t_ottoboni
Well-Known Member
- Joined
- Aug 9, 2009
- Messages
- 68
- Reaction score
- 9
Hi guys!
A few months ago I saw this oil pump in Popular Science Magazine and since then I wanted to build one. Instead of an oil pump, I´ll use it as a water pump for a (yet to be built) single cylinder IC engine.
I know it´s a silly project, but for a begginer like me this is a real challenge! =)
I have made the drawings in solidworks (2010), and after I finish this build and if the pump works well, I will share the final version of the drawings.
The pump in my drawings have basically two sides: a low pressure side visible through a plexiglass front cover and a high (have no idea how high) pressure side at the "barrel" next to the pulley.
I already started making some parts for this pump and need to buy material for the case and case cover.
The screws that hold the front cover are M2 button socket head and will take a while to arrive here... I bought a lot of 1000 from a chinese supplier and it can take up to 60 days to get in here so this can be a long build (specially if too much leaks begins to appear!)
I know a gear pump would be much better (and smaller) for an IC engine, but I thing it will be fun to watch this one working through the front cover.. :hDe:
A few months ago I saw this oil pump in Popular Science Magazine and since then I wanted to build one. Instead of an oil pump, I´ll use it as a water pump for a (yet to be built) single cylinder IC engine.
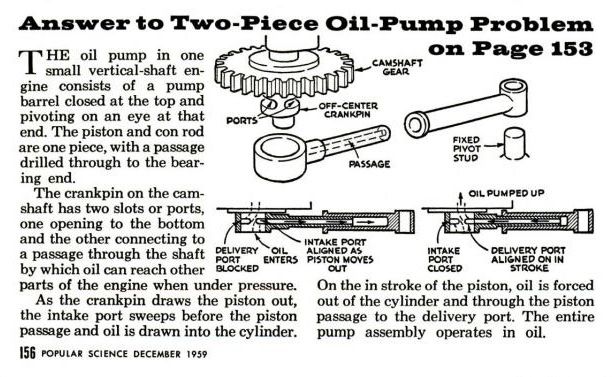
I know it´s a silly project, but for a begginer like me this is a real challenge! =)
I have made the drawings in solidworks (2010), and after I finish this build and if the pump works well, I will share the final version of the drawings.
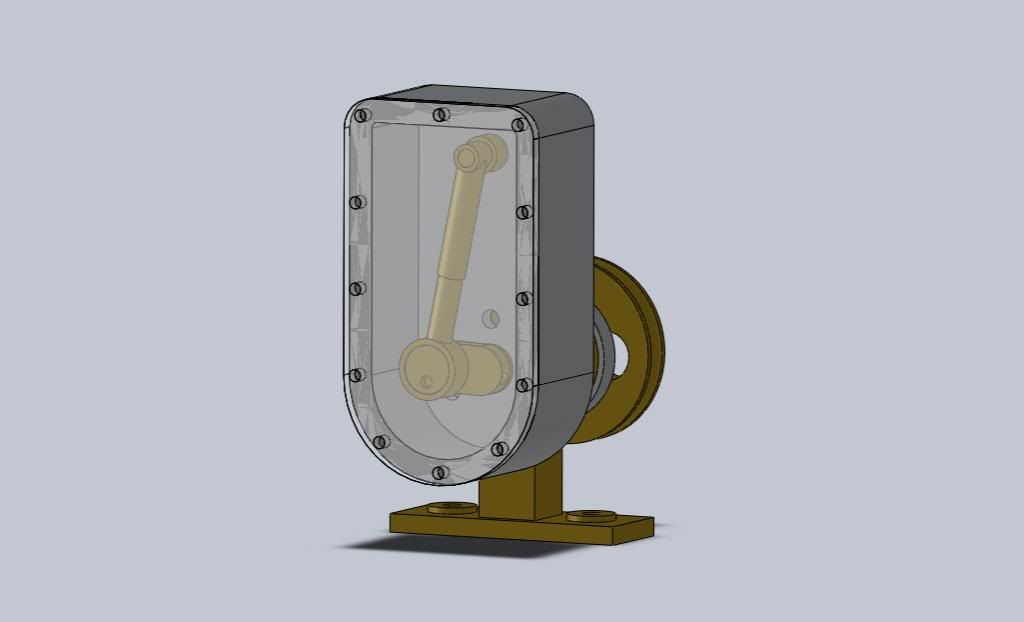
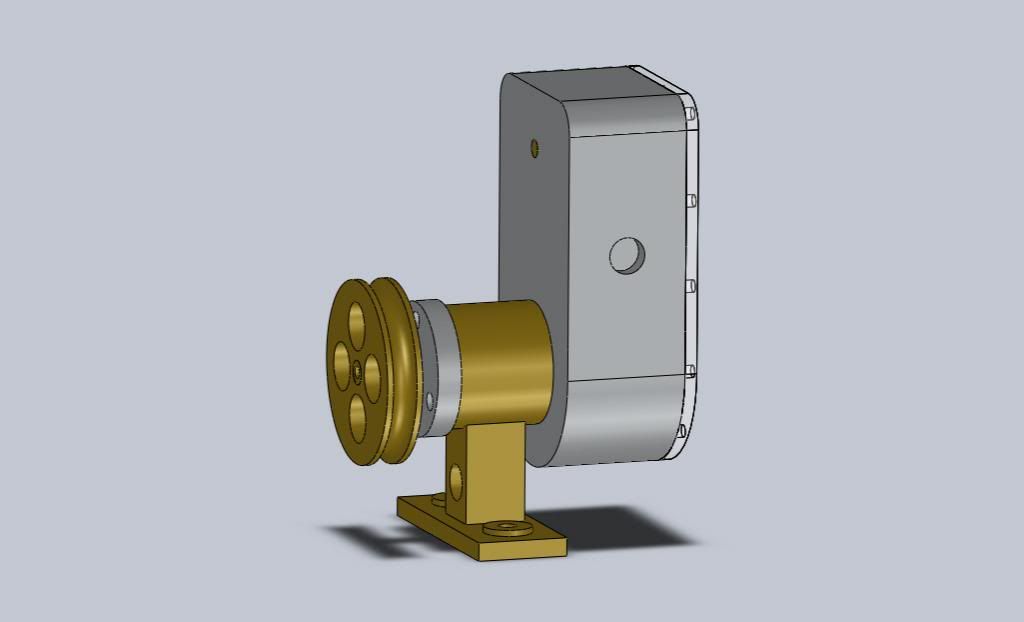
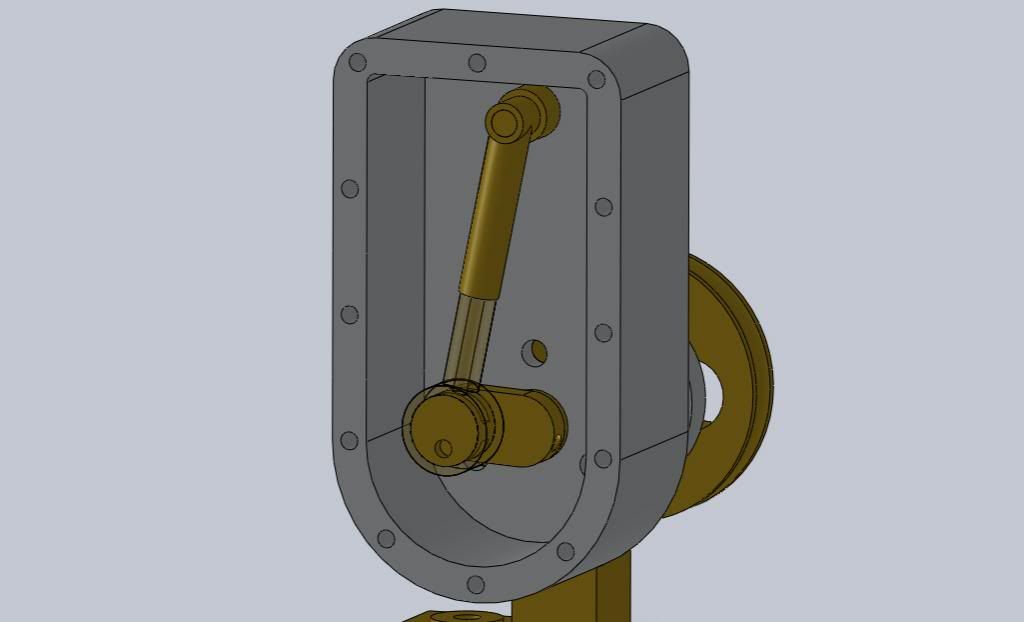
The pump in my drawings have basically two sides: a low pressure side visible through a plexiglass front cover and a high (have no idea how high) pressure side at the "barrel" next to the pulley.
I already started making some parts for this pump and need to buy material for the case and case cover.
The screws that hold the front cover are M2 button socket head and will take a while to arrive here... I bought a lot of 1000 from a chinese supplier and it can take up to 60 days to get in here so this can be a long build (specially if too much leaks begins to appear!)
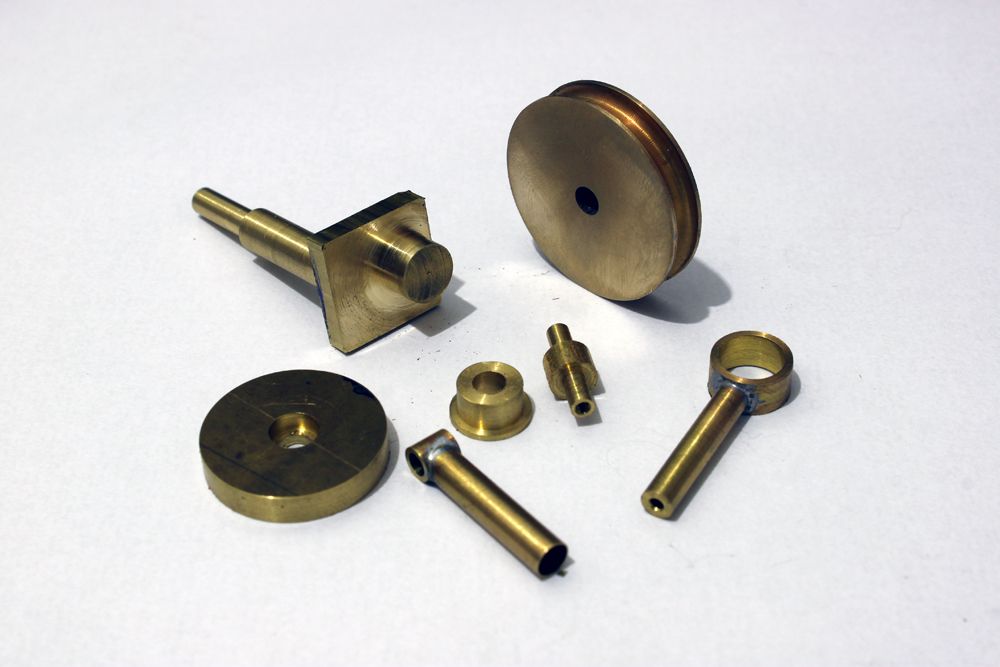
I know a gear pump would be much better (and smaller) for an IC engine, but I thing it will be fun to watch this one working through the front cover.. :hDe: