arnoldb
Well-Known Member
- Joined
- Apr 8, 2009
- Messages
- 1,792
- Reaction score
- 12
Thanks Andrew
- the planning, set-up and finishing takes a lot longer than the machining :big: I'll try and add more detail like that - that is if I remember to check the times; I don't do clock-watching while in the shop ;D
Pete, thanks mate; you keep at it; I'll need all the tips and ideas I can get on the Kerzel... My knowledge of IC engines is limited to getting "electrified" by a Briggs & Stratton lawn mower many years ago; I still hate mowing the lawn :big:
Ken, thanks for the heads-up on the compressor; I'll keep an eye on it. I rigorously switch off all machines in my shop when I'm done for the day; in fact, I modified my mill to have a master power switch for just that reason. I _think_ our power is a bit more dependable than RSA's, though I don't know for how much longer :big:
Yesterday, I f@rted around with a block of aluminium. The markings on the 1" square bar are indicative that this is an extrusion, and I expected it to be a bit gummy while machining:
It was gummy, and left a lot of burrs from fly-cutting:
Even though not ideal for the job, it's what I had available, so I carried on trimming it down to size with a 16mm end mill:
I ended up with the cylinder block and marked it out for the cylinder bore:
Then I spent quite a while mentally running the machining processes through my head. I was spoilt for choice on machining the bore; it could go on the 4-jaw on the lathe, or I could do it on the mill using drills and a reamer or the boring head. Even though the aluminium was gummy, I opted for the easy way of drilling and reaming, with lots of meths for lubricant while reaming:
If the reamer left a bad finish, I could have bored out the cylinder with the boring head in the same position, but fortunately it came out OK with just the reamer.
Before starting on the top of the cylinder, I drilled the exhaust passage on the side; it just makes it easier to drill the exhaust port on the top to the correct depth:
Then I started on the top. Drilled the exhaust port through, and milled the steam passages. The plans call for 1/8" passages 1/16" deep. I don't have a 3mm slot mill, so I used a 2mm one and to compensate for the width, I milled the slots 2mm deep rather than the 1.6mm called for:
With the ports milled deeper, I had to calculate new angles for drilling the ports through to the bore; a quick bit of rough sketching and trigonometry sorted that:
Come on daddy; the maths is boring:
With the new angles marked, I started off the passages with the 2mm center-cutting slot mill:
