In my introductory post I said I would be starting my Boll Aero build shortly. Well it's taken me a week or so to get under-way, but I finally got started last night.
I have minimal equipment at this stage, and I chose the Boll Aero due to the low part count, and the fact that it can be built entirely with a lathe and a drilling machine. I have a Myford Super 7 lathe and a very budget drilling machine (lesson learned there!) and am slowly amassing the requisite hand tools, drills, taps, dies, reamers etc.
I've spent quite a bit of time already thinking through the machining sequences and how I will hold work pieces. I've written up a series of steps for the first three parts I plan to machine. Those being the crank case, the backplate and the main bearing (nose piece).
One challenge I have been grappling with is how to accurately drill the holes in the three parts given I don't have a mill and my drilling machine is a bit rubbish. The plan I came up with was to make a drilling jig that I would use to position the holes in all three pieces so the line up correctly.
To that end I started with a hole guage for the main bore. This will be used to locate the jig over the crankcase for drilling. This was the first time I had ever used my four jaw chuck. I made the tool post mount for the dial indicator as I thought that would be useful when it comes to squaring up the crankcase and other parts soon.
Turning up the hole gauge
Marking out the drilling jig
First time boring in the lathe!
Testing with the hole gauge
I used the point of the knife tool to scribe the PCD to locate the mounting holes on
And this is where I finished for the evening
So I just have drill the mounting holes in the jig tapping size so that I can spot drill through it later.
I am going to remake the hole gauge as I screwed up and overshot so that it is now 0.02mm undersize and so is a bit loose in the hole in the drilling jig. According to my digital calipers that is the correct bore size.
Next up the crankcase.
I have minimal equipment at this stage, and I chose the Boll Aero due to the low part count, and the fact that it can be built entirely with a lathe and a drilling machine. I have a Myford Super 7 lathe and a very budget drilling machine (lesson learned there!) and am slowly amassing the requisite hand tools, drills, taps, dies, reamers etc.
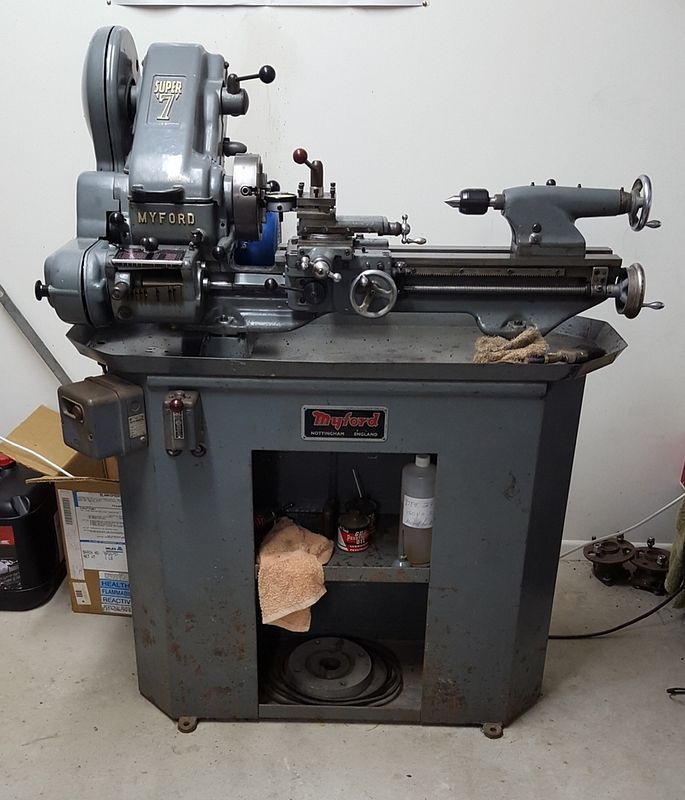
I've spent quite a bit of time already thinking through the machining sequences and how I will hold work pieces. I've written up a series of steps for the first three parts I plan to machine. Those being the crank case, the backplate and the main bearing (nose piece).
One challenge I have been grappling with is how to accurately drill the holes in the three parts given I don't have a mill and my drilling machine is a bit rubbish. The plan I came up with was to make a drilling jig that I would use to position the holes in all three pieces so the line up correctly.
To that end I started with a hole guage for the main bore. This will be used to locate the jig over the crankcase for drilling. This was the first time I had ever used my four jaw chuck. I made the tool post mount for the dial indicator as I thought that would be useful when it comes to squaring up the crankcase and other parts soon.
