After a long break from any serious machining due to an epic crash (in my book at least) I am ready to have a new go at the job that ended so badly.
What I was trying to machine was this flywheel:
I am trying to come up with a procedure that in the end will give me a flywheel with as little runout as absolutely possible.
I have access only to a regular 3-jaw chuck. I have collets up to 12 mm.
My plan is to start with a 25 mm diamer brass bolt and chuck it in the 3 jaw. It should be fairly easy even for me to machine everything to the right. As the flywheel is rather short in relation to the diameter, I plan to do this without support from the tailstock.
But what puzzles me is how to approch the short 4 mm diameter ball bearing axle to the left. I can not for the life of me figure out how to do this without having to rechuck the part after parting it off. The size of the flywheel in relation to the diameter of the axle prohibits turning the axle without support of the tailstock. But at the tailstock end I have just a feeble 2mm axle sticking out, so to me it seems like using the tailstock is no option.
And if I have to rechuck the part, is there any chance of getting acceptable results with a three-jaw chuck?
I would be very grateful for suggestions on how to approach this!
Best regards,
Hauk.
What I was trying to machine was this flywheel:
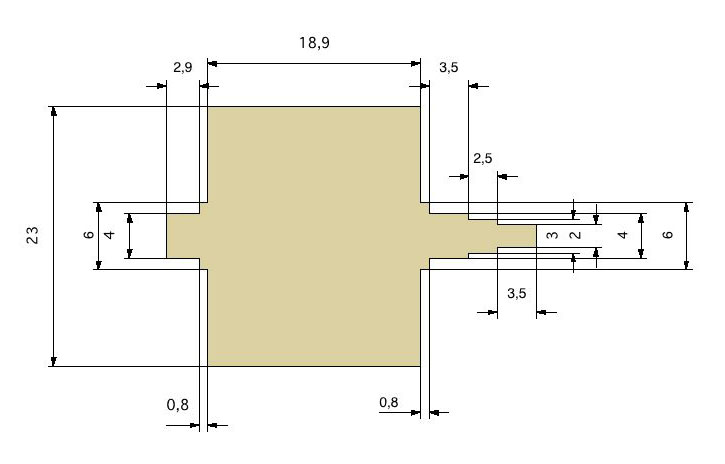
I am trying to come up with a procedure that in the end will give me a flywheel with as little runout as absolutely possible.
I have access only to a regular 3-jaw chuck. I have collets up to 12 mm.
My plan is to start with a 25 mm diamer brass bolt and chuck it in the 3 jaw. It should be fairly easy even for me to machine everything to the right. As the flywheel is rather short in relation to the diameter, I plan to do this without support from the tailstock.
But what puzzles me is how to approch the short 4 mm diameter ball bearing axle to the left. I can not for the life of me figure out how to do this without having to rechuck the part after parting it off. The size of the flywheel in relation to the diameter of the axle prohibits turning the axle without support of the tailstock. But at the tailstock end I have just a feeble 2mm axle sticking out, so to me it seems like using the tailstock is no option.
And if I have to rechuck the part, is there any chance of getting acceptable results with a three-jaw chuck?
I would be very grateful for suggestions on how to approach this!
Best regards,
Hauk.