That was followed with a 2mm drill.
Came out spot-on:
After a quick rub-down on emery, the cylinder block looks fairly presentable:
Two bits of brass plate and a bit of perspex followed:
The thinner brass plate is for the valve face, and the perspex and thicker brass plate are for exchangeable valve chest covers; the perspex for running on air and showing off the valve mechanism, and the brass one should I run the engine on live steam at some future point.
I machined the three down as a sandwich, with the perspex clamped between the brass plates, and the thicker, sturdier brass plate at the top, as end mills are inclined to want to pull up work pieces. With the perspex in the middle, it would be less inclined to want to crack or break:
Shop time ran out yesterday before I could carry on; I'll continue today:
Regards, Arnold
Pete, thanks mate; you keep at it; I'll need all the tips and ideas I can get on the Kerzel... My knowledge of IC engines is limited to getting "electrified" by a Briggs & Stratton lawn mower many years ago; I still hate mowing the lawn :big:
Ken, thanks for the heads-up on the compressor; I'll keep an eye on it. I rigorously switch off all machines in my shop when I'm done for the day; in fact, I modified my mill to have a master power switch for just that reason. I _think_ our power is a bit more dependable than RSA's, though I don't know for how much longer :big:
Yesterday, I f@rted around with a block of aluminium. The markings on the 1" square bar are indicative that this is an extrusion, and I expected it to be a bit gummy while machining:
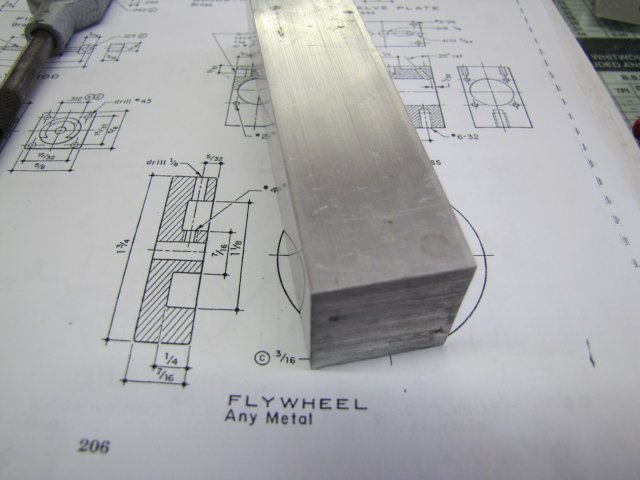
It was gummy, and left a lot of burrs from fly-cutting:
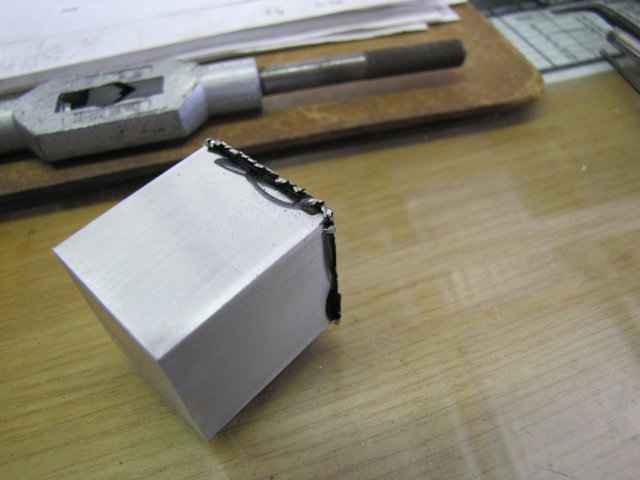
Even though not ideal for the job, it's what I had available, so I carried on trimming it down to size with a 16mm end mill:
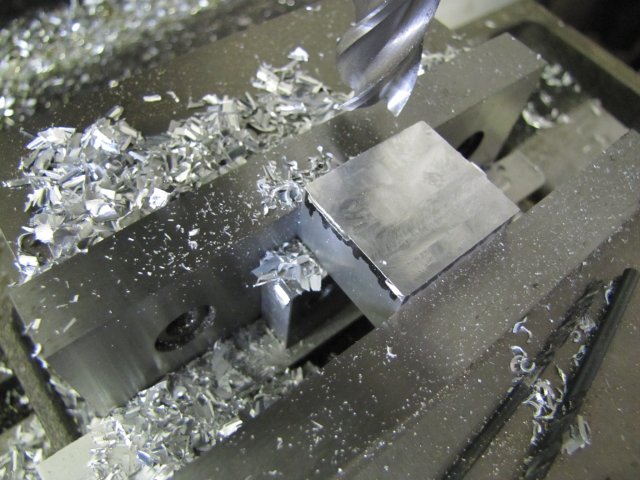
I ended up with the cylinder block and marked it out for the cylinder bore:
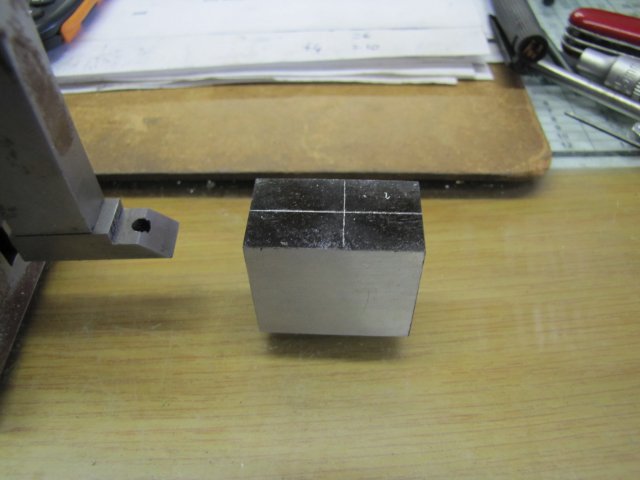
Then I spent quite a while mentally running the machining processes through my head. I was spoilt for choice on machining the bore; it could go on the 4-jaw on the lathe, or I could do it on the mill using drills and a reamer or the boring head. Even though the aluminium was gummy, I opted for the easy way of drilling and reaming, with lots of meths for lubricant while reaming:
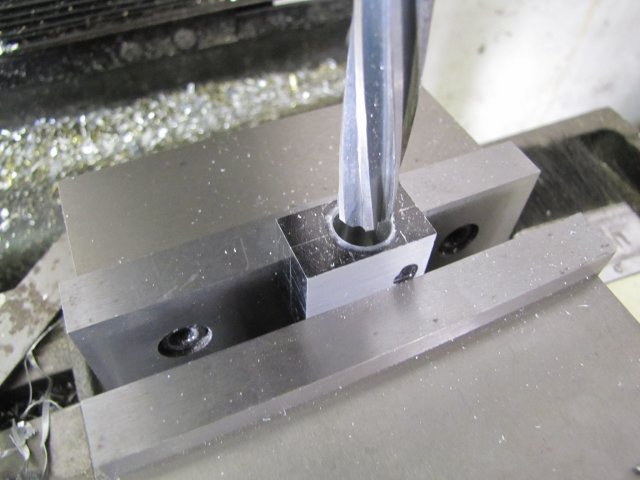
If the reamer left a bad finish, I could have bored out the cylinder with the boring head in the same position, but fortunately it came out OK with just the reamer.
