- Joined
- Dec 2, 2008
- Messages
- 971
- Reaction score
- 9
A few weeks ago I made some gears for my steam donkey project.
http://www.homemodelenginemachinist.com/index.php?topic=9212.30
These were the first gears that I had ever made and the results were better than I had expected. I cut an aluminum gear first, because aluminum is cheap, available and soft. Not knowing what to expect I started with the ali because I thought it would be easier. It worked fine. I first started with a cut to partial depth, but soon found that I could cut to full depth with ease.
When I got the courage to cut expensive brass, I started with full depth cut and that was fine too. I got the gears that I wanted but I didn't experiment much. It seemed that the way I was doing it was ok and I didn't want to risk the material trying something different.
I was happy with the results but one of the final comments that I made was, "I wouldn't want to try this on anything hard, like steel." Looking back, I realize that I had no real basis for the statement. It was a negative comment that might discourage someone, so today I cut steel gears. I wanted to take a break from building the donkey. It had become a little tedious and fiddly.
I didn't have to start at zero. I had everything that I needed. And there was no setup that I needed to retain. I didn't have to grind a cutter, I would just use the one I ground to cut the 12 tooth pinion.
So... I drilled a 1/4" hole in the end of a 1" bar of 12L14 and parted off a 1/4" slice. I mounted the blank on the same mandrel that I had used for the pinion and turned it to .68" dia. I realize that it would be more rigid if I just turned down the end of the bar and took the parent metal to the mill but that's not the way I did it with the brass , so I took the mandrel with the blank to the 4Jaw on the Rotary Table and set it up with the DTI.
I looked at the bit that I had used before and it looked good. I drew it across my thumbnail and it pulled up a nice curl. I took a few strokes across the cutting face on a Hard Arkansas stone be cause that's what I always do whenever I change cutting tools. I started the first tooth.
This was an experiment. I wanted to learn something and the gear was not needed for anything. My plan was to start with a partial depth cut. If it worked, I would advance to the next tooth and increase the depth. When I got to the deepest cut that was comfortable, I would make a full rotation, cutting all 12 teeth to this depth before cutting any deeper. To my great surprise, by the time I had cut 4 teeth, I had advanced the cut to full depth! I finished the 8 remaining teeth in single passes to full depth. Second surprise!! When I finished the first four teeth that had already been partially cut, I could barely feel the difference. The partial cuts did not help all that much if any.
I quickly prepared a brass blank to cut while the sensation of cutting a steel gear was clear in my mind. I experimented a little because that what this was, an experiment. I found that I could run the spindle speed just a hair faster with brass, but I could not increase the feed all that much. In the end, I did not find much of a difference between the two. I would not hesitate to cut a steel gear if the opportunity comes up.
Here is the results:
The mill that I am using is the standard HF version of the Chinese X2, unmodified. No concrete, no reinforced column, no stiffeners, no belt drive. The mill is fastened to a 3/4" particleboard bench top that is sitting (not bolted to cantilevered 2x4 support frames which are nailed to a 2x4 partition in a 12x20 temporary storage shed that is sitting on the ground. We plan to build a new large barn with a wood shop and a metal shop in the next year or two, but for right now, the closest piece of concrete is about 150 yards away. Rigid! Not so much! I held the cutter head shank in the drill chuck. The rotary table is the cheapest 4" unit that I could find with dividing plates. The point being that you can cut steel gears with a single point cutter on hobby size machines. I have no doubt that it could be done on a Shereline or Taig sized machine.
There are other ways to cut gears. I have not tried to make and use a hob because I'm a novice and hardening is a black art that I have yet to attempt. I have not used commercially made cutters because they are expensive and limited.
What I think is really important is the tool. It must be SHARP! I use my thumbnail as a test gauge. If the cutting edge skids across, its not sharp. It should curl up a nice curl without skipping or bouncing. If your ears are good you can tell by the sound.
Tool geometry is important. More important than in the lathe. If your lathe tool isn't cutting right, you take it out and regrind it, hone it, stone it, and polish it. That's the first place you look, the BIT!
Now, with all that made clear, I would not use this method to cut exotic metals like gold or platinum but that's only because I don't have any to try. If anyone would like to submit a sample of such metals for testing I Will be glad to fie a report. Samples should be at least 1/4" thick and at least .68" in diameter. Larger samples will be accepted.
All samples and the swarf therefrom become the property of the tester and will not be returned.
Jerry
http://www.homemodelenginemachinist.com/index.php?topic=9212.30
These were the first gears that I had ever made and the results were better than I had expected. I cut an aluminum gear first, because aluminum is cheap, available and soft. Not knowing what to expect I started with the ali because I thought it would be easier. It worked fine. I first started with a cut to partial depth, but soon found that I could cut to full depth with ease.
