ER 40 Collet
A couple weeks ago I set about getting opinions on the ER32 collet chuck sold by LMS. During the discussion I changed my mind about the size collet system and the vendor, so I ordered an ER40 set from 800watt on eBay. It arrived earlier this week and today I had a chance to use it and see exactly what I had purchased.
First Impression
The first thing I noticed is that nowhere has the country of origin been marked. Of course, the first assumption is China. However, except for the case, the pieces seem of pretty good quality so it could be India or possibly even somewhere in Eastern Europe. My guess is somewhere in Asia.
The case is made of yellow pine, or something very similar, and of very poor quality construction. It was broken and falling apart when it arrived. Its wobbly and all the pieces fit poorly. The corners are reinforced but there is only a nail or two holding the corner covers on.
Upon opening the case my first impression was good. The ground finish on the chuck seemed of good quality, no chattering or burn marks. All edges were properly finished, I didnt find any burrs or snags anywhere. Even the threads on the nose had a ground finish.
Some slight burrs on the collets are evident, but then I didnt really expect to have the edges of the longitudinal slitting finished. All the outside edges have a decent finish, though they could have done a better job around the ring slot.
The chuck and all the collets are laser or acid etched indicating the size of each. Hopefully this will prove more durable than the ink markings Ive come to expect.
For the sake of those who dont know, the ER collet systems are a self-extracting collet that allows stock to pass completely through it. The collet is held in the nut by an eccentric ring, the collet slips in at a slight angle then snaps into place. The nut is then screwed onto the nose of the chuck, pressing the collet into the taper in the chuck. No drawbar is necessary such as might by used by an R8 or Morse Taper collet. Of course, the R8 portion of the chuck prevents pass-through, but I won't be needing that feature on a mill.
Let the testing begin
First up, the mill spindle. As expected it came out dead-nuts on the money. No surprise there, this is old American iron, after all.
The chuck came out with about .0005 run out. Not bad for a inexpensive Asian tool.
So, I put a 3/8 end mill in a collet and tightened up the nut. I got about .00125 run out on the side of the end mill. Not great, but on the edge of tolerable.
I then tried a 1/2 inch end mill and collet. The results were much better at about .0005, about the limits of the chuck. This is also what I got using an R8 collet with the same end mill.
Last Impressions
I have no illusions that this is a high quality tool. I did not have any accuracy problems with the mill, so I didnt expect this to correct anything. What I did want was a little more convenience and flexibility and I think I got that, only time will tell. I may end up replacing the 3/8 collet from another vendor, that hopefully will correct the high runout experienced there. I still have to check the other collets but I expect similar results from them.
Overall I think it is a good, not great but good, addition to the shop.
Next up is to create a chuck for the lathe. Someday.
A couple weeks ago I set about getting opinions on the ER32 collet chuck sold by LMS. During the discussion I changed my mind about the size collet system and the vendor, so I ordered an ER40 set from 800watt on eBay. It arrived earlier this week and today I had a chance to use it and see exactly what I had purchased.
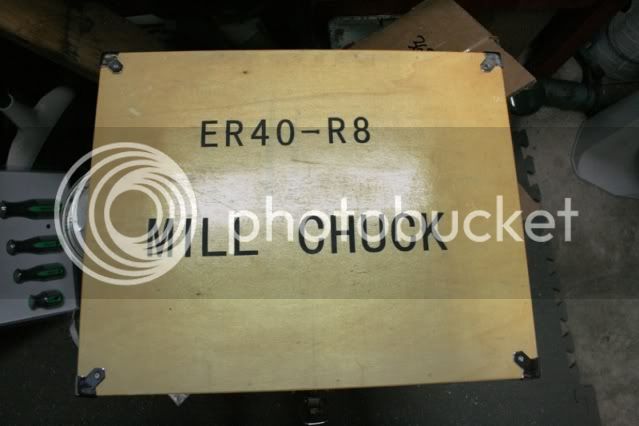
First Impression
The first thing I noticed is that nowhere has the country of origin been marked. Of course, the first assumption is China. However, except for the case, the pieces seem of pretty good quality so it could be India or possibly even somewhere in Eastern Europe. My guess is somewhere in Asia.