Turning up the hole gauge
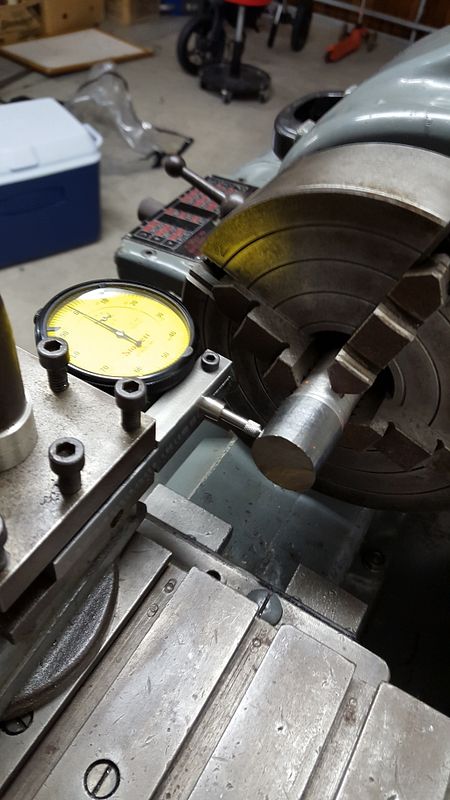
Marking out the drilling jig
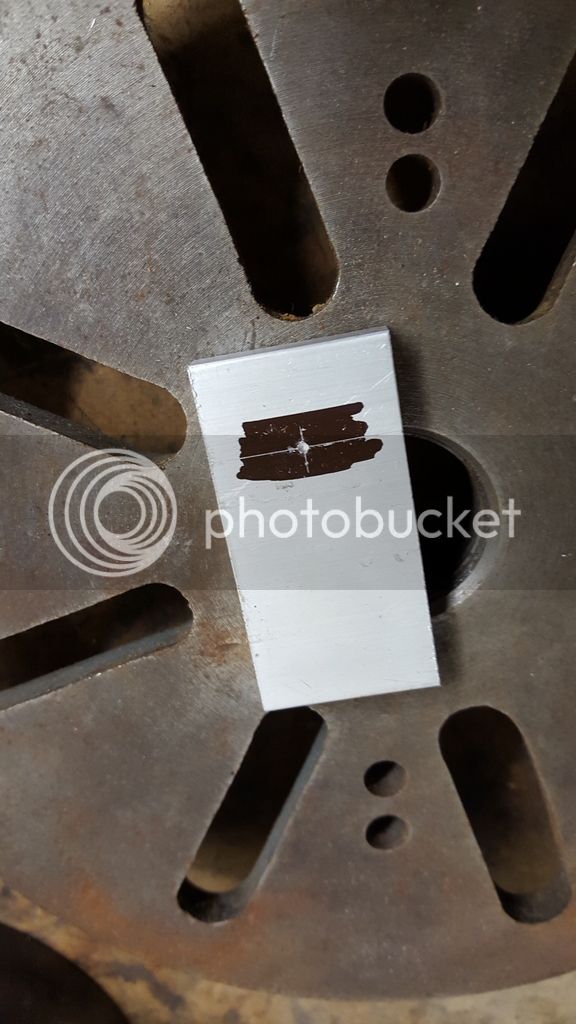
First time boring in the lathe!
