rodw
Well-Known Member
- Joined
- Dec 2, 2012
- Messages
- 1,146
- Reaction score
- 340
You guys must get sick of seeing these sort of posts, but here is another one!
Hare & Forbes wanted AUD $500 for a QCTP (I think it is a Dickson Style). The salesman reckons no one bothers to buy it as it is a major job to fit it to the AL320G that has a tool post like this:
I had seen several ways to fit a QCTP to this style of compound, Brian replaced the post (which I did not want to do to a new lathe), There is a two piece sleeve on Youtube, and I worked out yet another way. But in the end I found it was a lot simpler than I thought it might be by following the hollow bolt approach.
The post has a ground 12mm shoulder at the base, thins out to 10.8mm and ends in a M10 thread at the top. The top of the post is well below the top of the QCTP.
I got the BXA tool post from CTC tools in Hong Kong and it arrived in a week from finalising the order. When I looked at it, the post was 15.5mm in diameter and rattled around a bit in a 16mm hole. Off I went to my mates at the bolt shop and got a 16mm mild steel bolt (4.8 grade) with 100 mm of shank above the thread and a nice big high tensile washer. Once again, the blt had a bit of a layer of silt on it from the floods 2 years ago which washed off, but the price is right. While I was there, I spotted a range of extra long drill bits so I grabbed an 8.5mm one.
I had to go out last night but I managed to lop the thread off in the bandsaw, face it to length and drill the 8.5mm hole right through from one end before we had to depart. So far so good. You could actually make this a blind hole but I played safe so that I would not get into trouble with chip buildup making this part. The bolt is 15.8mm in diameter, so it is a lot nicer fit than the BXA's supplied post.
Anyway, after work tonight, I got stuck into it. First ater getting some good advice from this forum, I widened the hole to 29/64" for about 41 mm (plus the drill tip)
Chamfered the edge with a countersink
And reamed it to 12mm which christened my with my super high quality (not) eBay reamer set.
Thanks guys, this worked perfectly!.
The next step was to tap the hole above the reamed section to M10. I knew I would have to sink the tap in as far as it could go and decided to buy a set of M10 taps so I could work up to a bottoming tap to get as many threads as possible without running too many risks.
Initially, I had a bit of trouble holding the chuck and turn the tap until I worked out to stick the toolpost back on and hold the chuck with a lathe tool.
And I kept threading until I ran out room to hold the tap.
That's it guys, Jobs done!
You can see the finish of the bolt is not the best after its dunking in flood waters but no one will know.
This shot shows the detail inside, the 12mm reamed section followed by the M10 threaded section.
I found this a really easy project and it was nice for nothing to go wrong
I found I can finger tighten it right up and finish it off with a spanner so I was happy with my accuracy.
The compound has a nice spring loaded pin that acts as a detent for the original tool post which has four holes at every 90 degrees and I was thinking I would be able to mill these into the base of the BXA. However, this pin caught on the slots for the wedges so I removed it and just squared the post with a set square.
The AL320G is sold as a lathe suited for 12mm (1/2") tooling but has a massive toolpost hat can easily accept 16mm tooling. However, I found that the raised platform on the compound means you can't drop a 16mm tool low enough to be dead on centre. It is about 1mm high on the factory toolpost and the BXA is similar, aybe about 0.7mm too high. I wondered if this had been done deliberately by Hare and Forbes to make you pay another $1k for a lathe that can take 16mm tooling! Maybe if I was Brian, I would just mill the platform off the compound!
I think the BXA is the right size tool post for a lathe of this size. However, if you wanted to use 16mm tools, I think it would be just a matter of milling 1mm off the base of your tool holders. I think I will stick to 12mm tooling.
I did a couple of quick test cuts after aligning two tools to the tailstock and they were bang on first time.
I can't believe how much easier everything has become on my (much) bigger lathe! (And that's before I have used my new QCTP!)