The case is made of yellow pine, or something very similar, and of very poor quality construction. It was broken and falling apart when it arrived. Its wobbly and all the pieces fit poorly. The corners are reinforced but there is only a nail or two holding the corner covers on.
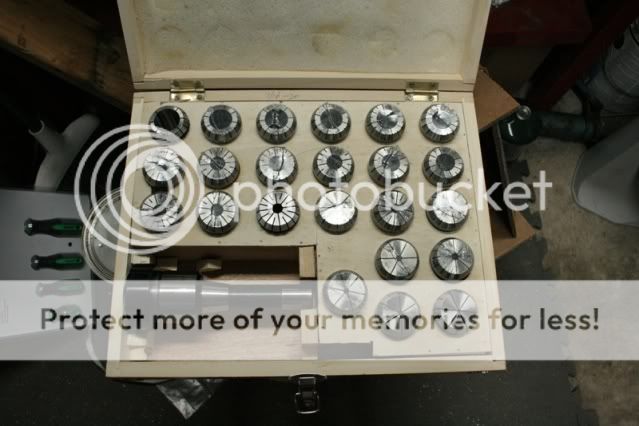
Upon opening the case my first impression was good. The ground finish on the chuck seemed of good quality, no chattering or burn marks. All edges were properly finished, I didnt find any burrs or snags anywhere. Even the threads on the nose had a ground finish.
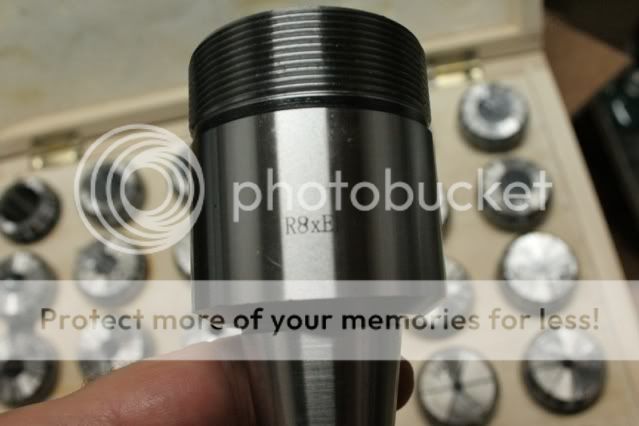
Some slight burrs on the collets are evident, but then I didnt really expect to have the edges of the longitudinal slitting finished. All the outside edges have a decent finish, though they could have done a better job around the ring slot.
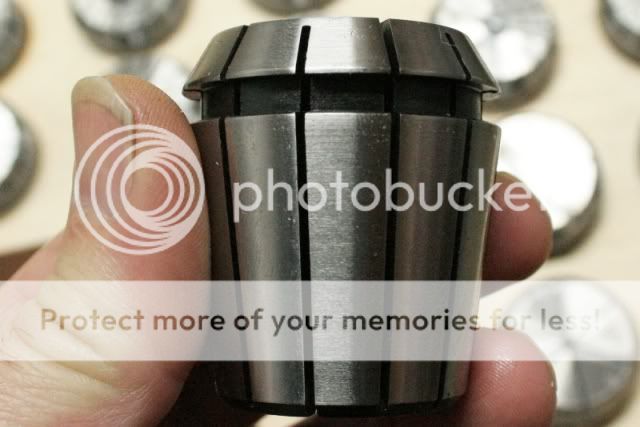
The chuck and all the collets are laser or acid etched indicating the size of each. Hopefully this will prove more durable than the ink markings Ive come to expect.
