In response to a request for plans by DaveRC as well as a forthcoming need of my own - plus I can't find anything "off the shelf" that I like - I designed and built a wire / tube - bending / forming fixture.
Here are some sample parts bent on the fixture.
You can use the centre pins as a pair to hold the rod whilst bending with the outer pin as a one size fits all general purpose approach - like this it can bend wire up to 5mm diameter.
You can also perform double parallel bending which is handy for manufacuring offsets.
By slipping rollers over the pins and adding the guide unit you can form the wire around your inner form roller to generate specific bend radii.
Set up like this to do one bend at a time it will bend up to 1/4" mild steel rod (I have bent 7mm diameter).
By adding the stop you can set for a "production run" to get a whole bunch of identically bent parts.
By making forming rollers to slip over the pins you can bend tubing with minimal flattening or kinking.
Whilst I haven't tried it I would guess you could also perform some limited bending of flat or profiled stock.
The main pins are made from 6mm diameter silver steel (unhardened) and the rollers and for bending and forming are also machined from silver steel and hardened.
For radii smaller than 3mm you would have to make a stepped pin.
Sure over time you will have to make a bunch of rollers & pins as required but they should last forever and you will ultimately accumulate a useful set.
Other than for forming tube the inner and outer roller do not need to "nest" exactly with the wire being bent.
I did not trust myself to accurately hand grind a 1/16" radius form tool and had zero faith in my mini-lathe's ability to plunge form turn it in any case so I milled the rads on the RT (relying on the cutter diameter to give an exact radius).
Here the forming rollers being used to form 1/8" x 3/32 steel tube (for NOS injection lines) as well as 1/8" x 3/32" brass tube etc.
Here are the various parts that make up the fixture - which is intended to be mounted in a vice.
Note the smaller knock out holes drilled right through in case of a pin getting stuck.
I will post the 2D ACAD drawings in the downloads section for anyone who's interested - you can obviously play with it to your heart's content and adjust to imperial dimensions where better suited to your purpose.
Since making it I have added a few more holes to the torque ring to give more opportunity to use existing rollers on other sizes and I have increaced the length of the split clamp which holds the stop to make it more user friendly (it fouled the guide arm in some locations).
If anyone has any better ideas or improvements - lets have them.
Ken
Here are some sample parts bent on the fixture.
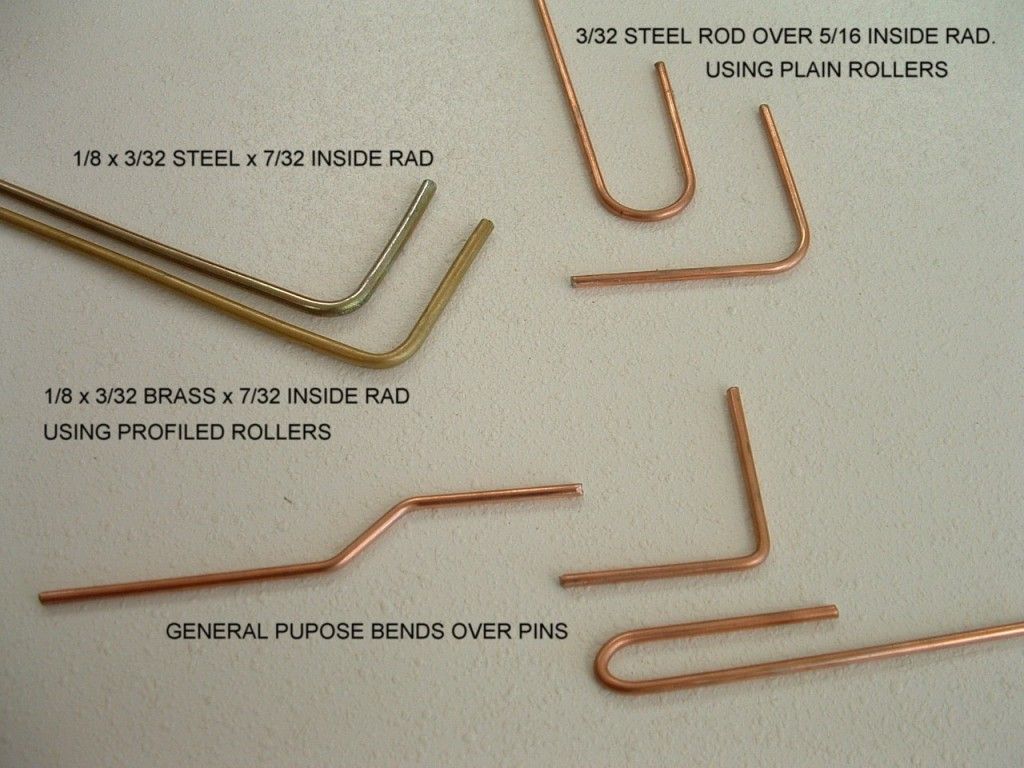
You can use the centre pins as a pair to hold the rod whilst bending with the outer pin as a one size fits all general purpose approach - like this it can bend wire up to 5mm diameter.
