Cedge
Well-Known Member
- Joined
- Jul 12, 2007
- Messages
- 1,727
- Reaction score
- 28
For the past few weeks, a "super heavy" load has been making its way from Hardeeville SC, enroute to Boiling Springs NC. It is a large electric generator destined for a clean coal power plant. The generator weighs in at 1.98 million pounds and isn't something you just jump on an interstate freeway with and truck it on down the road.
In order to support such a load without destroying every inch of road you travel, the weight has to be widely distributed. You also have to travel back roads so that day to day commerce isn't completely disrupted along your route. After all..... your top speed on level ground is less than 20 mph and this drops to as little as 1.5 mph on grades and slopes. Rush hour traffic traffic on an interstate would soon be solidly backed up to the state lines in both directions.
I finally had time to catch up with the load on Friday as it moved along a stretch of country road near the NC state line, but was unable to get near enough to shoot photos. Luckily, one of the crew let me know it would be on the move again early Sunday morning when they would be making a detour around an interstate overpass that was not rated for anything near the weight of the load.
Here is the rig I'm talking about.... The trailer, as rigged, is 300 ft long all by itself. There are 36 rows of axles, each with 8 tires. (288 total) These can be augmented with up to another additional 80 wheels on hinged outriggers, for a total of 368 potential flats. Add in 5 each 10 wheel heavy duty road tractors (2 pulling and 3 pushing) and that flat tire potential rises to 418. The outriggers are not deployed in these photos, so the total tire count, for the moment, is 338.
The load then had to negotiate the 90° turn seen in the photo. This had to be done while keeping all 338 tires solidly on paved surfaces. Note that each axle is steerable so it's only a little less exacting than a tap dancing centipede, but an on board computer system has things well in hand. It doesn't fully control the action since there is a "driver" in the chain of command. Here the action as begun and the lead tractors are making their initial turn.
As things advance, dozens of power crews are on hand to clear overhead wires and there are hundreds of other support crews and dozens of support trucks waiting to fall in line behind the convoy.
Notice that each large truck has a box firmly anchored over the rear wheels. Those are 18,500 pound weights which give the truck the needed traction this load requires to get it moving.
Looking closely at the rear section of the trailer, you'll see it is sitting at about an angle of 45° to the rest of the load. Once the main load was aligned as they wanted, the rear section crabbed and adjusted until it was in line and ready to travel. It was a strange action to watch but it worked perfectly.
Here is a shot of one of the two "Drivers" The computer might tell the all wheels how much to turn, but this guy tells the computer when to do it and how much at a time. He's apparently pretty durable since the dawn temperature was a chilling 25° as he began his ride.
Here you can see how the the immense weight was distributed across the trailer sections as well as the hinge points for the support bridge. Both ends are supported in this fashion, making the whole rig a lot more flexible than it might first appear. Those outriggers I mentioned are clearly visible along the outer edge of the trailer.
The main bridge beams suspend the huge generator about 18 inches above the roadbed. When the job is completed, the round pins near the bottom edge can be removed and the beams can be stacked for their return trip home. Even up close they almost look too small to be holding that much weight up in the air. Standing near this beam is a little spooky. All kinds of pops and groans can be heard, even when it isn't on the move.
It was a fun way to begin a new day. Everyone I met was friendly, including those doing some downright cold and dirty work. Even the local cops seemed to be in fine spirits as they dealt with more traffic than that small community has probably ever seen. I just wanted to share some of the sights with you guys.
Steve
In order to support such a load without destroying every inch of road you travel, the weight has to be widely distributed. You also have to travel back roads so that day to day commerce isn't completely disrupted along your route. After all..... your top speed on level ground is less than 20 mph and this drops to as little as 1.5 mph on grades and slopes. Rush hour traffic traffic on an interstate would soon be solidly backed up to the state lines in both directions.
I finally had time to catch up with the load on Friday as it moved along a stretch of country road near the NC state line, but was unable to get near enough to shoot photos. Luckily, one of the crew let me know it would be on the move again early Sunday morning when they would be making a detour around an interstate overpass that was not rated for anything near the weight of the load.
