- Joined
- Mar 3, 2008
- Messages
- 243
- Reaction score
- 20
Hi
Here is my 1st Flame-Licker Engine, my 4th project so far. This was the first project I did with my
new Mini-Mill, and enjoyed making it.
Here is a Picture:
Also a Video:
I took a few shortcuts like:
The crank is made from brass, I have not mastered creating a steel one yet!
I did a few 45Deg cuts on the main body instead of rounding off. I did not have a rotary table and I
did not want any file or sandpaper marks on the piece. I realy wanted to show the machined surface.
It appears that the seating of the valve and piston lubrication are most important for this type of
engine. I had to try a few different "bends" to the valve to get it to run and it needs adjustment
every so often. At first I ran the engine with a light machine oil, but after it cooled the valve
would be "glued" to the head and the oil in the cylinder was thick and sticky. I cleaned it out and
rubbed some extra-fine graphite on the cylinder walls and then I poured a small amount on a cloth and
rolled the piston in it to coat it all over. After I did that, it ran at twice the RPM and only needs
to be redone after a dozen or so 5 minuit runs.
Well, back to the next project.
Here is my 1st Flame-Licker Engine, my 4th project so far. This was the first project I did with my
new Mini-Mill, and enjoyed making it.
Here is a Picture:
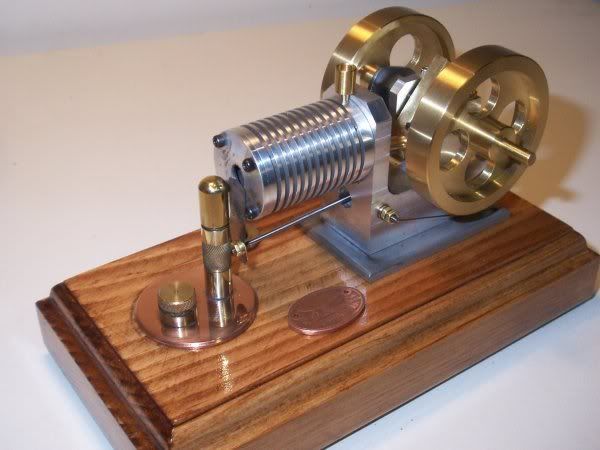
Also a Video:
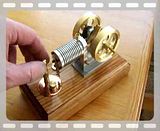
I took a few shortcuts like:
The crank is made from brass, I have not mastered creating a steel one yet!
I did a few 45Deg cuts on the main body instead of rounding off. I did not have a rotary table and I
did not want any file or sandpaper marks on the piece. I realy wanted to show the machined surface.
It appears that the seating of the valve and piston lubrication are most important for this type of
engine. I had to try a few different "bends" to the valve to get it to run and it needs adjustment
every so often. At first I ran the engine with a light machine oil, but after it cooled the valve
would be "glued" to the head and the oil in the cylinder was thick and sticky. I cleaned it out and
rubbed some extra-fine graphite on the cylinder walls and then I poured a small amount on a cloth and
rolled the piston in it to coat it all over. After I did that, it ran at twice the RPM and only needs
to be redone after a dozen or so 5 minuit runs.
Well, back to the next project.