Hare & Forbes wanted AUD $500 for a QCTP (I think it is a Dickson Style). The salesman reckons no one bothers to buy it as it is a major job to fit it to the AL320G that has a tool post like this:
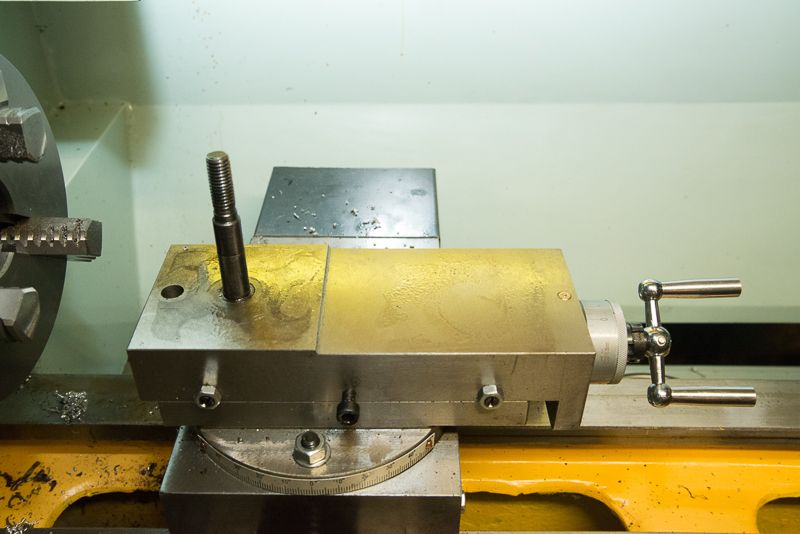
I had seen several ways to fit a QCTP to this style of compound, Brian replaced the post (which I did not want to do to a new lathe), There is a two piece sleeve on Youtube, and I worked out yet another way. But in the end I found it was a lot simpler than I thought it might be by following the hollow bolt approach.
The post has a ground 12mm shoulder at the base, thins out to 10.8mm and ends in a M10 thread at the top. The top of the post is well below the top of the QCTP.
I got the BXA tool post from CTC tools in Hong Kong and it arrived in a week from finalising the order. When I looked at it, the post was 15.5mm in diameter and rattled around a bit in a 16mm hole. Off I went to my mates at the bolt shop and got a 16mm mild steel bolt (4.8 grade) with 100 mm of shank above the thread and a nice big high tensile washer. Once again, the blt had a bit of a layer of silt on it from the floods 2 years ago which washed off, but the price is right. While I was there, I spotted a range of extra long drill bits so I grabbed an 8.5mm one.
I had to go out last night but I managed to lop the thread off in the bandsaw, face it to length and drill the 8.5mm hole right through from one end before we had to depart. So far so good. You could actually make this a blind hole but I played safe so that I would not get into trouble with chip buildup making this part. The bolt is 15.8mm in diameter, so it is a lot nicer fit than the BXA's supplied post.
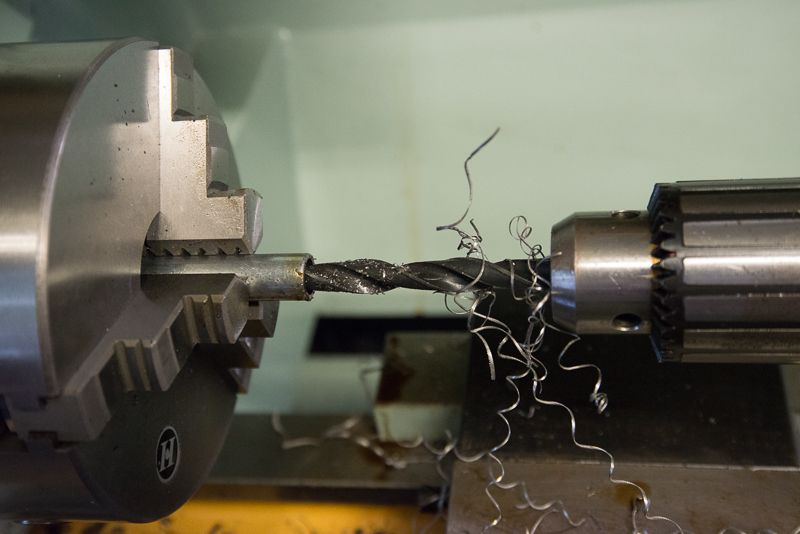
Anyway, after work tonight, I got stuck into it. First ater getting some good advice from this forum, I widened the hole to 29/64" for about 41 mm (plus the drill tip)
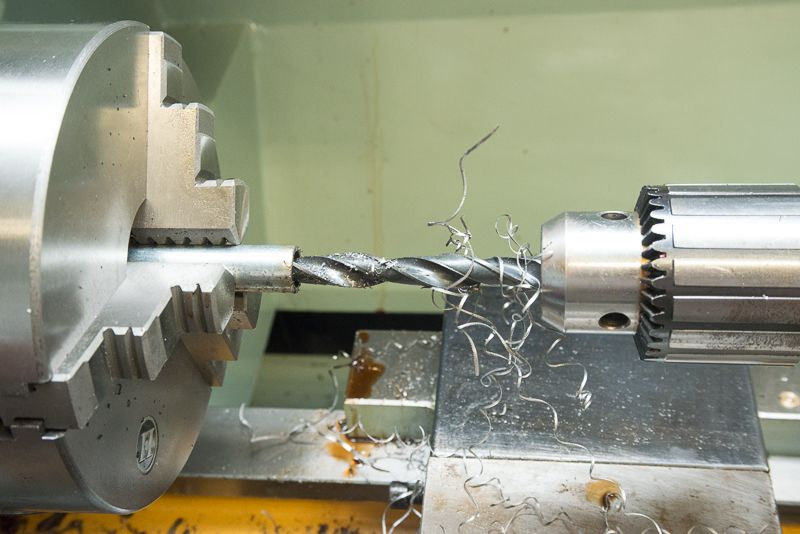
Chamfered the edge with a countersink
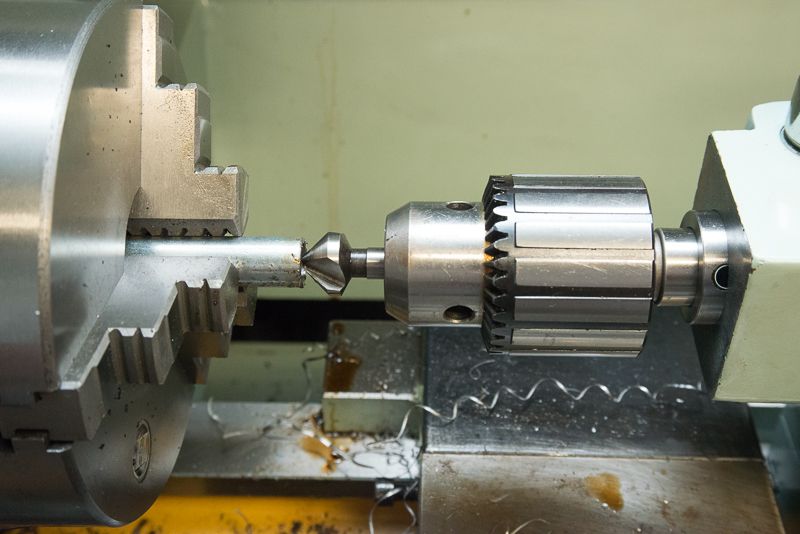
And reamed it to 12mm which christened my with my super high quality (not) eBay reamer set.
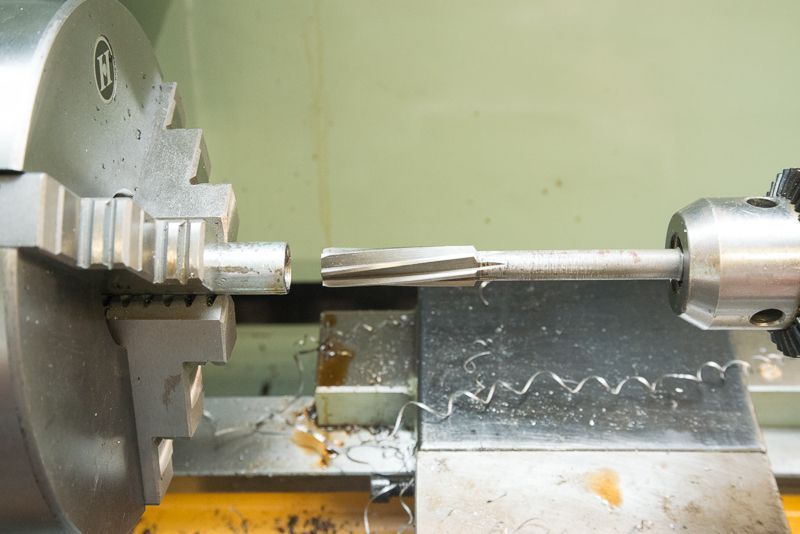
Thanks guys, this worked perfectly!.
The next step was to tap the hole above the reamed section to M10. I knew I would have to sink the tap in as far as it could go and decided to buy a set of M10 taps so I could work up to a bottoming tap to get as many threads as possible without running too many risks.
