This post isn't going to dwell on anything new or marvelous. However, some may find it interesting. I want to increase the diameter of the flywheel on the opposed piston engine I designed and built. I had originally built it with a 3 7/8" diameter flywheel, but found that it wasn't heavy enough. I had built in constraints that kept me from making a larger flywheel at the time, so I made it much thicker instead. This helped, but although the engine now runs, it still doesn't run as slow as I would like. I decided to keep the original flywheel, but add a 3/4" thick x 6" diameter ring to it, as the models show. Now what makes this interesting is that the largest diameter I can hold in my chuck is 4 1/4". This post will show how I managed to get around that obstacle.
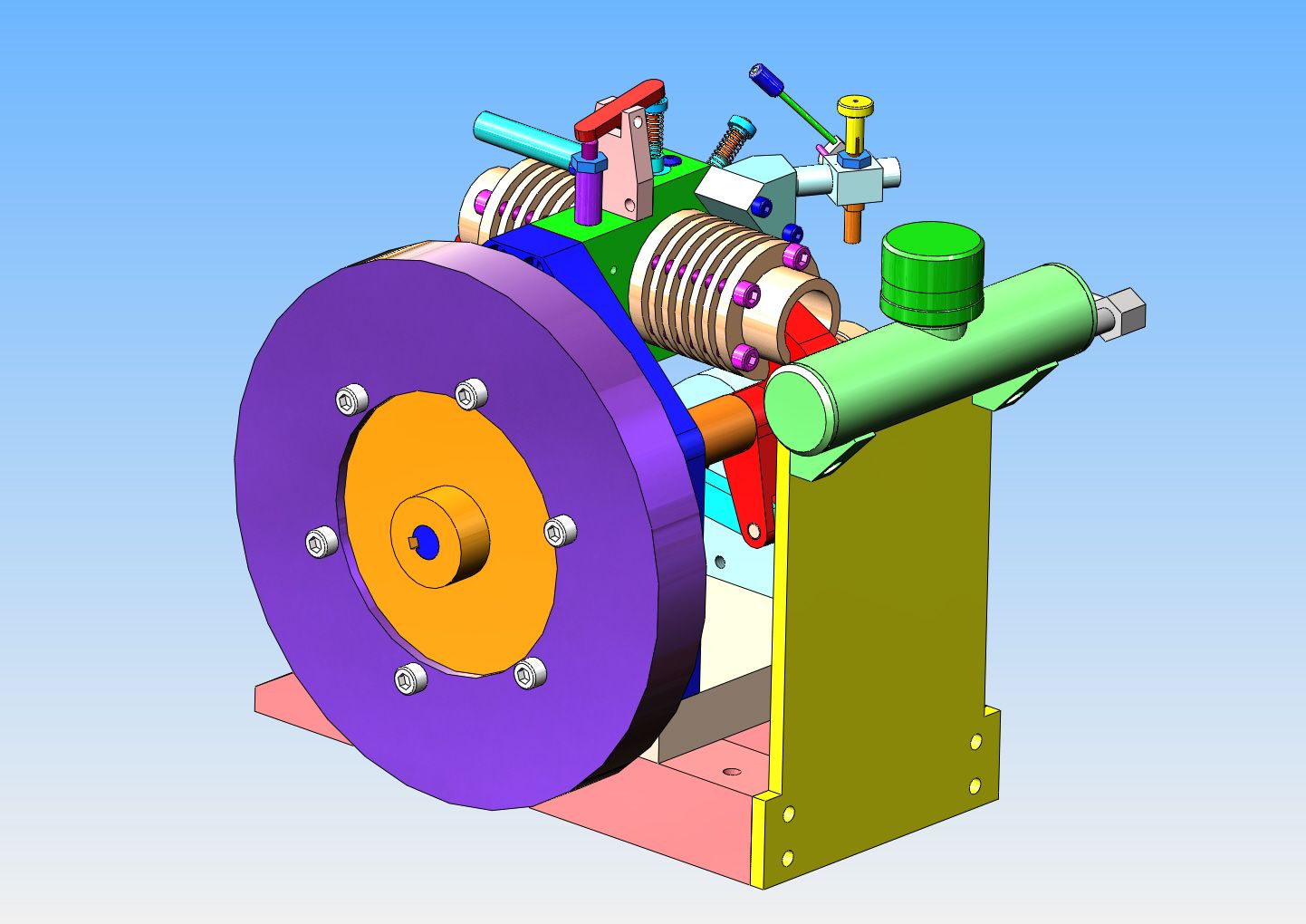
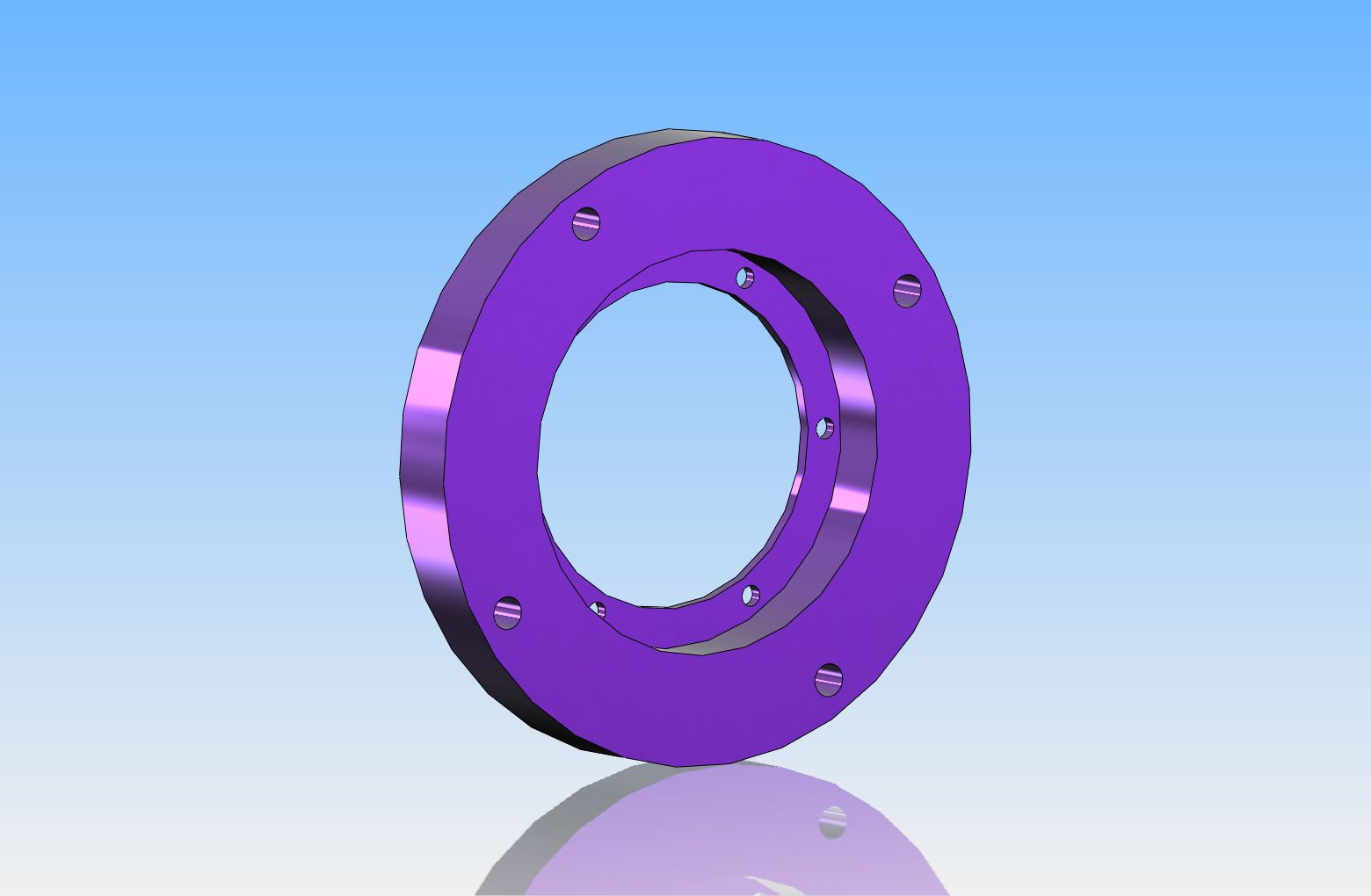