Tony Bird
Senior Member
Hi,
I have just started making a Stuart S50 mill engine. When making an engine from castings I often start with the cylinder and members might be interested in my approach. Having filed off any casting joints which on Stuart castings are very small I just flatten off the port face.
The cylinder is then bored and its one end cleaned up but not to size.
A piece of mild steel is centred both ends and set up between centres in the lathe. It is then turned to a good slide fit in the bore of the cylinder. Then shoulders of the same diameter are turned one at each end of the rod leave a raised portion which is less than the length of the bore of the cylinder. This raised section has several grooves cut in it.
This rod is then heated and shellac melted on to its. the cylinder is also heated and fitted over the rod. The shellac when cool will hold the cylinder in place.
The result can then be set up between centres and the cylinder machined to size.
The cylinder and its rod can then be removed from the lathe and mounted in the mill to do its flat surfaces.
When finished the combination can be heated and the rod can be removed from the cylinder. This has not been done as the steam chest and cover will be attached for machining.
A lot larger cylinders can also be done in this fashion. One I did as a demonstration for my model club. The ones on my 5" gauge locomotives were done the same way
The more usual way of using shellac on a disc chuck.
Hope this is found interesting.
Regards Tony.
I have just started making a Stuart S50 mill engine. When making an engine from castings I often start with the cylinder and members might be interested in my approach. Having filed off any casting joints which on Stuart castings are very small I just flatten off the port face.
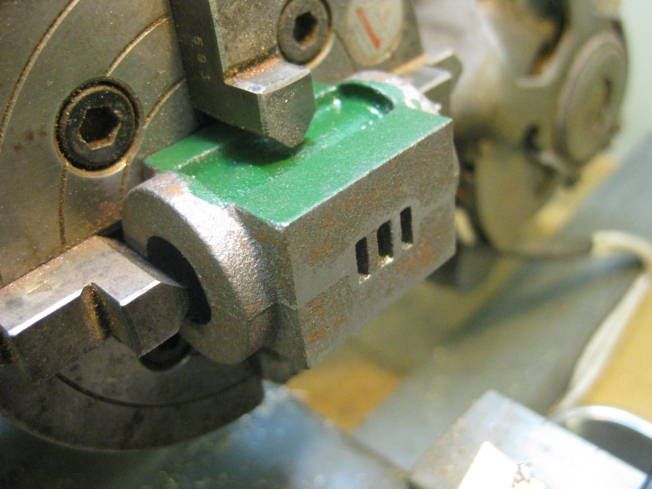
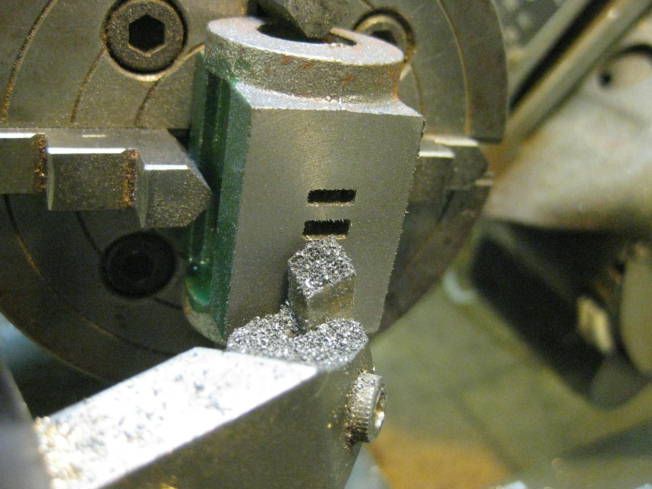
The cylinder is then bored and its one end cleaned up but not to size.
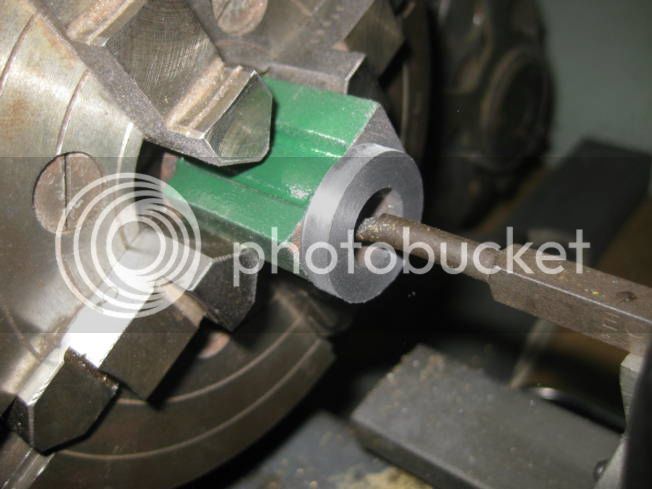
A piece of mild steel is centred both ends and set up between centres in the lathe. It is then turned to a good slide fit in the bore of the cylinder. Then shoulders of the same diameter are turned one at each end of the rod leave a raised portion which is less than the length of the bore of the cylinder. This raised section has several grooves cut in it.
