drysdam
Well-Known Member
- Joined
- Feb 10, 2012
- Messages
- 87
- Reaction score
- 7
I've started on a finger treadle engine based very loosely on the NAMES model. By "based very loosely" I mean I'm taking their approximate measurements and improvising from there.
All I have is a lathe and a drill press, no mill, so I'm trying out a bunch of techniques I've read about or thought up but have never tried before. In fact, the engine is a secondary consideration and I'm deliberately doing the hard parts first just to try out these new ideas with less pressure to "finish it finish it finish it!"
In this post, I'm making a flywheel. I'd like it to have "true" spokes rather than drilled web.
I started with 2.5-3" (don't remember which) "black pipe" coupling.
I wasn't sure what this was made of, but some googling indicated maybe mild steel. It actually acted more like cast iron. It machined very nicely...until I got to the cutoff.
Sweet Henry Malloy was this a trial. I had it pop out of the chuck *3 times* before I thought to reverse the work in the chuck to put less leverage on it. Finally got it off, though.
Then I embarked on the task of attempting to index a series of 6 holes. This turned into a boondoggle, but I kept moving forward. No dividing head or even an indexing head. In fact, not even a single gear in my head stock with a multiple of 6 teeth so I could do the poor man's indexing. Instead, I lined up the tip of the tool with each of the teeth in my 3 jaw and scribed a line all the way across the diameter using the cross feed. Then transfer those lines to the outer surface and punch some center holes for drilling spoke holes. (If you don't get what I did, there's a similar picture a couple down from here.)
It seemed at the time this went swimmingly, because I had no way to tell if it was or wasn't right.
The line-scribing went so well above, I thought I'd do it again on the hub so they'd be perfectly aligned.
Now we enter the part where things got so frustrating I apparently forgot to take pictures. The scribed hub you see above was tossed into the scrap bin when the holes weren't even close to alignment. I moved on to another method that involved a wooden form to hold the hub inside the ring while I drilled through the existing ring holes to perfectly align the hub holes.
A block of wood
machined to fit snugly inside the ring
and drilled-with-a-mill-in-the-tailstock to fit the hub
This didn't really work that well either. I have no pictures, but I had to discard hub #2 as well. I tried the same technique on hub #3 and it kind of worked, but there are visible non-alignment issues.
Here it is assembled
and completely finished
I think at least one of the hubs I discarded was probably actually fine. I noticed when inserting the spokes on the third hub that the holes AGAIN didn't line up. WTF?! Then I realized I didn't have the hub centered in the rim. Ooooohhhh, right.
If I'd been a little more careful, my line scribing method (using a level on one of the jaws, say) would probably have been fine. The wooden form was theoretically smart but practically a bit of a hassle since there's nowhere for the hub chips to go.
Another idea would be to spend the $50 on an indexing head. Trouble is, they all take 5c collets and my lathe takes 6k.
All I have is a lathe and a drill press, no mill, so I'm trying out a bunch of techniques I've read about or thought up but have never tried before. In fact, the engine is a secondary consideration and I'm deliberately doing the hard parts first just to try out these new ideas with less pressure to "finish it finish it finish it!"
In this post, I'm making a flywheel. I'd like it to have "true" spokes rather than drilled web.
I started with 2.5-3" (don't remember which) "black pipe" coupling.
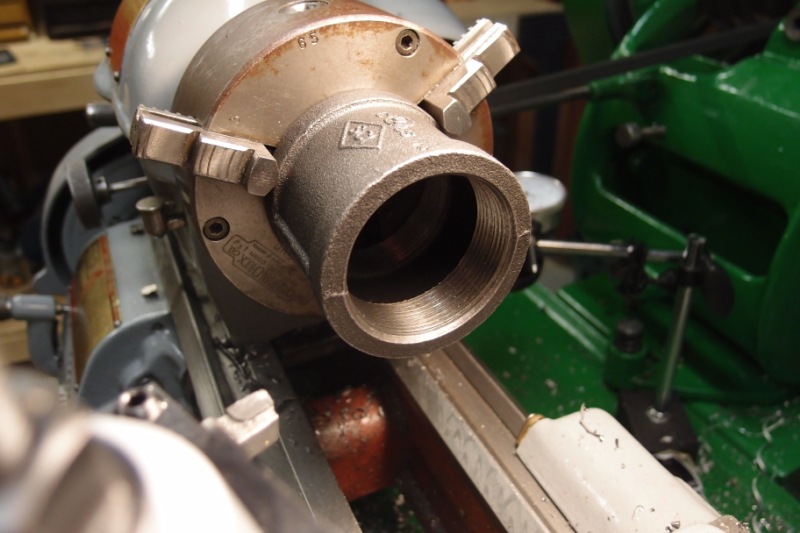
I wasn't sure what this was made of, but some googling indicated maybe mild steel. It actually acted more like cast iron. It machined very nicely...until I got to the cutoff.