When I got the courage to cut expensive brass, I started with full depth cut and that was fine too. I got the gears that I wanted but I didn't experiment much. It seemed that the way I was doing it was ok and I didn't want to risk the material trying something different.
I was happy with the results but one of the final comments that I made was, "I wouldn't want to try this on anything hard, like steel." Looking back, I realize that I had no real basis for the statement. It was a negative comment that might discourage someone, so today I cut steel gears. I wanted to take a break from building the donkey. It had become a little tedious and fiddly.
I didn't have to start at zero. I had everything that I needed. And there was no setup that I needed to retain. I didn't have to grind a cutter, I would just use the one I ground to cut the 12 tooth pinion.
So... I drilled a 1/4" hole in the end of a 1" bar of 12L14 and parted off a 1/4" slice. I mounted the blank on the same mandrel that I had used for the pinion and turned it to .68" dia. I realize that it would be more rigid if I just turned down the end of the bar and took the parent metal to the mill but that's not the way I did it with the brass , so I took the mandrel with the blank to the 4Jaw on the Rotary Table and set it up with the DTI.
I looked at the bit that I had used before and it looked good. I drew it across my thumbnail and it pulled up a nice curl. I took a few strokes across the cutting face on a Hard Arkansas stone be cause that's what I always do whenever I change cutting tools. I started the first tooth.
This was an experiment. I wanted to learn something and the gear was not needed for anything. My plan was to start with a partial depth cut. If it worked, I would advance to the next tooth and increase the depth. When I got to the deepest cut that was comfortable, I would make a full rotation, cutting all 12 teeth to this depth before cutting any deeper. To my great surprise, by the time I had cut 4 teeth, I had advanced the cut to full depth! I finished the 8 remaining teeth in single passes to full depth. Second surprise!! When I finished the first four teeth that had already been partially cut, I could barely feel the difference. The partial cuts did not help all that much if any.
I quickly prepared a brass blank to cut while the sensation of cutting a steel gear was clear in my mind. I experimented a little because that what this was, an experiment. I found that I could run the spindle speed just a hair faster with brass, but I could not increase the feed all that much. In the end, I did not find much of a difference between the two. I would not hesitate to cut a steel gear if the opportunity comes up.
Here is the results:
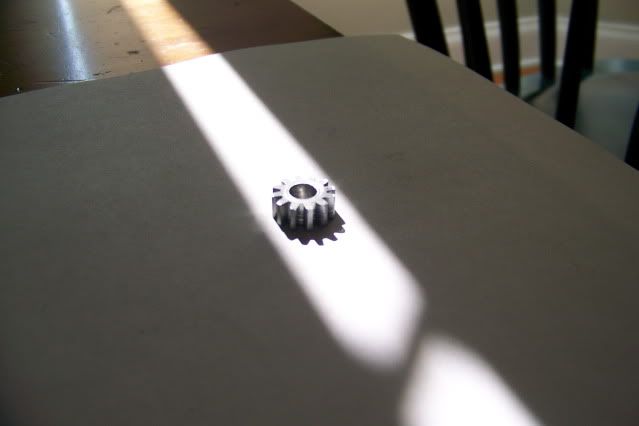
The mill that I am using is the standard HF version of the Chinese X2, unmodified. No concrete, no reinforced column, no stiffeners, no belt drive. The mill is fastened to a 3/4" particleboard bench top that is sitting (not bolted to cantilevered 2x4 support frames which are nailed to a 2x4 partition in a 12x20 temporary storage shed that is sitting on the ground. We plan to build a new large barn with a wood shop and a metal shop in the next year or two, but for right now, the closest piece of concrete is about 150 yards away. Rigid! Not so much! I held the cutter head shank in the drill chuck. The rotary table is the cheapest 4" unit that I could find with dividing plates. The point being that you can cut steel gears with a single point cutter on hobby size machines. I have no doubt that it could be done on a Shereline or Taig sized machine.
There are other ways to cut gears. I have not tried to make and use a hob because I'm a novice and hardening is a black art that I have yet to attempt. I have not used commercially made cutters because they are expensive and limited.
What I think is really important is the tool. It must be SHARP! I use my thumbnail as a test gauge. If the cutting edge skids across, its not sharp. It should curl up a nice curl without skipping or bouncing. If your ears are good you can tell by the sound.
Tool geometry is important. More important than in the lathe. If your lathe tool isn't cutting right, you take it out and regrind it, hone it, stone it, and polish it. That's the first place you look, the BIT!
Now, with all that made clear, I would not use this method to cut exotic metals like gold or platinum but that's only because I don't have any to try. If anyone would like to submit a sample of such metals for testing I Will be glad to fie a report. Samples should be at least 1/4" thick and at least .68" in diameter. Larger samples will be accepted.
All samples and the swarf therefrom become the property of the tester and will not be returned.
Jerry