You can also perform double parallel bending which is handy for manufacuring offsets.
By slipping rollers over the pins and adding the guide unit you can form the wire around your inner form roller to generate specific bend radii.
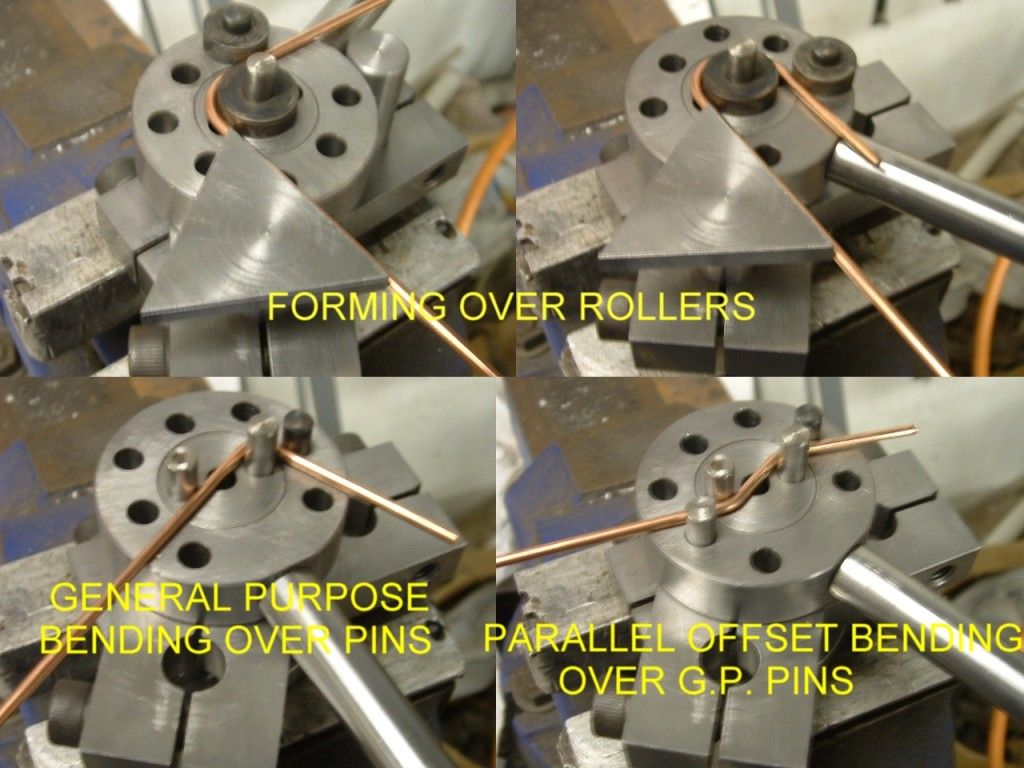
Set up like this to do one bend at a time it will bend up to 1/4" mild steel rod (I have bent 7mm diameter).
By adding the stop you can set for a "production run" to get a whole bunch of identically bent parts.