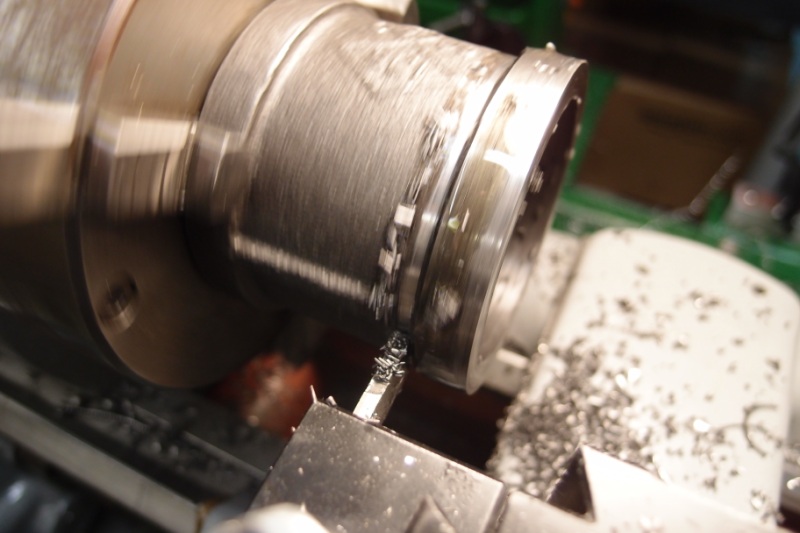
Sweet Henry Malloy was this a trial. I had it pop out of the chuck *3 times* before I thought to reverse the work in the chuck to put less leverage on it. Finally got it off, though.
Then I embarked on the task of attempting to index a series of 6 holes. This turned into a boondoggle, but I kept moving forward. No dividing head or even an indexing head. In fact, not even a single gear in my head stock with a multiple of 6 teeth so I could do the poor man's indexing. Instead, I lined up the tip of the tool with each of the teeth in my 3 jaw and scribed a line all the way across the diameter using the cross feed. Then transfer those lines to the outer surface and punch some center holes for drilling spoke holes. (If you don't get what I did, there's a similar picture a couple down from here.)
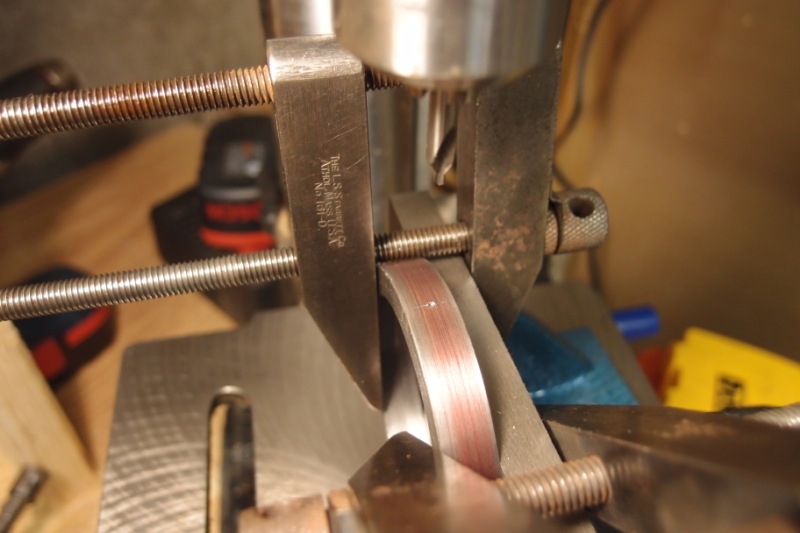
It seemed at the time this went swimmingly, because I had no way to tell if it was or wasn't right.