Here is the rig I'm talking about.... The trailer, as rigged, is 300 ft long all by itself. There are 36 rows of axles, each with 8 tires. (288 total) These can be augmented with up to another additional 80 wheels on hinged outriggers, for a total of 368 potential flats. Add in 5 each 10 wheel heavy duty road tractors (2 pulling and 3 pushing) and that flat tire potential rises to 418. The outriggers are not deployed in these photos, so the total tire count, for the moment, is 338.
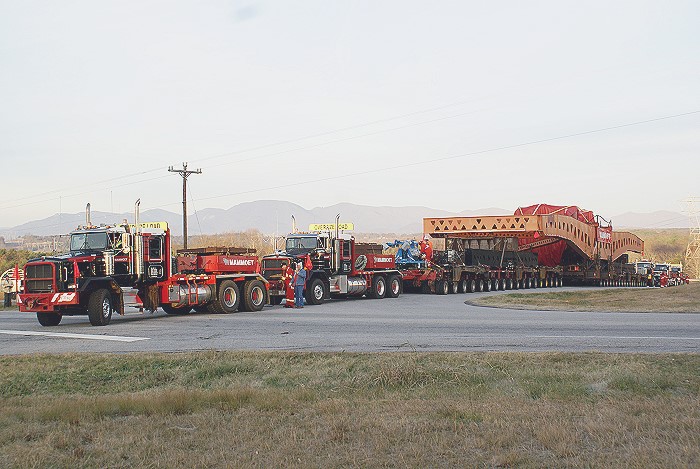
The load then had to negotiate the 90° turn seen in the photo. This had to be done while keeping all 338 tires solidly on paved surfaces. Note that each axle is steerable so it's only a little less exacting than a tap dancing centipede, but an on board computer system has things well in hand. It doesn't fully control the action since there is a "driver" in the chain of command. Here the action as begun and the lead tractors are making their initial turn.
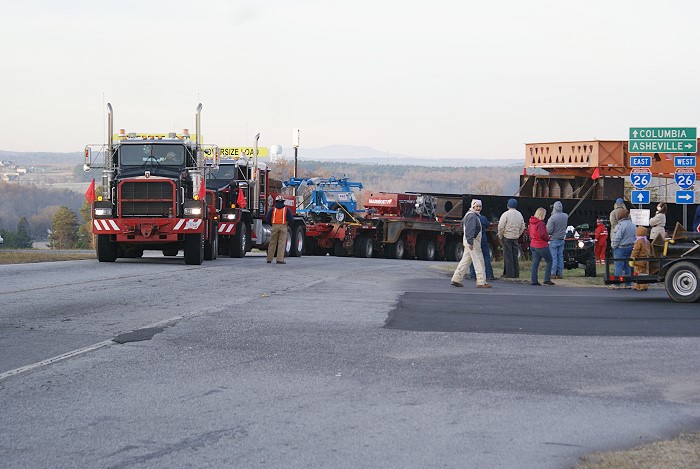
As things advance, dozens of power crews are on hand to clear overhead wires and there are hundreds of other support crews and dozens of support trucks waiting to fall in line behind the convoy.
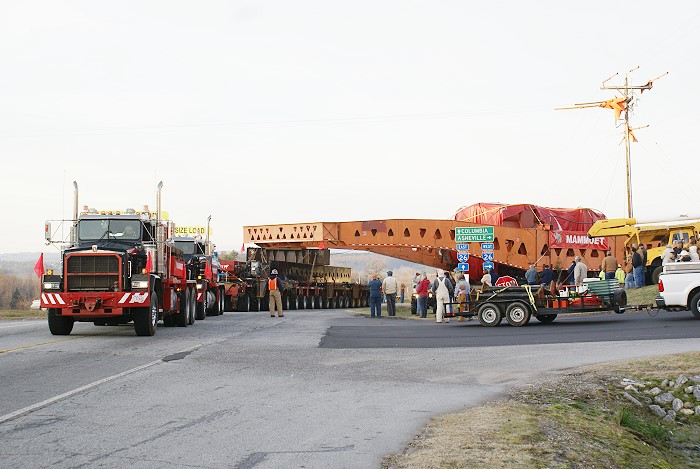
Notice that each large truck has a box firmly anchored over the rear wheels. Those are 18,500 pound weights which give the truck the needed traction this load requires to get it moving.