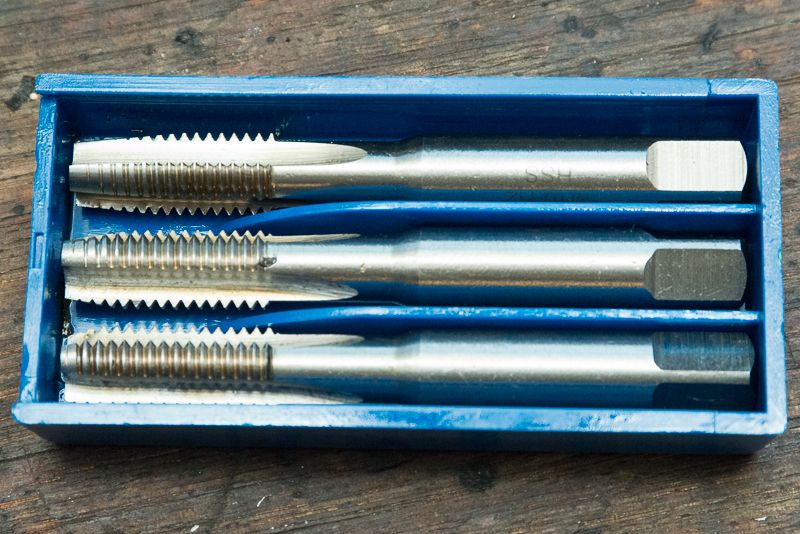
Initially, I had a bit of trouble holding the chuck and turn the tap until I worked out to stick the toolpost back on and hold the chuck with a lathe tool.
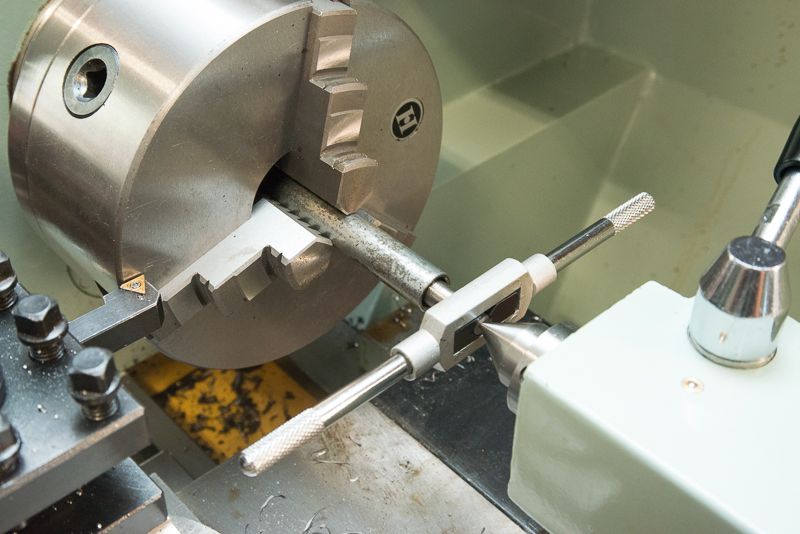
And I kept threading until I ran out room to hold the tap.
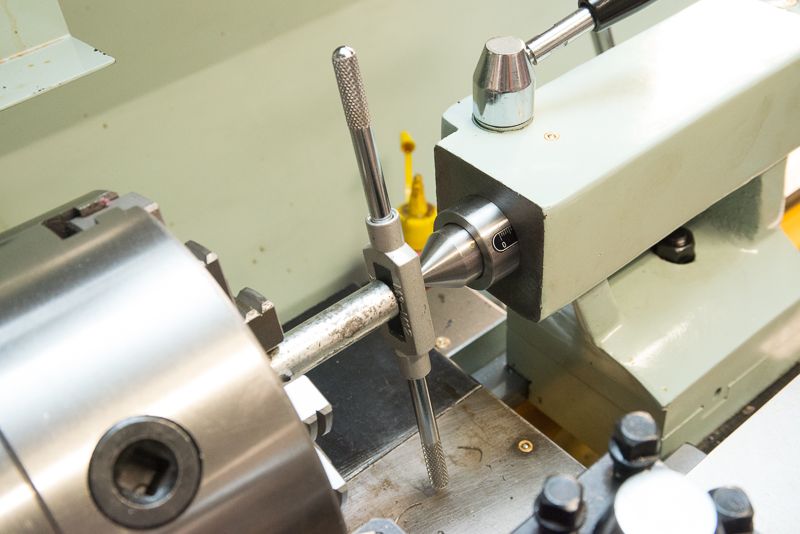
That's it guys, Jobs done!