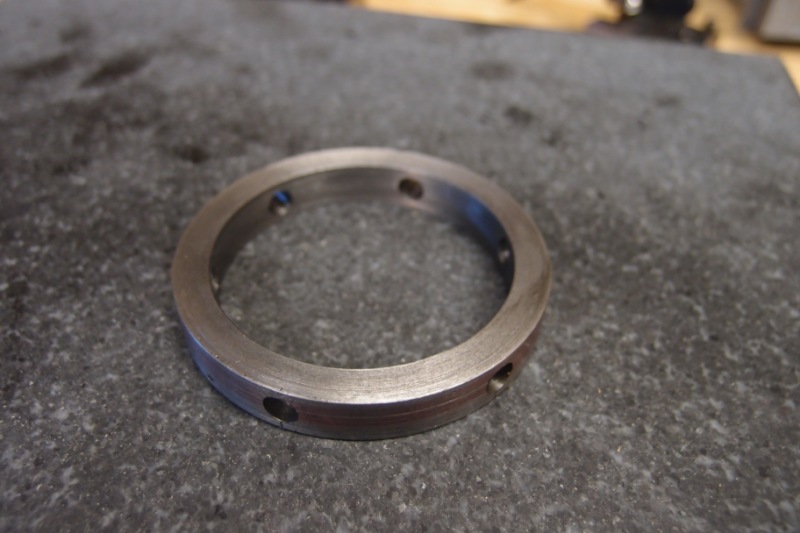
The line-scribing went so well above, I thought I'd do it again on the hub so they'd be perfectly aligned.
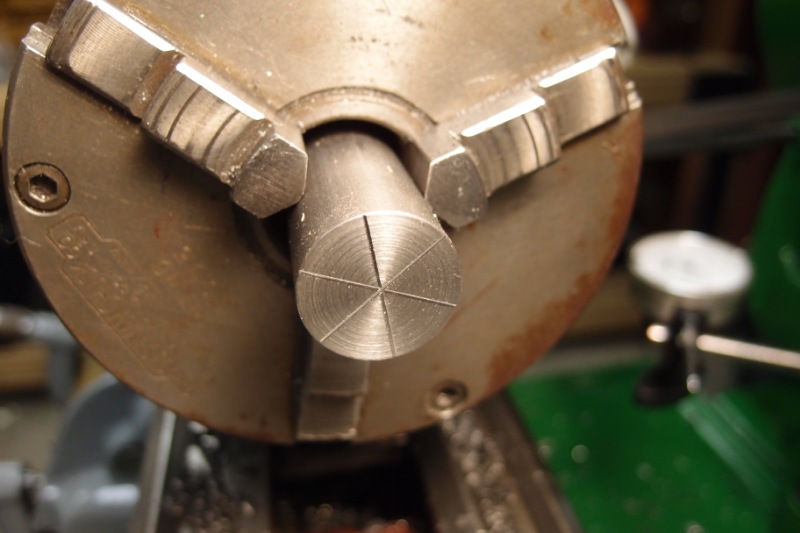
Now we enter the part where things got so frustrating I apparently forgot to take pictures. The scribed hub you see above was tossed into the scrap bin when the holes weren't even close to alignment. I moved on to another method that involved a wooden form to hold the hub inside the ring while I drilled through the existing ring holes to perfectly align the hub holes.