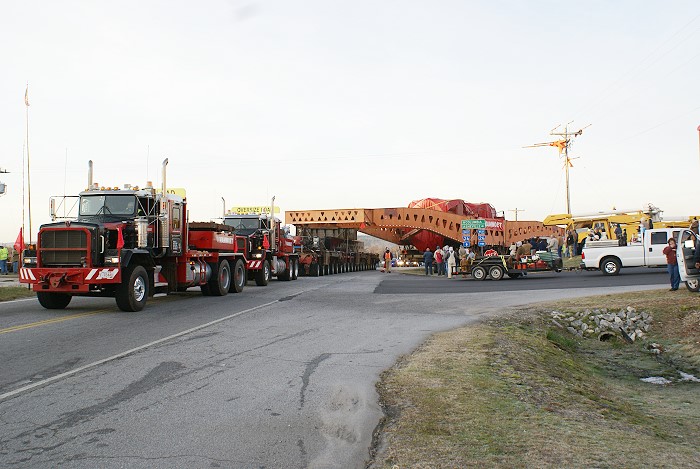
Looking closely at the rear section of the trailer, you'll see it is sitting at about an angle of 45° to the rest of the load. Once the main load was aligned as they wanted, the rear section crabbed and adjusted until it was in line and ready to travel. It was a strange action to watch but it worked perfectly.
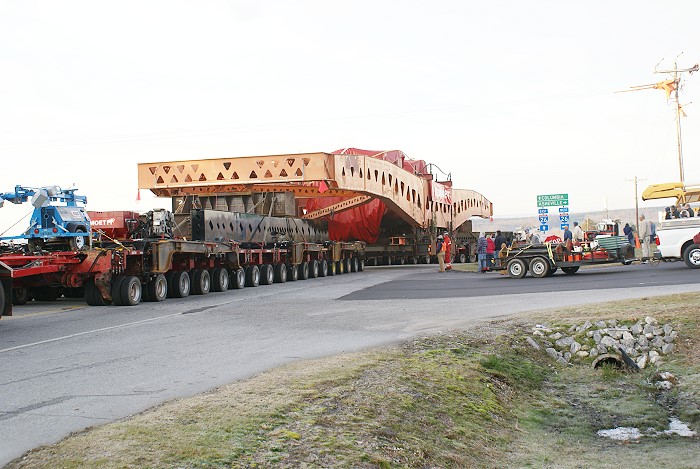
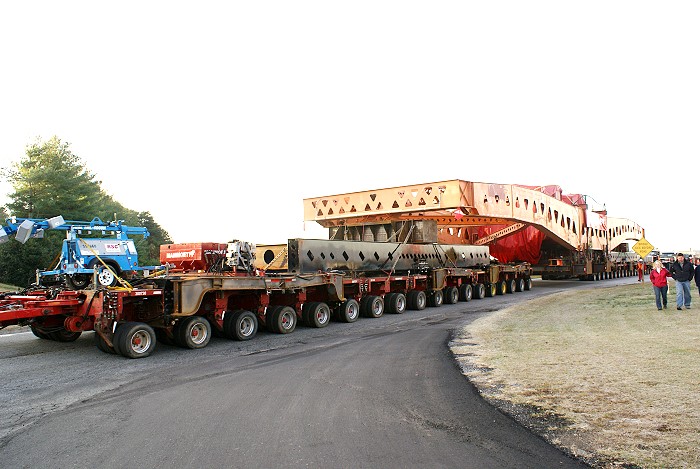
Here is a shot of one of the two "Drivers" The computer might tell the all wheels how much to turn, but this guy tells the computer when to do it and how much at a time. He's apparently pretty durable since the dawn temperature was a chilling 25° as he began his ride.
