arnoldb
Well-Known Member
- Joined
- Apr 8, 2009
- Messages
- 1,792
- Reaction score
- 12
I finished the height gauge today ;D - and used it for the first time as well.
First up - the top caliper retainer. Another bit of HRS sawn off, and lightly cleaned up, then clamped to the top guide for drilling for a couple of M3 cap screws:
I just drilled the holes 2.5mm for threading, then separated the lot and finished the retainer on it's own by enlarging the holes to 3mm for clearance, and counter bored with a 5mm end mill to recess the screw caps for a neater look. A cutout slightly wider than the caliper shank was milled into it - but not as deep as the caliper shank is thick. Then overall dimensions were milled to size, and the result:
The scriber tip was then taken outside - together with a can of oil, and heated red hot and dunked in the oil to cool down. This left it nice and black... So I cleaned off some of the black with emery, and gently heated it again only on the thick side till the cleaned area changed to a light yellow-orange colour close to the scriber tip. I then left it to cool down; that should be enough tempering. Then I cleaned it all up again, and lightly stoned the bottom of the piece on the sharpening stone, followed by quite a bit of stoning on the top angle to get it nice and sharp. It's pretty hard so takes a bit of effort to sharpen up:
Trying to get rid of the black left in the screw recesses seemed too daunting, so I left it :
Now for final assembly
A flat reference surface is needed; a surface plate would be ideal, but I don't have one. I do have the glass sheet that I use instead, so I thoroughly cleaned an area of it, as well as the underside of the base of the stand and the bottom of the scribing tip.
It's important that the caliper shank stands as close as possible to vertical - but if it's out of vertical by, say, 0.1mm over the 120mm range my caliper has, it would make the princely error of being out by about 0.00005mm over the measuring range... - way more accurate than can usually be measured in a home shop. So I just used a square against the protruding caliper tips to set it vertical in the stand:
Setting the scribing bit level and flat with respect to the base is more important. I did this by holding the scribing arm with the foot flat on the glass, and raising the caliper's top leg into the machined slot. Then a light tighten of the middle screw, followed by the outer ones, and that's that:
To make double sure, I measured the shank of a broken 1.4mm drill both at the tip of the scriber foot:
As well as at the back:
Finally; good to go; I'll get some shorter set screws to replace the ones holding the arm when I get to the nuts and bolts supplier next time:
In use for the first time on my next project:
MUCH easier than jiggling the workpiece to scribe some lines on it with a normal caliper ;D - I think I'm going to like this tool!
Regards, Arnold
First up - the top caliper retainer. Another bit of HRS sawn off, and lightly cleaned up, then clamped to the top guide for drilling for a couple of M3 cap screws:
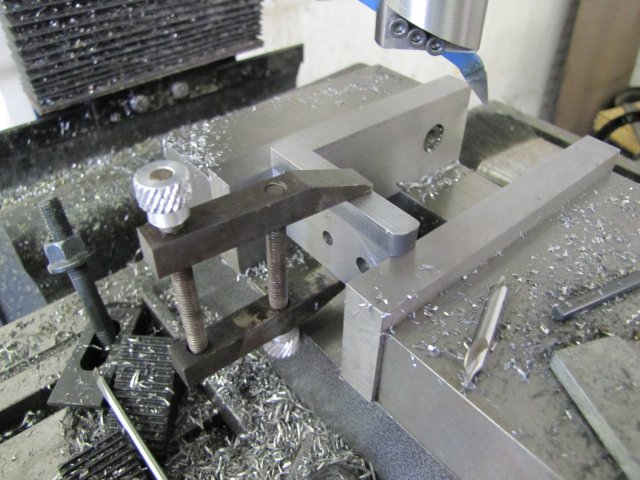
I just drilled the holes 2.5mm for threading, then separated the lot and finished the retainer on it's own by enlarging the holes to 3mm for clearance, and counter bored with a 5mm end mill to recess the screw caps for a neater look. A cutout slightly wider than the caliper shank was milled into it - but not as deep as the caliper shank is thick. Then overall dimensions were milled to size, and the result:
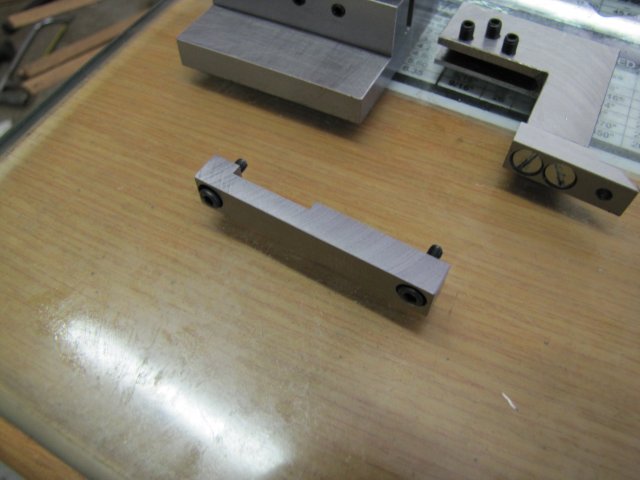
The scriber tip was then taken outside - together with a can of oil, and heated red hot and dunked in the oil to cool down. This left it nice and black... So I cleaned off some of the black with emery, and gently heated it again only on the thick side till the cleaned area changed to a light yellow-orange colour close to the scriber tip. I then left it to cool down; that should be enough tempering. Then I cleaned it all up again, and lightly stoned the bottom of the piece on the sharpening stone, followed by quite a bit of stoning on the top angle to get it nice and sharp. It's pretty hard so takes a bit of effort to sharpen up:
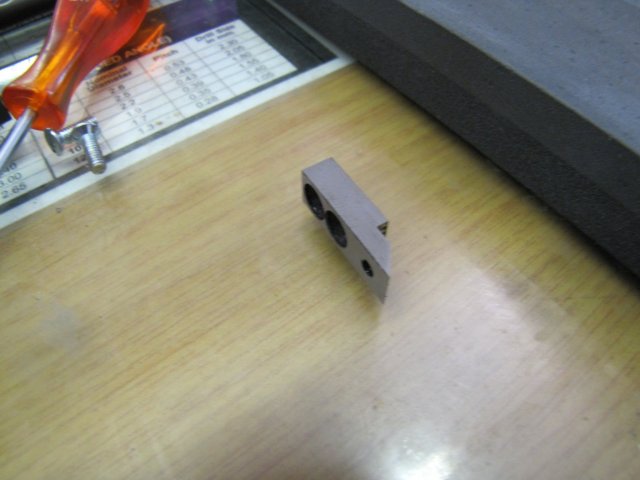
Trying to get rid of the black left in the screw recesses seemed too daunting, so I left it :
Now for final assembly
A flat reference surface is needed; a surface plate would be ideal, but I don't have one. I do have the glass sheet that I use instead, so I thoroughly cleaned an area of it, as well as the underside of the base of the stand and the bottom of the scribing tip.
It's important that the caliper shank stands as close as possible to vertical - but if it's out of vertical by, say, 0.1mm over the 120mm range my caliper has, it would make the princely error of being out by about 0.00005mm over the measuring range... - way more accurate than can usually be measured in a home shop. So I just used a square against the protruding caliper tips to set it vertical in the stand:
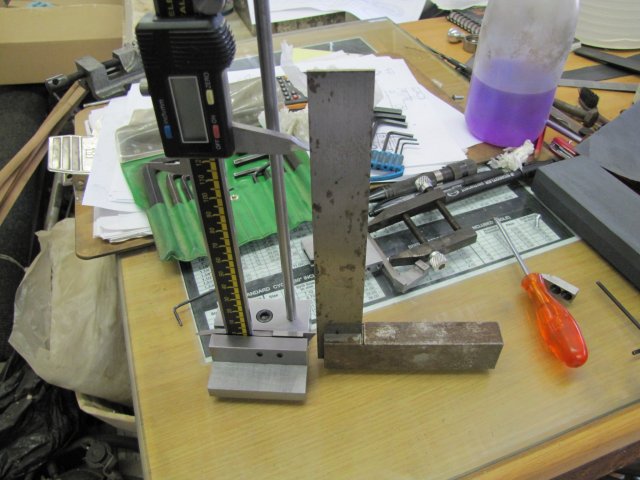
Setting the scribing bit level and flat with respect to the base is more important. I did this by holding the scribing arm with the foot flat on the glass, and raising the caliper's top leg into the machined slot. Then a light tighten of the middle screw, followed by the outer ones, and that's that:
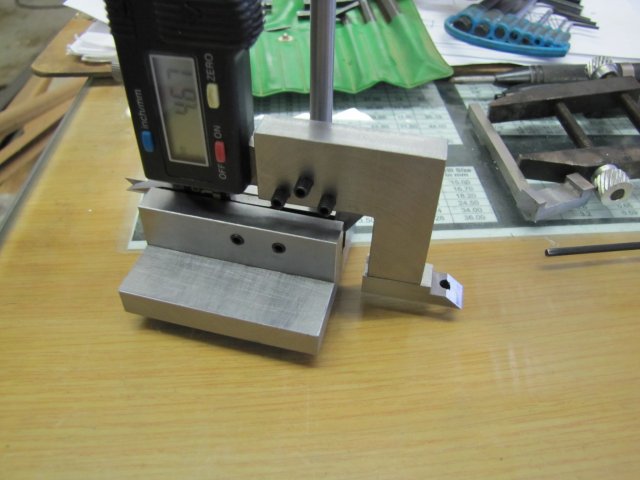
To make double sure, I measured the shank of a broken 1.4mm drill both at the tip of the scriber foot:
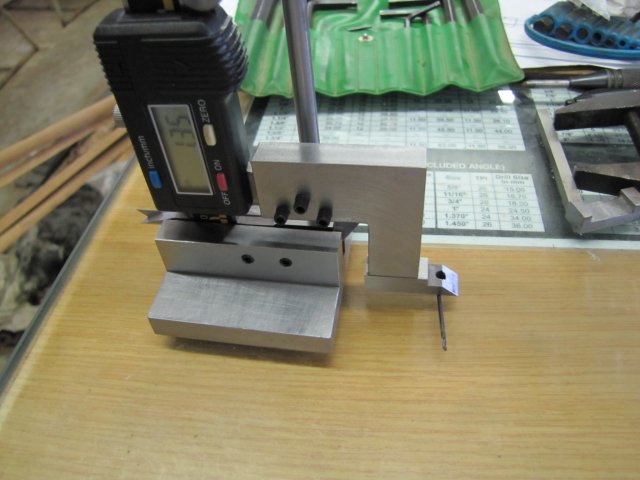
As well as at the back:
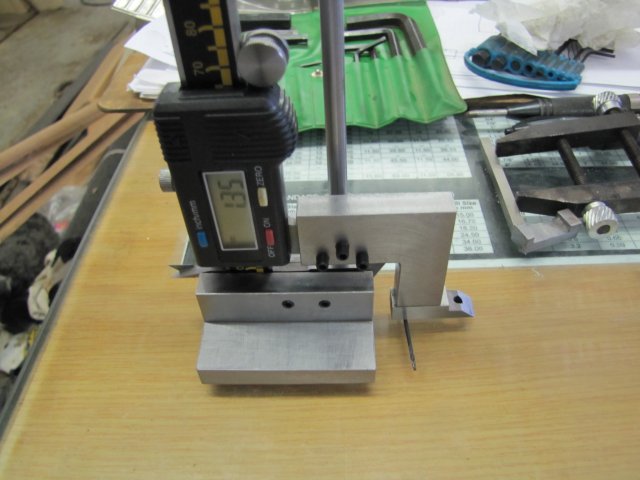
Finally; good to go; I'll get some shorter set screws to replace the ones holding the arm when I get to the nuts and bolts supplier next time:
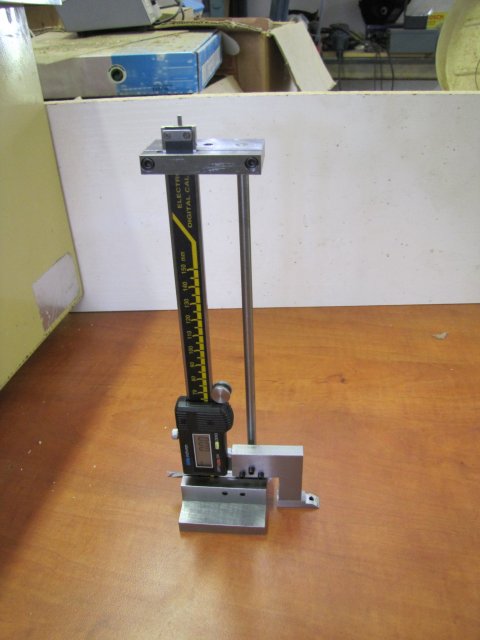
In use for the first time on my next project:
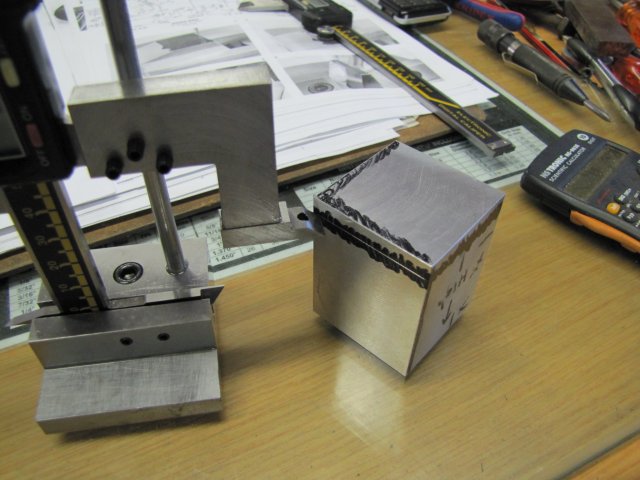
MUCH easier than jiggling the workpiece to scribe some lines on it with a normal caliper ;D - I think I'm going to like this tool!
Regards, Arnold