A block of wood
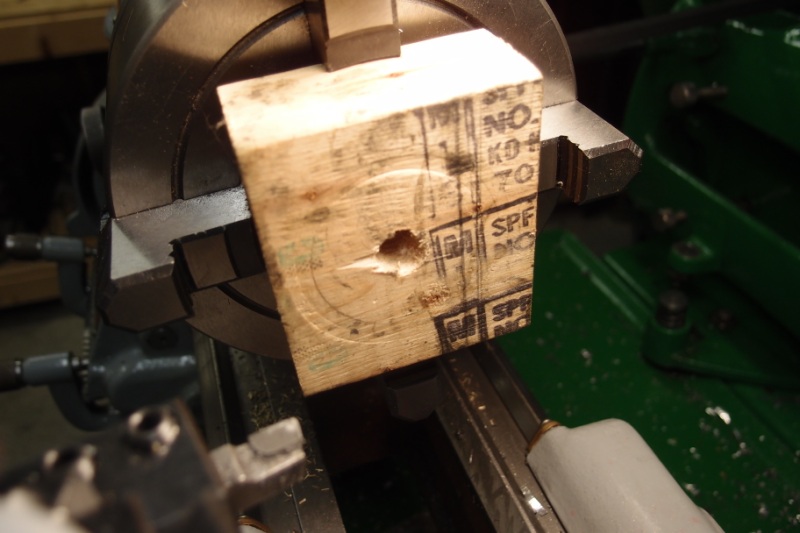
machined to fit snugly inside the ring
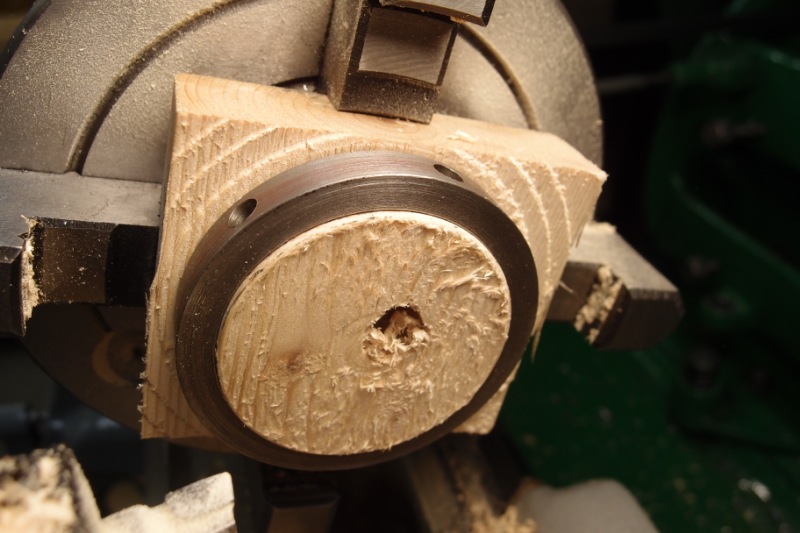
and drilled-with-a-mill-in-the-tailstock to fit the hub
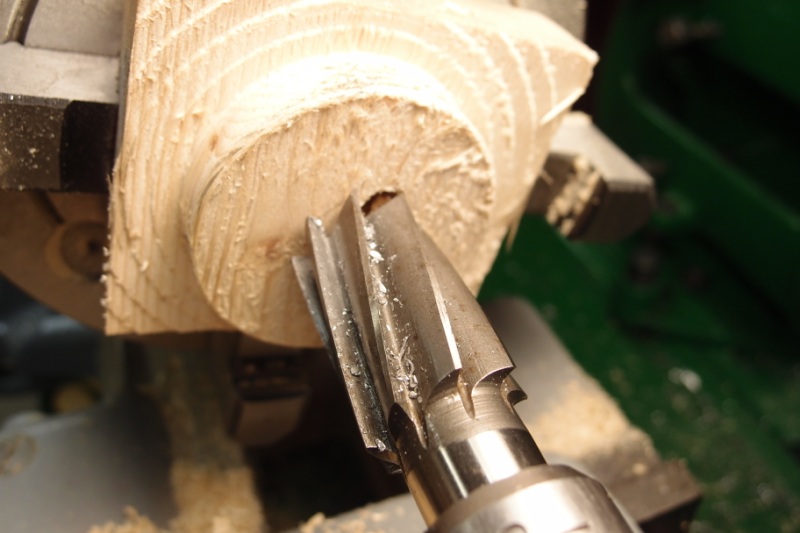
This didn't really work that well either. I have no pictures, but I had to discard hub #2 as well. I tried the same technique on hub #3 and it kind of worked, but there are visible non-alignment issues.