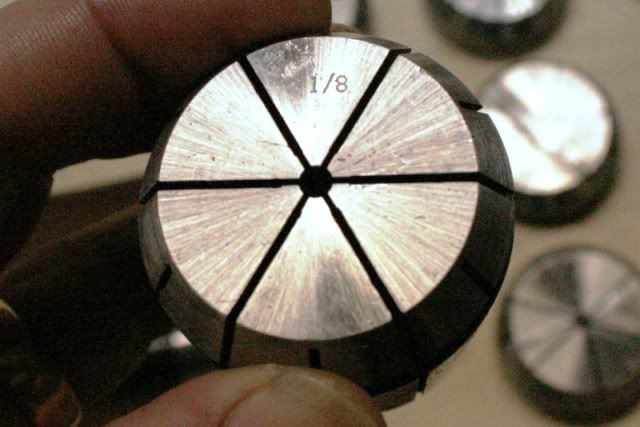
For the sake of those who dont know, the ER collet systems are a self-extracting collet that allows stock to pass completely through it. The collet is held in the nut by an eccentric ring, the collet slips in at a slight angle then snaps into place. The nut is then screwed onto the nose of the chuck, pressing the collet into the taper in the chuck. No drawbar is necessary such as might by used by an R8 or Morse Taper collet. Of course, the R8 portion of the chuck prevents pass-through, but I won't be needing that feature on a mill.
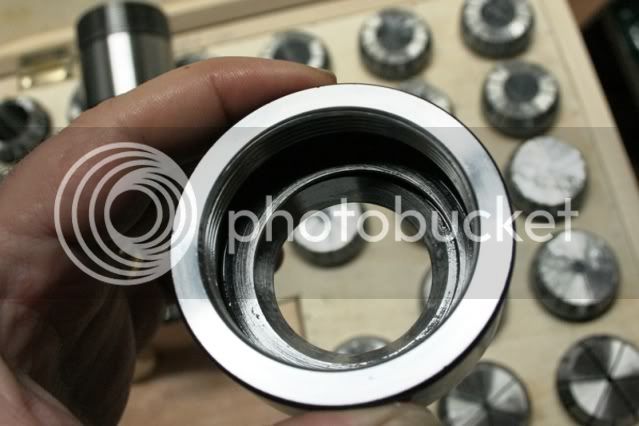
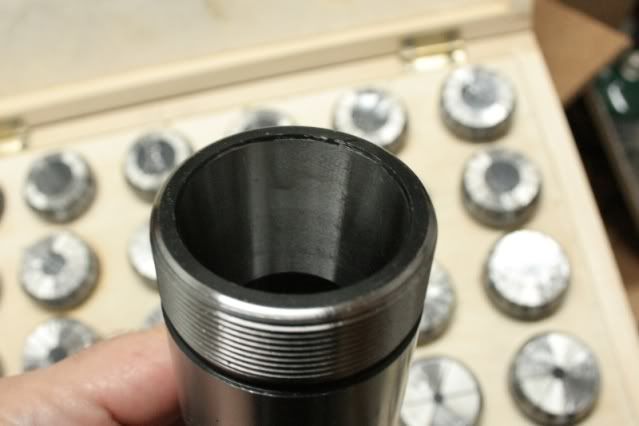
Let the testing begin
First up, the mill spindle. As expected it came out dead-nuts on the money. No surprise there, this is old American iron, after all.
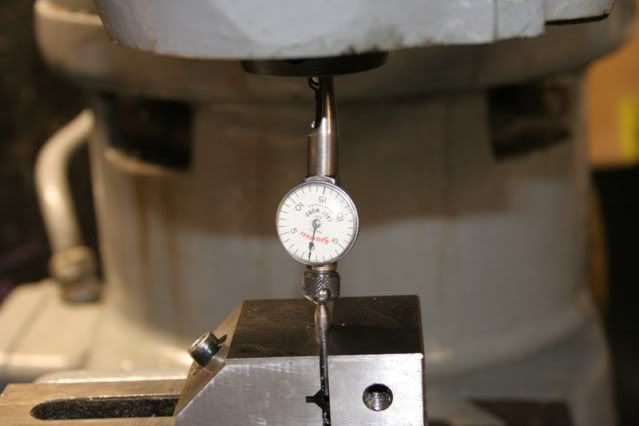
The chuck came out with about .0005 run out. Not bad for a inexpensive Asian tool.
