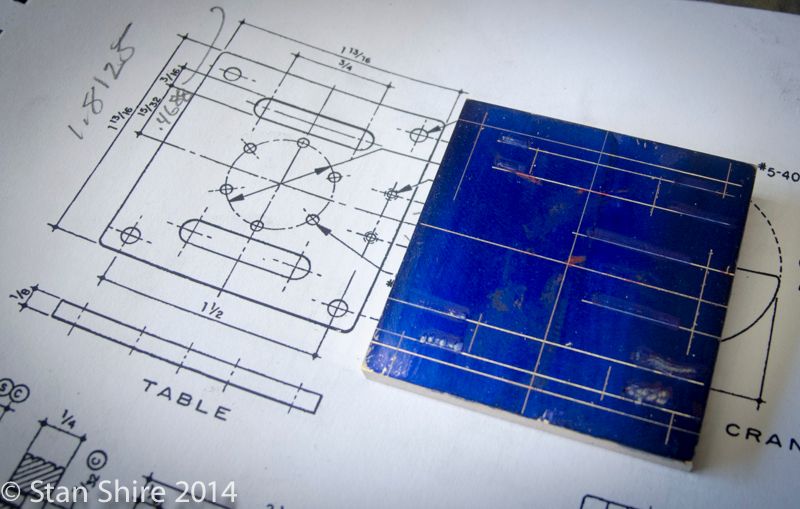
Everything is referenced from the center of the table.
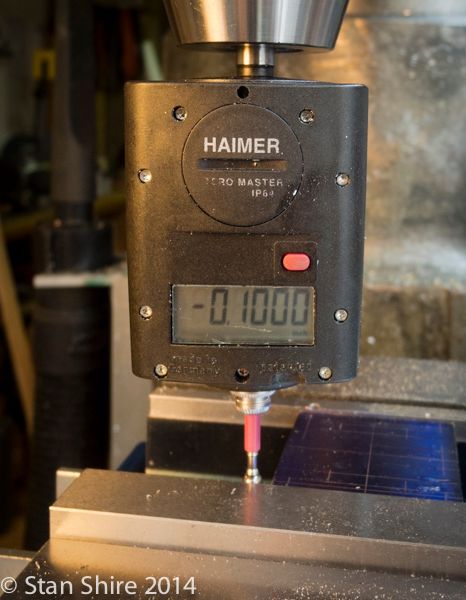
2-56 form tap. This is a Balax. I only say that because they were the only form tap manufacturer whose tech support guy would talk to me after finding out that I wasnt General Motors or NASA. He was fascinated when I mentioned small engines and spent a long time telling me more than anyone needs to know about form taps. Im a committed Balax purchaser and quite sure that the 5 form taps Ive bought this year made a significant difference to their bottom line.
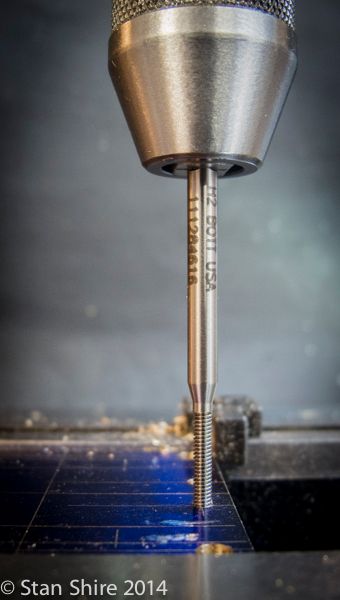
Bolt hole circle
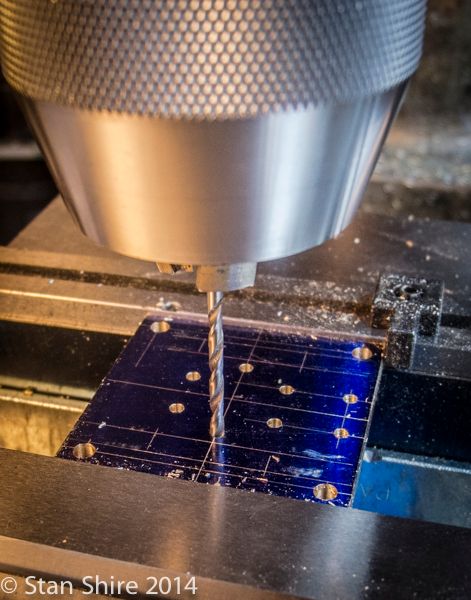
Slots milled and that finished this part.
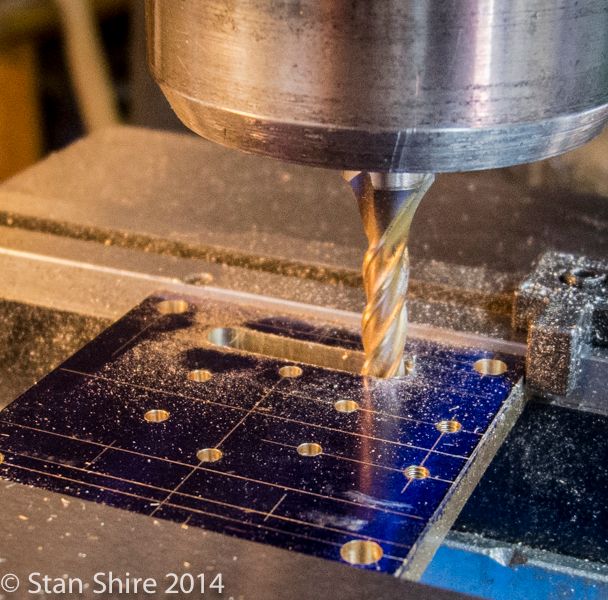
So, here we are after two days in the shop. More to come.
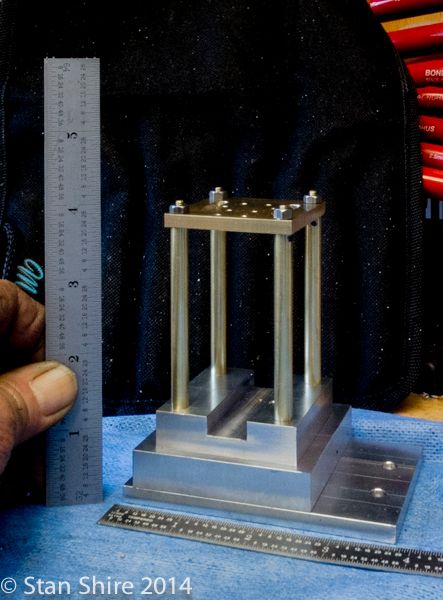