Here it is assembled
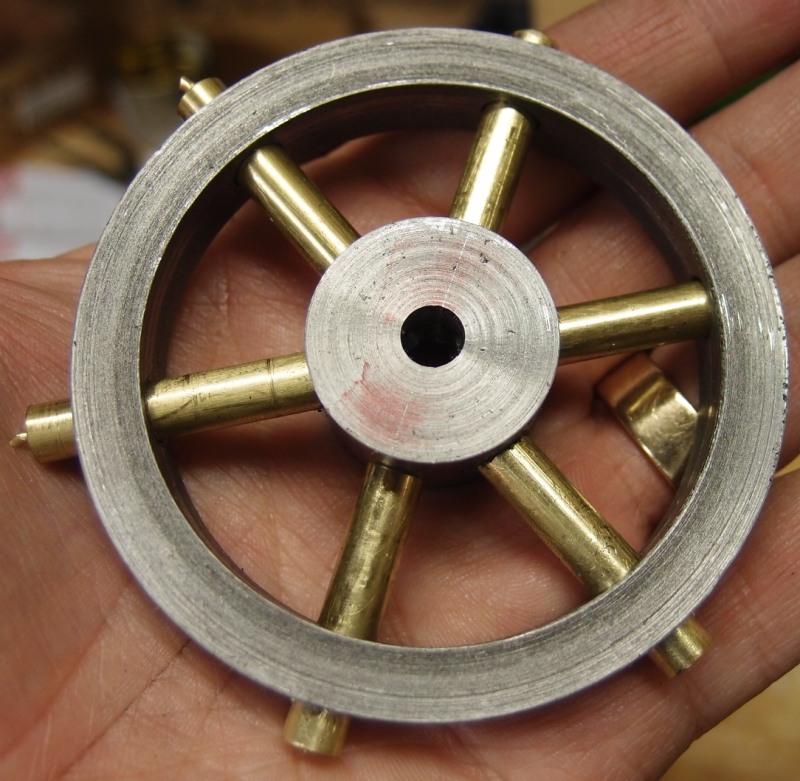
and completely finished
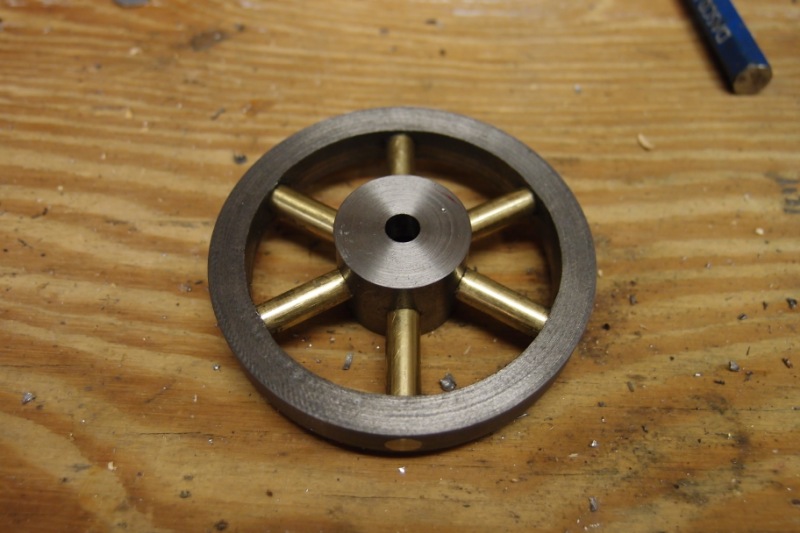
I think at least one of the hubs I discarded was probably actually fine. I noticed when inserting the spokes on the third hub that the holes AGAIN didn't line up. WTF?! Then I realized I didn't have the hub centered in the rim. Ooooohhhh, right.
If I'd been a little more careful, my line scribing method (using a level on one of the jaws, say) would probably have been fine. The wooden form was theoretically smart but practically a bit of a hassle since there's nowhere for the hub chips to go.
Another idea would be to spend the $50 on an indexing head. Trouble is, they all take 5c collets and my lathe takes 6k.