Rolland
Well-Known Member
Been working on the Webster for the past month or so and had a light bulb moment when it came to making the tank. Using the basic instruction sheet with the engine for the tank using one inch brass tubing turned the end capsfor the tank and needing to solder on an outlet, filler cap and base came up with this idea. ;D
I used Brownell HI-Force 44 solder for the endcaps by tinning them and holding them on with a "C" clamp, then used standard 50-50 solder (the stuff for copper pipe)to clamp and attach the other small parts including the bases since Hi-Force melts at 475 it stays put when attaching the other small parts using standard solder, a much lower temp, no need to clamp the end pieces. I just need to clean up a couple of joints and I'm there. Also pressure checked the tank in water to be sure of a seal.
I used Brownell HI-Force 44 solder for the endcaps by tinning them and holding them on with a "C" clamp, then used standard 50-50 solder (the stuff for copper pipe)to clamp and attach the other small parts including the bases since Hi-Force melts at 475 it stays put when attaching the other small parts using standard solder, a much lower temp, no need to clamp the end pieces. I just need to clean up a couple of joints and I'm there. Also pressure checked the tank in water to be sure of a seal.
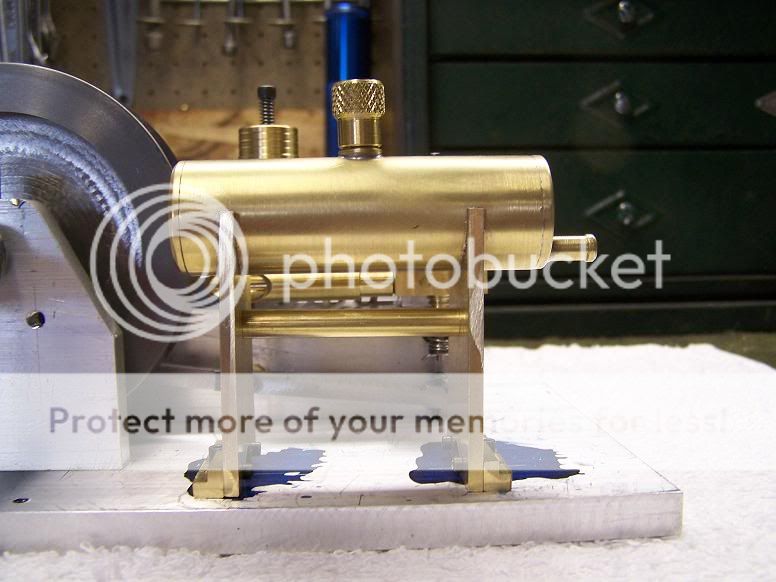
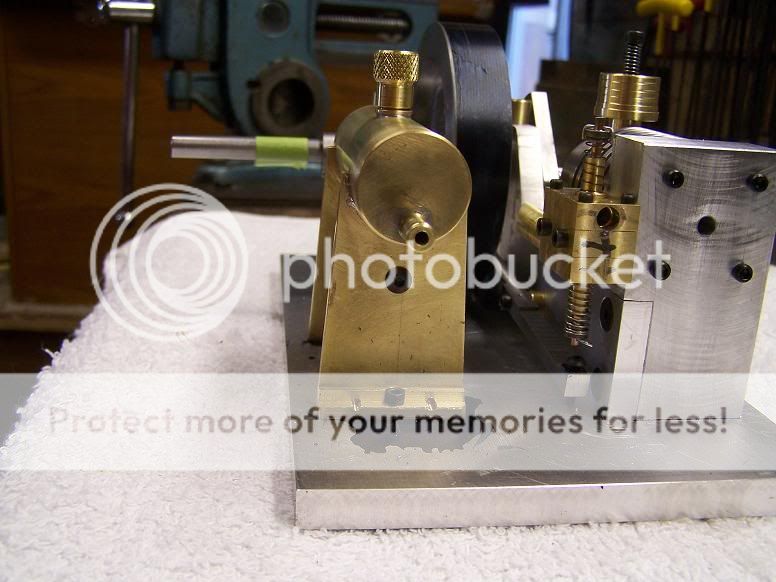