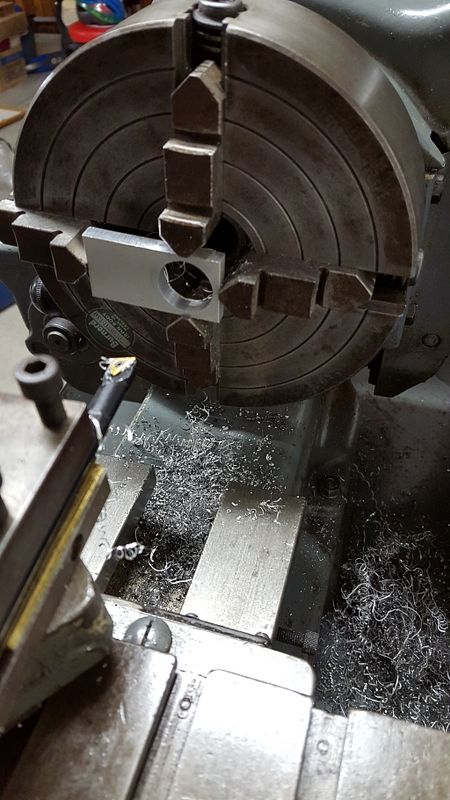
Testing with the hole gauge
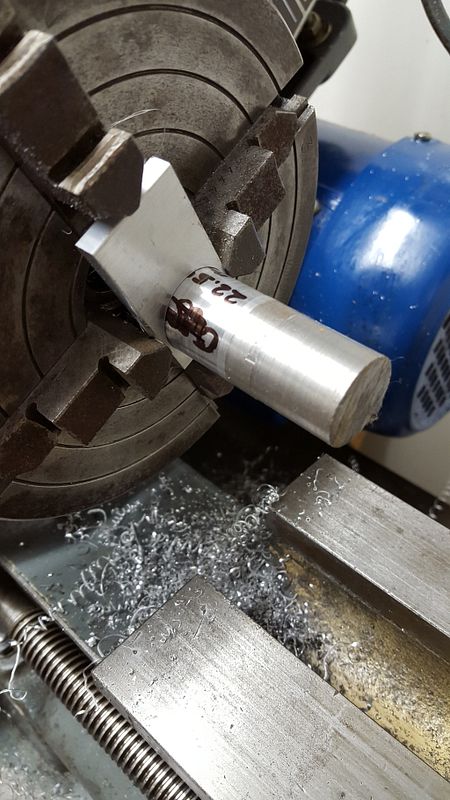
I used the point of the knife tool to scribe the PCD to locate the mounting holes on
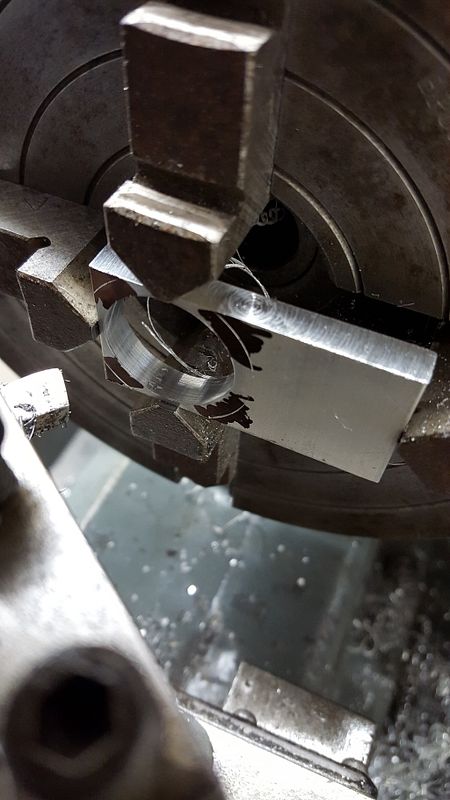
And this is where I finished for the evening
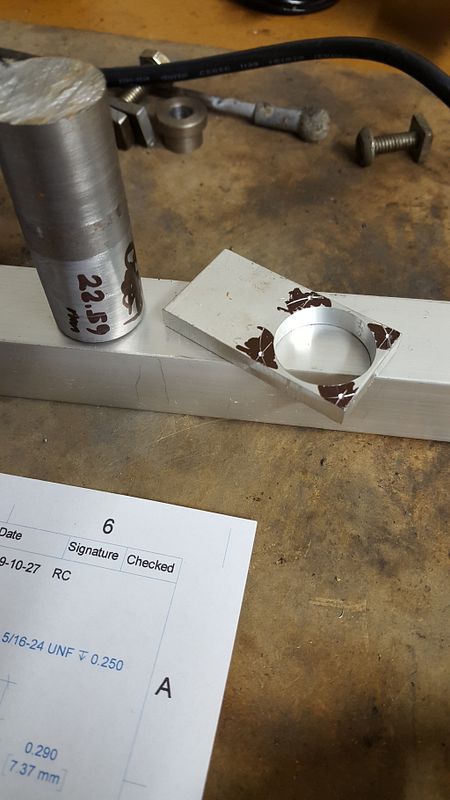
So I just have drill the mounting holes in the jig tapping size so that I can spot drill through it later.
I am going to remake the hole gauge as I screwed up and overshot so that it is now 0.02mm undersize and so is a bit loose in the hole in the drilling jig. According to my digital calipers that is the correct bore size.
Next up the crankcase.