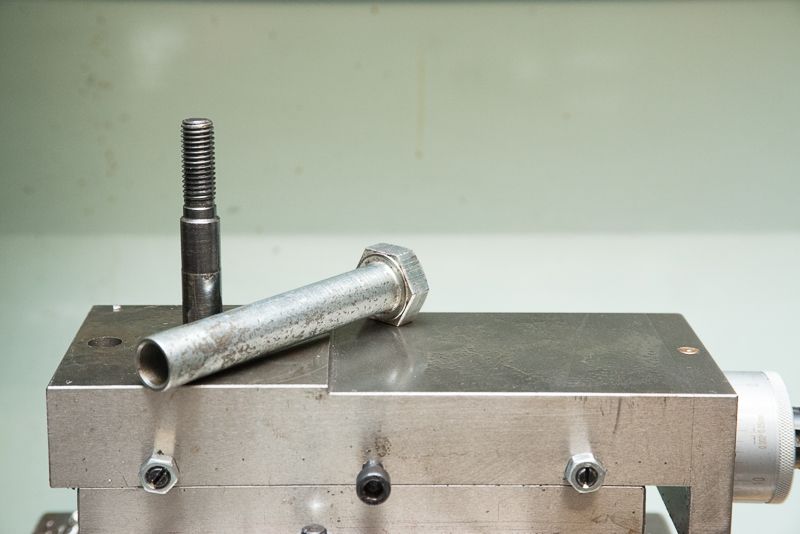
You can see the finish of the bolt is not the best after its dunking in flood waters but no one will know.
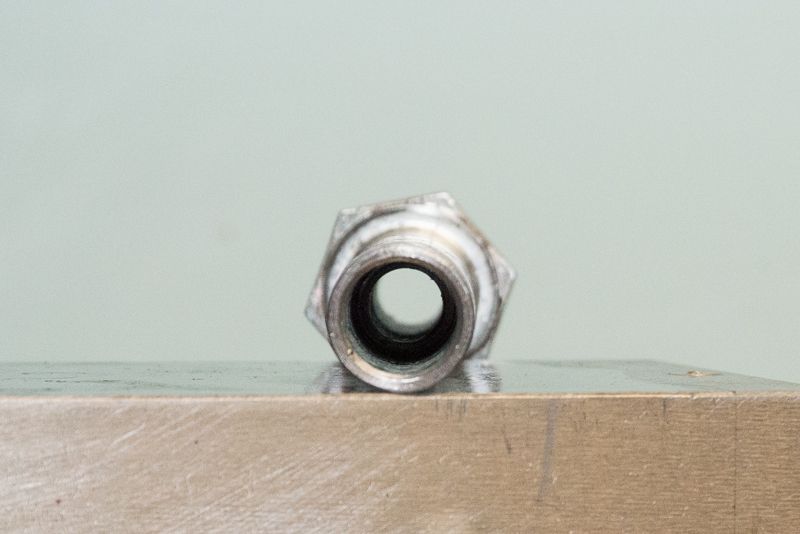
This shot shows the detail inside, the 12mm reamed section followed by the M10 threaded section.