By making forming rollers to slip over the pins you can bend tubing with minimal flattening or kinking.
Whilst I haven't tried it I would guess you could also perform some limited bending of flat or profiled stock.
The main pins are made from 6mm diameter silver steel (unhardened) and the rollers and for bending and forming are also machined from silver steel and hardened.
For radii smaller than 3mm you would have to make a stepped pin.
Sure over time you will have to make a bunch of rollers & pins as required but they should last forever and you will ultimately accumulate a useful set.
Other than for forming tube the inner and outer roller do not need to "nest" exactly with the wire being bent.
I did not trust myself to accurately hand grind a 1/16" radius form tool and had zero faith in my mini-lathe's ability to plunge form turn it in any case so I milled the rads on the RT (relying on the cutter diameter to give an exact radius).
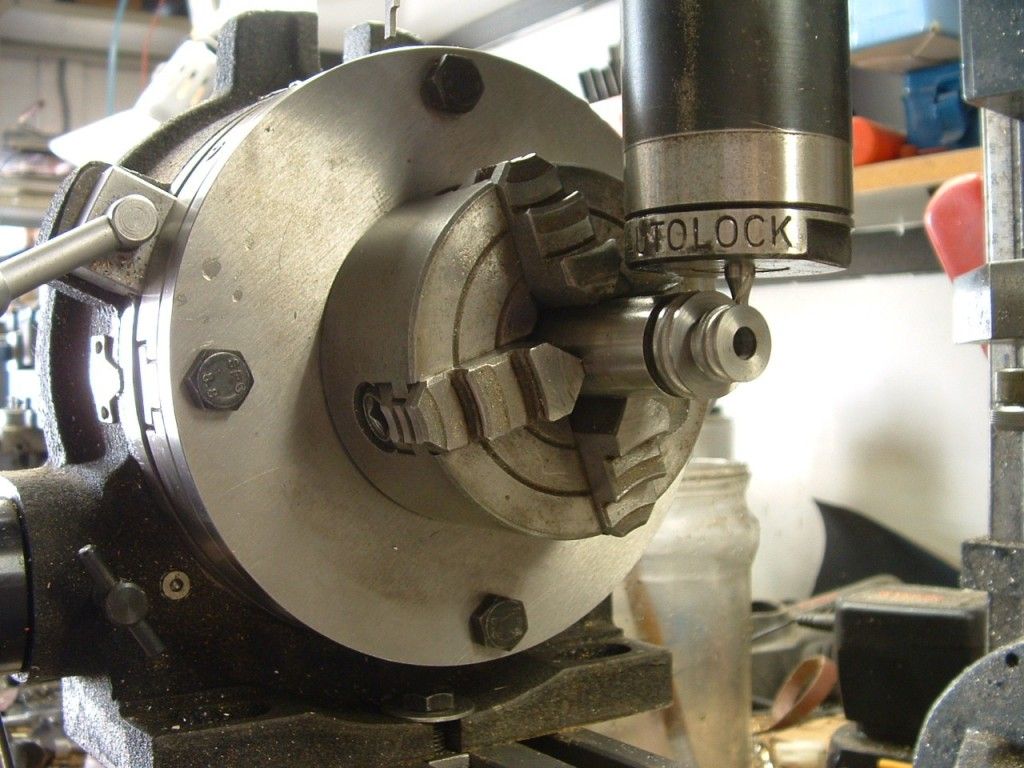
Here the forming rollers being used to form 1/8" x 3/32 steel tube (for NOS injection lines) as well as 1/8" x 3/32" brass tube etc.
