Twmaster
Well-Known Member
- Joined
- Oct 24, 2009
- Messages
- 917
- Reaction score
- 3
This evening I spent some quality time in my workshop. Earlier today I took a trip to a buddy's shop in OKC to use his bandsaw. I cut me off a half dozen 1" long chunks from a bar of 1" 12L14 hex.
Hiding in one of those chunks was this spindle adapter. This is for the old Craftsman/Dunlap model 109 lathes. The 109 has a very tiny spindle (1/2"-20 thread is typical). Finding good accessories for these is not easy. So the easy way is to have a spindle adapter. This goes from 1/2"-20 to 3/4"-16 like found on the Taig and Sherline lathes. This way you can use good US made chucks, faceplates etc.
Anyhow, after thinking for a bit how I wanted to make these I got busy and 2 hours later this popped out of the little hunk of bar.
Over the time I've been a member here I've read everything I've seen posted about single point threading. I don't know why but it always sorta made me break out in a sweat thinking about this operation.
Anyhow, it's a piece of cake. CAKE I SAY!!
As my lathe does not have a thread dial I simply ran the spindle by hand back and forth with an improvised crank handle.
I'm tickled pink needless to say.
Operations were really straight forward.
Face the ends. Center drill, drill with a 1/4" bit, enlarge hole with a 29/64 drill, tap for 1/2"-20 using a center in the tailstock to keep the tap aligned.
I have a nice little arbor with 1/2"-20 threads that I put in my ER-25 collet chuck and used as the holder for the remaining machining.
Next turn the part you want to thread down to just a hair under 3/4". Set compound to 29 degrees, align your 60 degree tool to the part, make a skim cut and check pitch with a gauge.
All looks great, cut some threads. I stopped periodically to see if a 3/4" die would spin on. When it did I just cleaned the threads up with the die. I made an undercut at the ends of the threads. Chamfer some edges. Done.
I spun a Taig 4 Jaw chuck onto the thing and it seated just like it belonged there! WOOOO!!
Anyhow. I applied more than a few things I learned here from the lot of you guys. Thank you. Thank you.
Hiding in one of those chunks was this spindle adapter. This is for the old Craftsman/Dunlap model 109 lathes. The 109 has a very tiny spindle (1/2"-20 thread is typical). Finding good accessories for these is not easy. So the easy way is to have a spindle adapter. This goes from 1/2"-20 to 3/4"-16 like found on the Taig and Sherline lathes. This way you can use good US made chucks, faceplates etc.
Anyhow, after thinking for a bit how I wanted to make these I got busy and 2 hours later this popped out of the little hunk of bar.
Over the time I've been a member here I've read everything I've seen posted about single point threading. I don't know why but it always sorta made me break out in a sweat thinking about this operation.
Anyhow, it's a piece of cake. CAKE I SAY!!
As my lathe does not have a thread dial I simply ran the spindle by hand back and forth with an improvised crank handle.
I'm tickled pink needless to say.
Operations were really straight forward.
Face the ends. Center drill, drill with a 1/4" bit, enlarge hole with a 29/64 drill, tap for 1/2"-20 using a center in the tailstock to keep the tap aligned.
I have a nice little arbor with 1/2"-20 threads that I put in my ER-25 collet chuck and used as the holder for the remaining machining.
Next turn the part you want to thread down to just a hair under 3/4". Set compound to 29 degrees, align your 60 degree tool to the part, make a skim cut and check pitch with a gauge.
All looks great, cut some threads. I stopped periodically to see if a 3/4" die would spin on. When it did I just cleaned the threads up with the die. I made an undercut at the ends of the threads. Chamfer some edges. Done.
I spun a Taig 4 Jaw chuck onto the thing and it seated just like it belonged there! WOOOO!!
Anyhow. I applied more than a few things I learned here from the lot of you guys. Thank you. Thank you.
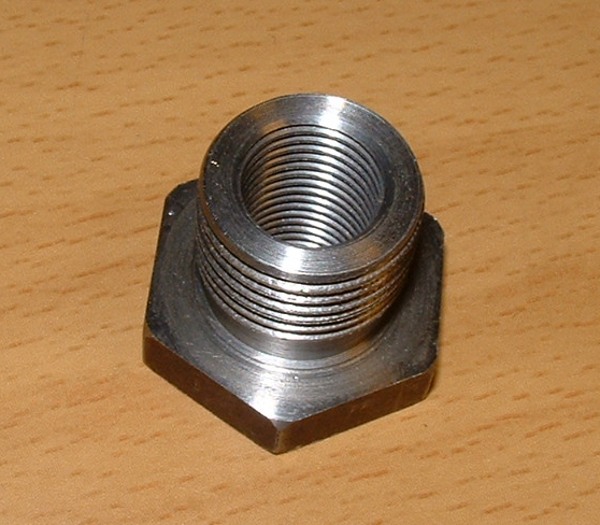
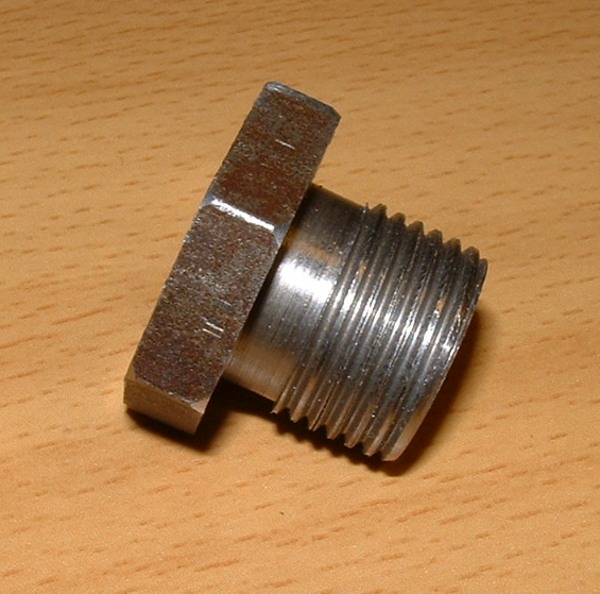