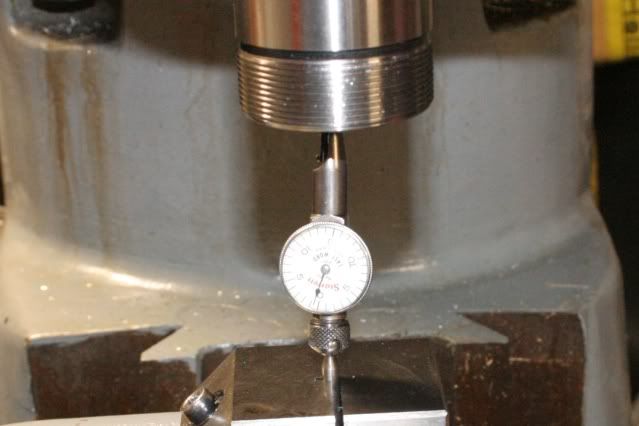
So, I put a 3/8 end mill in a collet and tightened up the nut. I got about .00125 run out on the side of the end mill. Not great, but on the edge of tolerable.
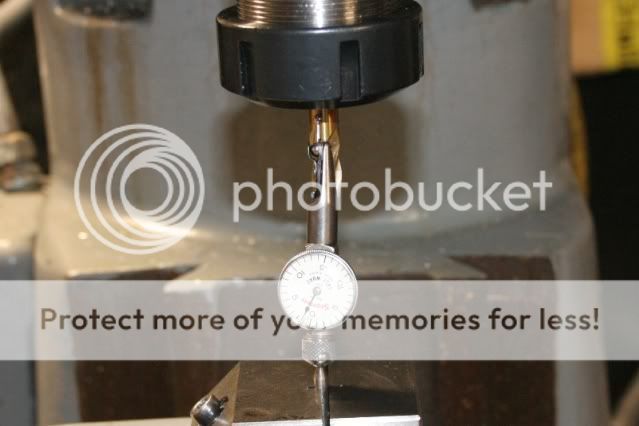
I then tried a 1/2 inch end mill and collet. The results were much better at about .0005, about the limits of the chuck. This is also what I got using an R8 collet with the same end mill.
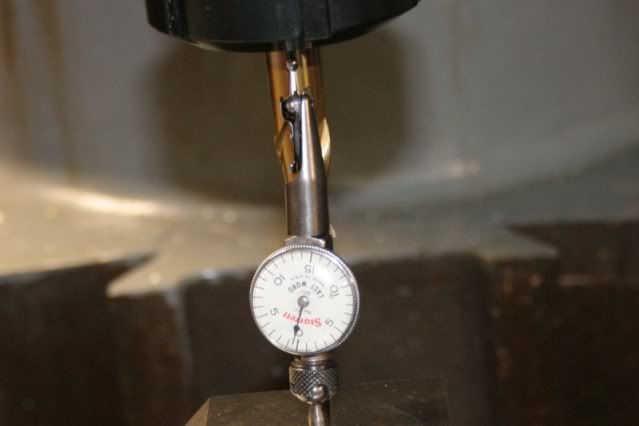
Last Impressions
I have no illusions that this is a high quality tool. I did not have any accuracy problems with the mill, so I didnt expect this to correct anything. What I did want was a little more convenience and flexibility and I think I got that, only time will tell. I may end up replacing the 3/8 collet from another vendor, that hopefully will correct the high runout experienced there. I still have to check the other collets but I expect similar results from them.
Overall I think it is a good, not great but good, addition to the shop.
Next up is to create a chuck for the lathe. Someday.