- Joined
- Feb 25, 2008
- Messages
- 464
- Reaction score
- 7
Hi,
I'm hoping someone will give me some advice on how to go about fabricating the cylinder block for the steam tractor I'm building. I have a thread going under works in progress, but this part is way ahead of where I am on the build as of today. However, I've been stewing and thinking about this and realize I need some help. Here's the rough outline of the part.
I've never made this combination of a cylinder and block. The material is brass. I'm thinking turn the cylinder, mill a flat on it and silver solder a rectangular block to it. Is this the way, or is there a better way?
I'm also new to silver solder, but have done some trial pieces and have read the threads and still have a couple of questions. I know I have to keep the two pieces from moving and also provide for a small gap between them (prick punch dimples). However, do I "tin" the two faces with silver solder before joining them or is it better to place small bits of solder randomly between them? Alternatively, if I apply solder to the joint from the outside edges will it wick all the way into the middle of the face (I'm a little shaky, so am not particularly thrilled with this approach)?
Any help or advice is greatly appreciated.
Regards,
Dennis
I'm hoping someone will give me some advice on how to go about fabricating the cylinder block for the steam tractor I'm building. I have a thread going under works in progress, but this part is way ahead of where I am on the build as of today. However, I've been stewing and thinking about this and realize I need some help. Here's the rough outline of the part.
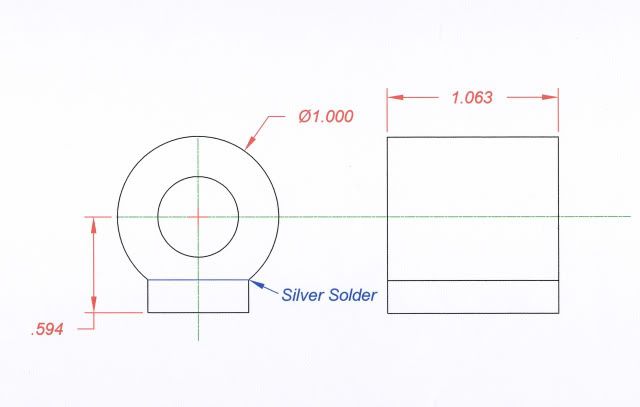
I've never made this combination of a cylinder and block. The material is brass. I'm thinking turn the cylinder, mill a flat on it and silver solder a rectangular block to it. Is this the way, or is there a better way?
I'm also new to silver solder, but have done some trial pieces and have read the threads and still have a couple of questions. I know I have to keep the two pieces from moving and also provide for a small gap between them (prick punch dimples). However, do I "tin" the two faces with silver solder before joining them or is it better to place small bits of solder randomly between them? Alternatively, if I apply solder to the joint from the outside edges will it wick all the way into the middle of the face (I'm a little shaky, so am not particularly thrilled with this approach)?
Any help or advice is greatly appreciated.
Regards,
Dennis