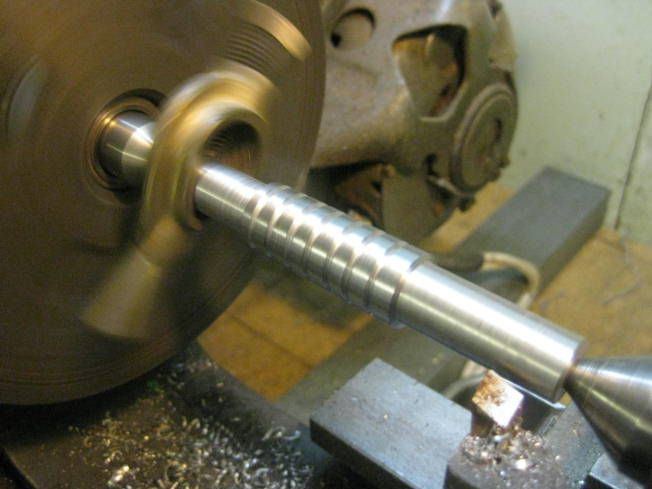
This rod is then heated and shellac melted on to its. the cylinder is also heated and fitted over the rod. The shellac when cool will hold the cylinder in place.
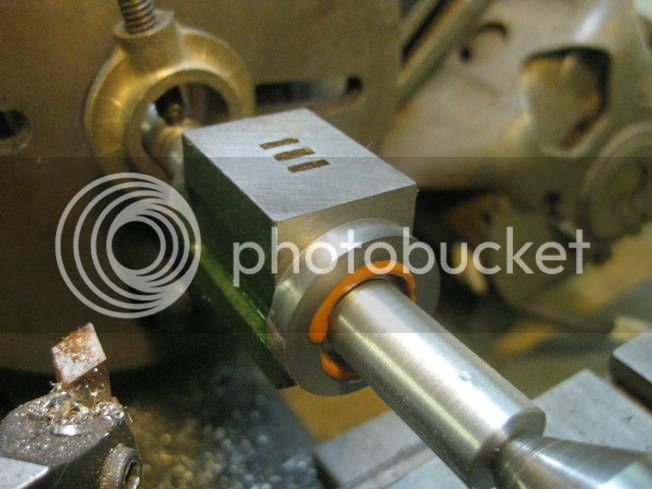
The result can then be set up between centres and the cylinder machined to size.
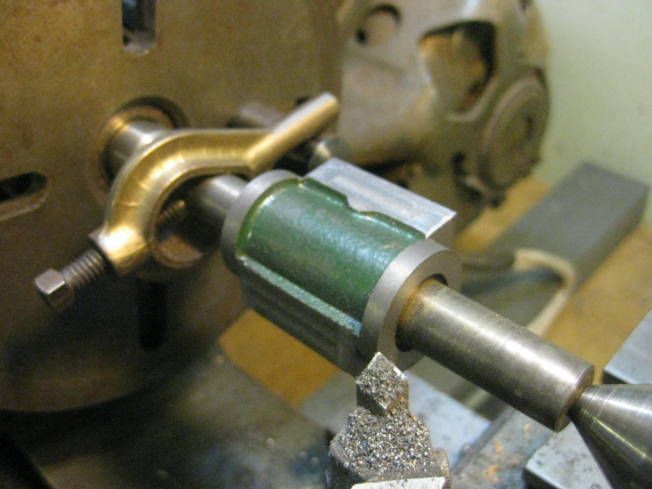
The cylinder and its rod can then be removed from the lathe and mounted in the mill to do its flat surfaces.