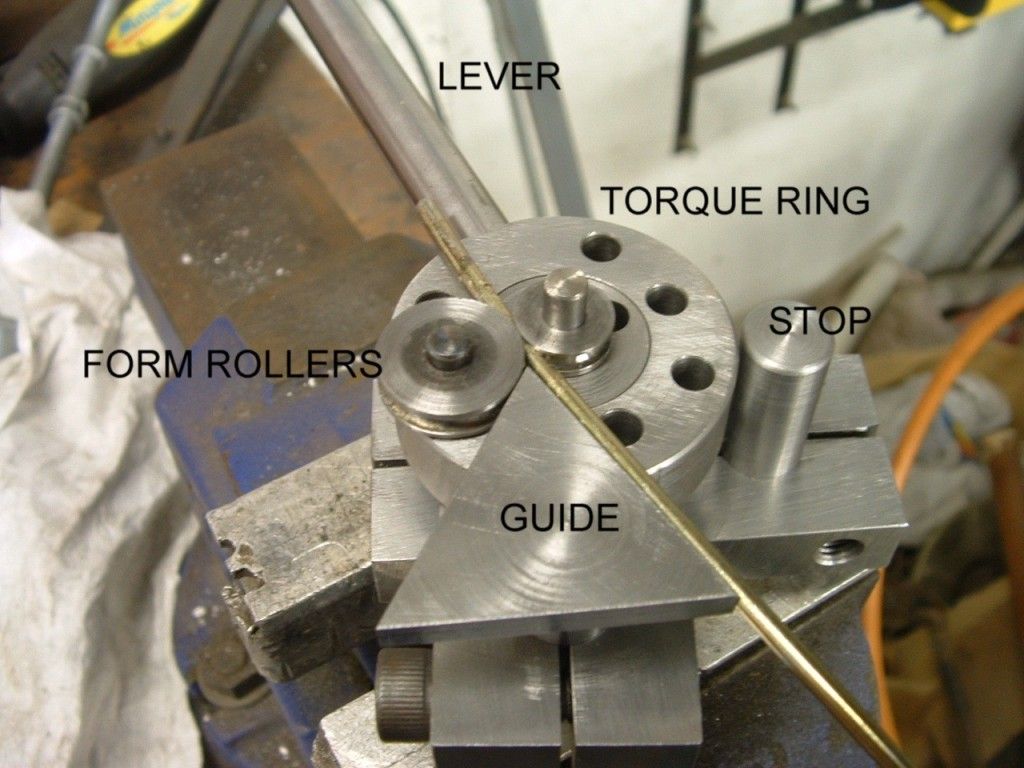
Here are the various parts that make up the fixture - which is intended to be mounted in a vice.
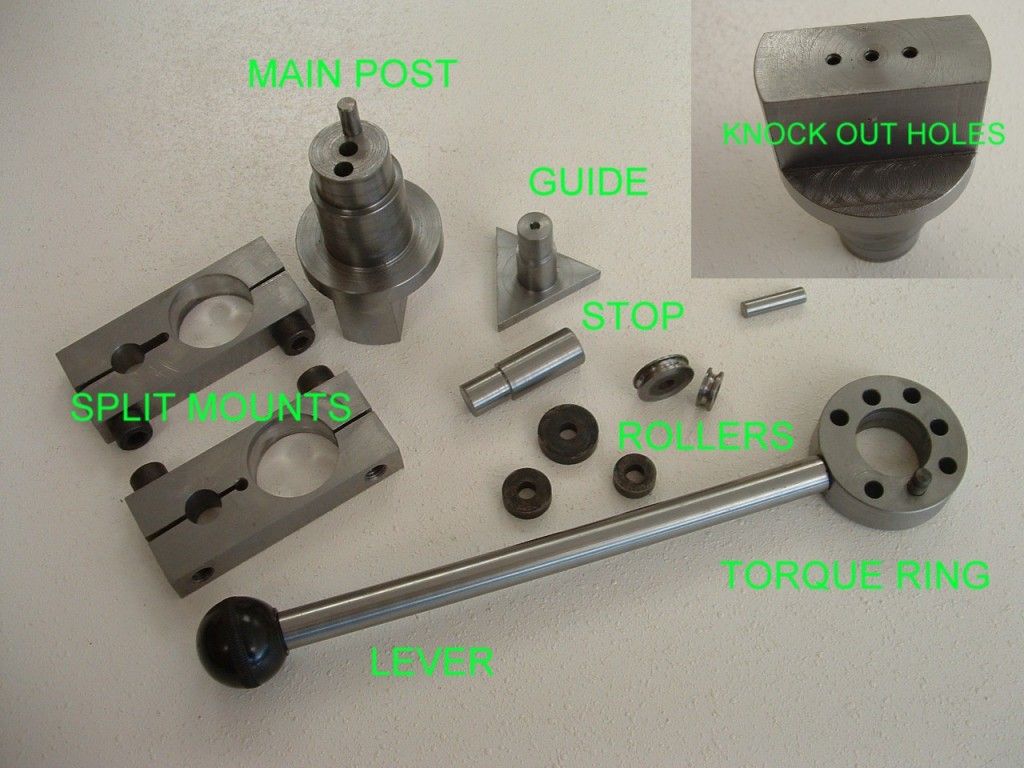
Note the smaller knock out holes drilled right through in case of a pin getting stuck.