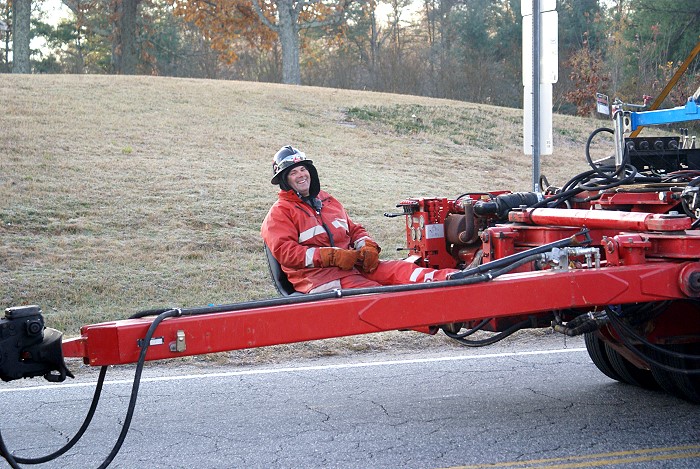
Here you can see how the the immense weight was distributed across the trailer sections as well as the hinge points for the support bridge. Both ends are supported in this fashion, making the whole rig a lot more flexible than it might first appear. Those outriggers I mentioned are clearly visible along the outer edge of the trailer.
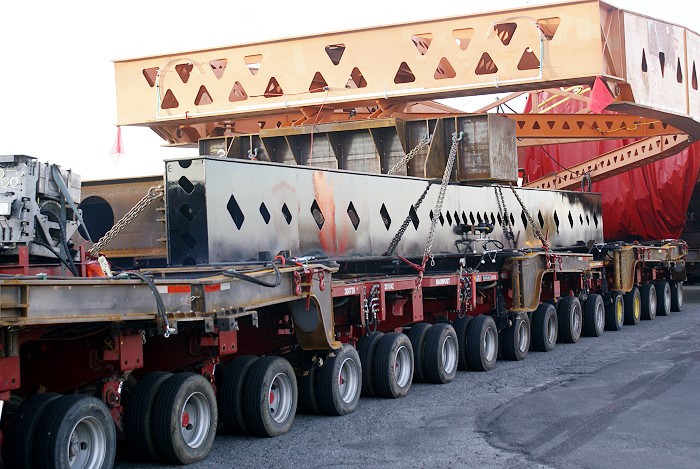
The main bridge beams suspend the huge generator about 18 inches above the roadbed. When the job is completed, the round pins near the bottom edge can be removed and the beams can be stacked for their return trip home. Even up close they almost look too small to be holding that much weight up in the air. Standing near this beam is a little spooky. All kinds of pops and groans can be heard, even when it isn't on the move.
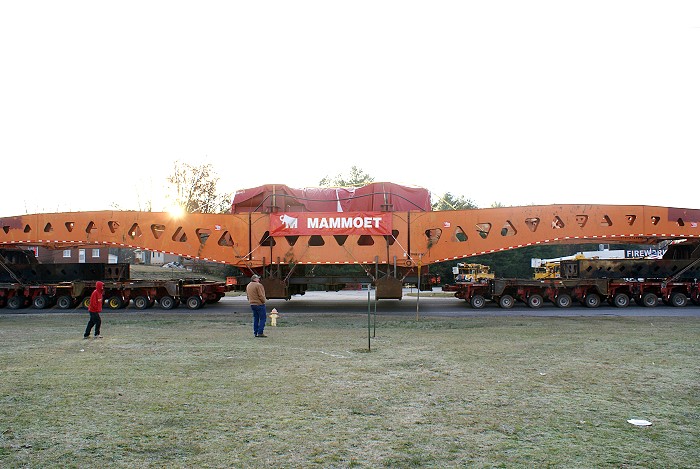
It was a fun way to begin a new day. Everyone I met was friendly, including those doing some downright cold and dirty work. Even the local cops seemed to be in fine spirits as they dealt with more traffic than that small community has probably ever seen. I just wanted to share some of the sights with you guys.
Steve