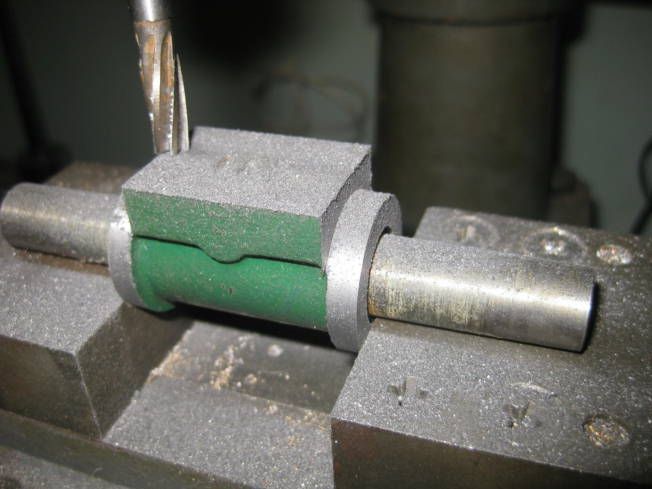
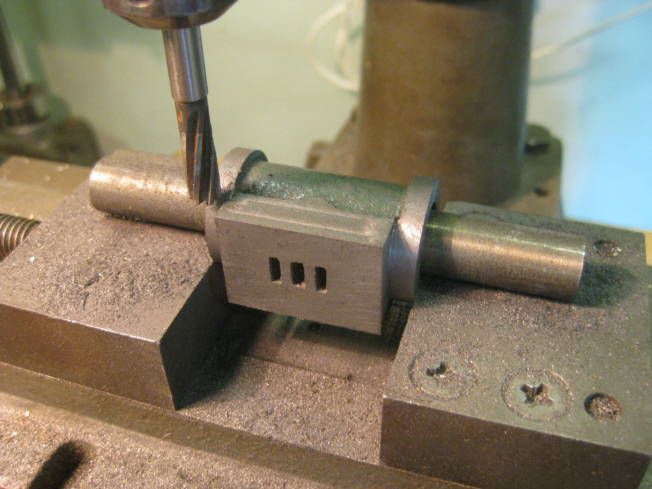
When finished the combination can be heated and the rod can be removed from the cylinder. This has not been done as the steam chest and cover will be attached for machining.
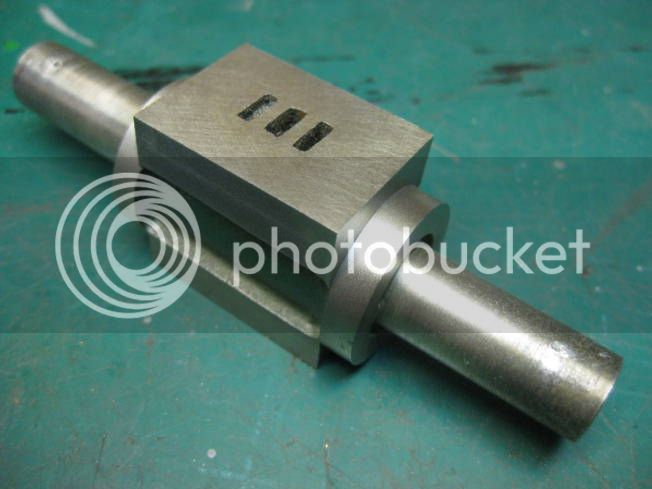
A lot larger cylinders can also be done in this fashion. One I did as a demonstration for my model club. The ones on my 5" gauge locomotives were done the same way
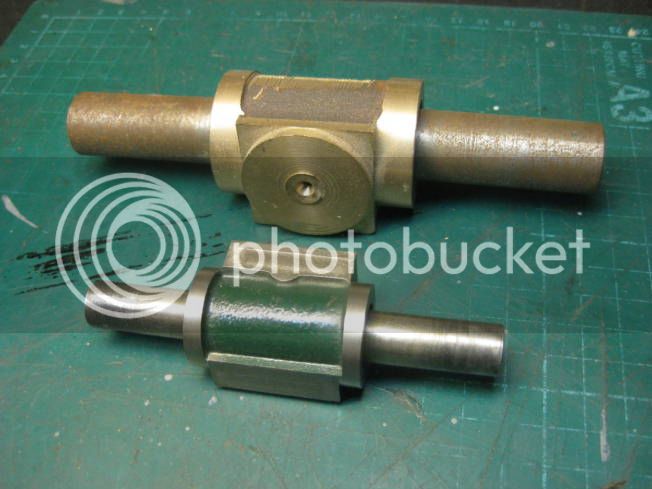
The more usual way of using shellac on a disc chuck.
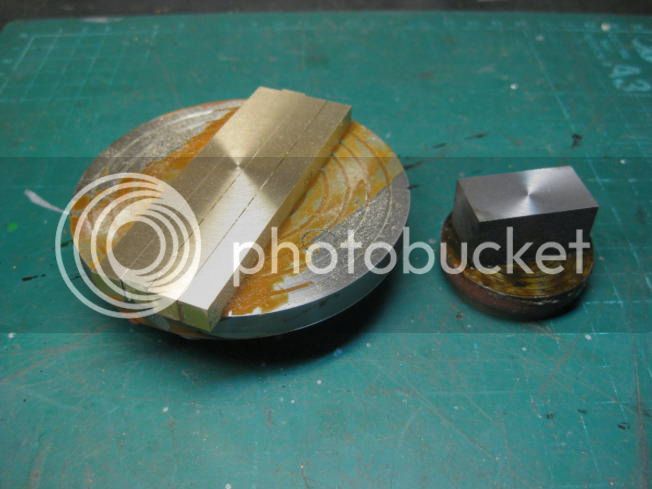
Hope this is found interesting.
Regards Tony.