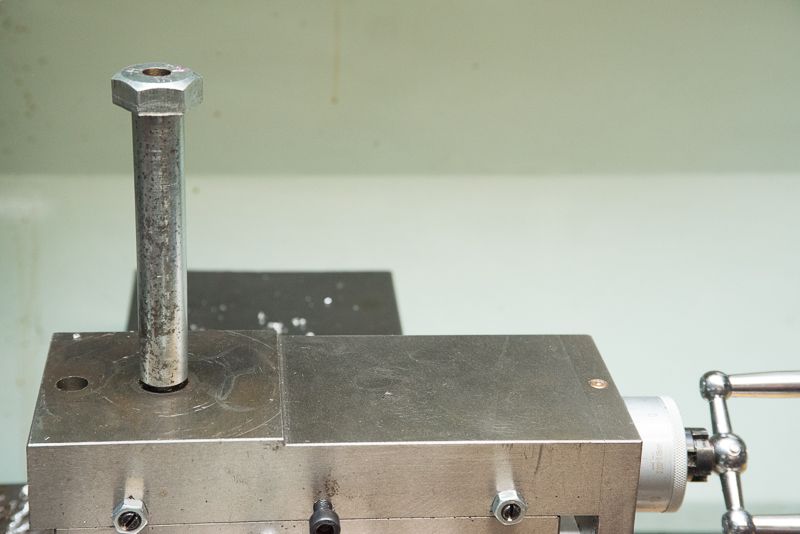
I found this a really easy project and it was nice for nothing to go wrong
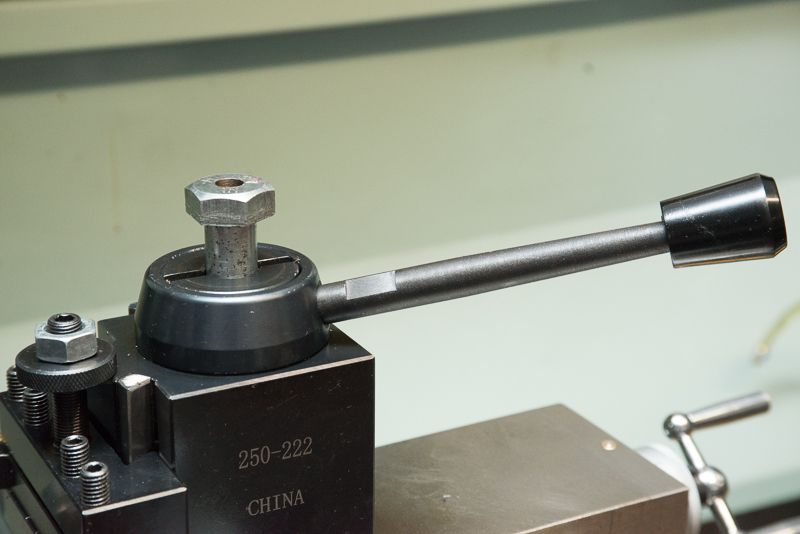
I found I can finger tighten it right up and finish it off with a spanner so I was happy with my accuracy.
The compound has a nice spring loaded pin that acts as a detent for the original tool post which has four holes at every 90 degrees and I was thinking I would be able to mill these into the base of the BXA. However, this pin caught on the slots for the wedges so I removed it and just squared the post with a set square.
The AL320G is sold as a lathe suited for 12mm (1/2") tooling but has a massive toolpost hat can easily accept 16mm tooling. However, I found that the raised platform on the compound means you can't drop a 16mm tool low enough to be dead on centre. It is about 1mm high on the factory toolpost and the BXA is similar, aybe about 0.7mm too high. I wondered if this had been done deliberately by Hare and Forbes to make you pay another $1k for a lathe that can take 16mm tooling! Maybe if I was Brian, I would just mill the platform off the compound!
I think the BXA is the right size tool post for a lathe of this size. However, if you wanted to use 16mm tools, I think it would be just a matter of milling 1mm off the base of your tool holders. I think I will stick to 12mm tooling.
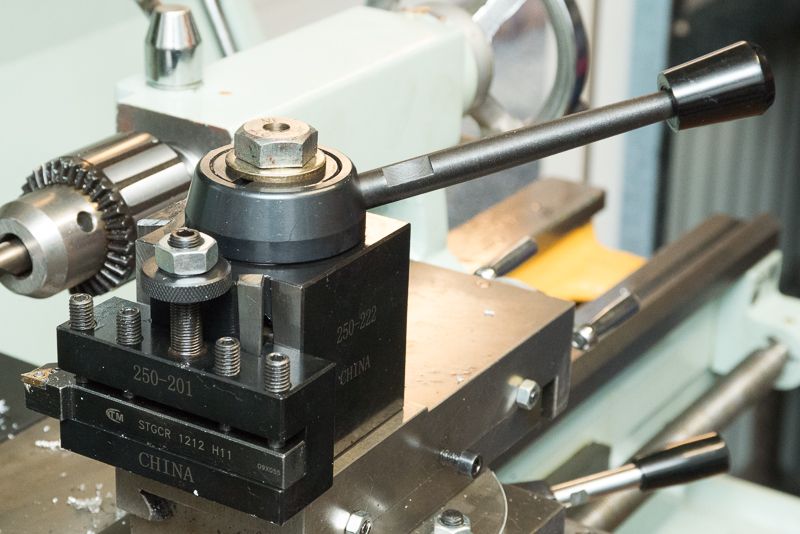
I did a couple of quick test cuts after aligning two tools to the tailstock and they were bang on first time.
I can't believe how much easier everything has become on my (much) bigger lathe! (And that's before I have used my new QCTP!)