Before starting on the top of the cylinder, I drilled the exhaust passage on the side; it just makes it easier to drill the exhaust port on the top to the correct depth:
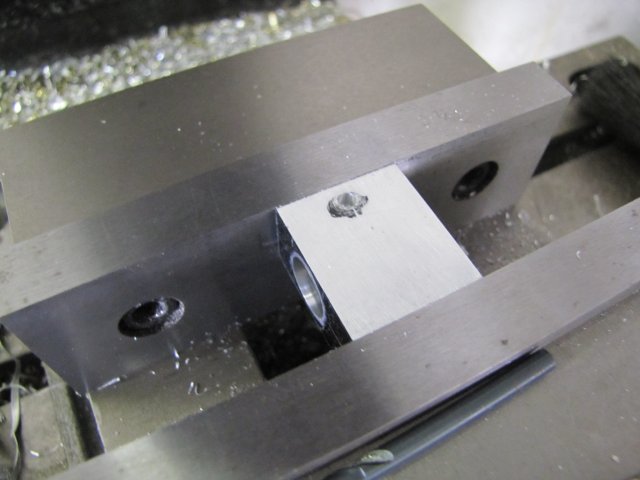
Then I started on the top. Drilled the exhaust port through, and milled the steam passages. The plans call for 1/8" passages 1/16" deep. I don't have a 3mm slot mill, so I used a 2mm one and to compensate for the width, I milled the slots 2mm deep rather than the 1.6mm called for:
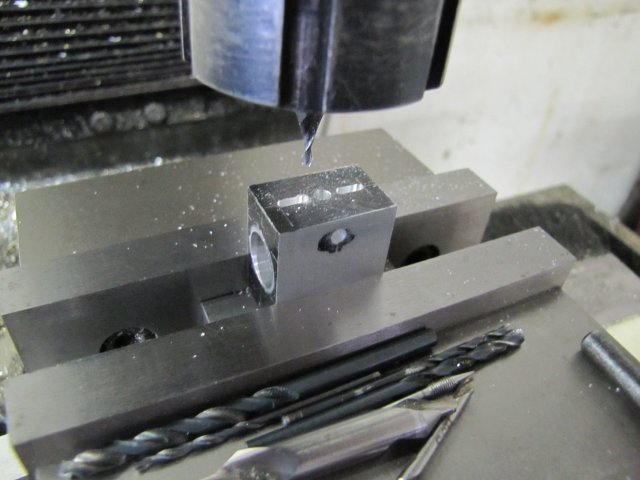
With the ports milled deeper, I had to calculate new angles for drilling the ports through to the bore; a quick bit of rough sketching and trigonometry sorted that:
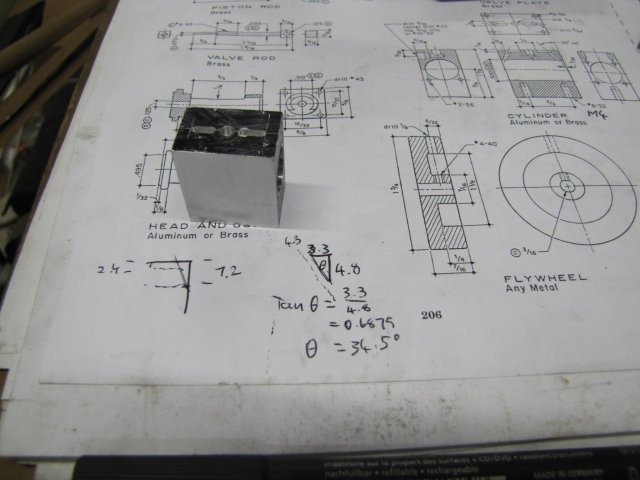
Come on daddy; the maths is boring:
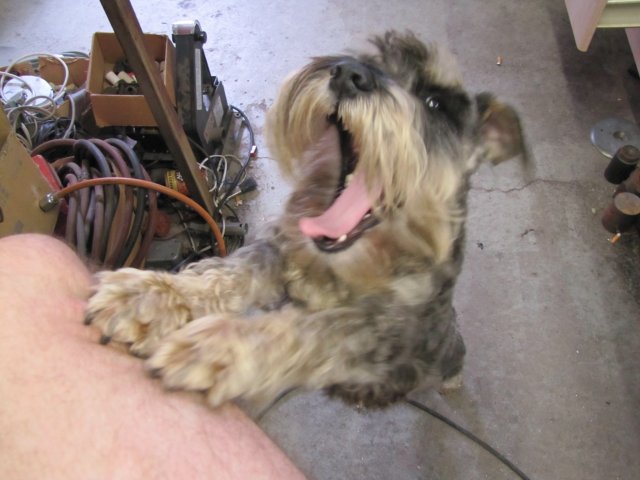
With the new angles marked, I started off the passages with the 2mm center-cutting slot mill:
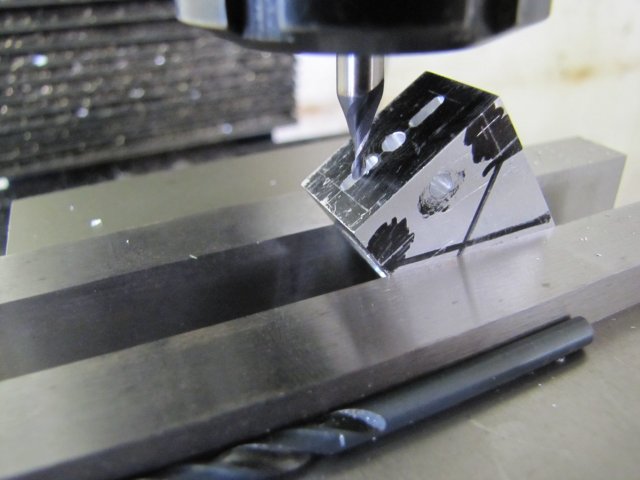
That was followed with a 2mm drill.
Came out spot-on:
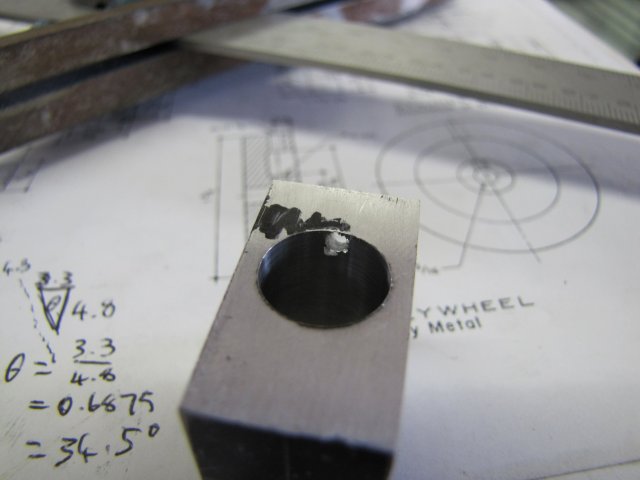
After a quick rub-down on emery, the cylinder block looks fairly presentable:
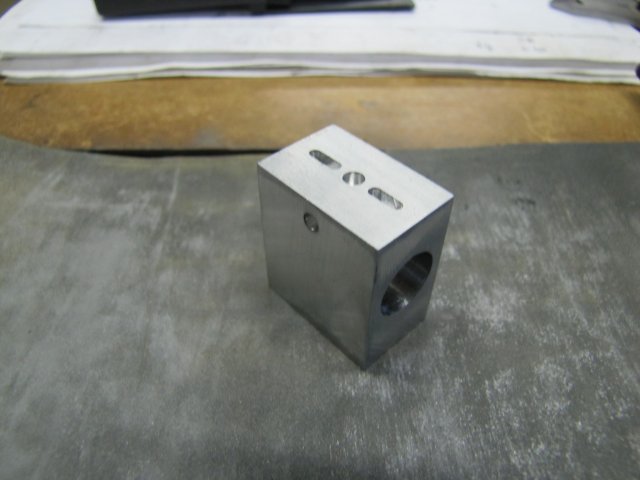
Two bits of brass plate and a bit of perspex followed:
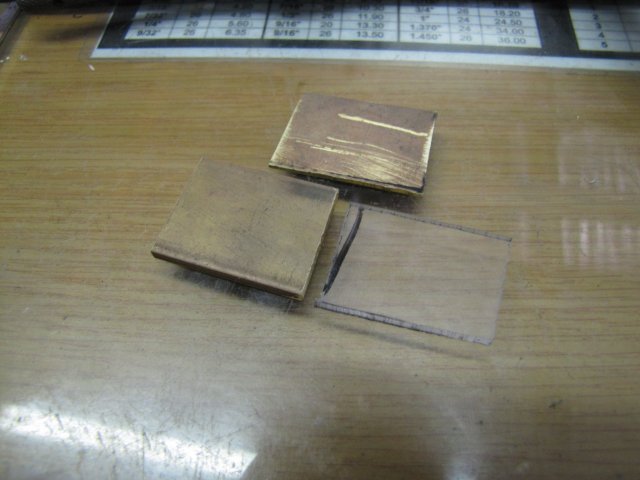
