- Joined
- Dec 12, 2012
- Messages
- 2,220
- Reaction score
- 1,288
As an apprentice in the UK in the 60s there were many grades of steel,many of which I was familiar with mainly mild steel or En2.Now in Australia the only 2 I know are 1214 free machining, or 1020 for welding.I don't know much about tensile strengths.Everything else for me is hot rolled.My main ref with what I am familiar with is grade of bolts. 4.6 = mild steel ?. 8.8 = high tensile
and cap screws 10.9 to 12.9
I saw a video on utube about machining rebar which I believe comes in 3 grades and would be classed as high tensile.A cheap supply of ht or very tough steel.Reebar is subject to strict quality control (it holds skyscrapers up)
The video shows making a special high tensile bolt from rebar with machining
very easy with rct.At the other exteme I saw a video of a contractor hiiting a piece of cheap imported rebar against concrete and it breaking.Poor quality very brittle.I assume a death trap
When a house was being built on the block next door I scrounged some pieces of rebar for possible use.I started with a 10" piece of nom 30dia and machined
to the most economical section. 22mm a/f octagonal just as an excersize
It machined well with good finish.I don't know the grade would call it high tensile,a good source of tough steel for pins,nuts and bolts etc.Any input
by others on the tensile strength of steels and differing names would be most welcome.The steel does ring when struck and is much tougher to file so
lets just call it High Tensile
and cap screws 10.9 to 12.9
I saw a video on utube about machining rebar which I believe comes in 3 grades and would be classed as high tensile.A cheap supply of ht or very tough steel.Reebar is subject to strict quality control (it holds skyscrapers up)
The video shows making a special high tensile bolt from rebar with machining
very easy with rct.At the other exteme I saw a video of a contractor hiiting a piece of cheap imported rebar against concrete and it breaking.Poor quality very brittle.I assume a death trap
When a house was being built on the block next door I scrounged some pieces of rebar for possible use.I started with a 10" piece of nom 30dia and machined
to the most economical section. 22mm a/f octagonal just as an excersize
It machined well with good finish.I don't know the grade would call it high tensile,a good source of tough steel for pins,nuts and bolts etc.Any input
by others on the tensile strength of steels and differing names would be most welcome.The steel does ring when struck and is much tougher to file so
lets just call it High Tensile

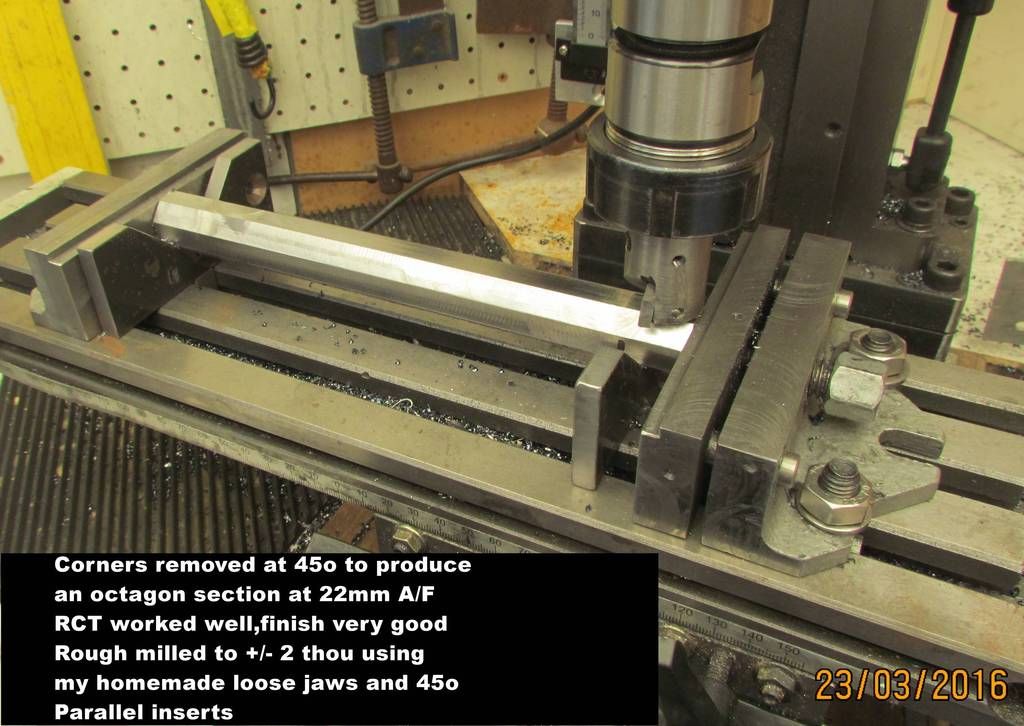
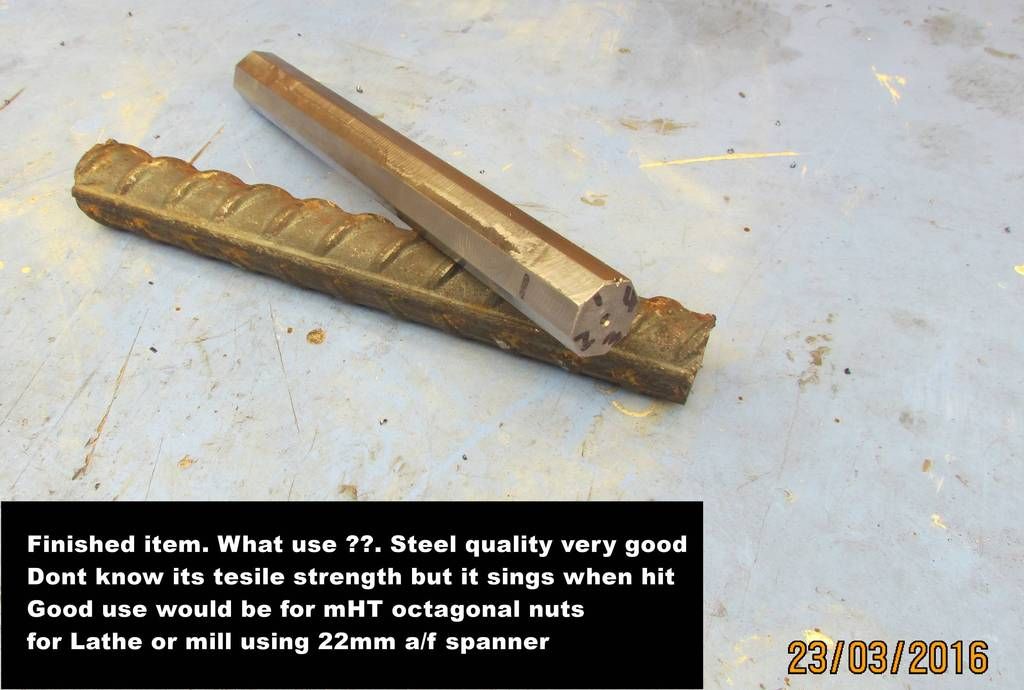