I will post the 2D ACAD drawings in the downloads section for anyone who's interested - you can obviously play with it to your heart's content and adjust to imperial dimensions where better suited to your purpose.
Since making it I have added a few more holes to the torque ring to give more opportunity to use existing rollers on other sizes and I have increaced the length of the split clamp which holds the stop to make it more user friendly (it fouled the guide arm in some locations).
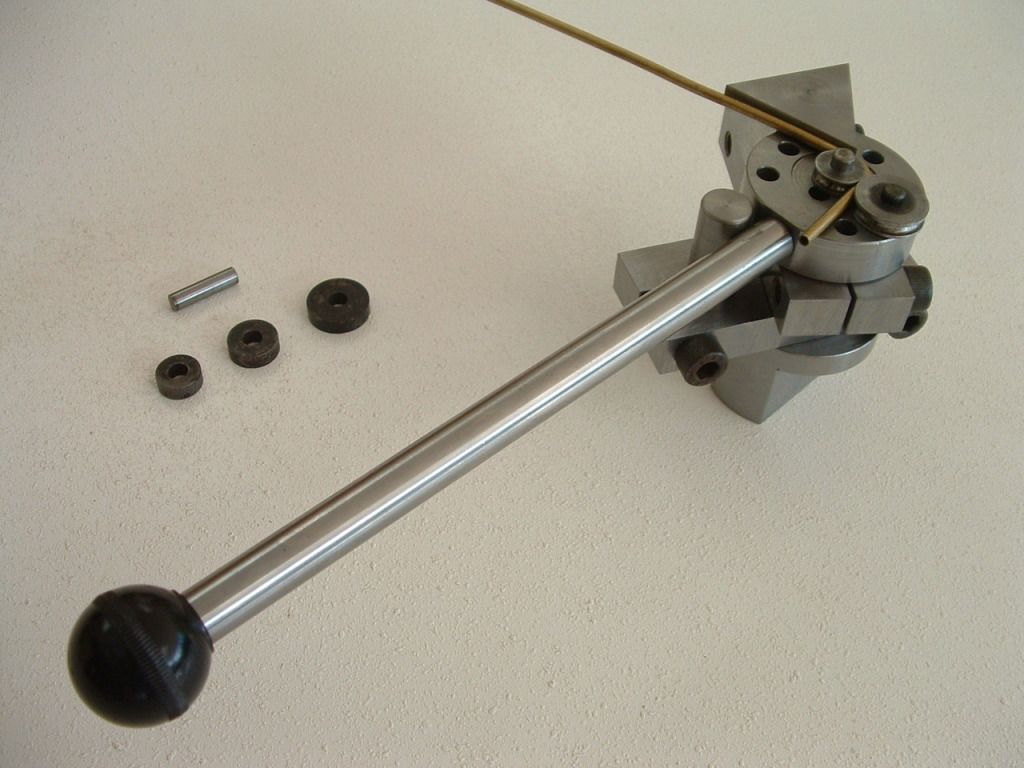
If anyone has any better ideas or improvements - lets have them.
Ken