The thinner brass plate is for the valve face, and the perspex and thicker brass plate are for exchangeable valve chest covers; the perspex for running on air and showing off the valve mechanism, and the brass one should I run the engine on live steam at some future point.
I machined the three down as a sandwich, with the perspex clamped between the brass plates, and the thicker, sturdier brass plate at the top, as end mills are inclined to want to pull up work pieces. With the perspex in the middle, it would be less inclined to want to crack or break:
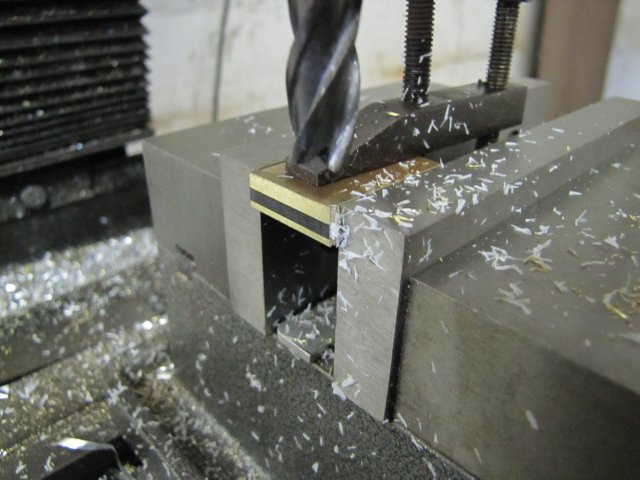
Shop time ran out yesterday before I could carry on; I'll continue today:
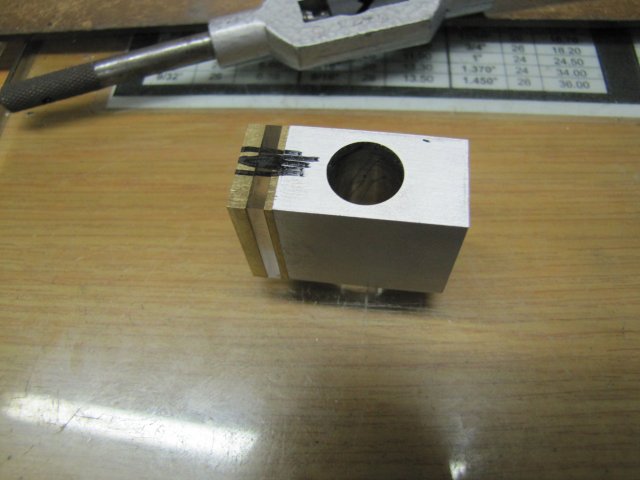
Regards, Arnold